Автор: А.А. Воробьев (ОАО «НИИК»)
Опубликовано в журнале Химическая техника №6/2017
В статье изложена информация о реконструкциях, выполненных ОАО «НИИК» за последние два года. Как известно, при расширении любого производства, в том числе и производства карбамида, необходимо принять решение о том, будет это происходить в результате строительства нового производства или в результате реконструкции существующих агрегатов.
По нашему опыту, целесообразность реконструкции обоснована с учетом поставленной цели по увеличению производительности. Эффективность капитальных вложений в реконструкцию имеет нелинейный характер. Она растет до определенного повышения производительности, а затем начинает падать. Это связано с тем, что для повышения мощности более 150% проектной необходима замена основного оборудования – аппаратов высокого давления, насосов высокого давления, компрессора диоксида углерода и др. В этом случае производить замену оборудования среднего и низкого давлений уже не имеет смысла, так как количество возвратного карбамата возрастает настолько, что энергозатраты увеличиваются непропорционально высоко.
Исходя из этого каждый агрегат карбамида имеет определенный резерв по его реконструкции с повышением мощности и снижением удельных энергозатрат. И, по нашему мнению, данный резерв необходимо использовать, так как такое вложение средств оптимально при желании относительно небольшого наращивания мощности.
ОАО «НИИК» при реконструкции учитывает три основных момента – повышение производительности, снижение энергопотребления и повышение экологичности производства. Институт, имея большой опыт работы со всеми основными схемами производства карбамида, готов предложить оптимальные решения для таких реконструкций.
Рассмотрим первый проект.
Реконструкция агрегатов №1–4 цеха карбамида ПАО «Акрон». Задачей проекта, задуманного в 2010 г., было увеличение производительности агрегатов №1–4 до 2000 т/сутки. Это был довольно амбициозный план, с учетом того, что проектная производительность этих четырех агрегатов составляла 1080 т/сутки. Фактически необходимо было получить агрегаты, работающие на нагрузке, в 2 раза превышающей проектную. К моменту реализации проекта нагрузка после частичной реконструкции цеха составляла 1300…1400 т/сутки, что сделало возможным выполнить задачу эффективно с точки зрения капитальных вложений.
Кроме того, при таком серьезном повышении производительности должны также снижаться и расходные коэффициенты по энергетике. Основные этапы данной работы:
- 2010 г. – проведение технологического обследования;
- 2011–2016 гг. – разработка технических решений, проектной и рабочей документации;
- 2016–2017 гг. – изготовление оборудования по этапу 1 (увеличение производительности до 1800 т/сутки), реализация проекта на площадке заказчика;
- 2017 г. – пусконаладочные работы после модернизации, гарантийные испытания после реализации этапа 1;
- 2018 г. … – реализация этапа 2 с увеличением производительности до 2000 т/сутки и снижением энергозатрат.
В качестве концепции реконструкции этих агрегатов с полным жидкостным рециклом была выбрана технология URECON®2006 разработки ОАО «НИИК» (рис. 1).
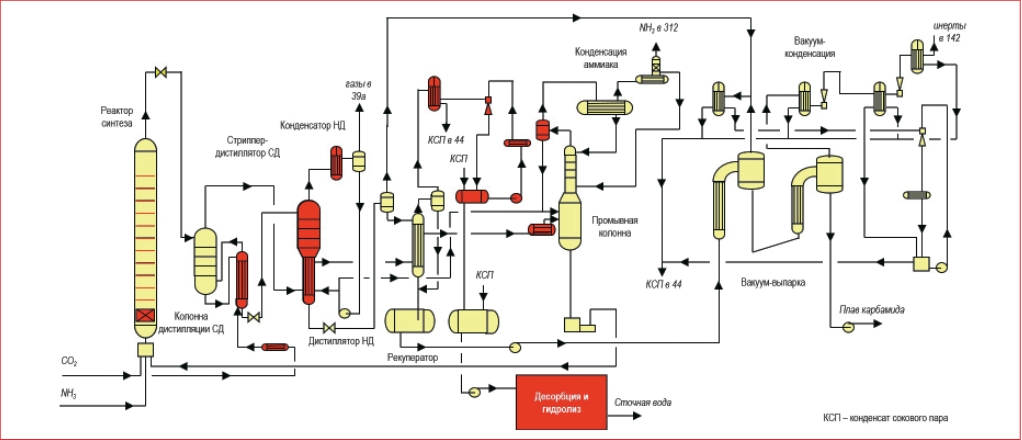
В колоннах синтеза установлены комплекты внутренних устройств конструкции ОАО «НИИК». Зоны смешения там, где это возможно, оборудованы вихревыми смесителями, обеспечивающими наилучшие условия смешения исходного сырья и исключающие образование мертвых зон в нижней части колонны синтеза. Зона образования карбамата оснащена специально разработанной ОАО «НИИК» насадкой продольного секционирования. Установлены насадки усовершенствованного типа, оборудованные специальными элементами – гидродинамическими генераторами, позволяющими получить минимальный размер пузырей в насадке для наиболее быстрого проведения реакции получения карбамата аммония. Зона образования карбамида в колоннах оборудована массообменными тарелками. Внутренние устройства в колоннах синтеза карбамида позволяют максимально уменьшить падение эффективности работы колонны синтеза при повышении нагрузки.
Заменены подогреватели колонн дистилляции первой ступени стрипперами-дистилляторами. Повышение степени разложения карбамата аммония и увеличение отгонки неконвертированных аммиака и СО2 из плава в токе СО2 под давлением 1,8 МПа снижает газовую нагрузку в узлах дистилляции II ступени и абсорбции, уменьшает количество аммиачной воды. Все это приводит к возможности повысить нагрузку на узел дистилляции и снижению энергозатрат.
В узле дистилляции низкого давления устанавливается один аппарат – дистиллятор низкого давления, объединяющий три аппарата: колонну дистилляции, подогреватель и сепаратор II ступени дистилляции. Предлагаемая конструкция дистиллятора низкого давления имеет небольшие размеры и существенно уменьшает число трубопроводов в узле дистилляции низкого давления.
Разложение карбамата и отгонка аммиака происходят за счет тепла конденсации газов дистилляции среднего давления. Кроме газов дистилляции в межтрубное пространство подогревателя подается также раствор УАС 2-й ступени для лучшей конденсации газов.
Система водоструйного эжектора позволяет надежно и стабильно поддерживать необходимую глубину вакуума в узле форвыпарки, где установлены рекуператоры тепла газов дистилляции.
Кроме основных технологических решений пристальное внимание было уделено и таким важным вещам, как выбросы в атмосферу и жидкие стоки за пределы агрегата. Разработаны решения по модернизации узлов абсорбции отходящих газов с последующим их кислотным улавливанием, а также по установке нового современного узла очистки сточных вод с двухзонными десорбером и гидролизером и рядом рекуперативных теплообменников.
Для облегчения нагрузки на бюджет предприятия реконструкцию решено было проводить в два этапа. Вначале необходимо было обеспечить производительность четырех агрегатов 1800 т/сутки, а после выполнения второго этапа – 2000 т/сутки.
Первый этап включал установку КВУ в колонны синтеза, стрипперов-дистилляторов с подогревателями диоксида углерода и замену конденсаторов-барботеров среднего давления новыми улучшенной конструкции с увеличенной площадью поверхности.
Второй этап предполагает установку дистилляторов низкого давления, конденсаторов низкого давления, конденсаторов форвыпарки, системы водоструйного эжектора и осуществление экологических мероприятий.
На текущий момент был успешно завершен первый этап данной реконструкции. Получена производительность 1800 т/сутки (450 т/сутки с каждого из четырех).
При проведении гарантийных испытаний было отмечено наблюдавшееся несколько раз нарушение температурного режима в промывных колоннах, что требует повышенного внимания; проблема будет полностью устранена после реализации второго этапа реконструкции.
Как видно, из-за большого повышения мощности относительно проектной реконструкция достаточно масштабная и включает в том числе и закупку дорогостоящего оборудования. Однако вследствие того, что она достаточно серьезно растянута во времени, окупаемость капитальных вложений находится на приемлемом уровне. При этом следует отметить, что замена насосно-компрессорного оборудования потребовалась бы в любом случае по причине его морального и физического износа.
ОАО «НАК «Азот» – реконструкция 2-й очереди цеха Карбамид 3. Агрегат работает по схеме Stamicarbon, проектная производительность 1100 т/сутки (модер-низирована ОАО «НИИК» до 1150 т/сутки). На момент до реконструкции агрегат работал на производительности до 1300 т/сутки. Задачей данного проекта было повышение мощности до 1450 т/сутки.
Реконструкция проводилась двумя компаниями. Фирма Casale реконструировала узел синтеза по своей технологии с затопленным карбаматным конденсатором
и системой эжекторов; НИИК – узлы дистилляции и рецикла. Применяемые решения, включая реконструкцию узла синтеза, относительно малозатратны, и повышение производительности еще на 150 т/сутки в данном случае было полностью оправдано. Общее повышение производительности относительно проектной составляет 32%. Для агрегата, работающего по технологии стриппинг-процесса в токе СО2, – это отличный результат, так как известно, что работа узла синтеза таких агрегатов сильно зависит от довольно капризной гидравлики потоков, которая при повышении нагрузки препятствует нормальной работе узла.
и системой эжекторов; НИИК – узлы дистилляции и рецикла. Применяемые решения, включая реконструкцию узла синтеза, относительно малозатратны, и повышение производительности еще на 150 т/сутки в данном случае было полностью оправдано. Общее повышение производительности относительно проектной составляет 32%. Для агрегата, работающего по технологии стриппинг-процесса в токе СО2, – это отличный результат, так как известно, что работа узла синтеза таких агрегатов сильно зависит от довольно капризной гидравлики потоков, которая при повышении нагрузки препятствует нормальной работе узла.
Основные этапы данной работы:
- 2011 г. – проведение технологического обследования;
- 2013–2014 гг. – разработка технических решений, проектной и рабочей документации;
- 2015–2016 гг. – изготовление оборудования, реализация проекта на площадке заказчика;
- 2016 г. – пусконаладочные работы после модернизации, гарантийные испытания.
В концепции реконструкции зоны ответственности НИИК – распределение раствора карбамида в стриппере, дистилляция среднего давления, рекуперация тепла перед узлом выпаривания, насосное оборудование высокого давления.
Примененные технические решения:
- изменение рабочей схемы скруббера-охладителя СО2 на всасывании компрессора с прямоточной на противоточную; установлен дополнительный ряд форсунок; для предотвращения уноса влаги предусмотрены новые демистеры;
- замена распределительного устройства плава в верхней камере стриппера высокого давления (ВД) для повышения эффективности его работы за счет более равномерного распределения жидкости и газа по теплообменным трубкам и сохранения степени отгонки избыточного аммиака из раствора карбамида на приемлемом уровне;
- для снижения нагрузки на узел дистилляции низкого давления (НД) произведена установка подогревателя и сепаратора под давлением 0,6…0,8 МПа последовательно после стриппера ВД. Подогреватель греется паром НД из карбаматного конденсатора ВД. Газы после дросселирования подаются в существующий конденсатор НД. Газы дистилляции из колонны дистилляции НД подаются во вновь устанавливаемый конденсатор НД. Газожидкостная смесь возвращается в существующий конденсатор НД. Эти решения позволяют кроме прочего снизить нагрузку на узел десорбции и гидролиза, а также исключить замену колонны дистилляции НД;
- установка предварительного подогревателя узла выпаривания. В качестве теплоносителя в подогревателе используется циркуляционный конденсат из контура охлаждения скруббера ВД, что позволяет снизить тепловую нагрузку на холодильник скруббера ВД.
- модернизация существующих аммиачных и карбаматных насосов ВД.
Осенью прошлого года были проведены гарантийные испытания. И здесь возникли трудности. Удалось достичь производительности лишь 1320 т/сутки. Работа узлов «НИИК» не вызвала нареканий. В каждом из них существовал запас по повышению нагрузки на него – узел охлаждения диоксида углерода, подогрев раствора карбамида перед дистиллятором НД, стабильное поддержание уровня в сепараторе СД, рекуперация тепла контура охлаждения скруббера ВД (запас по температурам обоих потоков рекуператора). Были лишь вопросы по нестабильному поведению дополнительного конденсатора газов дистилляции низкого давления.
Однако самой серьезной проблемой стала нестабильная работа узла синтеза и стриппера ВД при повышении нагрузки на них. Уровень раствора в реакторе синтеза начинал неконтролируемо возрастать, работа стриппера ухудшалась, температура его низа резко увеличивалась, что отражалось на работе узлов дистилляции и дестабилизировало работу всего агрегата.
После анализа возможных причин, среди которых рассматривалась и работа распределительного устройства раствора, специалистами «НИИК» было решено, что необходимы дополнительные решения по узлу синтеза карбамида, так как очевидно, что гидравлика потоков в нем после затопления карбаматного конденсатора стала еще менее устойчивой и непредсказуемой, чем по проектной схеме. НАК «Азот» проведет дополнительные работы в этом направлении с фирмой-разработчиком, и после чего будут проведены гарантийные испытания на нагрузке 1450 т/сутки.
RCF, Trombay, Индия – установка КВУ в реактор синтеза карбамида. В 2016 г. были установлены внутренние устройства в реакторе синтеза карбамида на установке RCF. Агрегат производительностью до 1300 т/сутки работает по технологии Snamprogetti. В первую очередь при реконструкции индийские компании интересует не увеличение мощности агрегата, а экономия энергоресурсов. Таким образом, главной задачей данного проекта было получение экономии пара среднего давления, потребляемого агрегатом карбамида на его границе.
Как известно, КВУ конструкции «НИИК» оказывают положительное влияние на эффективность работы реактора синтеза. Повышается степень конверсии диоксида углерода в карбамид, снижается количество возвращаемых в синтез непрореагировавших веществ. В состав поставляемых КВУ вошли вихревой смеситель и насадка продольного секционирования. В качестве гарантийного показателя выступила экономия пара 2,4 МПа на 75 кг/т готового продукта.
RCF были также поставлены условия о том, что внутренние устройства не окажут негативного влияния в первую очередь на компрессор диоксида углерода (отсутствие увеличения сопротивления линии подачи в реактор синтеза), а также на насосы подачи аммиака ВД.
Изготовление оборудования проводилось на российских заводах, установка проводилась нашим подрядчиком в Индии – фирмой Shiv Engineering, вместе
с которой в 2014 г. уже был установлен вихревой смеситель в NFCL.
с которой в 2014 г. уже был установлен вихревой смеситель в NFCL.
Предгарантийные испытания проводились в весеннее время при нагрузке 1080 т/сутки. Затем были проведены гарантийные испытания после пуска агрегата после капитального ремонта уже в летнее время года. И здесь специалисты столкнулись с рядом особенностей. Компания просила не работать на пониженной нагрузке, так как это приводит к потере выработки и прибыли. На данной нагрузке показать гарантированное значение экономии пара не удалось. Параметры работы агрегата существенно отличались от тех, что были при предгарантийных испытаниях. Второй этап испытаний был проведен при нагрузке 1080 т/сутки, но в очень жаркий период времени. Невозможно было выдержать необходимые значения температуры охлаждающей воды, что приводило к ухудшению работы узлов дистилляции низкого давления и выпаривания, что, в свою очередь, влияло на потребление пара 2,4 МПа в узле синтеза. Подтвердить экономию пара опять не удалось. ОАО «НИИК» и компанией RCF было решено проводить испытания в тот же период времени года, что и предгарантийные, чтобы все параметры работы агрегата были одинаковыми.
Третий этап испытаний был проведен в весеннее время, и были соблюдены все идентичные предгарантийным условия работы агрегата. Без каких-либо проблем гарантийный показатель был подтвержден и даже превысил гарантийное значение.
Из положительных результатов работы можно отметить:
- увеличение степени конверсии CO2 на 1,8%;
- увеличение содержания карбамида в растворе после реактора синтеза на 2,0%;
- экономию пара СД: достигнутая – 78,4 кг/т, гарантированная – 75 кг/т;
- снижение нагрузки на карбаматные насосы ВД с 101…102 до 95…96 об/м (уменьшение степени открытия клапана на подаче с 72,8% до 66,1%);
- уменьшение степени открытия клапана на подаче пара в дистиллятор НД с 51,2% до 37,0%.
В настоящее время в стадии обсуждения, проектирования и реализации находятся следующие проекты.
ПАО «Акрон» – расширение производства. Планы ПАО «Акрон» включают как реконструкцию действующих агрегатов, так и создание новых производств карбамида. Как уже было сказано, рассматривается реализация второго этапа реконструкции агрегатов №1-4.
Также в настоящее время при участии ОАО «НИИК» ведется проработка реконструкции агрегата №5 с повышением производительности до 1250 т/сутки и последующей возможностью увеличения ее до 1400…1500 т/сутки. Данный агрегат изначально располагался в Манфредонии, Италия. Проектная производительность – 900 т/сутки. ОАО «НИИК» была сделана не только привязка данного агрегата к российским условиям, но и его модернизация с повышением производительности до 1000 т/сутки – выполнена схема с частичной подачей диоксида углерода в стриппер, чего нет ни в одной применяемой на текущей момент схеме.
После выявления проблем с вертикальными карбаматными конденсаторами ОАО «НИИК» была предложена и реализована реконструкция узла синтеза с установкой одного большого горизонтального карбаматного конденсатора, а также рядом других мероприятий по улучшению работы агрегата. В итоге в настоящее время максимальная мощность агрегата составляет 1100 т/сутки.
Технические решения для реализации повышения нагрузки до 1250 т/сутки с учетом проведенной реконструкции узла синтеза достаточно просты и малозатратны. В расходы будут отнесены и затраты на замену карбаматных и аммиачных насосов ВД, но эта замена производится с учетом дальнейшего увеличения нагрузки до 1400…1500 т/сутки. Кроме того, в этом случае понадобится замена стриппера высокого давления и ряда других насосов.
Начаты работы по созданию новой установки производства раствора карбамида – агрегата №6. Планируется использовать существующую резервную колонну синтеза и на ее основе построить агрегат мощностью 600 т/сутки. Выбранная технология – URECON®2006, которая будет реализована в полной мере – единые аппараты дистилляции первой и второй ступеней, рекуперация тепла, водоструйный эжектор и абсорбция газов среднего давления.
После выполнения всех планов по расширению производства карбамида с учетом минимально возможных капитальных затрат производительность по раствору карбамида составит 3850 т/сутки, из которых 2240 т/сутки – в твердой форме. При этом старые производства будут работать при современном уровне энергопотребления, а выбросы и стоки будут соответствовать всем жестким требования.
АО «ФосАгро Череповец». На стадии выполнения находится проект по увеличению мощности ЦПМ №2 до 1650 т/сутки (рис. 2). Агрегат работает по схеме Stamicarbon, проектная производительность – 1200 т/сутки. На данный момент агрегат работает на нагрузке 1450 т/сутки.
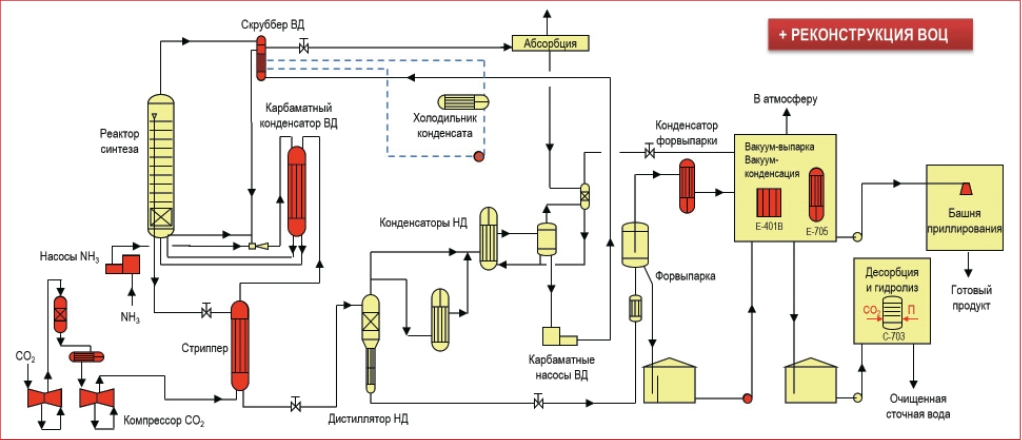
Примененные технические решения ОАО «НИИК»:
- для снижения содержания горючих в исходном диоксиде углерода устанавливается узел выжигания горючих между второй и третьей ступенями компрессора. Модернизацию компрессора диоксида углерода с увеличением производительности осуществляет заказчик;
- модернизация существующих аммиачных насосов ВД;
- с учетом плохого состояния аппаратов ВД узла синтеза предусматривается замена карбаматного конденсатора, стриппера и скруббера. Стриппер согласно патенту ОАО «НИИК» оснащается высокоэффективным распределительным устройством конструкции ОАО «НИИК», применяется распределенный ввод пара в межтрубное пространство. Карбаматный конденсатор поз. Е-202 также выполняется с применением ноу-хау ОАО «НИИК». Конструкция распределительного устройства обеспечит равномерное распределение газовой фазы по теплообменным трубам аппарата. Скруббер поз. Е-203 заменяется аналогичным.
Кроме того, замене подлежат:
- насос раствора карбамида, подающий его в узел вакуум-выпаривания;
- конденсатор форвыпарки (на больший по поверхности), существующий конденсатор заменяет концевой конденсатор узла вакуум-выпаривания;
- секция теплообмена первой ступени вакуум-выпаривания (секцией с увеличенной площадью поверхности).
- в гидролизере устанавливается дополнительный барботер пара для более равномерного распределения тепла;
- виброгранулятор в башне приллирования (новый увеличенной производительности);
- насос циркуляционного конденсата, охлаждающего скруббер ВД.
Немаловажную роль в реконструкции будет играть увеличение производительности существующего ВОЦ, так как его настоящих мощностей не хватит для обеспечения охлаждения технологического оборудования агрегата.
ОАО «НАК «Азот». Техническое перевооружение цеха Карбамид 2 с увеличением суммарной мощности до 1500 т/сутки. Три агрегата работают по схеме Stamicarbon с полным жидкостным рециклом, проектная производительность каждого 270 т/сутки (модернизированы ОАО «НИИК» до 400 т/сутки каждый). На данный момент производительность по узлам синтеза и дистилляции трех агрегатов достигает 1350 т/сутки.
Примененные технические решения ОАО «НИИК»:
- замена подогревателя аммиака перед колонной синтеза кожухотрубчатым;
- замена стриппер-дистиллятора новым увеличенной площадью поверхности теплообмена;
- замена колонны дистилляции НД новой увеличенного объема (конструкция ОАО «НИИК»), исключающей унос жидкой фазы. Применяются тарелки особой конструкции;
- замена виброприллера новым с двумя корзинами. Замена насоса в ванной очистного устройства;
- в узле очистки сточных вод: замена десорбера первой ступени увеличенным с массообменными тарелками конструкции ОАО «НИИК»; модернизация гидролизера с увеличением высоты, установкой дополнительных тарелок и отводом газовой фазы в десорбер первой ступени; замена тарелок в десорбере второй ступени тарелками конструкции ОАО «НИИК», рассчитанными на увеличенную производительность; установка дополнительных подогревателей десорбера первой ступени и гидролизера, холодильника очищенной сточной воды; замена насосов десорбера первой ступени и гидролизера.
Как видно, производители карбамида до сих пор зачастую идут по пути реконструкции для того, чтобы реализовать весь потенциал своих агрегатов. Вложение средств в реконструкции с повышением мощности до 130–150% проектной вполне оправданы. Они позволяют с минимальными затратами получить довольно быстрый результат. Разработка проекта модернизации и реконструкции значительно проще, чем для нового производства. Изготовление и поставка оборудования осуществляются, как правило в течение одного года. Все работы по реконструкции реализуются в рамках планового капитального ремонта.
ОАО «НИИК» предлагает всем производителям использовать полностью потенциал своих агрегатов. Этот процесс можно вести параллельно со строительством новых производств. Реконструкция при соблюдении определенных условий – всегда выгодное предложение.