Автор: Ю.А. Бадьин (АО «ВНИКТИнефтехимоборудование»)
Опубликовано на портале «Химическая техника», июнь 2021
Аннотация. Статья посвящена теме обеспечения промышленной безопасности сосудов со сжиженными углеводородными газами. Изложение ведется на основе анализа случая аварии на одном из промышленных предприятий. Анализируется нормативно-техническая база для такого оборудования. Формулируются рекомендации по дополнительным требованиям при техническом диагностировании такого оборудования.
ВВЕДЕНИЕ
Среди сосудов, эксплуатирующихся под давлением, значительное место занимают сосуды с рабочей средой в виде сжиженных газов. Для такого оборудования в ходе работ по техническому диагностированию и экспертизе промышленной безопасности предъявляются требования в соответствии с требованиями действующих нормативно-технических документов, определяющих периодичность, виды и объем работ по техническому диагностированию в ходе эксплуатации [1–4]. Поскольку существующие НТД не выделяют сосуды с рабочей средой в виде сжиженных газов среди других сосудов под давлением, дополнительные требования к такому оборудованию не предъявляются. Однако такое оборудование имеет специфические особенности, которые необходимо учитывать при эксплуатации, реконструкции и проведении работ по техническому диагностированию. Непринятие во внимание особенностей может привести к недопустимому снижению требований по обеспечению промышленной безопасности, что может вызвать возникновение аварий. Примером этому может служить случай, имевший место на одном из химических предприятий.
ОПИСАНИЕ ОБЪЕКТА ИССЛЕДОВАНИЯ
Сосуд использовался в качестве сборника жидкого ацетилена производства в технологическом процессе. Схема сосуда приведена на рис. 1.
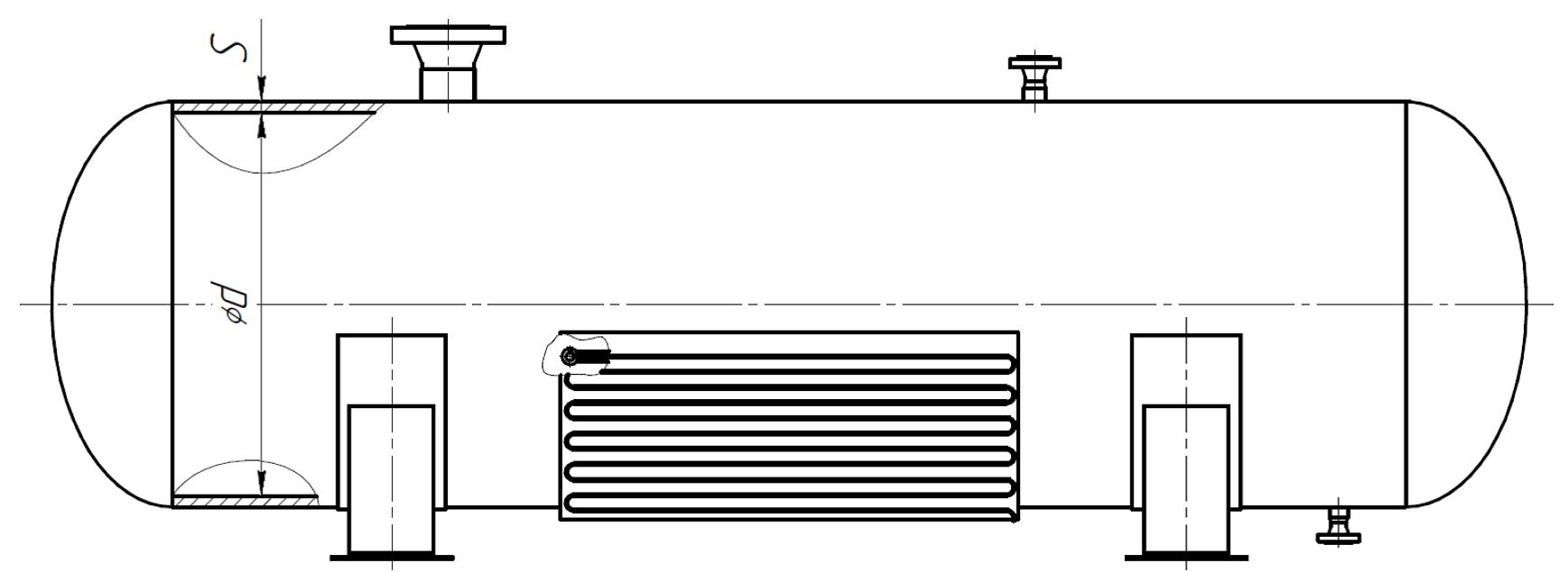
Технические данные сосуда
Сосуд в ходе эксплуатации был оснащен наружным подогревателем для испарения углеводородных фракций с более высокой температурой кипения. Также сосуд был оснащен предохранительным клапаном с необходимым резервным клапаном.
Сосуд эксплуатировался с 1966 г., периодически производились экспертизы промышленной безопасности, последний раз – в 2018 г, срок дальнейшей эксплуатации был продлен до 2026 г.
В ходе эксплуатации произошел разрыв емкости сжиженных углеводородных газов. Фото фрагментов корпуса после разрушения показаны на рисунках 2, 3.
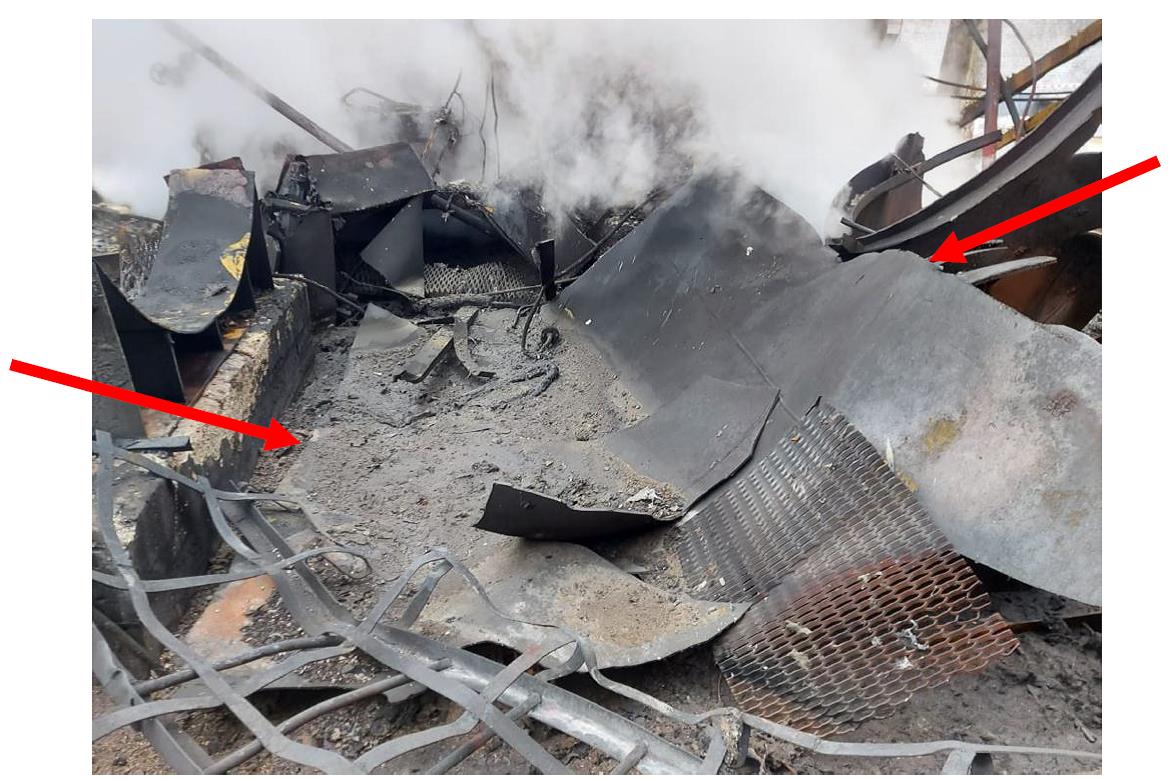
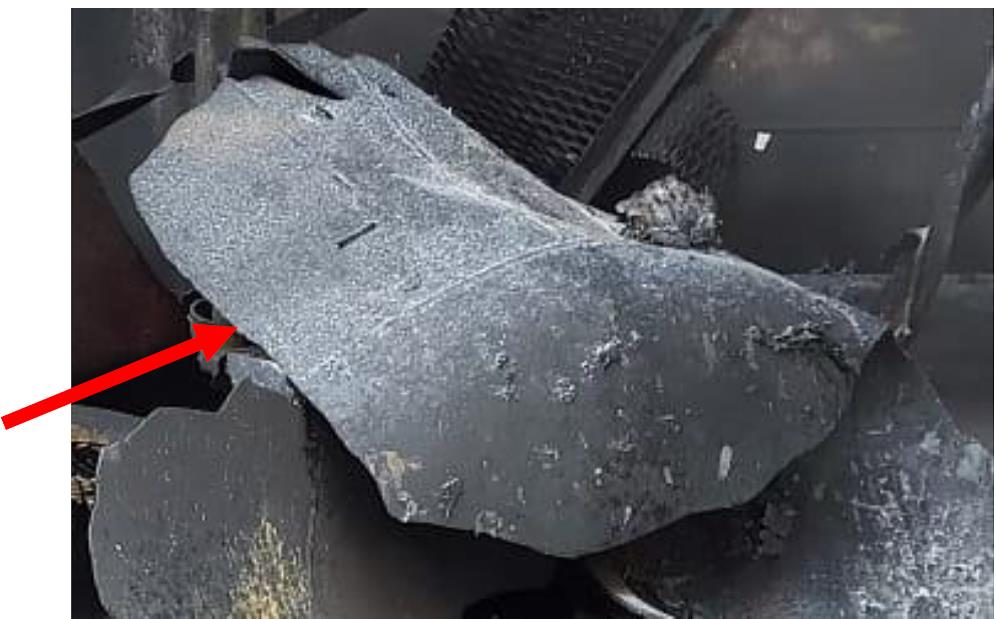
РАСЧЕТ НА ПРОЧНОСТЬ СОСУДА
Согласно указаниям действующих нормативно-технических документов, определяющих требования к проведению расчетов на прочность сосудов под давлением, если в ходе эксплуатации температура стенки поднимается до температуры среды, соприкасающейся со стенкой, то за расчетную температуру принимается наибольшая температура среды в сосуде, но не менее 20 оС. Расчетное давление для сосуда принимается, как правило, равным рабочему давлению или выше. При этом при назначении расчетного давления необходимо учитывать нестабильность перерабатываемых сред или технологического процесса [2]. На основании указанных требований были приняты расчетные температура и давление в сосуде tp = 30 oC, рp = 0,6 МПа и проведен расчет на прочность сосуда для определения минимально допустимой (отбраковочной) толщины стенки.
Расчетная толщина цилиндрического корпуса сосуда определяется по известной формуле [4]
В соответствии с требованиями [4] минимальная допустимая толщина стенки цилиндрического корпуса сосуда увеличивается до 4,0 мм.
За время длительной эксплуатации корпус сосуда подвергся изнашиванию, и минимальная измеренная толщина стенки составила 5,1 мм. Поскольку фактическая остаточная толщина стенки превышала минимальную допустимую (отбраковочную) толщину стенки, был сделан вывод, что имеется возможность дальнейшей эксплуатации сосуда.
ПРИЧИНЫ РАЗРУШЕНИЯ СОСУДА
Парциальное давление сжиженных газов с низкой температурой кипения очень сильно зависит от температуры. Сжиженные газы имеют особенность в виде возможности значительного увеличения внутреннего давления в сосуде в ходе повышения температуры от температуры сжижения до температуры окружающей среды.
Например, в зависимости от температуры и давления ацетилен может существовать в газообразном, жидком и твердом состоянии (рис. 4) [5].
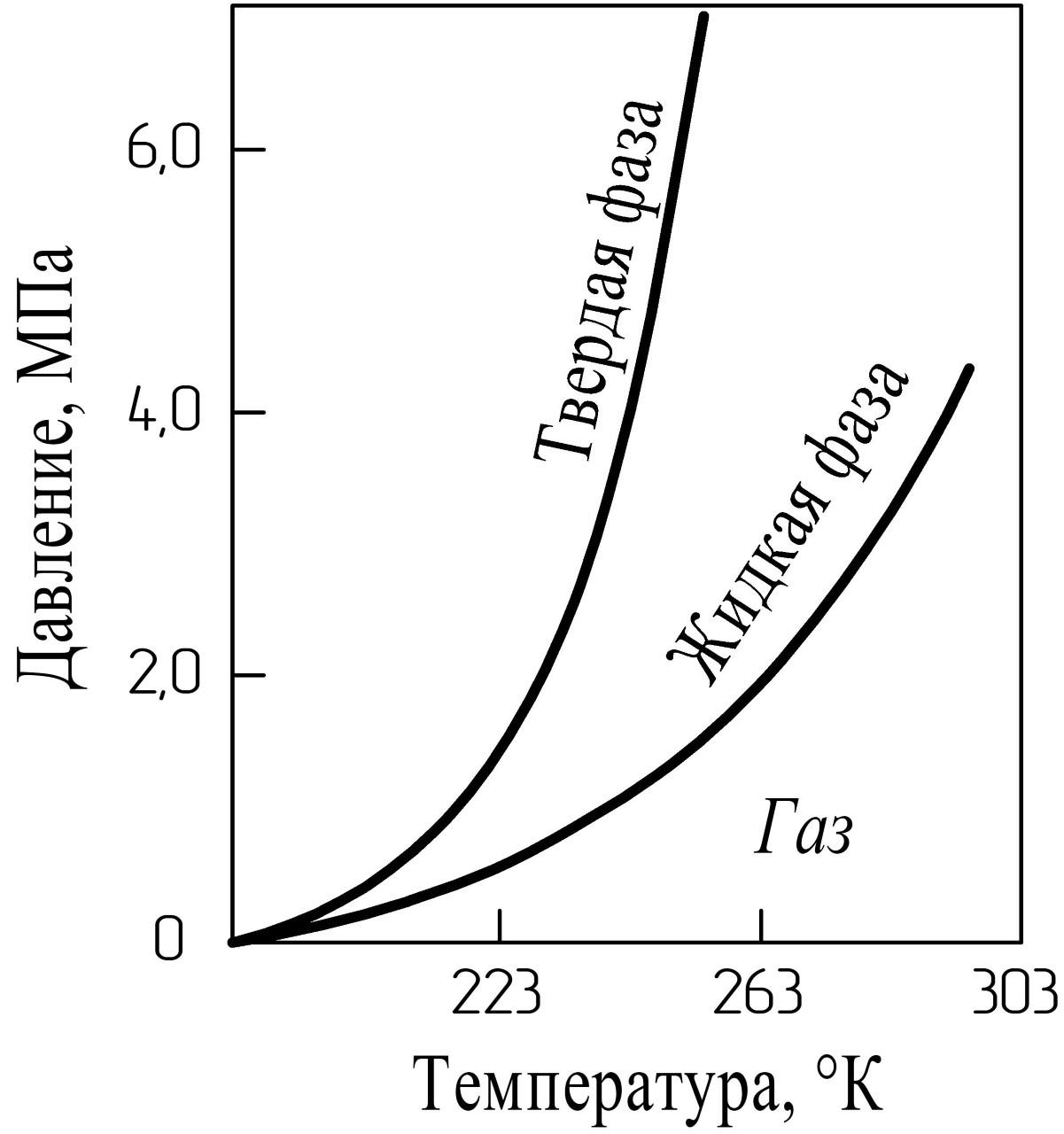
Данное обстоятельство должно быть учтено при назначении расчетного давления в сосуде, и соответствующие указания имеются в действующих НТД, где говорится, что при назначении расчетного давления необходимо учитывать нестабильность перерабатываемых сред или технологического процесса [2]. Аналогичные указания имеются в нормативно-техническом документе [6], где сказано, что «величина расчетного давления должна быть не менее максимально допустимого рабочего давления, для которого предназначено оборудование. Величина расчетного давления учитывает статический напор и динамические нагрузки рабочей среды, повышение давления из-за нестабильности рабочих сред и технологических процессов».
Представляется, что данных указаний недостаточно, чтобы обратить внимание заводских специалистов и специалистов экспертных организаций на необходимость увеличения расчетного давления для сосудов со сжиженными газами.
Имеющаяся литература по расчетам на прочность и конструированию сосудов под давлением не конкретизирует вопрос назначения расчетного давления. В действующей нормативно-технической документации, определяющей требования к сосудам под давлением, также отсутствуют указания по назначению расчетного давления за исключением указаний, относящихся к оборудованию складов сжиженных углеводородных газов и легковоспламеняющихся жидкостей под давлением [7]. В данном случае говорится, что «Резервуары, предназначенные для хранения СУГ и ЛВЖ под давлением с температурой кипения ниже 318,15 К (45 °С), рекомендуют рассчитывать на давление не ниже упругости паров продукта при температуре 323,15 К (50 °С). Для сосудов, предназначенных для хранения углеводородных фракций С3, С4 и С5, расчетное давление принимают следующим:
1,8…2,0 МПа (18…20 кгс/см2) – для фракции углеводородов С3;
0,6 МПа (6 кгс/см2) – для фракции углеводородов С4;
0,25…0,3 МПа (2,5…3 кгс/см2) – для фракции углеводородов С5».
Представляется, что данных указаний также недостаточно, поскольку действие их можно трактовать как относящееся к объектам хранения сжиженных углеводородных газов или только для «резервуаров сжиженных углеводородных газов на территории цехов и технологических установок», без указания на применимость в отношении сосудов аналогичного назначения и расположения. Недостаточность указаний проявляется также в отсутствии указаний по расчетному давлению для сосудов с рабочей средой в виде углеводородных фракций С2.
Отсутствие четких указаний по принятию расчетного давления для сосудов со сжиженными газами является серьезным недостатком. Ранее такие указания в технической литературе по конструированию сосудов под давлением имелись [8, 9]. Например, в работе [8] при изложении вопроса назначения расчетного давления сказано, что расчетное давление сосудов для сосудов с углеводородными фракциями и другими сжиженными газами во всех случаях рекомендуется принимать: «для углеводородных фракций С2 PR = 2,0 МПа; для фракций С3 на всасывающей линии PR = 1,6 МПа, на нагнетательной линии PR = 2,0 МПа; для фракций С4 PR = 0,6 МПа; для фракций С5 PR = 0,3 МПа; для аммиака PR = 1,6 МПа; для фреона PR = 1,0 МПа; для сернистого ангидрида PR = 0,8 МПа; для хлористого метила PR = 0,9 МПа; для углекислого газа PR = 7,6 МПа».
В данном случае для рабочей среды – жидкого ацетилена в качестве расчетного давления необходимо было принять значение 2,0 МПа, т.е. более чем в 3 раза больше рабочего давления в сосуде. В этом случае расчет на прочность сосуда даст следующие значения расчетной толщины стенки:
Таким образом, можно сделать вывод, что данный сосуд при существующих условиях эксплуатации вообще не мог соответствовать требованиям промышленной безопасности и должен был быть выведен из эксплуатации, это предотвратило бы возникновение аварии.
В ходе продолжительной эксплуатации в какой-то момент создались условия, когда повышение внутреннего давления в сосуде не смогло быть скомпенсировано срабатыванием предохранительного клапана (например, вследствие замедленного открытия). В результате в корпусе сосуда, который уже подвергся значительному утонению, напряжения в материале превысили максимально допустимое значение, и он был разрушен. Картина разрушения корпуса сосуда (см. рис. 2, 3) подтверждает сказанное, разрушение цилиндрической оболочки сосуда происходило по осевому сечению цилиндрической оболочки, от действия максимальных напряжений от внутреннего давления.
ВЫВОДЫ
- При проведении расчетов на прочность сосудов с рабочей средой в виде сжиженных газов расчетное давление необходимо принимать в зависимости от вида рабочей среды не менее минимально допустимых значений. Это позволит обеспечить промышленную безопасность сосудов для возможных условий эксплуатации.
- Необходимо введение в существующие нормативно-технические документы, определяющие требования к проведению расчетов на прочность сосудов под давлением, дополнительных указаний, конкретизирующих требования к назначению расчетного давления в зависимости от вида рабочей среды.
Список литературы
- Федеральные нормы и правила в области промышленной безопасности «Правила промышленной безопасности при использовании оборудования, работающего под избыточным давлением». Утв. приказом Федеральной службы по экологическому, технологическому и атомному надзору» № 536 от 15.12.2020 г.
- ГОСТ 34233.1–2017. Сосуды и аппараты. Нормы и методы расчета на прочность. Общие требования.
- ГОСТ 34233.2–2017. Сосуды и аппараты. Нормы и методы расчета на прочность. Расчет цилиндрических и конических обечаек, выпуклых днищ и крышек.
- СТО-СА-03-004–2009. Трубчатые печи, резервуары, сосуды и аппараты нефтеперерабатывающих и нефтехимических производств. Требования к техническому надзору, ревизии отбраковке. Волгоград: ОАО «ВНИКТИ нефтехимоборудование», 2009. 156 с.
- Антонов И.А., Кузнецов Л.М., Нешумова С.П. Получение ацетилена из карбида кальция. – М.: Химия, 1980. 112 с.
- Технический регламент Таможенного Союза «О безопасности оборудования, работающего под избыточным давлением» (ТР ТС 032/2013).
- Руководство по безопасности для складов сжиженных углеводородных газов и легковоспламеняющихся жидкостей под давлением. Серия 09. Выпуск 34. М.: ЗАО «Научно-технический центр исследований проблем промышленной безопасности», 2012. 56 с.
- Лащинский А.А. Конструирование сварных химических аппаратов. Справочник. М.: Машиностроение, 1981. 382 с.
- Лащинский А.А., Толчинский А.Р. Основы конструирования и расчета химической аппаратуры. Справочник. Изд. 2-е. М.: Машиностроение, 1970. 753 с.