Авторы: Л.Ю. Довгалов, А.В. Ушакова, Е.Ю. Ушакова (ООО НТП «Экор»).
Опубликовано в журнале Химическая техника №7/2018
В статье представлены новые современные методы мониторинга технологических процессов в производстве аммиачной селитры. Использование специализированных контроллеров позволяет вывести мониторинг процесса на качественно новый уровень: повысить надежность и точность измерений, а также обеспечить передачу данных в аналоговом и цифровом виде в системы SCADA.
Системы контроля процессов нейтрализации и массовой доли воды в плаве аммиачной селитры позволяют осуществить контроль и автоматизацию основных процессов, хорошо интегрируются в систему автоматизации производства и позволяют оптимизировать важные технологические процессы.
В производстве аммиачной селитры требуется не только контроль параметров технологического процесса, но и автоматическое поддержание их в оптимальном режиме. Важнейшим процессом в производстве аммиачной селитры является процесс нейтрализации. Рациональное ведение процесса нейтрализации дает возможность снизить расход азотной кислоты и аммиака, уменьшить их выбросы в окружающую среду с соковым паром, снизить коррозионные разрушения оборудования, повышает безопасность производства, поскольку при нарушениях возможны взрывы и пожары (из-за присутствия нитритов или самопроизвольного терморазложения аммиачной селитры) [1].
Оптимальным для процесса нейтрализации является стехиометрическое соотношение азотной кислоты и аммиака. Избыток азотной кислоты приводит к ее повышенным потерям, терморазложению и увеличению коррозионного изнашивания оборудования. Избыток аммиака также приводит к его повышенным потерям и резкому загрязнению окружающей среды, а также к образованию взрывоопасного нитрита аммония.
Таким образом, чем точнее осуществляется контроль и регулирование процесса, тем более эффективно производство. Требования к точности регулирования в настоящее время еще более возрастают при переходе на новые технологии получения аммиачной селитры.
Известные способы управления процессом нейтрализации по рН раствора аммиачной селитры [2] и рН сокового пара имеют недостатки. Они связаны, прежде всего, с необходимостью предварительной подготовки пробы (разбавление, охлаждение, конденсация). Поскольку на подготовку пробы требуется время, возникает задержка между изменением состава среды и измерением. Это не дает возможности качественно управлять процессом. Существенным недостатком также является потеря работоспособности датчиков рН вследствие образования загрязнений и осадков. Кроме того, замер рН не дает возможности количественного определения концентрации кислоты или аммиака.
Использование электрохимических методов позволило создать уникальную систему контроля процессов нейтрализации [3], свободную от перечисленных недостатков.
Работа системы основана на определении ряда электрохимических параметров:
- редокс-потенциала технологической среды;
- токов окисления ОН-ионов и восстановления Н+-ионов;
- потенциала поверхности оборудования.
Редокс-потенциал (рис. 1) раствора аммиачной селитры, токи окисления и восстановления ионов (рис.2), потенциал оборудования зависят от состава технологической среды. Кроме того, потенциал оборудования характеризует его коррозионное состояние.
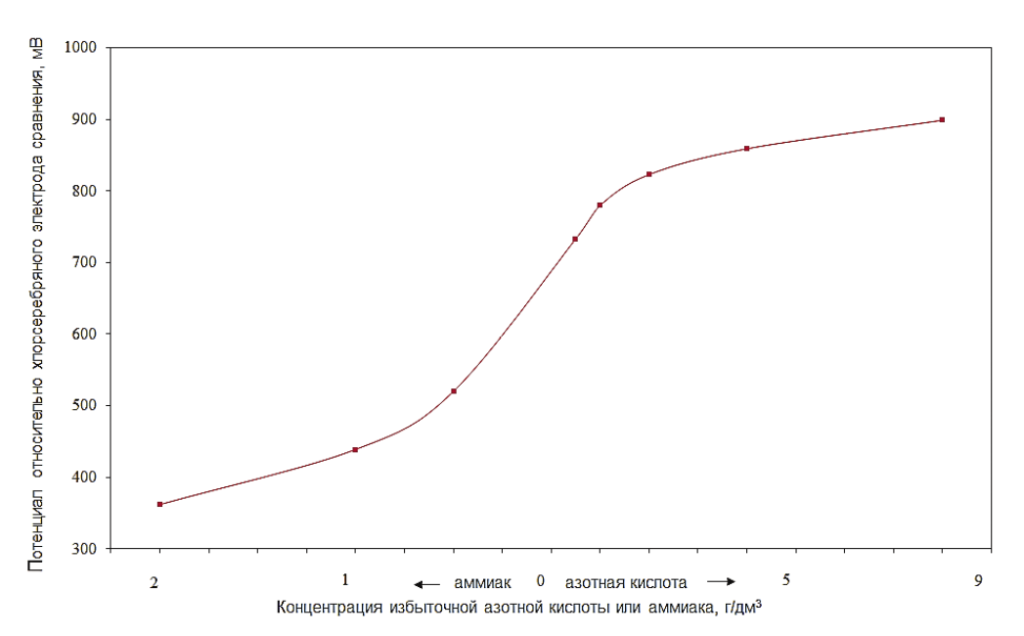
Как видно из рис. 1, редокс-потенциал зависит от концентрации аммиака и азотной кислоты. С уменьшением концентрации аммиака и увеличением концентрации азотной кислоты редокс-потенциал увеличивается, а в нейтральной области наблюдается скачок потенциала.
Аналогично меняется и потенциал поверхности оборудования из коррозионно-стойкой стали. При этом потенциал поверхности коррозионно-стойкой стали характеризует ее коррозионное состояние, поскольку имеется четкая зависимость скорости коррозии от потенциала поверхности стали [4]. При нерациональном ведении процесса нейтрализации (т.е. высоком содержании избыточной азотной кислоты) потенциал оборудования смещается в положительную сторону и находится в области локальной коррозии.
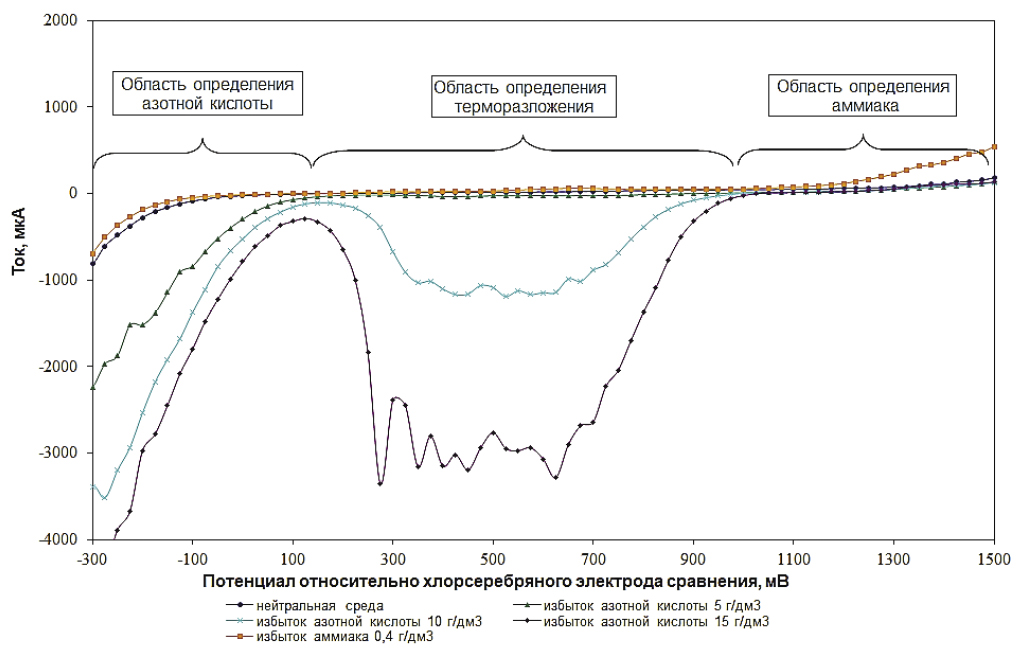
На рис. 2 представлены зависимости ток–потенциал для раствора аммиачной селитры с различным содержанием азотной кислоты и аммиака. Как видно, при определенных потенциалах имеется линейная зависимость токов восстановления Н+-ионов от концентрации азотной кислоты и токов окисления ОН-ионов от концентрации аммиака. По значению токов окисления–восстановления система позволяет количественно (в г/дм3) определять концентрацию азотной кислоты и аммиака в широком диапазоне концентраций.
Система обеспечивает контроль процессов нейтрализации на всех стадиях производства аммиачной селитры и состоит из необходимого числа измерительных каналов (порядка 10).
Измерительный канал системы включает датчик, барьер искрозащиты, потенциостат, контроллер (рис. 3). Информация передается в рабочую станцию в SCADA.
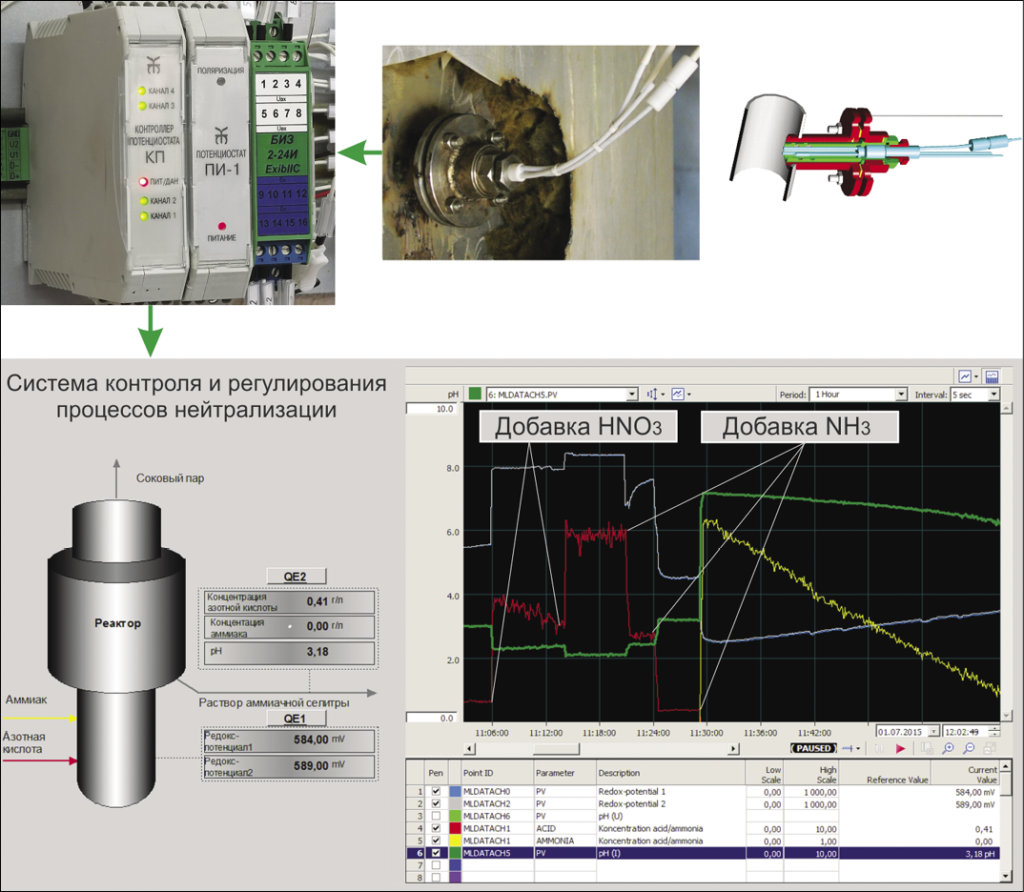
Датчики устанавливаются непосредственно в аппараты и трубопроводы производства аммиачной селитры. Например, в аппарате использования тепла нейтрализации (аппарат ИТН) датчики установлены в реакционной зоне аппарата и в трубопроводе выхода раствора из аппарата. Датчик состоит из измерительного поляризуемого электрода и электрода сравнения. Конструкция датчика концентрации обеспечивает его эксплуатацию при повышенных температурах (до 195°С) и давлениях (до 2 МПа). В загрязненных средах имеется возможность непрерывной электрохимической и механической (вибрационной) очистки измерительного электрода от загрязнений и осадков.
Работу датчика обеспечивает потенциостат, который управляет датчиком и получает от информацию об электрохимических параметрах рабочей среды (окислительно-восстановительный потенциал раствора в реакционной зоне, потенциал поверхности оборудования, токи окисления ОН-ионов и восстановления Н+-ионов, а также соотношение этих токов).
Контроллер управляет работой потенциостата, обрабатывает полученную от него информацию и определяет состав среды в точке контроля. По измеренным параметрам контроллер вычисляет концентрацию азотной кислоты или аммиака в технологическом потоке и выдает управляющий сигнал на регулятор расхода азотной кислоты или аммиака, тем самым поддерживая оптимальное протекание процесса нейтрализации.
Контроллеры позволяют организовать автономные измерительные каналы, повысить надежность и точность измерений, а также обеспечить передачу данных в аналоговом и цифровом виде в системы SCADA.
Для обеспечения искрозащиты используются барьеры.
Система внесена в Реестр средств измерений Российской Федерации.
В настоящий момент система внедрена на производствах аммиачной селитры в Российской Федерации, Украине, Казахстане, Узбекистане, Грузии, Литве, Сербии, Польше, Алжире.
По отзывам, применение системы дало возможность снизить выбросы в окружающую среду, повысить качество аммиачной селитры, снизить энергозатраты, уменьшить коррозионные разрушения оборудования.
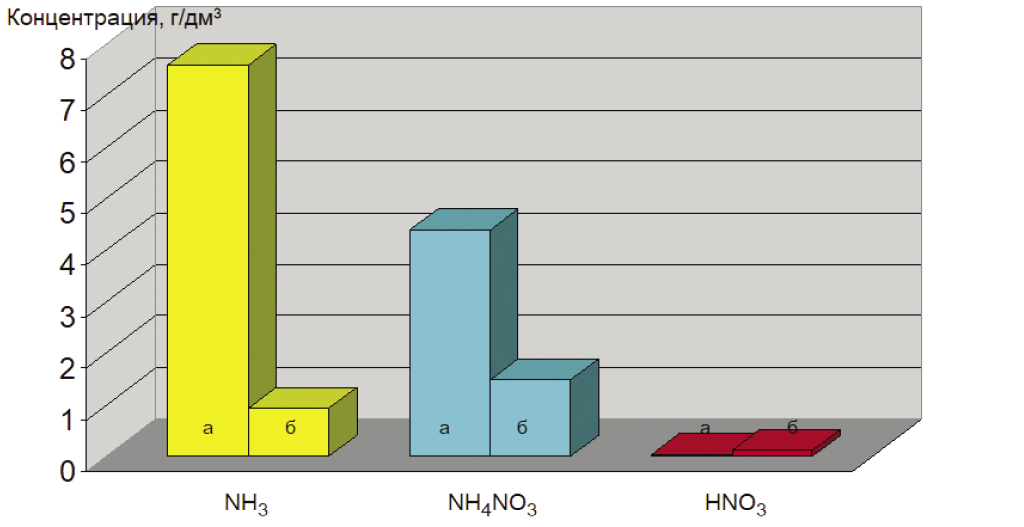
а – до внедрения системы; б – после внедрения системы
На рис. 4 показано снижение выбросов в окружающую среду с конденсатом сокового пара в ПАО «Северодонецкое объединение «Азот».
В настоящее время система получила развитие в части новых методов и средств контроля. Так, система была дополнена методами контроля, которые позволили определять следующие параметры:
- скорость терморазложения аммиачной селитры;
- рН плава, подаваемого на грануляцию, по редокс-потенциалу;
- массовую долю воды в плаве по температуре кристаллизации.
Для определения интенсивности терморазложения используется зависимость токов восстановления продуктов терморазложения аммиачной селитры от скорости терморазложения при определенных потенциалах (см. рис. 2) [5].
Контроль скорости терморазложения позволяет уменьшить потери аммиачной селитры, так как при неоптимальном ведении процесса они могут достигать существенных значений (в денежном выражении – несколько сотен тысяч долларов в год для агрегата АС-72).
При производстве аммиачной селитры требуется упаривание раствора аммиачной селитры до плава необходимой концентрации (95,0–99,8%) для дальнейшего получения гранул. Контроль процесса выпарки необходим для снижения энергозатрат и обеспечения качества товарного продукта (снижения брака).
В настоящее время контроль плава после стадии выпарки выполняется периодически с помощью трудоемкого лабораторного анализа. Это не дает возможности своевременно выявлять причины и источники попадания влаги в конечный продукт.
Для непрерывного автоматического контроля процесса выпарки была разработана система контроля массовой доли воды в плаве аммиачной селитры. Работа системы основана на зависимости температуры кристаллизации плава от концентрации в нем воды (рис. 5).
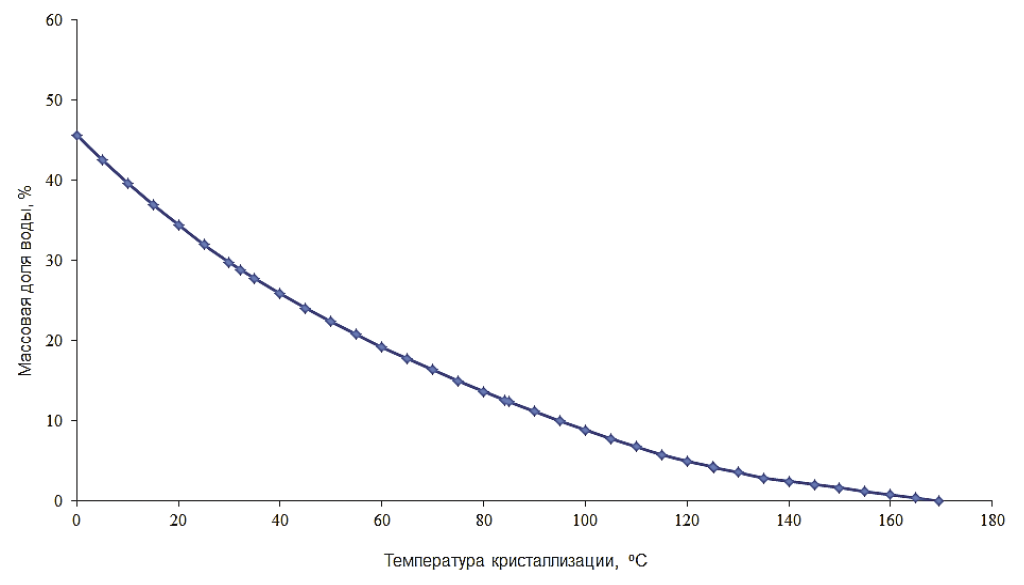
Измерительный канал системы состоит из датчика концентрации, контроллера фазового перехода, клапана подачи хладагента (рис. 6). Датчик концентрации устанавливается в поток плава аммиачной селитры и представляет собой теплообменник с датчиком температуры. Через датчик осуществляется проток плава. В теплообменник периодически по сигналу с контроллера с помощью клапана подается хладагент, например воздух. При этом плав охлаждается до температуры кристаллизации.
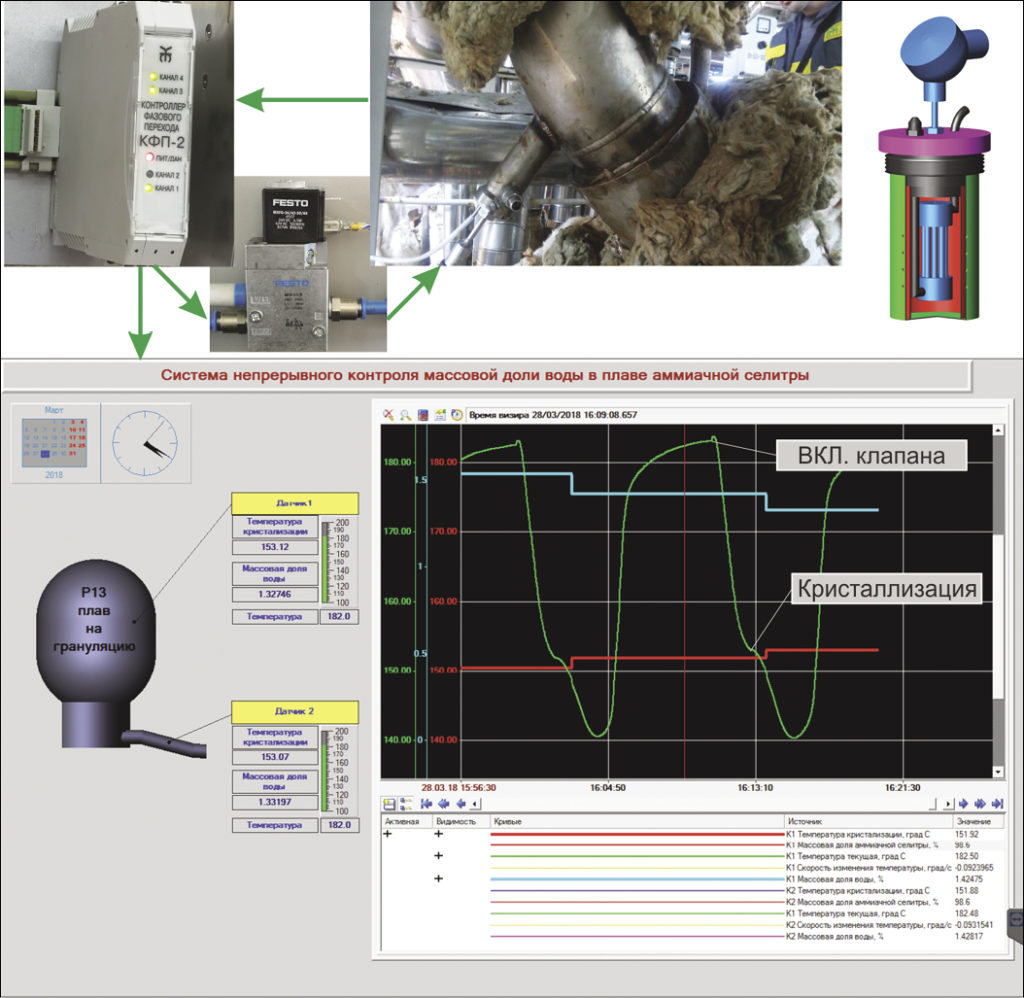
Контроллер по кривой охлаждения определяет температуру кристаллизации и массовую долю воды в плаве и передает данные в цифровом и аналоговом виде в SCADA.
Система позволяет в онлайн режиме контролировать процесс выпарки, что позволяет обеспечить качество конечного продукта (снизить количество брака), снизить энергозатраты на выпарку, а также заменить трудоемкий лабораторный анализ.
Кроме того, система позволяет своевременно определять причины и источники попадания влаги в плав аммиачной селитры.
Системы контроля процессов нейтрализации и массовой доли воды в плаве аммиачной селитры позволяют осуществить контроль и автоматизацию основных процессов, хорошо интегрируются в систему автоматизации производства и позволяют оптимизировать важные технологические процессы.
Список литературы
- Справочник азотчика. 2-е изд. М.: Химия, 1987, 464 с.
- Иванов М.Е., Олевский В.М., Поляков Н.Н. и др. Технология аммиачной селитры. М.: Химия, 1978, 312 с.
- Пат. Украины №43404. МПК (2006) G01N 27/48. Спосiб автоматичного управлiння процесом нейтралiзацii у виробництвi амiачно? селiтри в апаратi використання тепла нейтралiзацii.
- Новицкий В.С., Писчик Л.М. Коррозионный контроль технологического оборудования. Киев: Вид. Наукова думка. 2001. 172 с.
- Пат. Украины № 59482. МПК (2006) G01N 27/48. Спосiб вольтамперометричного визначення оксидiв азоту в кислих середовищах.