Авторы: Т.Д. Алеференко, А.Г. Александров, Е.А. Садовский (НПО «ЛЕНКОР-НЕФТЕХИМ»), А.Г. Аненко, А.В. Приходько, Ю.А. Иващенко (филиал ООО «Газпромнефть-СМ» «ОЗСМ»).
Опубликовано в журнале Химическая техника №7/2015
Оборудование установок деасфальтизации гудрона пропаном эксплуатируется при относительно невысоких температурах (для колонн рабочая температура составляет 80…90°С) и давлениях (до 5 МПа). Для такого оборудования известны случаи наводороживания металла в результате низкотемпературной сероводородной коррозии, при которой водород накапливается в мелких дефектах под большим давлением, что может приводить к образованию расслоений [1, 2].
В рамках данной работы были произведены вырезки темплетов диаметром 100 мм из колонны К-1 установки 36/1-1 и колонн К-1 и К-1а установки 36/1-3 (установка деасфальтизации гудрона пропаном). Исследование свойств металла после более чем 50-летней эксплуатации выполнено с целью получения дополнительной информации для оценки остаточного ресурса оборудования. В указанных колоннах методом УЗК зафиксировано наличие мелких дефектов типа неметаллических включений неизвестного происхождения, кроме того, полевая металлография на колонне К-1 установки 36/1-1 зафиксировала отсутствие перлитной составляющей стали (распад перлита обычно сопровождается падением прочностных свойств стали).
Методика вырезки темплетов
Вырезку темплетов и ремонтную заделку образовавшихся отверстий производили в основном согласно технологии, изложенной в регламенте [3], с небольшими доработками применительно к особенностям пропановых колонн.
Вырезка темплетов производилась путем высверливания электродрелью с помощью кондуктора (рис. 1).
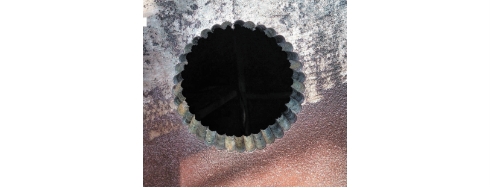
Ремонтная заделка образовавшегося отверстия включала:
- придание отверстию цилиндрической формы путем шлифовки;
- использование заглушки из того же металла, что и материал колонны (рис. 2);
- заварку заглушки и термообработку узла заделки (рис. 3).
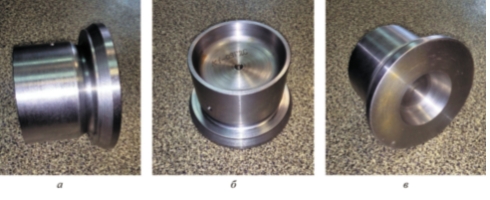
а – вид сбоку, б – вид со стороны хвостовика,
в – вид со стороны головки (монтируется с внутренней стороны аппарата)
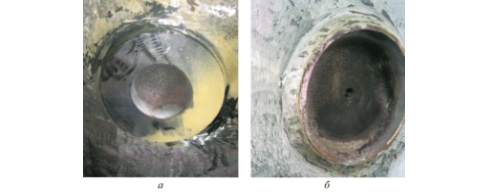
а – вид изнутри аппарата; б – вид снаружи аппарата
Использование технологии заделки с помощью заглушки имеет следующие преимущества:
- толщина заглушки практически совпадает с толщиной стенки обечайки;
- объем сварочных работ минимален – два кольцевых шва снаружи и внутри аппарата;
- предусмотрена возможность опрессовки (резьбовое отверстие под штуцер для данного типа оборудования в режиме эксплуатации заглушается болтом без заварки);
- отсутствуют застойные зоны для технологической среды.
Конструкция заглушки и узла заделки в целом обеспечивает достаточный запас по прочности. Имеется положительный опыт многолетней эксплуатации аппаратов с такими заглушками.
Вырезанные темплеты были разрезаны на слои толщиной 12…15 мм параллельно наружной поверхности аппарата. Из каждого слоя были изготовлены по 2…3 образца для испытаний на ударный изгиб и по 2…3 образца для испытания на растяжение. Темплет из колонны К-1 установки 36/1-3 удалось вырезать таким образом, что в его центре присутствовал зафиксированный УЗК дефект, идентифицированный как «неметаллическое включение «эквивалентной площадью» 4,2 мм2». Соответствующий фрагмент темплета был вырезан под контролем УЗК и разрез дефекта произведен перпендикулярно поверхности колонны (параллельно УЗ-лучу).
Исследования металла темплетов проводили с использованием следующего оборудования:
- испытания на на растяжение – испытательная машина Р-5;
- испытания на ударную вязкость – копер МК-30;
- металлография – световой металлографический микроскоп «Обсервер»; микротвердомер «Аффри» с пирамидой HV;
- содержание водорода – анализатор газообразующих примесей в металлах ONH-836-MC фирмы LECO;
- элементный состав стали (химический анализ, спектральный метод) – рентгенофлюоресцентный спектрометр INNOV-X SYSTEMS.
Характеристики колонн и полученные результаты
Установка | 36/1-1 | 36/1-3 | |
Колонна | К-1 | К-1 | К-1а |
Год изготовления/ год ввода в эксплуатацию | 1963/1965 | 1962/1963 | 1959/1960 |
Марка стали
обечайки и днищ |
09Г2ДТ (сталь М) | Ст22К | 09Г2ДТ |
Толщина стенки обечайки и днищ, мм | 63 | 63 | 46 |
Диаметр обечайки, мм | 2 800 | 2 800 | 2 400 |
Длина обечайки, мм | 12 500 | 12 500 | 15 852 |
Расчетная/рабочая температура корпуса, °С | 90/85 | 90/85 | 80/80 |
Расчетное/рабочее давление в корпусе, МПа | 4,5/4,2 | 4,5/4,2 | 5,5/4,0 |
Балл неметаллических включений по шкалам ГОСТ 1778 (металлография) | 5 | 3…4 | 3…4 |
Наличие фиксируемых УЗК неметаллических включений | Много | Единичные | Нет |
Предел прочности sв, МПа: | |||
минимальное измеренное значение | 494 | 500 | 510 |
требования ГОСТ 5520–79 | 440…600 | 440…600 | 440…600 |
разброс значений | 16 | 20 | 10 |
Условный предел текучести s0,2, МПа: | |||
минимальное измеренное значение | 236 | 280 | 260 |
требования ГОСТ 5520–79 | ≥ 270 | ≥ 270 | ≥ 270 |
разброс значений | 60 | 30 | 20 |
Ударная вязкость ан, Дж/см2: | |||
минимальное измеренное значение | 68 | 121 | 75 |
требования ГОСТ 5520–79 | ≥ 60 | ≥ 60 | ≥ 60 |
разброс значений | 64 | 67 | 18 |
Относительное удлинение δ, %: | |||
минимальное измеренное значение | 29 | 34 | 32 |
требования ГОСТ 5520–79 | ≥ 22 | ≥ 22 | ≥ 22 |
разброс значений | 6 | 4 | 2 |
Расчет отбраковочной
толщины Sотбр., мм |
40,6 | 32,6 | 26,9 |
Коэффициент Sфакт/Sотбр. | 1,55 | 1,93 | 1,71 |
Примечание. Sфакт – фактическая толщина стенки колонны. |
Содержание сероводорода в циркулирующем пропане составляло не более 0,42 ррм.
По результатам металлографического исследования шлифов вырезанных темплетов установлено следующее.
Структура металла всех колонн характерна для малоуглеродистых сталей ферритно-перлитного класса.
Согласно ТУ 159–59 на сталь 09Г2ДТ (сталь М) и ТУ 1–55 на сталь 22К фазовый состав металла и неметаллические примеси не нормируются. В металле колонны К-1 установки 36/1-1 фиксируется наличие феррита и структурно-свободного цементита, в остальных колоннах присутствуют феррит и перлит.
В металле всех колонн обнаружены хаотически распределенные мелкие включения оксидов и сульфидов (реже – силикатов); по действующим нормам металл всех колонн характеризуется невысоким металлургическим качеством – балл неметаллических включений по шкалам ГОСТ 1778 более 3.
Металлографические исследования фрагмента с зафиксированным УЗК неметаллическим включением показали наличие неметаллических включений, сосредоточенных в виде равноосных групп размером до 60 мкм, и отдельные частицы размером до 15 мкм строчечного вида (рис. 4).
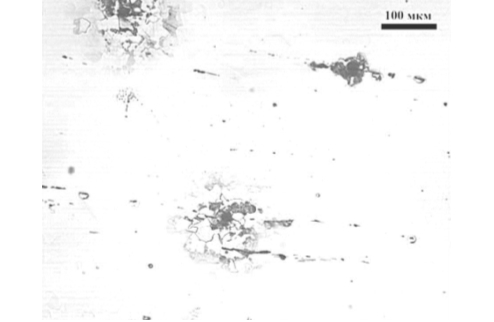
По полю шлифа включения распределены неравномерно. По морфологически признакам частицы классифицированы как оксисульфиды (оксиды в сульфидной оболочке). Вблизи наиболее крупных и недеформированных включений выявлены микротрещины межзеренного вида длиной до 10 мкм, ориентированные по направлению строчек.
В исследованном месте шлифа микротрещины единичны. На других участках микротрещины не обнаружены. Учитывая их ориентированность вдоль строчек частиц, можно полагать, что микротрещины образовались между недеформирующимися оксидами на этапе производства металлопроката.
Поскольку между выявленными группами включений расстояние невелико (~0,5 мм), можно полагать, что место их залегания и было определено при УЗК контроле стенки как «неметаллическое включение эквивалентной площадью 4,2 мм2». В металле колонн не зафиксировано каких-либо пузырей, блистеров, других признаков водородного повреждения металла вследствие низкотемпературной сероводородной коррозии. Общее утонение стенок колонн – менее 0,1 мм/год. Измеренное содержание водорода в металле – менее 1 ррm, что соответствует содержанию водорода в исходных сталях такого типа.
Механические свойства металла в целом соответствуют нормативным требованиям. Однако для колонны К-1 установки 36/1-1 зафиксировано, что для нескольких образцов (три из 12) σ0,2 меньше нормативного (236, 252 и 256 МПа при нормативном минимуме 270 МПа). В то же время среднее измеренное значение превышает установленный ГОСТ 5520–79 минимальный уровень. Кроме того, для этой колонны зафиксирован большой разброс (около 20%) измеренных значений σ0,2, а также минимальные значения ударной вязкости (превышающие нормативный уровень) и наибольший относительный разброс ее значений по сравнению с аналогичными характеристиками металла других колонн. Следует отметить, что приведены значения механических свойств образцов сталей разных марок, но одного класса, поэтому подобный сравнительный анализ, на наш взгляд, уместен.
Имеется определенная корреляция результатов металлографии, УЗК и измеренных механических свойств металла всех колонн. Максимальное количество неметаллических включений УЗК зафиксировал на колонне К-1 установки 36/1-1, где отмечены максимальный балл неметаллических включений по шкалам ГОСТ 1778, а также минимальные значения σ0,2 и ударной вязкости (разброс значений σ0,2 и ударной вязкости для этой колонны максимален). Это соответствует существующим представлениям о том, что рост концентрации мелких неметаллических включений должен приводить к падению пластичности и прочности металла. Неравномерность распределения неметаллических включений обусловливает полученный разброс механических свойств.
На основании минимальных измеренных значений σ0,2 рассчитаны отбраковочные толщины стенок обечаек.
Коэффициент запаса по прочности, определенный как отношение фактической толщины к отбраковочной, имеет минимальное значение для колонны К-1 установки 36/1-1 и составляет более 1,5.
На основании вышеизложенного можно заключить, что ослабление металла колонн неметаллическими включениями металлургического происхождения количественно отражено в измеренных значениях σ0,2.
Таким образом, можно считать установленным следующее.
Металл колонн, изготовленных в конце 50-х годов прошлого века, по действующим нормативным документам характеризуется невысоким металлургическим качеством – содержит заметное количество включений оксидов и сульфидов размером 20…60 мкм.
Зафиксированные УЗК неметаллические включения представляют собой совокупность мелких оксидов и сульфидов, расположенных на расстоянии друг от друга порядка 0,5 мм.
Механические свойства металла обеспечивают достаточный запас прочности колонн.
Реализуемые в рассматриваемом оборудовании параметры технологического процесса (деасфальтизация гудрона пропаном) обеспечивают отсутствие скольнибудь заметной сероводородной коррозии металла колонн. Содержание водорода в металле менее 1 ррm, что соответствует содержанию водорода в исходных сталях такого типа. Водородное повреждение металла вследствие низкотемпературной сероводородной коррозии отсутствует.
Признаков какой-либо деградации металла после более 400 000 ч эксплуатации колонн не зафиксировано.
Наличие недопустимых по действующим сейчас нормам неметаллических включений в металле, изготовленном в конце 1950-х годов, компенсировано имеющимися запасами по прочности.
Список литературы
- Коррозия и защита химической аппаратуры. Т. 9. Нефтеперерабатывающая и нефтехимическая промышленность/Под ред. А.М. Сухотина, А.В. Шрейдера, Ю.И. Арчакова. Л.: Химия, 1974.
- Коррозионная стойкость оборудования химических производств. Нефтеперерабатывающая промышленность/Под ред. А.М. Сухотина, Ю.И. Арчакова. Л.: Химия, 1990.
- 3. ТУ-Регламент по эксплуатации и обследованию оборудования установок каталитического риформинга и гидроочистки, работающих в водородосодержащих средах при повышенных температуре и давлении. СПб.:1998.