Автор: В.Н. Глаголев (ОАО «НИИК»)
Опубликовано на портале «Химическая техника», февраль 2021
Теплообменное оборудование в процессе своей эксплуатации подвергается различного рода воздействиям, которые в общем виде могут носить механический, коррозионный, эрозионный характер и т.п. Одной из основных причин преждевременного выхода из строя кожухотрубчатых теплообменников, как правило, являются повреждения теплообменных труб.
Для исключения аварийных ситуаций дефекты теплообменных труб должны своевременно обнаруживаться и классифицироваться по степени опасности для принятия соответствующих мер (глушение труб или продолжение эксплуатации при периодическом контроле).
Выявление дефектов в теплообменных трубах – достаточно трудоемкая и дорогостоящая процедура. И, тем не менее, во многих случаях она вполне оправдана, поскольку любая непредвиденная остановка из-за пропуска коррозионно-агрессивной и токсичной среды может быть чревата для предприятия значительными убытками.
Выявление дефектов в теплообменных трубах – это первый этап по обеспечению безопасной эксплуатации теплообменников. В настоящее время он осуществляется с помощью внутритрубной диагностики, в основу которой положен вихретоковый метод контроля. При внутритрубной диагностике этот этап сопряжен с определенными трудностями, заключающимися как в правильной идентификации дефектов, так и в точном определении их местонахождения и размеров.
Второй этап – оценка степени опасности выявленных дефектов. На основе результатов этого этапа принимается решение о ремонте либо продолжении подконтрольной эксплуатации. Это этап не менее важен, чем предыдущий, что обусловлено тем, что далеко не все выявляемые дефекты представляют реальную угрозу для теплообменных труб, и их глушение вовсе не обязательно.
Одним из основных в нашей стране способов оценки остаточной прочности и работоспособности оборудования с коррозионными дефектами является гидравлическое испытание. Недостатки этого способа как с экономической, так и технической точки зрения известны и подробно освещены в литературе, например [1]. Принципиальным недостатком гидравлических испытаний является невозможность обнаружения дефектов «докритических» размеров, но которые в процессе эксплуатации могут дорасти до размеров сквозных. Необходимо отметить, что во многих зарубежных странах проведение гидравлических испытаний для этих целей также признано нецелесообразным. В связи с этим для оценки остаточной прочности труб с дефектами желательно использование другого, простого и достаточно надежного метода.
Для правильной оценки возможности дальнейшей эксплуатации трубы с дефектом требуется знание большого числа факторов, таких как прочность материала трубы, действующие напряжения, число и характер распределения дефектов, механизм их роста и др. При этом одни из них оказывают на прочность трубы большее значение, другие – меньшее. В отношении поверхностных дефектов может быть показано, что их глубина – наиболее важный параметр, характеризующий степень опасности. Далее идут осевая длина и окружная длина. В общем случае глубина определяет начало разрушения, а осевая длина – вид разрушения (утечка или разрыв). И хотя для определения истинной опасности дефекта должны использоваться несколько параметров, такие доминирующие факторы, как глубина и осевая длина дефекта, могут быть применены в упрощенных математических выражениях для получения приблизительного, но достаточно безопасного прогноза поведения дефекта в трубе.
Степень опасности поверхностных дефектов на трубах и пригодность последних к эксплуатации в настоящее время принято оценивать расчетными методами. Одним из наиболее известных и широко применяемых в мировой практике методов, является критерий B31G из стандарта ANSI/ASME B31G [2]. Критерий B31G основан на полуэмпирической зависимости, полученной с использованием методов механики разрушения. Зависимость базируется на модели размеров поврежденной зоны, анализе трещины (дефекта) Фолиаса, расположенной вдоль оси находящегося под давлением цилиндра (трубы, сосуда), и определенного эмпирическим путем соотношения между глубиной дефекта и толщиной стенки трубы [3].
В общем виде выражение «критерий B31G» базируется на следующем уравнении:
где σр – величина разрушающих кольцевых напряжений;
σт – минимальный нормативный предел текучести материала трубы;
A – площадь проекции (профиля) дефекта на продольное сечение стенки трубы;
А0 = Ls – площадь продольного сечения стенки трубы, на которую проецируется дефект;
L – глубина дефекта;
s – толщина стенки трубы;
М – коэффициент Фолиаса, рассчитанный для длины дефекта L:
d – наружный диаметр трубы.
Общая длина зоны коррозионного повреждения вдоль оси трубы принимается равной L, даже если она не располагается вдоль оси трубы.
Для максимальной глубины коррозионного повреждения t:
Прочностной критерий работоспособности обычно имеет вид
где n, [n] – соответственно фактический и нормативный коэффициенты запаса прочности.
Фактический коэффициент запаса прочности для трубы с дефектом [4]
n = σр/σm, (5)
где σm – напряжения, возникающие в теплообменной трубе.
Способность поврежденного участка трубы выдерживать эксплуатационные нагрузки определяется на основании оценки количества и распределения потерь металла в процессе эксплуатации и снижения предела прочности (предела текучести) материала при этом. Если расчетная способность выдерживать давление превышает максимально допустимое рабочее давление на достаточную величину (запас прочности), то труба с дефектом сохраняет остаточную работоспособность, и её можно продолжать эксплуатировать. В противном случае её необходимо заглушить.
И хотя первоначально стандарт ANSI/ASME B31G разрабатывался для трубопроводов, учитывая достаточную общность теоретических представлений, положенных в основу стандарта, в данной работе предпринята попытка использовать его при оценке остаточной прочности теплообменных труб в кожухотрубчатых теплообменниках.
Проиллюстрируем это на примере оценки остаточной работоспособности стриппинг-аппаратов установок синтеза карбамида. Стриппинг-аппарат представляет собой вертикальный кожухотрубчатый теплообменник с неподвижными трубными решетками и температурным компенсатором на кожухе. В результате ведения технологического процесса, внутренняя поверхность теплообменных труб в верхней части подвергается интенсивному эрозионно-коррозионному изнашиванию. Основной причиной изнашивания является воздействие газожидкостного потока на материал труб в зонах «вскипания» плава и ударное воздействие пузырьков газа, выделяющегося из жидкой фазы [5]. Типичные результаты вихретоковой диагностики теплообменных труб стриппинг-аппаратов, выполненные с использованием различного оборудования, представлены на рис. 1, 2.
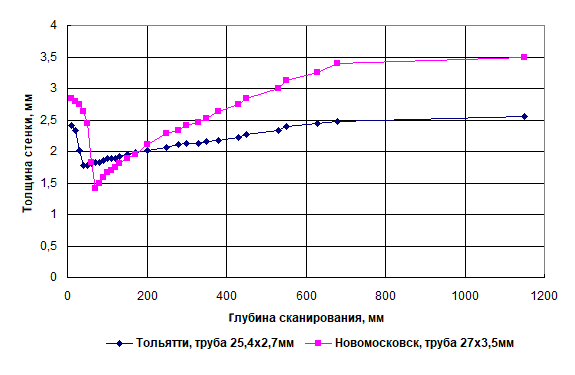
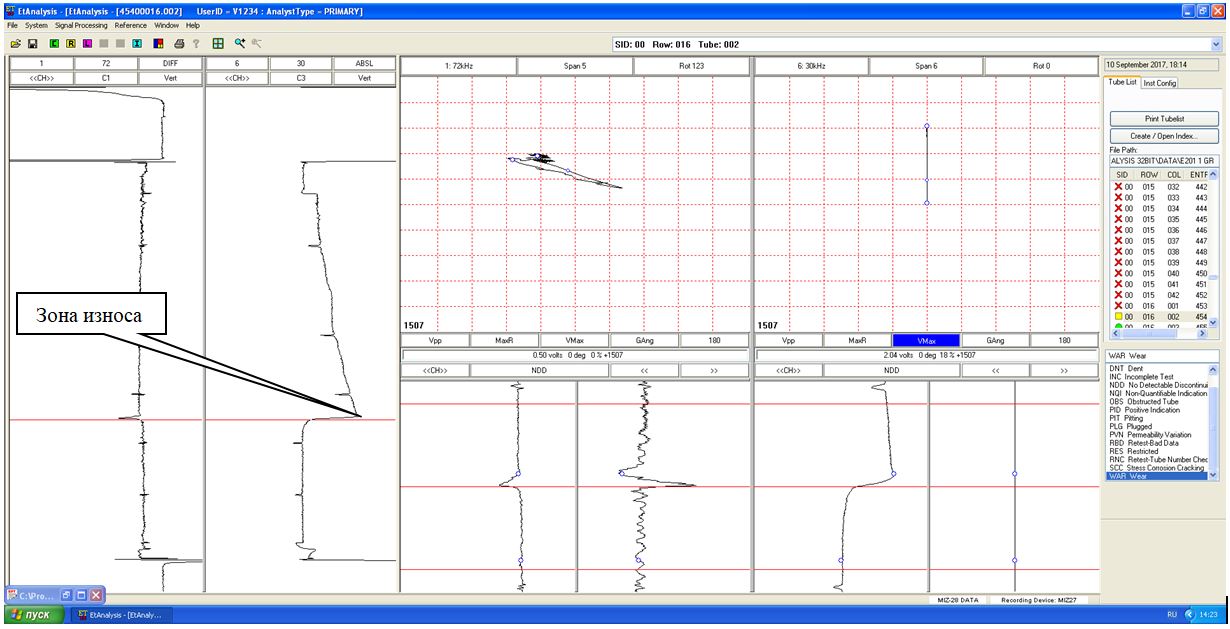
В зависимости от продолжительности эксплуатации аппаратов, глубина дефектов может достигать 30–65% номинальной толщины стенки трубы, а протяженность в осевом направлении составляет 250…2500 мм (при длине трубы 6 м).
В таблице представлены сводные данные о характерных размерах дефектов теплообменных труб, зафиксированных при вихретоковой диагностике трубных пучков стриппинг-аппаратов на различных установках карбамида за разные годы, и результаты расчета. Под расчетной толщиной в таблице принимается допустимая толщина стенки в дефектной зоне, определенная на основе критерия B31G, при которой ещё сохраняется работоспособность трубы. Необходимо отметить, что все теплообменники, представленные в таблице, на момент проведения диагностики продолжали безаварийно работать (без пропусков и разрывов труб), т.е. полностью сохраняли свою работоспособность.
Анализ таблицы показывает, что при выявленных дефектах толщина стенки трубы в зоне дефекта больше толщины, определенной расчетным путем, и остаточная работоспособность теплообменных труб ещё достаточна. Следовательно, обнаруженные дефекты не опасны, и их наличие не является препятствием для дальнейшей эксплуатации, что и подтвердилось практикой эксплуатации. В то же время, как видно из таблицы, отсутствие подобной методики в ряде случаев привело к преждевременному глушению труб.
Также необходимо отметить, что, как видно из таблицы, относительная глубина дефекта (выраженная в процентах номинальной толщины стенки трубы), до которой еще можно эксплуатировать трубу с дефектом, составляет 65–66%. Однако для исключения аварийных ситуаций и обеспечения безостановочной работы эту значение следует ограничить 60%.
Таким образом, использование этой методологии позволяет оценивать остаточную прочность теплообменных труб и минимально допустимую толщину стенки, при которой ещё сохраняется их работоспособность, и тем самым ответить на вопрос о степени опасности тех или иных дефектов. А по имеющимся данным о реальной скорости роста дефектов становится возможным прогнозировать остаточный ресурс теплообменных труб и теплообменника в целом.
Критерий B31G был разработан более 30 лет назад. Многочисленные статьи, опубликованные за это время, подтверждают справедливость этого критерия и его эффективность. В то же время сейчас признано, что с учётом вновь накопленных экспериментальных исследований, в большинстве случаев методология оценки опасности дефектов основана на слишком большом запасе прочности. Это часто приводило к необоснованным заменам и ремонтам. В связи с этим в последние годы был принят ряд новых стандартов, а часть старых, в том числе и B31G, модифицирована. Но даже использование критерия B31G в его первоначальном варианте, позволит более точно оценивать остаточный ресурс и более обоснованно подходить к вопросу о необходимости ремонта (глушения) теплообменных труб либо замене теплообменника в целом.
Список литературы
- Петров В.А. О перегрузочных испытаниях // Дефектоскопия. – 1997. №3. С. 92–98.
- ANSI/ASME B31G – 1984. Manual for determining the remaining strength of corroded pipelines. – ASME, New York.
- Kiefner J.F., Maxey W.A., Eiber R.J., Duffy A.R. Failure stress levels of flavs in pressurized cylinders// Progress in flaw growth and fracture toughness testing, ASTM STP 536, American society for testing and materials. – 1973. – P. 461–481.
- Полозов В.А. Прочность и безопасность магистральных трубопроводов// Безопасность труда в промышленности. – 2007.№5. С. 26–28.
- Потапов В.В., Макаров А.Г. Козлов В.В., Сонин И.Н. Эрозионно-коррозионный износ конструкционных материалов стриппинг-аппаратов установок синтеза карбамида // Химическая промышленность. 1988. №6. С. 24–27.