Автор: А.В. Седельников (АО «НОРДВЕГ»).
Опубликовано в журнале Химическая техника №1/2017
Обычно большинство повреждений в трубах теплообменников, используемых на промышленных предприятиях, происходит на первом (150 мм) участке трубного пучка. Повреждения труб проявляются в виде утонения трубы, образования канавок, точечной коррозии, трещин, что в конечном итоге может привести к утечке и сбою в работе трубного пучка (рис. 1).



В прошлом эту весьма локализованную проблему было принято решать путем полной замены труб, даже несмотря на то, что более 95% длины трубного пучка оставалось неповрежденным. В некоторых случаях пучок могли «спасти», укоротив теплообменник, но при этом уменьшалась площадь теплопередающей поверхности.
Любое из этих радикальных решений является дорогостоящим и требующим слишком много времени.
В середине 1970-х годов была разработана новая технология ремонта труб теплообменников, в которой используются развальцованные металлические дублеры трубок (щиты). Этот универсальный способ восстановления «по месту» (in-situ) был успешно применен и в случае разрушения труб по всей их длине путем установки вставок (дублеров) на всю длину поврежденных труб.
Обычные механизмы разрушения труб теплообменников
Эрозия конца впускной трубы распространена в охладителях из сплавов углеродистой стали и меди, технологических теплообменниках и трубках конденсаторов и обусловлена кинетической силой жидкости (или газа), особенно, если она содержит абразивные примеси.
На входах в теплообменные трубы изменения направления потока среды и образующиеся пузырьки воздуха создают сильную турбулентность, приводя к повреждению защитных пассивных пленок на внутренних поверхностях трубок. Через 150 мм длины трубок турбулентный поток становится ламинарным, и агрессивное воздействие среды резко уменьшается. Другие факторы, способствующие сильной турбулентности, – неправильная форма распределительной камеры (канала) и подающей трубы.
Если в среде содержатся коррозионные составляющие, то негативных последствий для теплообменных трубок может быть значительно больше. Это так называемое явление эрозия–коррозия. Совместный эффект от эрозии и химического воздействия среды значительно выше, чем от их воздействия по отдельности. Причиной эрозии–коррозии чаще всего являются коррозионноактивные технологические жидкости. Однако это явление также может вызвать и вода, например, когда теплообменные трубки подвергают воздействию охлаждающей воды с примесью сульфидов и/или аммиака.
Коррозионное растрескивание под напряжением (КРН) представляет собой другой распространенный вид разрушения трубок теплообменников. Его причиной является совместное действие напряжения при растяжении и коррозии. КРН часто происходит на участке развальцовки труб непосредственно за трубной решеткой, особенно при чрезмерной развальцовке. Наиболее часто встречающиеся формы – это аммиачное коррозионное растрескивание сплавов на основе меди, хлоридное КРН аустенитной коррозионно-стойкой стали и щелочное КРН углеродистой и легированной сталей.
Другие виды коррозии, которые встречаются на концах трубок и соединениях труба-трубная решетка, – это точечное воздействие и щелевая коррозия. Щелевая коррозия – опасная форма глубокого локального проникновения, которая наиболее часто встречается в аустенитной (Cr-Ni) коррозионно-стойкой стали, подверженной воздействию хлоридов.
Скорость как КРН, так и щелевой коррозии значительно увеличивается при повышении температуры.
Причиной разрушения на участках впускной трубной решетки и концов теплообменных трубок могут быть также механические факторы (например, неправильное развальцовывание трубы) и плохо выполненные сварные швы между трубой и трубной решеткой.
Тонкостенные металлические вставки для ремонта концов трубок (щиты)
Металлические тонкостенные вставки (щиты) были впервые применены в 1976 г. При этом способе восстановления происходят защита, восстановление и герметизация поврежденных концов труб. Щиты (рис. 2) изготовливаются по специальным размерам и сохраняют пластичность, необходимую для развальцовки.
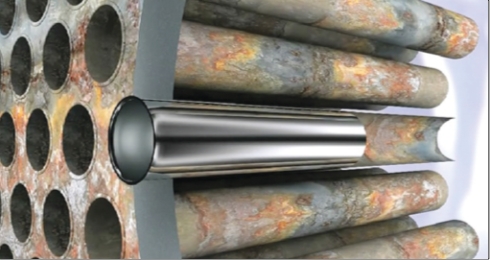
Как и в случае с установкой труб в теплообменнике, важно выбрать нужный сплав для изготовления щитов в зависимости от материала трубы, функций теплообменника и механизма разрушения.
Вставки изготавливаются из медных сплавов (Cu-Ni и латунь), обычной коррозионно-стойкой стали (аустенитная, ферритная, мартенситная, двухфазная), сверхаустенитных коррозионно-стойких сталей (шесть молибденовых сплавов) и сплавов на основе никеля (Сплав 400, Сплав С-276). Это дает возможность выбрать необходимый сплав для защиты от специфических механизмов разрушений, например, хлоридной точечной коррозии, КРН, образования канавок под действием аммиака и др.
Процесс установки выполняют «по месту», начиная с чистки внутреннего диаметра трубы проволочной щеткой для герметичного уплотнения. После продувки труб сжатым воздухом измеряют внутренний диаметр трубы для определения требований к развальцовке. Затем щиты вставляют в каждый конец трубы. Внешний конец щита развальцовывают с ограничением крутящего момента, используя обычный инструмент для развальцовки труб, в то время как внутренний участок щита развальцовывается с использованием механического ограничителя, таким образом, уменьшается вероятность чрезмерного развальцовывания. Последним шагом является развальцовка конца щита таким образом, чтобы он соответствовал профилю трубной решетки.
Щиты устанавливались в установки высокого давления (30 МПа) и высокой температуры (300°С). В некоторых случаях щиты могли соединять полностью разъединенные трубы. Восстановление труб посредством развальцованных металлических щитов представляет собой экономически целесообразный способ ремонта.
Благодаря тонкостенной конструкции и возможности гидравлического расширения щитов, площадь проходного сечения теплообменных трубок уменьшается незначительно.
Трубные вставки (дублеры) на полную длину труб
Успешное применение щитов для устранения разрушений конца трубок обусловило разработку аналогичной технологии ремонта, позволяющей восстанавливать трубы с разрушениями по всей длине. Такой ремонт предполагает установку вставки (лайнер), равной длине всей трубы, и ее последующее гидравлическое расширение для обеспечения контакта металл–металл.
Вследствие точечной коррозии на внутренней поверхности и образования канавок на внешней поверхности, уменьшения толщины стенки по всей длине теплообменных трубок и повреждениям в результате ударной коррозии в трубном пучке появляются утечки. В таких случаях, как правило, на поврежденные трубы устанавливаются заглушки. При этом теплообменные трубки выводятся из эксплуатации.
По мере износа теплообменника с течением времени и увеличением числа труб с установленными заглушками начинает снижаться эффективность установки и увеличиваться расход жидкости. Если заглушено более 10% труб, то необходима полная замена трубного пучка теплообменного аппарата.
В подобных случаях привлекательной альтернативой становится установка вставок на всю длину трубок. Благодаря регулярному восстановлению заглушенных труб можно обеспечить дополнительный срок эксплуатации теплообменника в течение многих лет.

Процесс установки трубных вставок (лайнеров) начинается с удаления заглушек и тщательной очистки трубок (гидравлической, гидромеханической, применением различных щеток и скребков из металла и нейлона). Далее в штатные теплообменные трубки устанавливают лайнеры (рис. 3, 4) с некоторым припуском по длине, позволяющим использовать специальные насадки для подачи воды и стравливания воздуха.
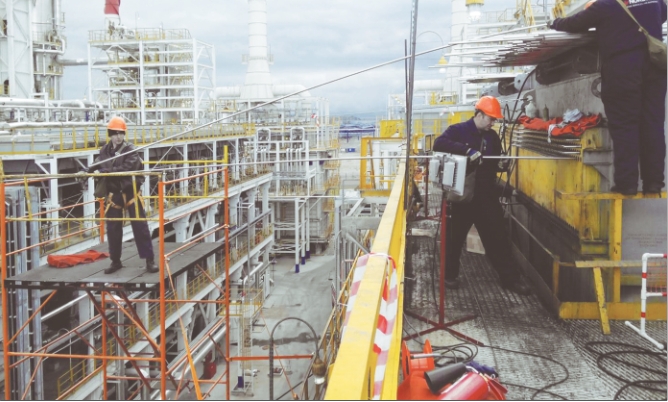
трубками
Следующий этап – гидравлическое расширение лайнеров (рис. 5). При подаче внутрь лайнеров воды под высоким давлением (15…75 МПа) происходит увеличение их размеров (по диаметру на всей длине) до соприкосновения со штатными трубками.
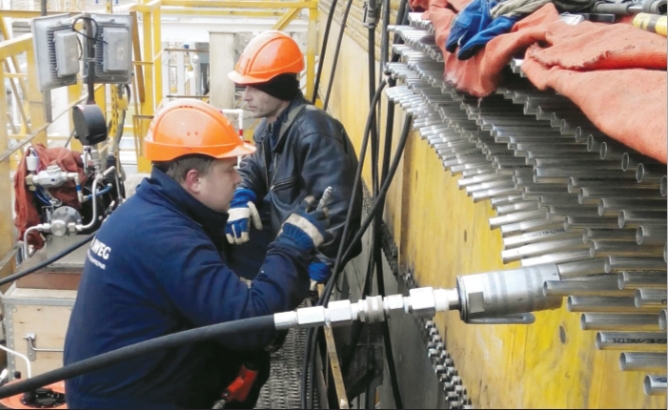
Гидравлическое расширение прекращается только после полного соприкосновения стенок лайнеров со стенками штатных трубок с необходимым натягом. Несмотря на высокое давление, создаваемое внутри лайнеров, технология гидравлического расширения практически исключает риск повреждения штатных трубок. Далее лайнеры подрезают, фрезеруют и развальцовывают в соответствии с ТУ.
Признанные непригодными предварительно заглушенные трубы возвращаются в эксплуатацию.
Тонкостенные металлические вставки эффективно используются на протяжении более чем 35 лет для восстановления вышедших из строя труб и возращения в эксплуатацию трубок теплообменников во всем мире.
Благодаря широкому спектру сплавов, пригодных для изготовления трубных вставок, при помощи этого недорогого способа можно продлевать срок эксплуатации теплообменников в коррозионной среде и в условиях высокой температуры и давления.
В настоящее время зачастую в проект новых теплообменников также входит методика по установке щитов и вставок полной длины.
В России этот метод успешно применяется с 2010 г. на предприятиях энергетического и нефтеперерабатывающего комплекса.