Автор: В.В. Иванников, А.Г. Николаев, В.М. Шварц, О.Б. Рябов, В.Н. Степанов (ОАО «НОРЭ»).
Опубликовано в журнале Химическая техника №7/2015
Основная деятельность компании ОАО «НОРЭ» – проведение экспертизы промышленной безопасности на опасных производственных объектах, в том числе экспертизы промышленной безопасности зданий и сооружений на опасных производственных объектах.
При проведении обследования объектов экспертизы специалисты ОАО «НОРЭ» уделяют повышенное внимание несущим конструкциям производственных зданий и сооружений. В этой статье рассматриваются наиболее характерные дефекты и повреждения металлических конструкций, выявленные при обследовании несущих строительных конструкций зданий и сооружений.
Металлические конструкции являются одними из самых распространенных видов строительных конструкций. Металлоконструкции подразделяются на стальные и из легких сплавов (например, алюминиевые). В современном строительстве получили распространение стальные конструкции, используемые в несущих каркасах промышленных зданий и сооружений, жилых и общественных зданий, в пролетных строениях мостов, эстакад, галерей, в каркасах доменных печей, газгольдерах, резервуарах, мачтах, башнях и др. Конструкции из алюминиевых сплавов наиболее широко применяются в качестве ограждающих элементов и в виде отделочных деталей зданий.
Основные достоинства металлических конструкций:
- высокая несущая способность – возможность воспринимать значительные нагрузки при относительно небольших сечениях благодаря значительной прочности металла;
- высокая надежность, так как конструкции могут быть рассчитаны достаточно точно;
- легкость и транспортабельность. Металлические конструкции по сравнению с конструкциями из камня, железобетона и дерева много легче. Они почти в 4 раза легче железобетонных и часто легче деревянных (при использовании под действием одинаковых нагрузок). А поскольку металлические конструкции наиболее легкие, они и наиболее транспортабельны и легко монтируемы;
- сплошность материала и соединений, что позволяет производить водои газонепроницаемые конструкции;
- индустриальность, достигаемая изготовлением конструкций на специализированных заводах.
Металлические конструкции удобны в эксплуатации, так как легко могут быть усилены при увеличении нагрузки. Они наиболее полно используются при реконструкциях и легко ремонтируются.
К недостаткам металлических конструкций относится низкие коррозионная стойкость и огнестойкость. Эти недостатки иногда требуют применения специальных коррозионно-стойких сталей и специальных защитных покрытий, предохраняющих их от коррозии и относительно высоких (более 400°С) температур.
Качество изготовления и монтажа стальных конструкций; а также правила их технической эксплуатации регламентируются СП-СНиП, ГОСТ и отраслевыми документами. Однако в результате несовершенства норм и ошибок проектирования, низкого качества работ по изготовлению и монтажу конструкций, нарушений правил технической эксплуатации в конструкциях появляются отклонения от проектных размеров, формы и качества сверх допускаемых пределов. В соответствии с СП 13102–2003 «Правила обследования несущих строительных конструкций зданий и сооружений» дефекты – это отдельные несоответствия конструкций какому-либо параметру, установленному проектом или нормативным документом (СНиП, ГОСТ, ТУ, СН и др.), полученные конструкцией на стадии изготовления и монтажа, а повреждения – это неисправности, полученные конструкцией при изготовлении, транспортировании, монтаже и эксплуатации.
Очагами развития повреждений часто являются дефекты изготовления и монтажа. Дефекты характеризуют начальное состояние конструкций. Повреждения возникают и развиваются во времени и зависят от срока эксплуатации и интенсивности воздействий. В зависимости от вызывающих их воздействий они могут быть разделены на следующие:
- силовые (механические) – разрывы, трещины, потеря устойчивости, искривления и местные погибы, расстройство соединений, абразивный износ и т.п.;
- температурные – коробление и разрушение элементов при высоких температурах, хрупкие трещины при отрицательных температурах, повреждения защитных покрытий при нагреве;
- химические и электрохимические – коррозия металла и разрушение защитных покрытий.
Повреждения от силовых воздействий возникают в результате несоответствия расчетных предпосылок действительным условиям работы конструкций и обусловлены следующими факторами:
- ошибками проектирования, связанными с неправильным определением нагрузок и внутренних усилий и подбором сечения элементов и узлов;
- отличием фактического напряженного состояния от расчетного вследствие неизбежного упрощения и идеализации расчетной схемы конструкции, ее элементов, узлов и действующих нагрузок, а также недостаточной изученности действительной работы конструкций и характера воздействий;
- пониженными прочностными характеристиками основного и наплавленного металла, дефектами, приводящими к концентрации напряжений и способствующими усталостному и хрупкому разрушению;
- произвольным изменением сечений элементов, размеров сварных швов, числа заклепок и болтов при изготовлении и монтаже по сравнению с проектными решениями;
- недопустимой перегрузкой конструкций при эксплуатации;
- нарушениями при монтаже и эксплуатации взаимного расположения конструкций (смещение прогонов, эксцентриситет и перепады в стыках подкрановых рельсов и т.п.), что приводит к появлению дополнительных, не учитываемых расчетом, нагрузок и динамических воздействий;
- нарушениями правил технической эксплуатации: ударами транспортируемых грузов, использованием конструкций для подвески блоков и опирания домкратов, подъема и перемещения грузов при ремонтах без соответствующего расчета и необходимого усиления, вырезкой отверстий в элементах конструкций для пропуска коммуникаций, удалением связевых элементов и т.п.
Нередко повреждения от силовых воздействий связаны с неудачным конструктивным решением узлов.
Для конструкций, подвергающихся действию подвижных динамических нагрузок, – подкрановых балок (особенно при кранах тяжелого и весьма тяжелого режимов работы) характерны усталостные повреждения, которые проявляются в виде трещин в основном металле, сварных швах и околошовной зоне и в расстройстве болтовых и заклепочных соединений.
Значительные повреждения металлических конструкций возникают при нарушении правил технической эксплуатации зданий и сооружений.
Повреждениям от температурных воздействий в наибольшей степени подвержены элементы, расположенные вблизи источников тепловыделения. В горячих цехах при изменении температуры появляются значительные температурные перемещения, приводящие к отклонению конструкций от проектного положения. При наличии связей, которые препятствуют свободным перемещениям, в элементах конструкций возникают дополнительные напряжения, имеющие циклический характер. При определенных условиях эти напряжения могут привести к искривлению элементов или появлению трещин. При нагреве стальных конструкций до температуры 100°С разрушается защитное покрытие, при 300…400°С происходит коробление элементов, особенно тонкостенных.
Нарушения правил эксплуатации оборудования и возникновение аварийных ситуаций могут привести к проливам расплавленного металла, короблению и пережогу элементов перекрытий и нижних частей колонн.
Повреждения от действия низких температур возникают, как правило, в открытых сооружениях и неотапливаемых зданиях. К таким повреждениям относятся хрупкие трещины в местах концентрации напряжений (сварные швы, резкие изменения сечения, фасонки ферм и т.п.). Особенно подвержены хрупким разрушениям конструкции, выполненные из кипящих сталей.
Повреждения от действия агрессивных сред проявляются в виде разрушения защитных покрытий и коррозии металла. Интенсивность коррозионных повреждений, измеряемая скоростью (мм в год) проникания коррозии по толщине элемента и относительной площадью участков, пораженных коррозией, зависит от степени агрессивности эксплуатационной среды, материала конструкций (марки стали), конструктивной формы элементов, системы и качества нанесения антикоррозионной защиты, а также от соблюдения правил технической эксплуатации (своевременная ликвидация протечек кровли, трубопроводов, контроль герметичности оборудования и т.д.). Дефекты и повреждения антикоррозионной защиты проявляются в виде шелушения, отслаивания, пор, трещин и других нарушений защитных свойств.
Повреждения металла возникают вследствие химической и электрохимической коррозии. Для стальных конструкций производственных зданий характерна электрохимическая коррозия. Коррозионные повреждения металла разделяются на общие равномерные или неравномерные по площади поверхности и местные в виде отдельных питингов, язв, сквозных поражений. Местные коррозионные поражения возникают при локальных воздействиях, например, при протечках кровли, нарушении герметичности трубопроводов и т.д. Если общая поверхностная коррозия приводит к уменьшению площади поперечного сечения элементов и повышению уровня напряжений, то местная коррозия не только ослабляет сечение, но и повышает концентрацию напряжений, что может привести к хрупкому разрушению конструкций.
Наиболее характерными дефектами и повреждениями металлоконструкций являются:
- ослабление поперечного сечения или отсутствие элемента (вырез элемента или части сечения, отсутствие элемента, предусмотренного проектом, уменьшение сечения по сравнению с проектом в результате замены при изготовлении, монтаже или эксплуатации);
- деформации отдельных элементов или конструкций в целом в виде погнутостей, прогибов, искривлений;
- отклонение или смещение конструкций относительно проектного положения;
- непроектное размещение элементов конструкций;
- трещины в основном металле, в сварном шве и околошовной зоне;
- дефекты сварных швов: неполномерность швов, пороки сварки, отсутствие швов;
- дефекты болтовых и заклепочных соединений, такие, как трещиноватость, неполномерность головок, перекос стержня, неплотность пакета, ослабление или отсутствие болтов или заклепок и т.д.;
- наличие в конструкциях концентраторов напряжений;
- взаимное смещение конструкций (расцентровка элементов, внеузловое опирание и т.д.);
- механические или температурные повреждения металла;
- разрушение антикоррозионных защитных покрытий и коррозионные повреждения металла и соединений;
- неграмотно выполненное усиление конструкций;
- деформации в элементах конструкций вследствие неравномерных осадок;
- непроектное приложение нагрузок на элементы конструкций в процессе эксплуатации (подвеска технологического оборудования, подвески, допущенные при выполнении ремонтных работ и т.п.).
Рассмотрим наиболее часто встречающиеся дефекты и повреждения в основных несущих металлоконструкциях производственных зданий.
Колонны
Колонны производственных зданий работают в более благоприятных условиях, чем другие элементы каркаса.
Расчет колонн выполняется на совместное действие большого числа нагрузок, поэтому расчетные усилия в колоннах значительны, и сечения их относительно велики. В нормальных условиях эксплуатации усилия в колоннах значительно меньше расчетных, так как одновременное воздействие большого числа нагрузок маловероятно и за весь период эксплуатации конструкций такого воздействия может даже и не быть. Мощные сечения колонн при невысоких рабочих напряжениях обладают большими запасами несущей способности, а также лучше сопротивляются механическим воздействиям и имеют высокую стойкость против коррозии.
Преимущественная работа колонн на сжатие и слабое воздействие динамических и вибрационных нагрузок не приводят к усталостным повреждениям стержня колонн, так как эти нагрузки прикладываются к колонне не непосредственно, а через другие конструкции, поэтому не создается предпосылок для возникновения хрупких разрушений. Даже при большом сроке эксплуатации ступенчатые колонны, наиболее широко применяемые в промышленных зданиях, и при наличии повреждений не теряют своей несущей способности, и случаев их разрушений не зафиксировано.
Дефекты изготовления (искривления и погибы отдельных элементов, дефекты сварных швов), как правило, незначительны и мало влияют на несущую способность колонн. Более существенны дефекты монтажа, основными из которых являются отклонения от проектного положения (смещение в плане, отклонение от вертикали), искривления колонн и слабая затяжка анкерных болтов. Эти дефекты изменяют расчетную схему колонн, вызывают дополнительные моменты вследствие эксцентричного приложения нагрузок от подкрановых балок и элементов покрытия и могут привести к преждевременной потере устойчивости. Кроме того, отклонение колонн от проектного положения ухудшает работу элементов стенового ограждения и нарушает геометрию подкрановых путей, что может мешать их нормальной эксплуатации.
Повреждения колонн при эксплуатации связаны в основном с нарушениями правил технической эксплуатации (рис.1). В зонах проездов, складирования, работы кранов колонны часто подвергаются ударам транспортируемыми грузами, магнитными шайбами, грейферами и получают искривления и местные погибы. Особенно повреждаются гибкие элементы решетки и полки подкрановых ветвей. В стенках колонн устраиваются вырезы для пропуска коммуникаций без усиления ослабленных сечений. При опирании подкрановых балок на консоли колонн отмечались случаи обрыва консолей, вызванные усталостным разрушением швов их крепления. Недопустимо отношение к связям как к второстепенным элементам. Удаление и вырезка связей для пропуска коммуникаций приводит к изменению расчетной схемы зданий и сооружений, снижению пространственной жесткости, перераспределению усилий и может способствовать преждевременному выходу конструкций из строя.
Трещины в основном металле и в сварных швах стержня колонны наблюдаются редко. В отдельных случаях зафиксированы трещины в местах прикрепления подкрановых и тормозных балок в зданиях с кранами особо тяжелого режима работы.
Эти повреждения вызваны жестким креплением подкрановых конструкций к колоннам, появлением в местах креплений знакопеременного цикла напряжений и, как следствие, развитием усталостных трещин.
В зданиях, построенных на просадочных грунтах, наблюдаются значительные осадки и повороты фундаментов, что нарушает положение подкрановых путей и конструкций покрытия и может вызвать повреждение узлов их крепления.
В горячих цехах металлургических заводов колонны зданий и рабочих площадок подвергаются значительным температурным воздействиям. В результате разрушаются узлы крепления вертикальных связей; в элементах связей появляются трещины. Особенно значительные повреждения (искривления, деформация сечения, пережог) возникают при соприкосновении колонн с горячим металлом и шлаком.
Характерные повреждения колонн – отклонения от проектного положения как в плоскости, так и из плоскости рам. Учитывая большие запасы прочности в колоннах и не учитываемые расчетом связи, эти отклонения для несущей способности конструкций не представляют существенной опасности, однако они приводят к повреждениям элементов стенового ограждения, расстройству узлов сопряжения примыкающих конструкций, нарушению проектного положения подкрановых путей и тем затрудняют нормальную эксплуатацию здания.
Общие коррозионные поражения сплошных колонн и ветвей сквозных колонн сравнительно невелики вследствие большой мощности сечения, открытых профилей и вертикального расположения элементов, исключающего отложение пыли. В худших условиях находятся элементы решетки, ребра жесткости и диафрагмы из-за относительной тонкостенности сечения и возможности скопления пыли на горизонтальных поверхностях, что при увлажнении интенсифицирует коррозию.
Значительной местной коррозии подвергаются отдельные узлы и части колонн, особенно в случае соприкосновения их с грунтом, мусором, вблизи внутренних водостоков с неисправной гидроизоляцией, в местах возможных протечек технических жидкостей и т.д. К таким узлам относятся оголовки колонн, узлы опирания подкрановых балок и особенно базы колонн и узлы крепления вертикальных связей, расположенные ниже отметки пола и необетонированные. Периодическое увлажнение и воздействие агрессивных жидкостей в короткие сроки может привести к сквозному коррозионному поражению конструкций. Еще более значительно подвержены общим поражениям коррозией колонны наружных сооружений – открытых крановых и технологических эстакад, вследствие того, что выполнены они чаще всего сквозными из тонкостенных элементов, малой мощности сечений.
Подкрановые балки
Подкрановые конструкции промышленного здания включают подкрановые балки, тормозные балки или фермы, узлы креплений балок и тормозных ферм к колоннам, крановый рельс с креплениями и упоры. Подкрановые конструкции работают в наиболее сложных условиях, значительно отличающихся от работы обычных балок и уже через 2…3 года после начала эксплуатации в зданиях с кранами «особого» режима работы в подкрановых балках появляются первые повреждения: расстраиваются узлы крепления подкрановых и тормозных балок к колоннам, появляются усталостные трещины в сварных швах и в стенке около верхнего пояса балок, в клепаных балках ослабляются заклепки верхнего пояса и появляются трещины в уголках. Со временем эти повреждения развиваются и препятствуют нормальной работе кранов.
Основными факторами, способствующими развитию повреждений и снижающими долговечность подкрановых конструкций, являются интенсивность работы мостовых кранов и срок эксплуатации.
Наиболее значительно повреждаются подкрановые конструкции в цехах с кранами тяжелого и весьма тяжелого режима работы, особенно с жесткими грузозахватными механизмами. В зданиях же с кранами среднего и легкого режима работы повреждения встречаются значительно реже.
Основные факторы, способствующие появлению повреждений подкрановых конструкций:
- действие сосредоточенных подвижных нагрузок, достигающих 800 кН и носящих динамический характер;
- переменный и знакопеременный многократно повторяющийся цикл напряжений, вызывающий усталость металла;
- сложный характер напряженного состояния; жесткость узлов крепления подкрановых конструкций к колоннам и несоответствие их фактической работы принимаемой расчетной схеме;
- наличие дополнительных факторов, усложняющих работу конструкций, таких, как эксцентриситет приложения нагрузки, неравномерность давлений на колесах крана, неровности контактной поверхности рельса и пояса балки, сварочные напряжения и т.д.
Интенсивному развитию повреждений способствуют также дефекты и повреждения сварных швов и другие несовершенства изготовления и монтажа.
Одной из причин повреждения подкрановых конструкций является низкое качество сварных соединений.
Поясные швы, выполняемые автоматом, в нарушение требований норм на изготовление конструкций часто не доводятся до торцов балок на 150…400 мм и завариваются полуавтоматической или ручной сваркой. Низкое качество швов, выполненных вручную или полуавтоматом, создает дополнительную концентрацию напряжений. Глубина проплавления швов, даже выполненных автоматом, часто не превышает половины высоты шва, и по линии сопряжения стенки и пояса возникает непровар. Стыки поясов выполняются без выводных планок и имеют кратеры. Все эти дефекты уменьшают предел выносливости соединения и вызывают зарождение усталостных трещин. Монтаж подкрановых конструкций нередко выполняется с отклонениями от проектного положения, рельсы укладываются с эксцентриситетом, что вызывает дополнительные не учитываемые при расчете воздействия.
В швах крепления тормозных конструкций к балкам также встречается много дефектов и повреждений. Часто эти соединения выполняются прерывистыми швами, отсутствует подварка и т.д.
Наиболее характерными повреждениями сварных подкрановых балок являются: трещины в верхнем поясном шве и в стенке в околошовной зоне, трещины в швах крепления ребер жесткости к верхнему поясу, трещины в стенке под короткими ребрами жесткости, поперечные трещины в верхнем поясе, местные погибы верхнего пояса и ребер жесткости.
В балках с ребрами, имеющими вырез, трещины в стенке развиваются от конца выреза. Все трещины носят ярко выраженный усталостный характер и возникают под действием многократно повторяющейся местной нагрузки.
Трещины в нижнем поясе подкрановых балок встречаются крайне редко и возможны лишь при наличии существенных дефектов (например, непровары, кратеры, глубокие подрезы в стыках швов).
Местные прогибы верхнего пояса балок возникают от эксцентричного приложения местной нагрузки и поворота пояса. Иногда погибы пояса являются следствием потери местной устойчивости. Кроме того, при ремонте кранов на верхние пояса балок опирают домкраты для подъема крана, что также может вызвать местные повреждения.
Отсутствие остаточных сварочных напряжений, меньшая концентрация напряжений, утолщение верхней части стенки полками поясных уголков, податливость заклепочных соединений облегчают условия работы клепаных балок и делают их более долговечными. Повреждения в них возникают значительно позже, чем в сварных балках.
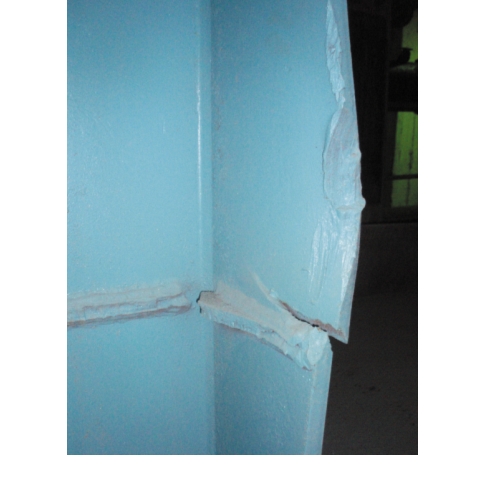
Основные виды повреждений клепаных балок: ослабление и разрушение заклепок верхнего пояса, продольные и поперечные трещины в верхних поясных уголках, местные погибы верхнего пояса. Повреждений в нижнем поясе, как и в сварных балках, практически не наблюдается.
В наиболее сложных условиях работают элементы решетчатых подкрановых балок, которые широко применялись в 50-х годах ХХ века в зданиях с тяжелым режимом работы. Наличие острых концентраторов напряжений в узлах, знакопеременный цикл напряжений в верхнем поясе приводят к ускоренному развитию повреждений усталостного характера. Трещины возникают в продольных швах верхнего пояса (аналогично сварным балкам) и в фасонках. Наблюдались случаи разрыва раскосов.
Основными причинами повреждений тормозных конструкций являются несоответствие действительной работы тормозных конструкций принимаемой расчетной схеме и появление дополнительных не учитываемых при проектировании усилий.
Совместная работа тормозной конструкции и подкрановой балки приводит к их косому изгибу с кручением и значительному увеличению касательных напряжений по сравнению с вычисленными по принятой методике расчета по расчлененным плоским схемам. Трещины в швах сопряжения тормозных конструкций и балок появляются чаще у опор, в местах вырезов для пропуска крючьев крепления рельса и у смотровых люков.
Неудовлетворительное качество приварки тормозных листов, отсутствие подварки, прерывистые швы способствует раннему появлению трещин. Часть повреждений тормозных конструкций связаны с грубыми нарушениями правил технической эксплуатации: складированием на тормозных площадках тяжелых грузов, вырезкой отверстий и отдельных элементов тормозных ферм и т.д.
Много повреждений возникает в узлах крепления подкрановых конструкций к колоннам. Это трещины и ослабление болтовых соединений в местах крепления тормозных конструкций и балок, повреждения элементов крепления, ослабление болтов взаимного соединения балок (рис. 2). Особенно часто повреждаются узлы разрезных балок с жесткими элементами (диафрагмами, горизонтальными накладками), препятствующими повороту и продольному перемещению опорных сечений балок. В немалой степени повреждения подкрановых конструкций зависят от состояния крановых путей: нарушение геометрии путей в плане и по вертикали вызывает дополнительные усилия, смещение рельса с оси балки способствует возникновению крутящего момента, неровности пути и повреждения стыков рельса увеличивают динамический характер нагрузки.
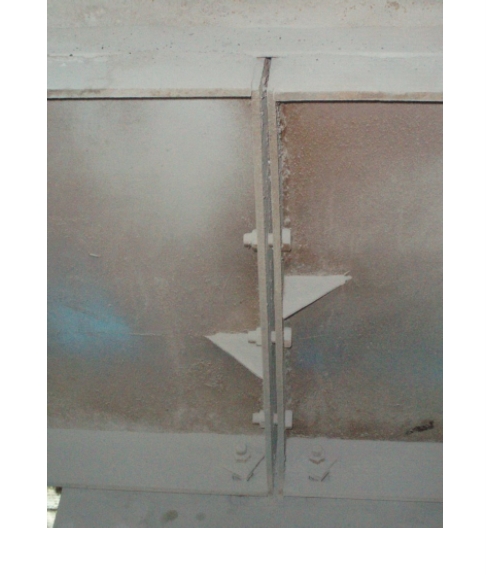
Повреждения подкрановых конструкций общей поверхностной коррозией незначительны благодаря мощности сечений и открытому, хорошо обдуваемому профилю. При обследованиях старых цехов иногда наблюдались отдельные очаги повышенной местной коррозии у опорных узлов, в местах крепления к балке тормозного листа, особенно при наличии в таких местах производственной пыли и атмосферной влаги. Это относится чаще всего к подкрановым балкам крайних рядов при плохом состоянии бокового остекления.
Из других повреждений балок путей следует отметить остаточные прогибы, которые возникают при подъеме грузов, превышающих грузоподъемность крана, отгибы полок балок, трещины и расстройство болтовых соединений в узлах крепления балок к вышележащим конструкциям.
Повреждения крановых упоров заключаются в ослаблении креплений, остаточных деформациях, а при сильных ударах – и в разрушении. Остановка крана при подходе к упору должна обеспечиваться концевыми выключателями и системой блокирования, обеспечивающими торможение.
Наиболее характерные повреждения крановых рельсов – износ верхних и боковых граней головки, повреждения рельсов в местах стыков и трещины в шейке рельса, что зависит от непараллельности путей и от перекоса колес крана. Необходимо подчеркнуть, что повреждения крановых рельсов и их креплений сильно сказываются на работе подкрановых конструкций и ускоряют появление в них повреждений.
Конструкции покрытия
К конструкциям покрытия относятся стропильные и подстропильные фермы, прогоны, фонари, горизонтальные связи и распорки. Основным типом стропильных конструкций эксплуатируемых промышленных зданий являются фермы с элементами из парных уголков. Наличие тонкостенных гибких стержней, сложная конфигурация сечений, повышенная концентрация напряжений в узлах делает эти конструкции весьма чувствительными к общим и местным перегрузкам, механическим, температурным и коррозионным воздействиям.
Важным фактором, определяющим состояние ферм, является качество их изготовления и монтажа. Существенно снижают надежность и долговечность стропильных ферм дефекты изготовления и монтажа. К ним относятся начальные искривления стержней ферм (до 15% элементов ферм уже на стадии изготовления имеют искривления, превышающие допустимые по нормам – основными причинами искривления элементов ферм являются недостаточная правка проката и влияние сварки при несимметричном наложении швов), дефекты сварных соединений (неполномерность швов, подрезы, незаваренные кратеры), расцентровка узлов и внеузловая передача нагрузки из-за смещения прогонов.
При изготовлении ферм нарушаются требования норм по ограничению минимального расстояния между торцами элементов решетки и поясами (40…50 мм). Это ухудшает условия работы фасонок и способствует появлению в них трещин. Пропуск соединительных прокладок в сжатых элементах ферм может привести к преждевременной потере ими устойчивости.
Много дефектов наблюдается в опорных узлах ферм.
Торцы опорных фланцев не имеют пристрожки, неплотно опираются на опорные столики, имеют перекосы; отсутствуют болты сопряжения фермы с колоннами и т.п.
При транспортировании и монтаже число поврежденных стержней и искривления возрастают. В процессе эксплуатации наблюдается дальнейший рост числа поврежденных элементов (более чем в два раза) и размеров искривлений. Преобладающими становятся искривления элементов из плоскости ферм (рис. 3).
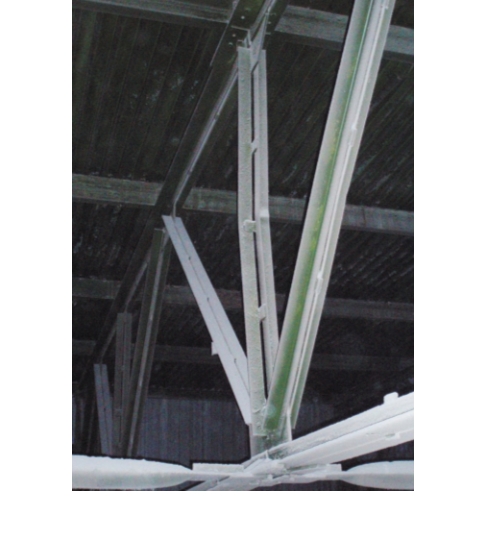
Кроме общих искривлений, частым повреждением элементов ферм являются местные погибы, возникающие при ударных воздействиях и креплении тросов для подвески грузов. Если в растянутых элементах эти повреждения не представляют существенной опасности, то в сжатых они могут привести к преждевременной потере устойчивости и, таким образом, снижают надежность конструкций.
Искривления нижних поясов ферм направлены из плоскости ферм, т.е. в направлении наибольшей гибкости. Помимо начальных искривлений при монтаже конструкций, причинами этого вида повреждений могут быть нагрев конструкций в горячих цехах и вызванные этим сжимающие усилия, а также горизонтальные усилия, возникающие из-за рамного момента, при частичном защемлении фермы на опоре. Появление этих дополнительных усилий связано с несоответствием конструктивной схемы расчетной, принятой при проектировании. Нередко повреждение нижних поясов вызвано такими грубыми нарушениями правил технической эксплуатации, как подвеска блоков для подъема грузов при ремонте и монтаже оборудования, внеузловое крепление трубопроводов, устройство площадок и проходных галерей и т.п. на элементах решетки ферм (решетка ферм работает на восприятие поперечной силы и выполняет функции стенки сплошной балки).
Из других дефектов монтажа следует отметить пропуск накладок и некачественное выполнение сварных швов в монтажных узлах, отклонение ферм от вертикальной плоскости, смещение узлов ферм относительно осей колонн, внеузловое опирание прогонов и плит. Наиболее серьезны дефекты монтажных узлов.
Смещение опорных узлов ферм относительно колонны, не оказывая влияния на работу ферм, приводит к появлению в колоннах дополнительных моментов, что должно быть учтено при расчете. Внеузловое опирание прогонов и плит вызывает изгиб поясов, в то же время, если точка приложения нагрузки не выходит за пределы фасонок, то дополнительные напряжения в поясах невелики и практически не снижают несущую способность ферм.
При креплении ферм к колоннам сбоку частыми дефектами монтажа являются такие, как перекос опорной поверхности фланца фермы и внецентренная передача нагрузки на опорный столик; зазор между фланцем и опорным столиком и «зависание» фермы на монтажных болтах; зазор между фланцем и колонной и малая площадь опирания фланца на опорный столик. Все эти дефекты искажают принятую при расчете схему работы опорного узла и приводят к перенапряжению его элементов. Особенно опасно отсутствие опорного столика и передача опорного давления фермы на колонну через нерасчетные монтажные болты.
Основными видами повреждений ферм, возникающих при эксплуатации, являются искривления и местные погибы элементов. Как и при изготовлении чаще повреждаются средние гибкие элементы решетки и большинство искривлений направлено из плоскости ферм. Среди причин, вызывающих искривления и местные погибы элементов при эксплуатации, следует выделить следующие:
- начальные несовершенства (искривления и местные погибы), возникающие при изготовлении и монтаже;
- нарушение правил технической эксплуатации (использование ферм для подвески блоков при ремонте оборудования, крепление коммуникации между узлами и т.д.);
- несоответствие фактической расчетной схемы принятой при проектировании (ужесточение опорных узлов ферм при шарнирной расчетной схеме, внеузловое опирание прогонов и плит, пропуск связей, закрепляющих сжатые пояса из плоскости ферм, и т.д.);
- перегрузка ферм;
- температурные воздействия в горячих цехах.
При работе ферм под нагрузкой начальные искривления сжатых элементов увеличиваются, а растянутых — уменьшаются, однако полного их исправления не происходит. Поэтому, если при обследовании выявлено, что количество искривленных сжатых и растянутых элементов приблизительно одинаково, то основной причиной их повреждений следует считать низкое качество изготовления и монтажа.
При подвеске блоков и креплении коммуникаций общие искривления часто сопровождаются местными погибами, а на элементах остаются следы крепления тросов.
Такие повреждения чаще встречаются в поясах ферм.
Ужесточение опорного узла ферм (увеличение толщины фланца, обварка узла) при шарнирной расчетной схеме приводит к появлению дополнительного не учитываемого расчетом опорного момента. Нижний пояс от горизонтальной составляющей оказывается сжатым и при большой гибкости теряет устойчивость. Нередко предусмотренные в проекте распорки по верхним поясам ферм в подфонарном участке пропускаются при монтаже или вырезаются в процессе эксплуатации. В результате увеличивается расчетная длина пояса из плоскости фермы, и он может потерять устойчивость.
Перегрузка ферм возникает при возрастании собственной массы покрытия (применение более тяжелых, чем принято в проекте, плит покрытия, увеличение толщины и утяжеление утеплителя и стяжки, наложение дополнительных слоев гидроизоляционного ковра и т.д.), подвеске дополнительных, не предусмотренных проектом коммуникаций и оборудования, отложений пыли на кровле, больших снегоотложений, превышающих расчетное значение снеговых нагрузок и образование снеговых мешков.
Трещины в фасонках и стыковых накладках ферм хотя и встречаются редко, тем не менее представляют одно из наиболее опасных повреждений. Их появление связано, как правило, с низким качеством материала (применение кипящих сталей, сильно загрязненных вредными примесями), наличием острых концентраторов (дефекты сварных швов, надрезы кромок и т.п.), предварительным пластическим деформированием металла в результате перегибов при кантовке ферм. В этих условиях трещина может возникнуть и при достаточно низких рабочих напряжениях (для кипящих сталей при 4…5 кН/см2).
Нередко трещины возникают еще во время изготовления и монтажа ферм. При эксплуатации конструкций при пониженной температуре (ниже критической для данной марки стали) или увеличении нагрузки трещины развиваются и могут привести к обрушению конструкций.
Расстройство болтовых соединений в опорных узлах ферм встречается довольно редко и связано в основном с повышенными динамическими воздействиями кранов.
Подстропильные фермы имеют достаточно мощное сечение элементов и повреждаются в значительно меньшей степени, чем стропильные.
Основным видом повреждений прогонов кровли являются остаточные прогибы, вызванные перегрузкой покрытий от чрезмерного скопления снега, пыли и превышения собственного веса покрытия по сравнению с проектом.
Особенно часты остаточные прогибы в местах перепада высот и у фонарей, т.е, в зонах образования снеговых мешков. Недостаточное раскрепление прогонов (удаление или провисание тяжей по прогонам, отсутствие элементов крепления кровельного настила и т.п.) приводит к искривлению их в плоскости ската.
Для конструкций фонарей наиболее частым повреждением является искривление раскосов стоечных фонарей с нисходящими раскосами. В соответствии с принимаемой расчетной схемой расчет раскосов выполняется в предположении их работы на растяжение. В то же время в нисходящем раскосе при достаточной жесткости его прикрепления в узлах от действия ветровой нагрузки возникает сжимающее усилие, что вызывает потерю их устойчивости.
Массовый характер носят повреждения связей по покрытию, особенно в зданиях, где эксплуатируются краны особо тяжелого режима работы. К наиболее частым повреждениям связей относятся искривления и местные погибы, удаление связей для пропуска коммуникаций, расстройство узлов крепления. При этом снижается пространственная жесткость каркаса, увеличивается расчетная длина сжатых поясов ферм, нарушается проектное положение конструкций. Особую опасность вызывает удаление или повреждение распорок по верхним поясам ферм в подфонарных участках, что может привести к потере устойчивости пояса и вызвать обрушение покрытия.
При малых зазорах между мостовыми кранами и конструкциями покрытия провисающие связи препятствуют нормальной эксплуатации кранов.
Опасным дефектом является недостаточная площадь опирания плит покрытия на стропильные фермы, что может привести к обрушению конструкций покрытия здания.
К грубым нарушениям требований монтажа относится также отсутствие приварки железобетонных плит к поясам ферм, так как при этом ухудшаются условия раскрепления поясов и увеличивается их расчетная длина.
Сложная конфигурация сечений, малые толщины проката, зазоры в элементах из парных уголков уменьшают коррозионную стойкость решетчатых элементов покрытия. Повышенная влажность воздуха, наличие агрессивных по отношению к металлу компонентов приводят к развитию равномерной коррозии элементов. Протечки кровли и стенового ограждения, выделение пара или конденсата из-за неисправностей стыков трубопроводов способствуют развитию местных коррозионных поражений. Особо интенсивные местные коррозионные поражения возникают в опорных узлах стропильных и подстропильных ферм, расположенных вблизи воронок внутренних водостоков, в верхних поясах ферм в местах опирания фонарей. Ускорению коррозии способствует скопление пыли на элементах конструкций, особенно в случае ее увлажнения. Наиболее высокая скорость коррозии элементов покрытия отмечается в производствах, связанных с агрессивными жидкостями, находящимися в открытых емкостях.
Большая площадь поверхности решетчатых конструкций, трудность доступа ко всем элементам, особенно к верхним поясам, затрудняет качественную подготовку и окраску их при эксплуатации. В результате уже через 2…3 года после дополнительной окраски защитные покрытия разрушаются и коррозионный процесс интенсифицируется.
При обследовании несущих металлоконструкций производственных зданий в первую очередь следует выявлять дефекты и повреждения, приводящие к снижению несущей способности конструкций или к ненадежности общей пространственной схемы обследуемого здания, для своевременного их устранения.