Авторы: А. Н. Любимов, ООО НПФ «ЭНТЕХМАШ»;
А. Г. Лахман, ООО НПФ «ЭНТЕХМАШ», Университет ИТМО
Опубликовано на портале «Химическая техника», август 2024
Проектирование и расчёт центробежных компрессоров – сложный процесс, требующий учёта множества факторов. Один из ключевых аспектов – рабочее тело (сжимаемый газ). При разработке центробежного компрессора углекислого газа важно учитывать изменения термодинамических свойств газа (показатель изоэнтропы, коэффициент сжимаемости) при приближении к критической точке на диаграмме состояния газа, а также изменения состава газа (удельная газовая постоянная) из-за различной относительной влажности газа на входе каждой секции компрессора. Эти свойства существенно влияют на газодинамический расчёт проточной части и характеристики компрессора. В статье рассматривается пример модернизации компрессора углекислого газа высокого давления в производстве карбамида, описываются технические сложности, с которыми пришлось столкнуться, и способы их преодоления. В результате работы были обеспечены гарантийные параметры.
Введение
Центробежные компрессоры углекислого газа (СО2) высокого давления играют важную роль в промышленности. Они используются в производстве карбамида, который служит сырьём для изготовления удобрений, гербицидов, карбамидно-формальдегидных смол, клеёв, меламина, а также успокаивающих и снотворных лекарств, зубной пасты и косметики.
Расчёт и конструирование таких компрессоров – одни из самых сложных задач [1, 2]. Высокое отношение давлений (~150) вызывает проблемы с согласованием газодинамических характеристик неохлаждаемых секций и ступеней компрессора (эффект «снежного кома»). Также важно учитывать свойства реального газа [3–7].
Классические методы проектирования центробежных компрессоров, сжимающих реальные газы, неточны, поскольку основаны на одномерных расчётах по безразмерным параметрам, полученным в результате стендовых испытаний на воздухе. Необходимо учитывать теплофизические свойства CO₂ в каждом контрольном сечении проточной части из-за резких изменений термодинамических свойств при высоких давлениях [8, 9].
Центробежные компрессоры углекислого газа высокого давления являются импортными. Развитие расчетных методик проектирования таких компрессоров [10–12] необходимо для их модернизации, поскольку в последнее время требуется увеличить производство минеральных удобрений, в частности карбамида. Существующие компрессоры углекислого газа не соответствуют современным требованиям по производительности, энергоэффективности и надёжности.
Оригинальный компрессор фирмы Nuovo Pignone
Компрессор фирмы Nuovo Pignone был спроектирован и изготовлен в 1971 г. Затем он был законсервирован и вывезен из Италии в Россию в 2010 г. Компрессор выполнен трёхцилиндровым, пятисекционным (рис. 1). В состав цилиндра низкого давления (ЦНД) входят две секции: в 1-й секции – 3 ступени, во 2-й секции – 4 ступени. В состав цилиндра среднего давления (ЦСД) входит две секции, в каждой по три ступени. В состав цилиндра высокого давления (ЦВД) входит одна секция с пятью ступенями. Секции ЦНД и ЦСД расположены по аэродинамической схеме «спина к спине».
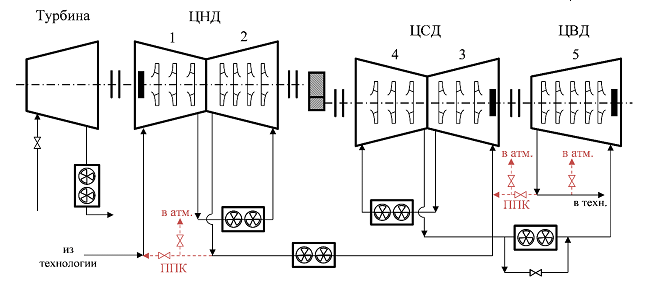
Приводом компрессора служит паровая турбина производства Nuovo Pignone номинальной мощностью 4,35 МВт (максимальной мощностью ~5,3 МВт) и диапазоном частоты вращения 6750…9450 об/мин. Мультипликатор с косозубым зацеплением с передаточным отношением i = 1,447 расположен между ЦНД и ЦСД. Газ после каждой секции, за исключением 5-й (ЦВД), охлаждается в промежуточном газоохладителе воздушного типа.
Основные проектные параметры компрессора
Состав газа, об. доля: | CO2 – 98%, N2– 2% (ϕотн.= 100%) |
Производительность на всасывании, нм3/ч (20°С, 1 физ. атм.): |
17 170 |
Начальное давление, бар абс: | 1,0 |
Конечное давление, бар абс: | 150,0 |
Начальная температура газа на входе: | 42,0 °С |
Частота вращения ротора ЦНД/ЦСД-ЦВД, об/мин: |
9000/13 020 |
Потребляемая мощность: | 3,95 МВт |
Особенности компрессора
Подаваемый сжимаемый газ представляет собой смесь углекислого газа (94%), азота (5%), кислорода (~1%) со 100%-ной относительной влажностью. Влажный углекислый газ является коррозионно активным, поэтому для статорных узлов применяется коррозионно-стойкая сталь, для деталей ротора – специальные нержавеющие стали, а для обойм лабиринтных уплотнений – коррозионно-стойкая марка алюминия.
На вход в каждую последующую секцию влажный газ поступает из предыдущей секции с повышенным давлением, но охлаждённый промежуточным охладителем до температуры 35…45°С. Часть паров воды, растворённых в газе, конденсируется в промежуточном охладителе и выводится установленным за ним сепаратором. В результате состав газа, поступающего в каждую последующую секцию, отличается от состава газа в предыдущей секции и содержит меньше воды. Поскольку количество отводимой воды зависит от давления, на каждом режиме работы компрессора перед каждой секцией свой состав газа и, следовательно, своя удельная газовая постоянная R, которая сильно влияет на расчётное отношение давлений и приводит к значительным несоответствиям при неучёте конденсации воды в сепараторах.
Псевдокритическая точка смеси газов находится в рабочем диапазоне давлений и температур, что приводит к стремительным изменениям термодинамических свойств смеси газов (коэффициент сжимаемости z и показатель изоэнтропы k). Таким образом, z и k значительно изменяются не только по секциям компрессора, но и по их ступеням, что делает некорректным использование методик расчёта газодинамических характеристик компрессора, основанных на перерасчёте заранее рассчитанных газодинамических характеристик (ГДХ) секций на иные условия работы [13, 14]. Единственный корректный способ – это расчёт ГДХ компрессора по отдельным безразмерным ГДХ ступеней, что требует создание новой методики [15] и требует в ~100 раз большие вычислительные ресурсы в связи с вложенной итеративностью процесса вычисления. Для расчета термодинамических свойств газа использовалось уравнение состояния реального газа Редлиха–Квонга в модификации Соаве.
Термодинамические параметры смеси газов на входе в 5-ю секцию (ЦВД) близки к значениям в псевдокритической точке, что создаёт риск сжижения CO2 при снижении температуры на входе ЦВД до ~28°С при давлении ~74 бар абс. Это может вызвать неожиданный помпаж во время эксплуатации. Для повышения температуры на входе ЦВД (до 45…50°C) часть горячего газа с выхода из четвёртой секции ЦСД направляют мимо промежуточного охладителя через регулирующий клапан, управляемый ПИД-регулятором АСУ. Это решает проблему, но одновременно повышает мощность, потребляемую компрессором.
Углекислый газ – тяжёлый и легкосжимаемый газ. Из-за этого скорость звука в нём относительно низкая, и в эскизном проекте проточной части возникла проблема раннего звукового запирания базового варианта рабочего колеса первой ступени ЦНД. Уже на номинальном режиме местные числа Маха достигали значений около 1,0, и устанавливался трансзвуковой режим течения. С помощью методов вычислительной газодинамики в ПО Numeca Fine/Turbo [16] была проведена оптимизация геометрических параметров рабочего колеса. В результате была получена благоприятная форма лопаток и входной части колеса, что обеспечило дозвуковое течение газа и повышенный запас устойчивости работы ступени и всей секции в целом.
В ЦВД свойства газа изменяются очень быстро. Например, на входе при давлении 76 бар абс. и температуре 50°С коэффициент сжимаемости zн = 0,65, а на выходе секции при давлении 150 бар абс. и температуре 145°С коэффициент сжимаемости zк = 0,8. Плотность газа достигает 250 кг/см2 (1/4 плотности воды). В связи с этим в ЦВД используются малорасходные ступени, а при низких углах потока на выходе из рабочего колеса α2 = 10° применение лопаточного диффузора (ЛД) нецелесообразно и приведёт к преждевременной потере устойчивости работы ЦВД. В эскизном проекте был выбран канальный направляющий аппарат, который направляет поток из РК предыдущей ступени в РК следующей ступени. Преимущество этого решения в том, что скоростью потока можно управлять за счёт изменения площади поперечного сечения каналов и их кривизны. С помощью методов вычислительной газодинамики была проведена оптимизация геометрических параметров РК совместно с канальным направляющим аппаратом и получена благоприятная форма, что обеспечило безотрывное течение во всём диапазоне работы ступени и увеличенный запас по помпажу при относительно высоком значении политропного КПД ступени ηпол.
В проточных частях компрессора используется множество лабиринтных уплотнений (статорные усы с острыми кромками, установленные с равным шагом и уплотняющие вращающиеся поверхности ротора). Чем выше плотность газа, тем выше перетечка, которая вызывает повышенную потребляемую мощность компрессора из-за необходимости повторно сжимать перетекающий поток газа. Например, утечка через уплотнение думмиса ЦВД при номинальном радиальном зазоре 0,2 мм составляет ~15% массового расхода компрессора, что в 10–15 раз больше, чем у воздушных центробежных компрессоров общего назначения с конечным давлением 9 бар абс. При задевании ротора об уплотнение сминаются кромки усов, и перетечка увеличивается вдвое. Помимо этого, возникает дополнительный негативный эффект от подмешивания горячего газа в основной поток, что приводит к повышению его температуры и потребляемой мощности компрессора. Повышение температуры основного потока газа, а, следовательно, и объемного расхода, происходит в первую очередь из-за направления задуммисной перетечки на вход в первую секцию соответствующего корпуса, а уже в меньшей степени – из-за перетечки через уплотнения покрывающих дисков каждого РК, а также из-за перетечек через валовые уплотнения между соседними РК. Учёт перетечек в проточной части приводит к дополнительной итеративной сложности расчёта ГДХ, поскольку на каждом режиме свои давления в каждом сечении проточной части, а, следовательно, и свои значения перетечек и подогрева основного потока. Учёт при расчёте эффектов, вызванных перетечкой газа через лабиринтные уплотнения, требует в ~4 раза большие вычислительные ресурсы в связи с вложенной итеративностью процесса вычисления (температура влияет на термодинамические свойства газа).
Центробежный компрессор имеет систему концевых лабиринтных уплотнений, которая снижает давление на концах каждого вала от значений на входе в соответствующий корпус (ЦСД и ЦВД) до атмосферного давления в машинном зале. В оригинальном компрессоре была реализована система концевых уплотнений, которая перепускает газ из камер концевых уплотнений цилиндров компрессора на вход предыдущего по ходу газа корпуса (с ЦВД на ЦСД, а с ЦСД на ЦНД). Режимы работы компрессора существенно зависят от величины перетекаемого через систему концевых уплотнений газа. Влияние перетечек через концевые уплотнения на центробежный компрессор высокого давления с большой «крутизной» ГДХ, вызванных согласованием работы пяти секций, работающих на «тяжёлом» газе, можно проиллюстрировать сравнением работы компрессора с герметичной системой (перетечки через концевые уплотнения равны нулю) и с реальной системой. В герметичном варианте компрессор имеет конечное давление 150 бар абс., а в варианте с реальной системой – около 70 бар абс.
Ещё одна проблема, связанная с системой концевых уплотнений, – сжижение сжимаемого газа в концевых уплотнениях ЦСД и ЦВД из-за его резкого расширения и охлаждения (эффект Джоуля–Томсона) при дросселировании влажного углекислого газа между усиками уплотнений и валом. Образующаяся при этом углекислота в присутствии индуцированного тока, вызванного малой остаточной намагниченностью роторов, вызывает разрушение обойм лабиринтных уплотнений и повреждение поверхностей вала под ними. Расчёт дросселирования газа в концевых лабиринтных уплотнениях выявил наличие конденсации углекислого газа в местах где и наблюдались следы коррозии. Для решения этой проблемы была разработана новая «горячая» схема, в которой в концевые уплотнения (в начало расширения) направляется горячий газ температурой 100…140°С, вместо штатной «холодной» схемы, в которой газ начинал расширяться с температуры не более 40°С, что фактически исключило сжижение газа в конце расширения.
Эффект рассогласования режимов работы секций и включенных в их состав ступеней проявляются «снежным комом»: при небольшом пережатии первыми ступенями ЦНД ступени ЦВД попадают в предпомпажное состояние, а при небольшом недожатии, наоборот, попадают в зону звукового запирания. Эти особенности требуют точного расчёта.
Одна из причин ненадёжной работы роторов центробежных компрессоров – автоколебание роторов из-за наличия циркуляционной силы в лабиринтных уплотнениях. Её природа вызвана вращением ротора в зазоре уплотнения со сдвигом оси (эксцентриситетом), что приводит к переменному во времени зазору вокруг уплотняемой поверхности ротора и, следовательно, к разному расходу и давлению с противоположных сторон ротора. Окружная разница давлений, действующая на ротор, вызывает образование силы, стремящейся вывести ротор из состояния равновесия. При этом возбуждающая сила тем больше, чем больше окружная компонента скорости потока в уплотнении. Опережение газом окружной скорости метала ротора неминуемо вызовет резкое снижение динамической устойчивости ротора. Для уменьшения данного явления при входе в новые уплотнения с торцевой стороны выполнены лунки, которые поворачивают закрученный поток газа в осевое направление и препятствуют появлению дополнительных возбуждающих аэродинамических сил.
Все описанные особенности делают процесс расчёта центробежного компрессора углекислого газа высокого давления крайне трудным и ресурсозатратным.
Модернизация компрессора
Заказчиком и ООО НПФ «ЭНТЕХМАШ» было принято решение модернизировать проточные части ЦНД, ЦСД и ЦВД компрессора, чтобы повысить его производительность и энергоэффективность. При этом использовались существующие корпусы компрессора, фундамент, паровая турбина, трубопроводная обвязка и масляная система. Также были поставлены новый мультипликатор, сухие пластинчатые муфты и вкладыши подшипников.
Цели модернизации:
- Повышение производительности компрессора на выходе с фактической 16 500 до 20 500 нм3/ч;
- Увеличение энергоэффективности;
- Повышение надежности работы компрессора (уменьшение уровня вибрации роторов, исключение конденсации газа в концевых уплотнениях).
Проточная часть ЦНД показана на рис. 2 в процессе её монтажа в корпус, имеющий горизонтальный разъём. Первое рабочее колесо ЦНД выполнено с радиальными вырезами типа «ромашка» для снижения динамических напряжений. Это позволило дополнительно увеличить угол наклона покрывающего диска с целью раскрытия входного сечения и уменьшения чисел Маха в нём.
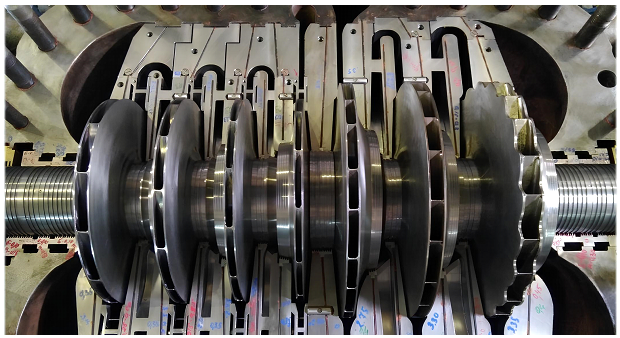
Проточная часть ЦСД приведена на рис. 3. При её проектировании применено современное надежное решение – цельный внутренний корпус (рис. 4), в который устанавливаются отдельные диафрагмы вместо набора дисков, скреплённых болтами и шпильками в осевом направлении.
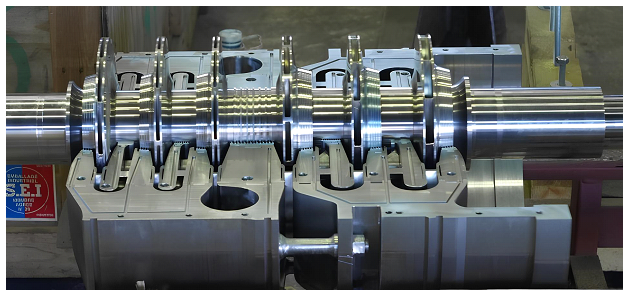
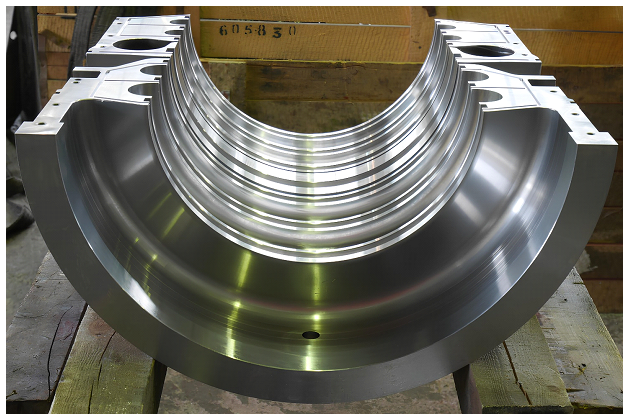
Проточная часть ЦВД приведена на рис. 5 и 6, в ней также применён цельный внутренний корпус. Низкорасходная статорная часть ЦВД полностью перепроектирована: созданы диафрагмы, объединяющие диффузор и обратно-направляющий аппарат в единый канальный направляющий аппарат.
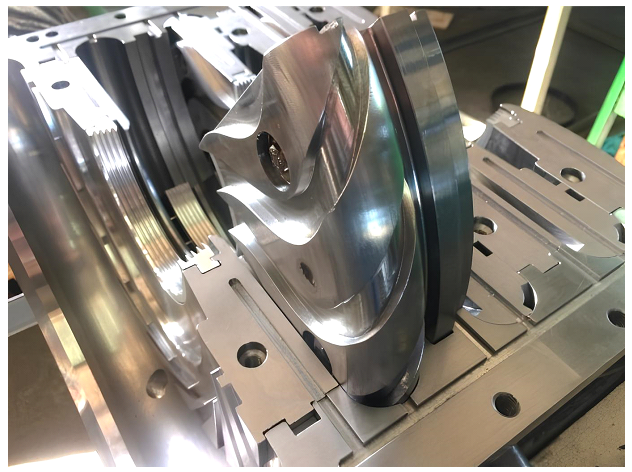
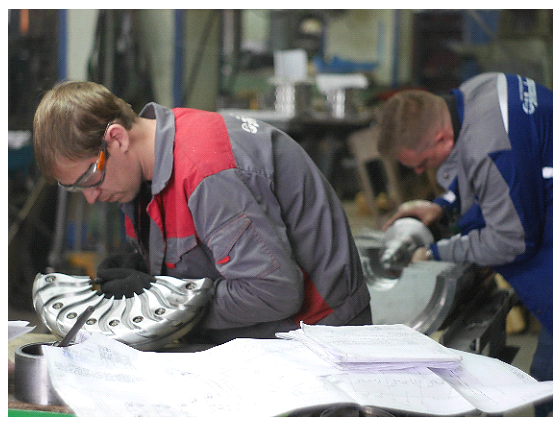
В ходе работы над проектом потребовалось оперативно освоить производство сварных РК малого диаметра. На рис. 7 представлено РК диаметром 200 мм, сваренное через прорези в покрывающем диске.
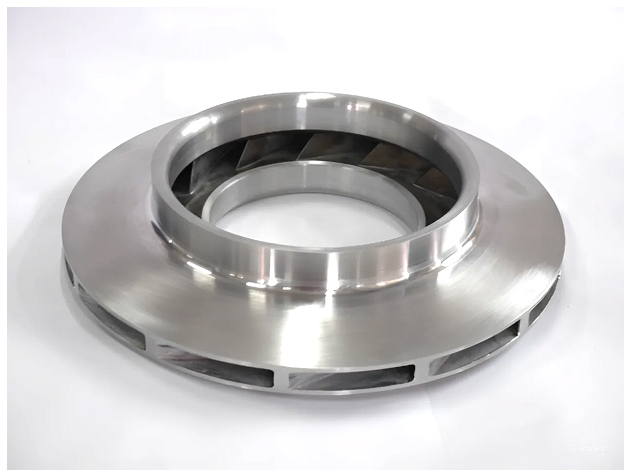
Новые лабиринтные уплотнения выполнены в виде алюминиевых обойм с усиками и спроектированы для уменьшения перетечек газа. На входе в уплотнения выполнены лунки (рис. 8), которые препятствуют появлению дополнительных аэродинамических сил, возбуждающих колебания ротора.
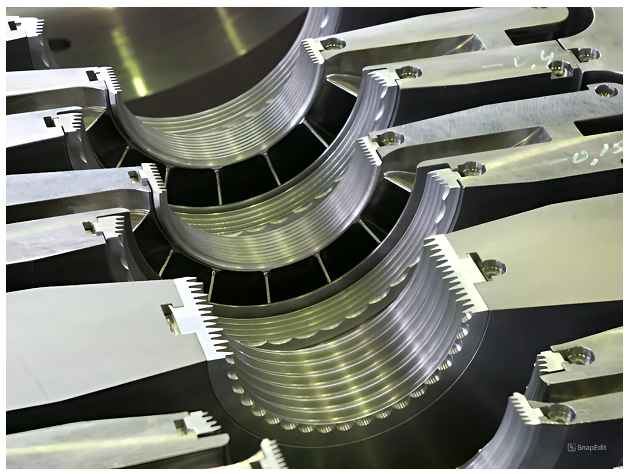
Для снижений вибрации роторов ЦСД и ЦВД, масса которых мала и составляет всего 112 и 47 кг соответственно, было целесообразно провести высокочастотную балансировку в вакуумной камере на рабочей частоте вращения, что позволяет снять дисбалансы при реальной линии изгиба средней линии ротора.
Результаты модернизации
Модернизация позволила повысить производительность компрессора на 24%, а удельную мощность снизить на 17% при сопоставимых условиях. Это существенно увеличило производительность при сохранении штатного привода (паровой турбины).
В табл. 1 представлены параметры работы исходного и модернизированного компрессора.
Таблица 1
Сравнение параметров компрессора до и после модернизации
Политропный КПД исходного и модернизированного компрессора приведен в табл. 2.
Таблица 2
Сравнение политропного КПД секций компрессора до и после модернизации
Заключение
Проведена модернизация центробежного компрессора углекислого газа высокого давления. Учтены особенности модернизации, разработаны программы для расчёта и математического моделирования различных отдельных аспектов компрессорной машины.
Результаты показали потенциал и перспективы развития одномерных расчётных методик проточной части центробежного компрессора и методов вычислительной газодинамики для моделирования пространственного течения газа в проточной части, лабиринтных уплотнениях и зазорах между роторными и статорными узлами.
Необходимо дальнейшее развитие методик расчёта реальности газа в контрольных сечениях проточной части секций компрессора, перетечек газа через лабиринтные уплотнения на каждом режиме его работы. Актуальна разработка комплекса программ для итеративного моделирования компрессорного агрегата, включающего взаимодействующие и взаимодополняющие математические модели.
Мы уверены, что полученный опыт, разрабатываемые методики и программный комплекс станут основой для будущих успешных проектов по модернизации компрессорных машин.
Список литературы
- Любимов А.Н., Евдокимов В.Е. О расчете газодинамических характеристик ступени центробежного компрессора//Компрессорная техника и пневматика. 2012. №7. C. 28–33.
- Боровков А.И., Войнов И.Б., Галеркин Ю.Б. и др. Моделирование газодинамических характеристик на примере модельной ступени центробежного компрессора//Научно-технические ведомости СПбПУ. Естественные и инженерные науки. 2018. Т. 24. №2. С. 44–57.
- Соколов М.И., Кожухов Ю.В. Анализ расчета проточной части центробежного компрессора с учетом реальности газа различными методами //Материалы научной конференции с международным участием. СПб: СПбПУ, 2016. С. 15–19.
- Коршунов А.В., Стрижак Л.Я. Термогазодинамический расчет компрессоров, сжимающих реальные газы и их смеси. СПб: Изд-во ГТУ. 1998. С. 3–6.
- Р. Рид, Дж. Праусниц, Т. Шервуд. Свойства газов и жидкостей. Нью-Йорк. 1977 г. С. 82–83.
- Юн В.К. Методы расчета термодинамического процесса сжатия реальных газов в проточных частях центробежного компрессора//Компрессорная техника и пневматика, 2011.
- Методика моделирования потока реального газа в ступени центробежного компрессора в составе установки сжижения диоксида углерода//Холодильная техника и биотехнологии. Сб. тезисов 5-й Национальной конференции студентов, аспирантов и молодых ученых. Кемерово. 2023. С. 65–67.
- Денисенко В.В., Миронов Ю.Р., Малев К.Г. и др. Задача валидации газодинамических характеристик многоступенчатого центробежного компрессора дожимной станции природного газа//Труды международного симпозиума им. К.П. Селезнева. СПб: СПбПУ, 2018. С. 89–103.
- Рекстин А.Ф., Семеновский В.Б., Солдатова К.В,, Галеркин Ю.Б., Соколов К.К. Особенности моделирования газодинамических характеристик центробежных компрессоров турбодетандерных агрегатов//Компрессорная техника и пневматика 2018. №1. С. 13–20.
- Peng Jiang, Yong Tian, Bo Wang, Chaohong Guo. Design and analysis of centrifugal compressor in carbon dioxide heat pump//Scientific Reports, Article number 14: 5286 (2024).
- Javad Hosseinpour, Mekuannint Messele, Abraham Engeda. Design and development of a stable supercritical CO2 centrifugal compressor//Thermal Science and Engineering Progressm. 2024. Vol. 47. Р.102–273.
- Samira Sayad Saravi, Savvas A. Tassou. An investigation into sC02 compressor performance prediction in the supercritical region for power systems//Energy Procedia. //Vol. 161. 2019. P. 403–411.
- Шамеко С. Л., Любимов А. Н., Гаман Е. В. К пересчету газодинамических характеристик многоступенчатой проточной части ЦКМ на иные условия работы// Компрессорная техника и пневматика. 2010. № 3. С. 28–31.
- Шамеко С. Л., Любимов А. Н., Гаман Е. В. Получение газодинамических характеристик многоступенчатой проточной части ЦКМ при изменившихся условиях работы // Вестник Международной академии холода. 2011. № 1. С. 26–30.
- Любимов А. Н. Совершенствование методов расчёта газодинамических характеристик проточной части стационарных центробежных компрессоров. Дис. … канд. техн. наук. 2016. 138 с.
- Неверов В. В., Чеглаков И. В., Любимов А. Н. Проектирование центробежных компрессорных машин с использованием методов вычислительной газодинамики // Компрессорная техника и пневматика. 2018. № 4. С. 24–28.