Автор: И.Н. Антоненко (НПП «СпецТек»).
Опубликовано в журнале Химическая техника №5/2014
Ремонтная деятельность как плановая, так и внеплановая, формирует разрывы в технологическом процессе нефтепереработки, который по своей природе является непрерывным. Возникающие простои оборудования в ремонтах принципиально не устранимы в силу известных причин (износ, требования промышленной безопасности, необходимость поддержания технических параметров оборудования, обеспечивающих заданные характеристики продуктов нефтепереработки).
В связи с этим усилия предприятий направлены на достижение управляемости ремонтной деятельностью и уже на этой основе – на оптимизацию процессов технического обслуживания и ремонта (ТОиР) по критерию максимума эксплуатационной готовности. Препятствия, с которыми сталкиваются предприятия, это, в частности, отсутствие полной и достоверной информации о состоянии оборудования и процессах ТОиР, информационные разрывы между ремонтной и производственной программами. Поэтому закономерно, что менеджментом нефтеперерабатывающих предприятий осознана и сформулирована потребность в информационных системах управления ТОиР (ИСУ ТОиР) [1].
Возможности, которые открываются благодаря внедрению и использованию ИСУ ТОиР, если рассматривать их с самых общих позиций, заключаются в следующем:
- единые шаблоны обслуживания однотипного оборудования, средства управления типовыми неисправностями и аналитическая отчетность становятся доступны всем подразделениям; это дает возможность сравнивать эффективность обслуживания оборудования по разным подразделениям (филиалам), выявлять лучшие практики и распространять их на все предприятие;
- появляется унифицированный подход к ТОиР на всех объектах компании; это позволяет централизованно внедрять и сопровождать корпоративные политики и процедуры в области ТОиР, в том числе реализовывать на практике решения руководства по пересмотру этих политик и процедур;
- появляются единые инструменты для классификации оборудования по критичности и мониторингу его состояния, благодаря чему становится понятной картина приоритетов обслуживания и ремонта в масштабе предприятия;
- всем службам – механической, энергетической, транспортной – становится доступна единая классификация всего оборудования предприятия; это позволяет координировано планировать и выполнять работы на различном оборудовании;
- формируется единая система норм использования материалов и запчастей в масштабе предприятия и всех его филиалов; это позволяет с общих позиций подходить к выявлению источников и причин издержек в складском хозяйстве и материально-техническом снабжении, вести системную работу по сопровождению и корректировке регламентов, нормативов ТОиР;
- предприятие получает инструмент ведения электронного технического архива документации, который устраняет известное противоречие между доступностью и сохранностью бумажного документа; электронный архив обеспечивает наличие документов в местах их применения без тиражирования бумажных копий, релевантность которых с момента выпуска неизбежно снижается.
Рассмотрим отраслевые особенности использования ИСУ ТОиР на предприятиях нефтепереработки. При этом в качестве примера будем использовать TRIM – специализированный программный продукт разработки НПП «Спец- Тек», предназначенный для создания ИСУ ТОиР [2].
Эффективность ИСУ ТОиР, в частности, можно оценивать по вкладу этой системы в увеличение эксплуатационной готовности (ЭГ). Показатель ЭГ в общем виде определяется как отношение времени нахождения установки (агрегата) в работе или резерве к годовому номинальному фонду времени производства, и отражает долю времени, в течение которого оборудование способно производить продукцию. На лучших в мире предприятиях нефтепереработки ЭГ достигает 97%, в России – 95%.
При этом каждый процент увеличения ЭГ – это переработка дополнительных десятков тысяч тонн нефти и получение соответствующего объема продуктов переработки, это сотни миллионов рублей дополнительной выручки предприятия. Понятно, что установка должна работать на выпуск продукции максимально возможное количество времени.
Для увеличения ЭГ менеджмент предприятия разрабатывает и осуществляет мероприятия, направленные на повышение межремонтного пробега, сокращение количества внеплановых простоев, оптимизацию плановых ремонтов и сокращение сроков их проведения. Это может быть переход к ремонтам технологическими цепями вместо ремонта установок по отдельности. Или мероприятия, связанные с внедрением средств диагностики и учетом состояния оборудования при выводе его в ремонт, объективно обоснованным переводом установок на увеличенный межремонтный пробег.
Информационное обеспечение этой деятельности трудно переоценить. Такой инструмент, как ИСУ ТОиР, позволяет максимизировать эффективность менеджмента.
Подготовка к ремонтам
Подготовка оборудования к ремонтам включает комплекс мероприятий – как промывкуа с ингибиторами, устранение отложений в трубопроводах и аппаратах и т.д.
Это требует времени, привлечения подрядных организаций и собственных ресурсов.
Заблаговременное описание и накопление этих работ в базе данных ИСУ ТОиР позволяет быть уверенным, что все необходимые подготовительные работы будут запланированы, необходимые для них ресурсы – предусмотрены, и не возникнет перерывов в их выполнении.
В дальнейшем становится возможным ведение описаний эти работ в информационной системе – их можно дополнять, корректировать.
При этом подготовительные мероприятия могут быть привязаны к соответствующему объекту – установке, аппарату, технологической цепи.
В подготовительный период целесообразно выполнение тех ремонтных работ, которые могут быть проведены без остановки технологического процесса. С этой целью в ИСУ ТОиР такие работы могут быть снабжены соответствующим признаком, с тем, чтобы при формировании плана-графика они автоматически планировались на период подготовки к ремонтам.
Дефектные ведомости
Составление дефектной ведомости, по сути, тоже является подготовкой к ремонту. В силу большой важности и трудоемкости этот документ имеет особое значение.
Механизм формирования и использования дефектных ведомостей в ИСУ ТОиР состоит в следующем.
В системе создаются описания типовых работ с комплектующими, запчастями, материалами, трудозатратами, инструментом, оснасткой, технологическим оборудованием, уровнем квалификации исполнителей, маршрутными технологическими картами, документацией.
Затем из этих типовых работ «набираются» типовые дефектные ведомости (рис. 1).
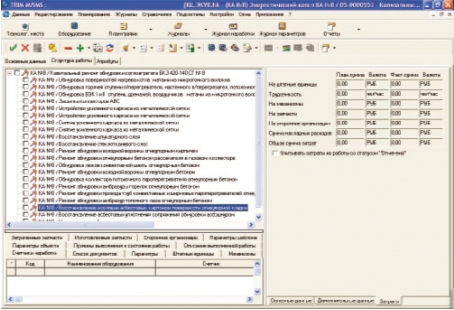
дефектной ведомости в ИСУ ТОиР «TRIM»
Рабочие дефектные ведомости формируются на этапе детальной проработки ремонтных мероприятий. Они составляются в ИСУ ТОиР путем копирования и редактирования типовых с удалением работ, в выполнение которых нет необходимости, или добавлением нетиповых работ, что значительно сокращает сроки подготовки к ремонту.
Данные о состоянии оборудования, накопленные в ИСУ ТОиР, вносятся в дефектные ведомости – это позволяет точно определить фронт работ, заранее к нему подготовиться, включая закупку оборудования для замены, и тем самым сократить сроки ремонта.
Упомянутая выше привязка ресурсов к типовым работам позволяет произвести автоматический расчет стоимости и материальнотехнического обеспечения при формировании рабочей дефектной ведомости.
Если привлекаются подрядчики, использование ИСУ ТОиР позволяет автоматизировать взаимодействие с ними: дефектная ведомость выгружается из ИСУ ТОиР и отправляется подрядчику в приемлемом для него электронном формате на этапе осмечивания и согласования.
Осмеченная подрядчиком, она возвращается предприятию и автоматически закачивается в ИСУ ТОиР, где ее можно сравнивать по стоимости с такой же дефектной ведомостью, полученной от другого подрядчика. При необходимости можно разбить одну ведомость на несколько частей, чтобы те или иные работы из нее отдать разным подрядчикам, предложившим более выгодные цены.
В базе данных ИСУ ТОиР возможно различное представление оборудования (рис. 2). Оно может быть, например, иерархическим или структурным (по подразделениям).
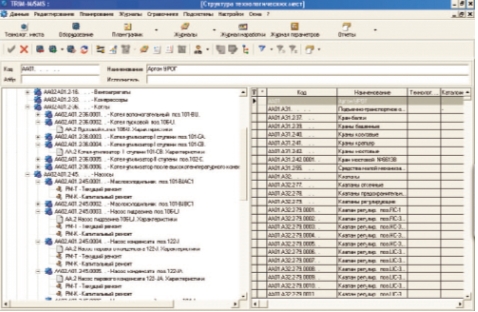
в базе данных ИСУ ТОиР «TRIM»
Возможно представление в виде технологических цепей. Это позволяет формировать и хранить в ИСУ ТОиР типовые дефектные ведомости по отдельным установкам или по технологическим цепям, и повторно использовать их при подготовке к новому ремонту.
Описание оборудования технологической цепи в базе данных ИСУ ТОиР может включать взаимосвязи с инфраструктурными объектами – межцеховые коммуникации, водообеспечение, энергоснабжение и т.п., которые, в свою очередь, описаны в базе данных с работами по ним и необходимыми ресурсами. Такая взаимосвязь позволяет «подтягивать» в дефектную ведомость данные по этим объектам, планировать отключения, планировать параллельно работы на технологической цепи и на объектах инфраструктуры.
Повышение межремонтного пробега
Современные методики, такие как RBI (Risk–Based Inspection, инспектирование с учетом рисков), помогают увеличить межремонтный пробег и/или обосновать его увеличение. Инспекции позволяют выявить «узкие места», снижающие надежность, разработать и включить в дефектную ведомость предупре-дительные мероприятия, определить срок очередной инспекции, оптимальный с точки зрения допустимого риска. С другой стороны, они нацелены на выявление излишних ревизий, требующих остановки оборудования, и разработку компенсирующих мероприятий для согласования с Ростехнадзором.
Для этого инспекции включают систематическое определение риска отказа (совокупность вероятности отказа и его последствий) для единицы или группы оборудования. ИСУ ТОиР предоставляет весь спектр возможностей для ведения RBI: создание базы данных по инспектируемым объектам, описание их функций с привязкой к каждому объекту, описание функциональных отказов с указанием видов каждого отказа, категорирование видов отказа по последствиям и тяжести последствий, связка оценок вероятности отказов с видами отказов, формирование типовых и долгосрочных программ работ по каждому критическому отказу, анализ эффективности и пересмотр программ работ.
Оптимизация графиков работ
Задача сокращения сроков работ требует формирования и оптимизации графиков работ по временной оси, сетевых графиков. В информационной системе временной график может быть автоматически сгенерирован на основе дефектной ведомости, исходя из длительностей составляющих работ. При этом он будет нагружен ресурсами, привязанными к работам. План-график, сформированный в электронном виде (рис. 3), позволяет выполнять операции перепланирования, формирования нескольких альтернативных вариантов.
Специалисты нефтеперерабатывающих предприятий давно освоили инструменты сетевого планирования. Однако интеграция этих инструментов в ИСУ ТОиР представляется необходимой. Сначала весь объем предстоящих работ должен быть сформирован в виде дефектной ведомости. При этом готовится следующий массив данных: объект, наименование работы, привлекаемые трудовые ресурсы, машины и механизмы, сроки, статус, связи между работами.
Далее все эти данные используются для построения календарносетевого графика. Анализируется полученный критический путь, загрузка ресурсов, проводится оптимизация графика по минимуму срока выполнения работ. Выявляются критические работы, определяющие сроки простоя в ремонтах, и по ним планируется круглосуточный режим выполнения. Полученный таким образом план-график используется в качестве рабочего в ИСУ ТОиР, где фиксируются данные о его исполнении – текущие статусы работ, фактические даты выполнения и т.д. Текущая информация о работах может использоваться для корректировки сформированного ранее плана-графика.
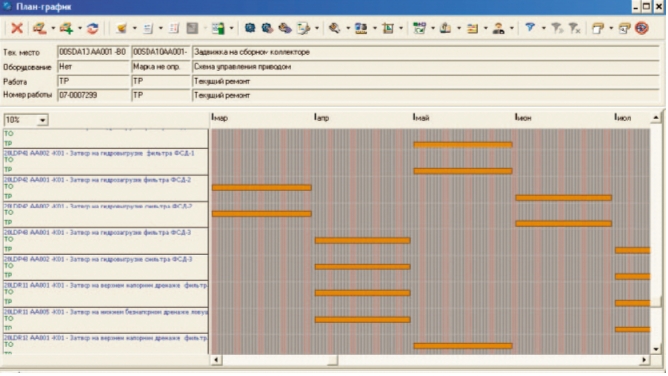
Это создает условия для решения важнейших задач управления ремонтами. Например, для прогнозирования и анализа вариантов «что – если» в отношении наличия или нехватки трудовых и нетрудовых ресурсов, соблюдения граничных параметров бюджета, изменения сроков выполнения работ и всего проекта. В конечном счете, принимаемые решения позволяют минимизировать время нахождения установки в ремонте.
Регистрация и обработка дефектов и отказов
Дефект – это невыполнение требования, связанного с предполагаемым или установленным использованием оборудования. Не всякий дефект является отказом, но многие дефекты являются предвестниками отказа, и потому они дают важную информацию о рисках. Очевидно, что возникновение дефекта, предвещающего появление критического отказа, свидетельствует о возрастании риска. И наоборот, дефект, не предвещающий никакого отказа, не влияет на величину риска. Анализ дефектов позволяет качественно или количественно оценивать риск. Таким образом, поток дефектов является источником ценной информации [3].
Используя ИСУ ТОиР, предприятие может классифицировать дефекты по тяжести последствий отказа, который они предвещают.
Кроме того, дефект может быть снабжен оценкой, отражающей вероятность трансформации дефекта в отказ. Электронный журнал дефектов (ЭЖД) позволяет оперативному персоналу регистрировать дефекты с привязкой к оборудованию, на котором они возникли, а ремонтному персоналу – видеть эти дефекты, анализировать их и планировать работы по их устранению с учетом класса (критичности) дефекта.
Наиболее очевидные преимущества ЭЖД – прозрачность процесса регистрации и устранения дефектов, повышение оперативности взаимодействия персонала. Но при переходе к ЭЖД появляются совершенно новые возможности, отсутствовавшие при бумажном журнале. Существенным обстоятельством является то, что в ЭЖД оператор не вводит вручную наименование оборудования, фамилии персонала и прочие реквизиты, а выбирает их из заранее заполненных справочников. Тем самым обеспечивается однозначная привязка дефекта к оборудованию и лицам, обнаружившим и устранившим дефект.
С помощью ЭЖД можно проследить «историю болезни» единицы оборудования, обнаружить повторные дефекты, найти единицы оборудования с наибольшим количеством дефектов. В этом случае ЭЖД становится инструментом для автоматизированного анализа повреждаемости и оценки риска. Результаты оценки риска используются при планировании работ по устранению зарегистрированных в ЭЖД дефектов и предупреждению отказов и, соответственно, простоев оборудования в ремонтах. При большом количестве оборудования ЭЖД является необходимым для того, чтобы эта деятельность была реально выполнимой.
При использовании ЭЖД пользователь может получить данные по ранее обнаруженным дефектам как на данной единице оборудования, так и на всем аналогичном оборудовании. При этом нетрудно отделить те дефекты, которые обладают теми же или аналогичными проявлениями.
Исходя из полученных таким образом сведений, можно прогнозировать уже сами дефекты, и ресурсы, которые могут потребоваться для его устранения.
Согласование с производственной программой
Деятельность нефтеперерабатывающего предприятия оценивается целым рядом показателей, таких как показатели объема производства продукции, себестоимости продукции, прибыли, рентабельности и т. д.
При этом показатели находятся в динамике, изменяются во времени по объективным причинам. В числе этих причин – нестабильность характеристик сырья, химический и фракционный состав которого может существенно изменяться. Это приводит к неоптимальным режимам оборудования, как следствие – к снижению его эффективности, это также отражается на качестве продукции, и на производственных показателях, которые становятся нестабильными во времени.
Если при этом оперировать только итоговыми за период показателями по ремонтной деятельности, то вклад ТОиР в снижение производственных показателей станет известным только к концу этого периода, когда время на корректирующие действия будет упущено.
В этой связи важно, чтобы показатели процессов ТОиР тоже можно было представить и анализировать в динамике, в реальном масштабе времени, как по текущим, так и по прогнозным значениям.
График простоев установок в ремонтах должен быть привязан к производственной программе и целевым показателям предприятия. Это позволит корректно и точно учитывать ремонтную составляющую себестоимости, вклад простоев в ремонтах в сокращение текущего значения рентабельности. Очевидно, что оперативная информация по ТОиР не может быть получена и проанализирована без соответствующей информационной системы.
Внедрение ИСУ ТОиР
НПП «СпецТек» обладает 20-летним опытом консультационных услуг и внедрения информационных систем в области управления ТОиР, обладает полной технологией выполнения таких проектов на базе программного комплекса TRIM собственной разработки. В арсенале компании имеются как небольшие экономичные проекты, выполняемые в течение двух месяцев на основе типовой платформы TRIMPMS, так и проекты на крупных предприятиях на основе решения «TRIM-Технический менеджмент», выполняемые в несколько этапов, включая пилотный проект. В общем виде состав этапов полномасштабного проекта приведен на рис. 4.
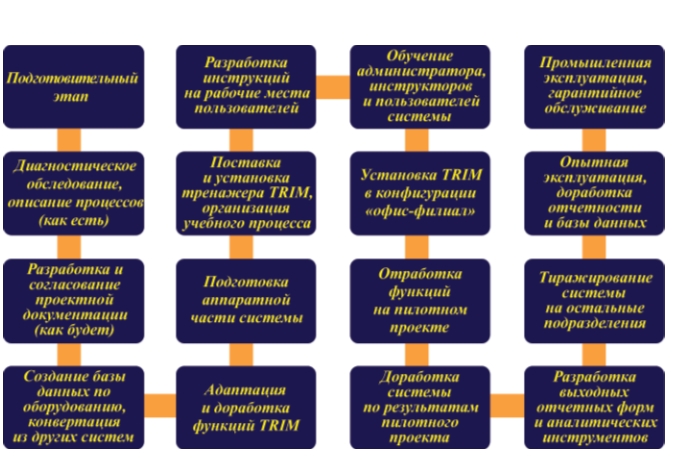
Проект обычно начинается с разработки проектной документации (техническое задание, спецификации). Обязательный этап проекта – сбор данных по оборудованию (паспорта, инструкции, чертежи, схемы, регламенты, нормативы и т.д.) и наполнение ими базы данных ИСУ ТОиР. Не менее важной является разработка подсистемы анализа данных и отчетности, поскольку именно она позволяет превратить данные в информацию. Часто в рамках проекта выполняется интеграция ИСУ ТОиР с другими системами предприятия [4], чтобы обеспечить автоматический обмен данными – с системой бухгалтерского учета, системой управления кадрами, АСУ ТП и т.д. Роль интеграционного шлюза выполняет конвертер, разработка и настройка которого осуществляется под конкретный проект.
Подготовка пользователей ИСУ ТОиР, разработка регламента эксплуатации системы и руководств пользователей – также неотъемлемая часть проекта. Без этого система фактически не будет работать.
Наконец, чисто технический этап – развертывание системы на аппаратных ресурсах заказчика и выполнение пуско-наладочных работ.
Сопровождение на этапе опытной эксплуатации и гарантийное обслуживание системы после ввода ее в промышленную эксплуатацию помогает заказчику плавно войти в режим повседневного использования системы.
Например, в декабре 2013 г. специалисты НПП «СпецТек» начали работу по внедрению ИСУ ТОиР на нефтеперерабатывающих заводах ООО «Холдинговая компания «КЕМ-ОЙЛ». Система должна обеспечить необходимую прозрачность и управляемость процессов ТОиР, создать условия для реализации принципа принятия решений на основании объективных данных, а также предоставить инструменты автоматизации деятельности в сфере ТОиР, которые просто необходимы такому крупному предприятию. Проект будет выполняться на программной платформе EAMсистемы TRIM.
В январе 2014 г. Международная организация по стандартизации выпустила новую серию стандартов ISO 55000 «Asset management». Их выход стал итогом многолетней деятельности специалистов и сообществ по консолидации знаний в области управления активами [5].
Согласно этим стандартам, к активам относится любой объект, имеющий потенциальную или действительную ценность для организации, в том числе: оборудование, запасы, объекты недвижимости. Область применения стандартов охватывает весь жизненный цикл актива на предприятии, в том числе процессы ТОиР.
При этом информационной системе в стандартах ISO 55000 отводится важная роль средства поддержки.
Как указано в стандарте, необходимость в информационной системе обусловлена тем, что необходимо решать множество проблем, связанных со сбором, верификацией и консолидацией данных об активах для того, чтобы преобразовать их в информацию об активах. Создание, контроль и документирование этой информации являются критическими функциями системы управления активами.
Разработкой российской версии стандартов ISO 55000 занимается НПП «СпецТек» в рамках деятельности Технического комитета по стандартизации №86 «Управление активами». Комитет создан на базе НПП «СпецТек» приказом Росстандарта №979 от 29.08.2013.
Выход стандартов международных, а затем и российских, в обозримом будущем повлечет за собой создание системы сертификации на соответствие этим стандартам.
В этой связи, несомненно, потребность предприятий в информационных системах управления активами, в том числе системах ИСУ ТОиР, будет возрастать.
Список литературы
- Антоненко И.Н. Управление техобслуживанием и ремонтом химического предприятия: нужна ли автоматизация?// Химическая техника. 2004. №3.
- Антоненко И.Н. Ремонты и техническое обслуживание: какое программное обеспечение использовать для управления?//Химическая техника. 2009. №1.
- Антоненко И.Н., Кац Б.А. Анализ рисков и электронный журнал дефектов//Химическая техника. 2013. №3.
- Кац Б.А. Взаимодействие информационной системы ТОиР с другими АСУ предприятия//Автоматизация в промышленности. 2013. №8.
- Иорш В.И., Крюков И.Э., Антоненко И.Н. Международные стандарты в области управления физическими активами// Вестник качества. 2012. №4.