Автор: В.Н. Глаголев (ОАО «НИИК»)
Опубликовано на портале «Химическая техника», май 2021
Доля теплообменного оборудования на различных производствах химической и нефтехимической промышленности по разным оценкам составляет от 50 до 70%. И при создании новых перспективных производств эта доля имеет устойчивую тенденцию к увеличению. В условиях постоянно сокращающихся сроков остановочных ремонтов и увеличения межремонтных интервалов обеспечение безаварийной работы теплообменников является важной задачей диагностики.
Одной из основных причин преждевременного выхода из строя кожухотрубчатых теплообменников являются, как правило, повреждения теплообменных труб. Практика эксплуатации агрегатов аммиака по технологии TEC показала, что у ряда теплообменников теплообменные трубы подвергаются интенсивному разрушению. Одним из характерных примеров, является повреждение труб в паровом кипятильнике поз.105-С.
Паровой кипятильник предназначен для подогрева раствора «Бенфильд» отходящими из высокотемпературного конвектора газами и представляет собой горизонтально установленный кожухотрубчатый теплообменник с U-образными трубами и неподвижной трубной решеткой. Аппарат содержит 2035 труб типоразмера 19×2мм из стали 12Х18Н10Т.
На одном из предприятий в паровом кипятильнике поз.105-С после замены трубного пучка в 2004 г. неоднократно фиксировался переток из трубного пространства в межтрубное, о чем свидетельствовал анализ на содержание водорода в углекислом газе. Причиной этого являлась течь теплообменных труб и, как следствие, нарушение нормальной эксплуатации аппарата. Это в свою очередь приводило к аварийной остановке агрегата, поиску и глушению дефектных труб и в конечном итоге – к значительным убыткам для предприятия. В связи с этим обнаружение дефектов и обеспечение безаварийной работы кипятильника являлось актуальной задачей.
В качестве метода диагностики теплообменных труб кипятильника использовался вихретоковый метод. Как показывает обширная практика, он обладает рядом неоспоримых преимуществ, имеет высокую достоверность [1] и является основным методом эксплуатационного контроля металла теплообменных труб во всем мире. Методика основана на введении вихретокового зонда в теплообменную трубу со стороны трубной решетки и сканировании трубы по всей длине. Сигналы, возникающие при сканировании трубы, регистрируются вихретоковым дефектоскопом и затем с помощью специального ПО анализируются на предмет наличия или отсутствия дефектов.
Диагностика вновь установленного трубного пучка показала следующее. На ряде труб имелись дефекты в виде перетираний о межтрубные перегородки, и, кроме того, все трубы оказались не мерной длины, т.е. состояли из нескольких труб, сваренных встык. На каждой трубе было от одного до двух швов. На рис. 1 показаны характерные сигналы от перетираний в перегородках, на рис. 2 – сигналы от бездефектных труб со сварными швами.
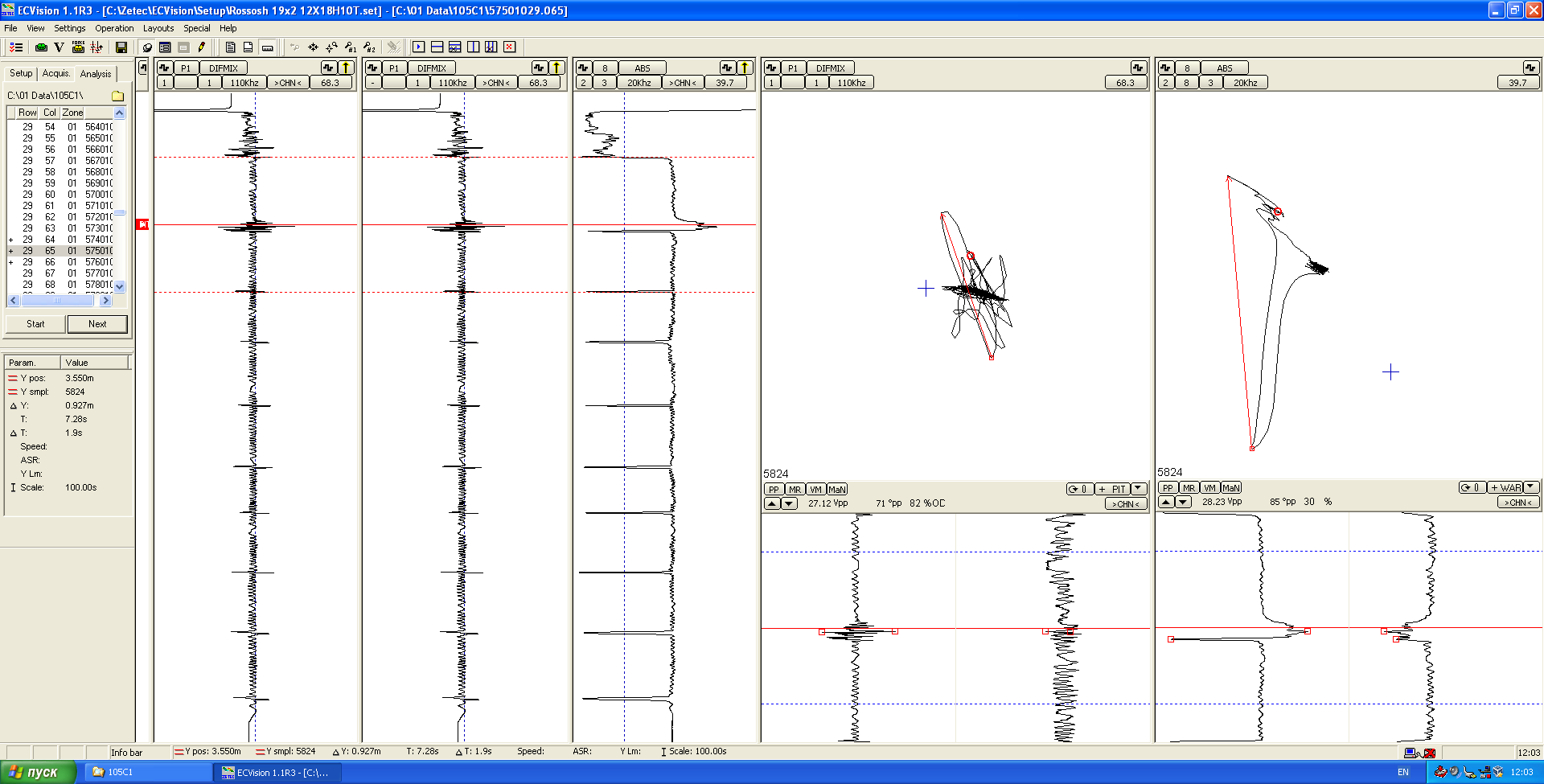

Трубы с наиболее глубокими дефектами были заглушены, но задачу безаварийной работы аппарата это решило лишь частично. В процессе последующей эксплуатации периодически фиксировались пропуски, что свидетельствовало о наличии сквозных дефектов на трубах, не обнаруженных при вихретоковом контроле. Регулярные инспекции кипятильника обнаруживали лишь новые дефекты под поддерживающими перегородками (трубы, которые, как правило, глушились), но после пуска аппарата через некоторое время пропуски фиксировались вновь. Все это приводило к внеплановым остановкам агрегата и повторному ремонту аппарата.
На рис. 3 представлена картограмма трубной доски с трубами, рекомендуемыми к глушению по результатам инспекции 2018 г. (отмечены красным цветом, черным цветом – ранее заглушенные трубы). На рис. 4 – фото трубной доски аппарата в 2020 г. Как видно, за период эксплуатации аппарата с 2018 до 2020 г. дополнительно было заглушено 35 U-образных труб. Очевидно, в этих трубах имелись дефекты, превращающиеся с течением времени в сквозные, не диагностируемые вихретоковым методом. Предположительно такими дефектами могли быть дефекты в стыковых сварных швах теплообменных труб. Косвенным подтверждением этого являлся тот факт, что в паспорте на трубный пучок, были сведения о возникновении у ряда труб перетока (т.е. сквозных дефектов) сразу после монтажа трубного пучка и пуска в эксплуатацию.
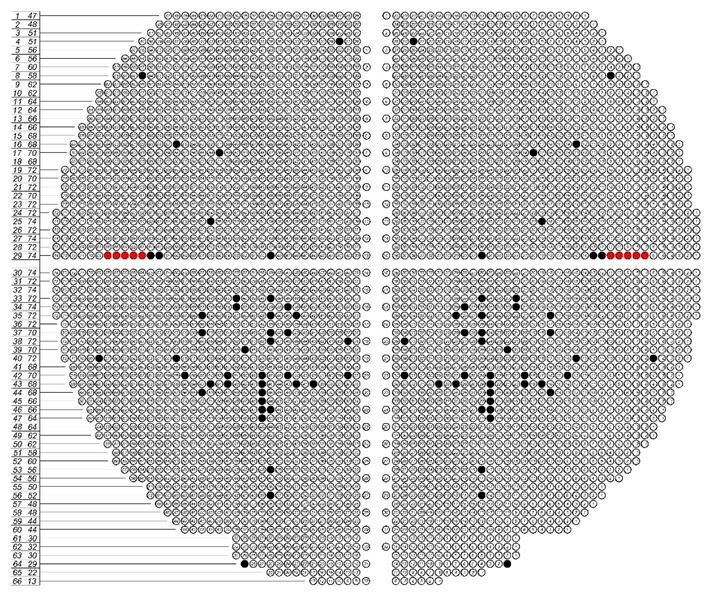
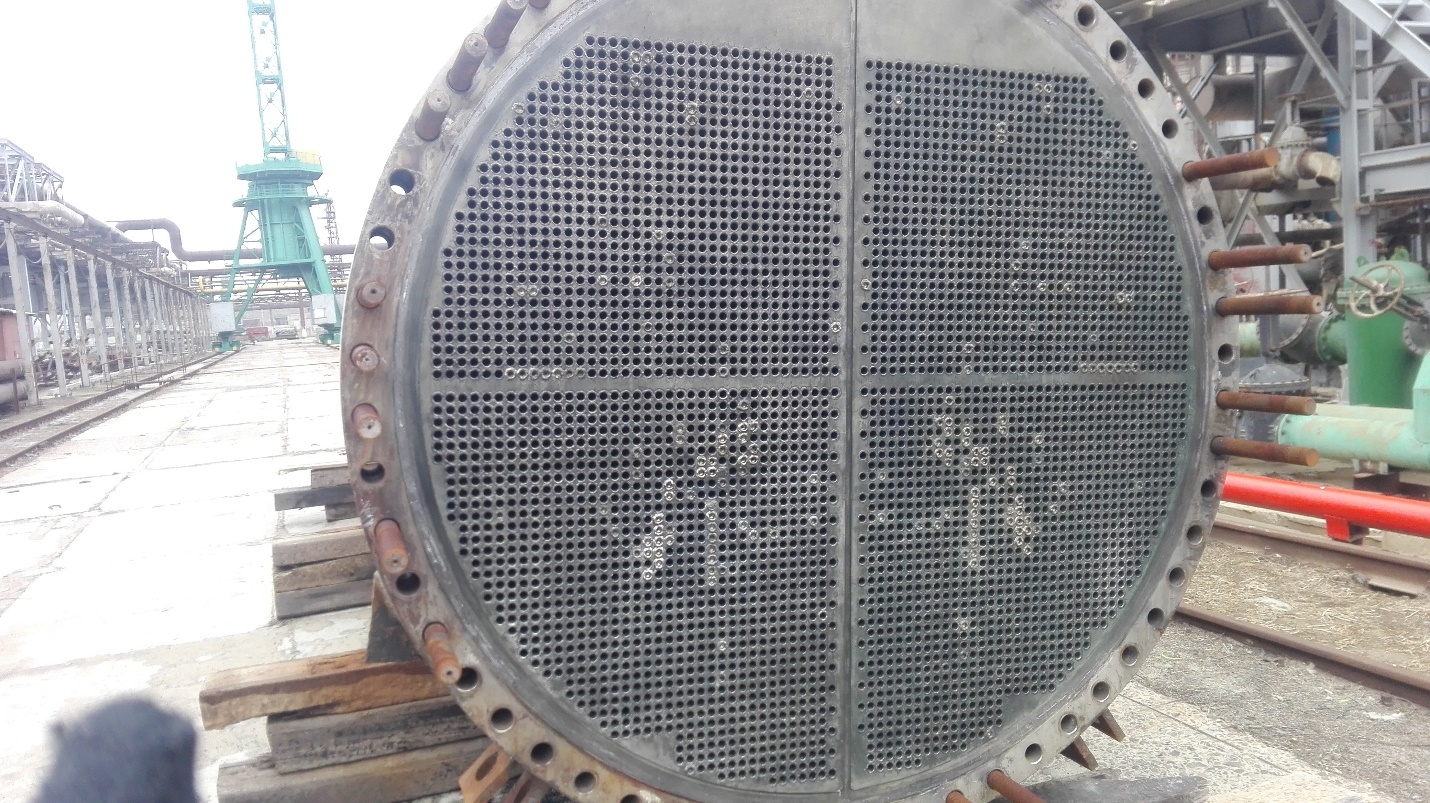
После вывода трубного пучка из эксплуатации в сентябре 2020 г. для выяснения причин разрушения теплообменных труб кипятильника были проведены дополнительные исследования, включающие повторный анализ 35 U-образных труб, потекших в процессе эксплуатации 2018–2020 г.г., и анализ образцов труб, вырезанных из демонтированного трубного пучка.
Повторный анализ 35 U-образных труб показал следующее. На ряде труб были обнаружены дефекты под перегородками, которые требовали глушения, что свидетельствовало об определенной недобраковке при проведении анализа. Но на большинстве труб никаких дефектов обнаружено не было, т.е. объективных причин для глушения таких труб в инспекцию 2018 г. также не было. Следовательно, эти трубы дали течь в результате образования сквозных дефектов, не диагностируемых вихретоковым методом.
Для поиска возможных причин разрушения теплообменных труб из демонтированного трубного пучка были вырезаны участки труб для проведения дальнейших исследований. Образцы были вырезаны из труб №0147 и 1668, выбранных случайным образом. На каждом образце имелось по одному сварному шву. Внешний вид образцов труб представлен на рис. 5, 6.
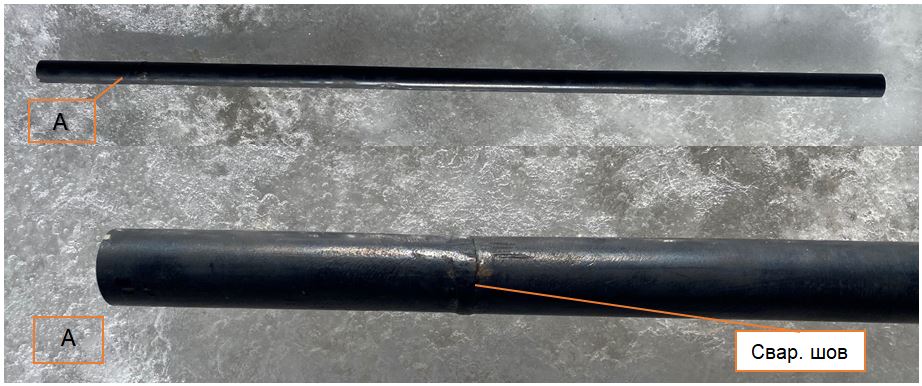
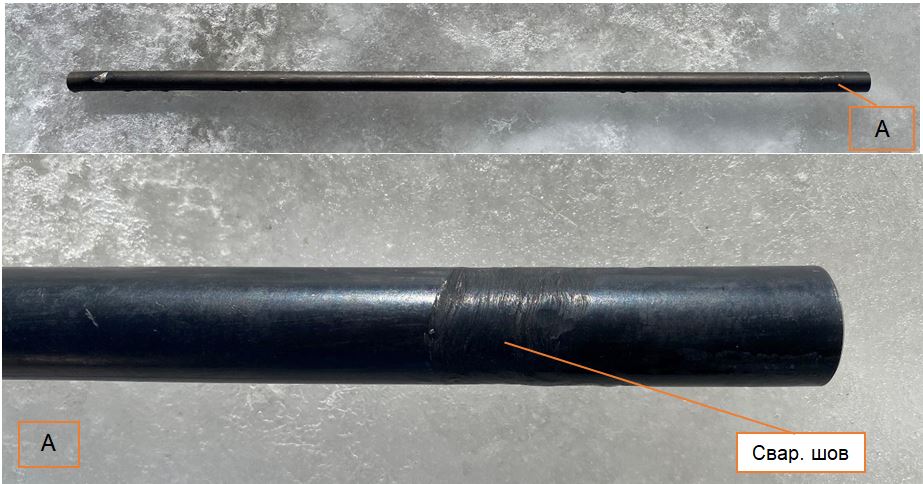
Образцы прошли вихретоковый контроль, который подтвердил наличие сварного шва на каждом образце и не выявил никаких дефектов (рис. 7, 8).
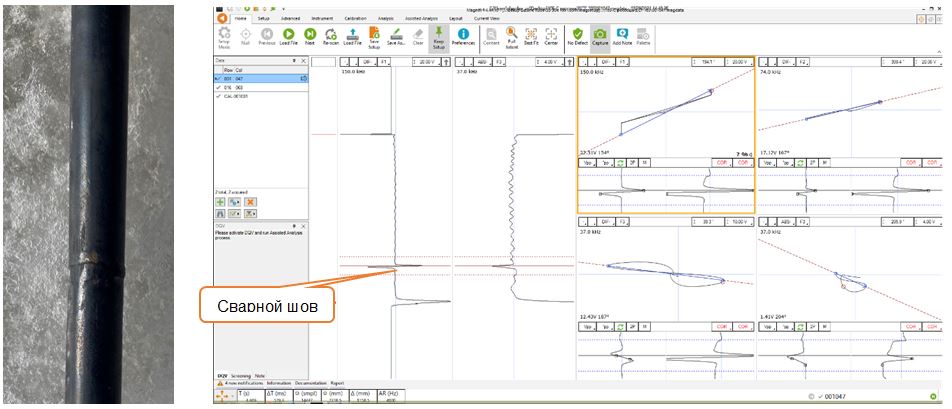
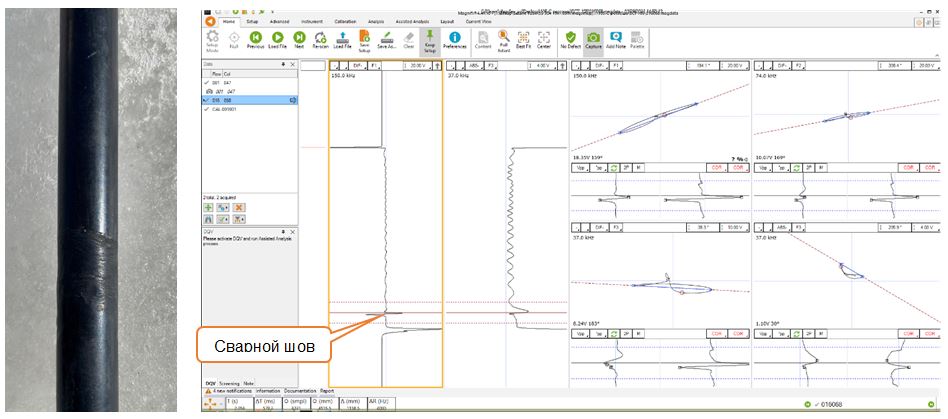
После этого образцы были разрезаны вдоль для осмотра. На наружной и внутренней поверхности основного металла обоих образцов дефектов обнаружено не было, что подтвердило результаты вихретокового контроля. На сварном шве образца из трубы №1668 был обнаружен дефект в виде непровара корня шва (рис. 9).
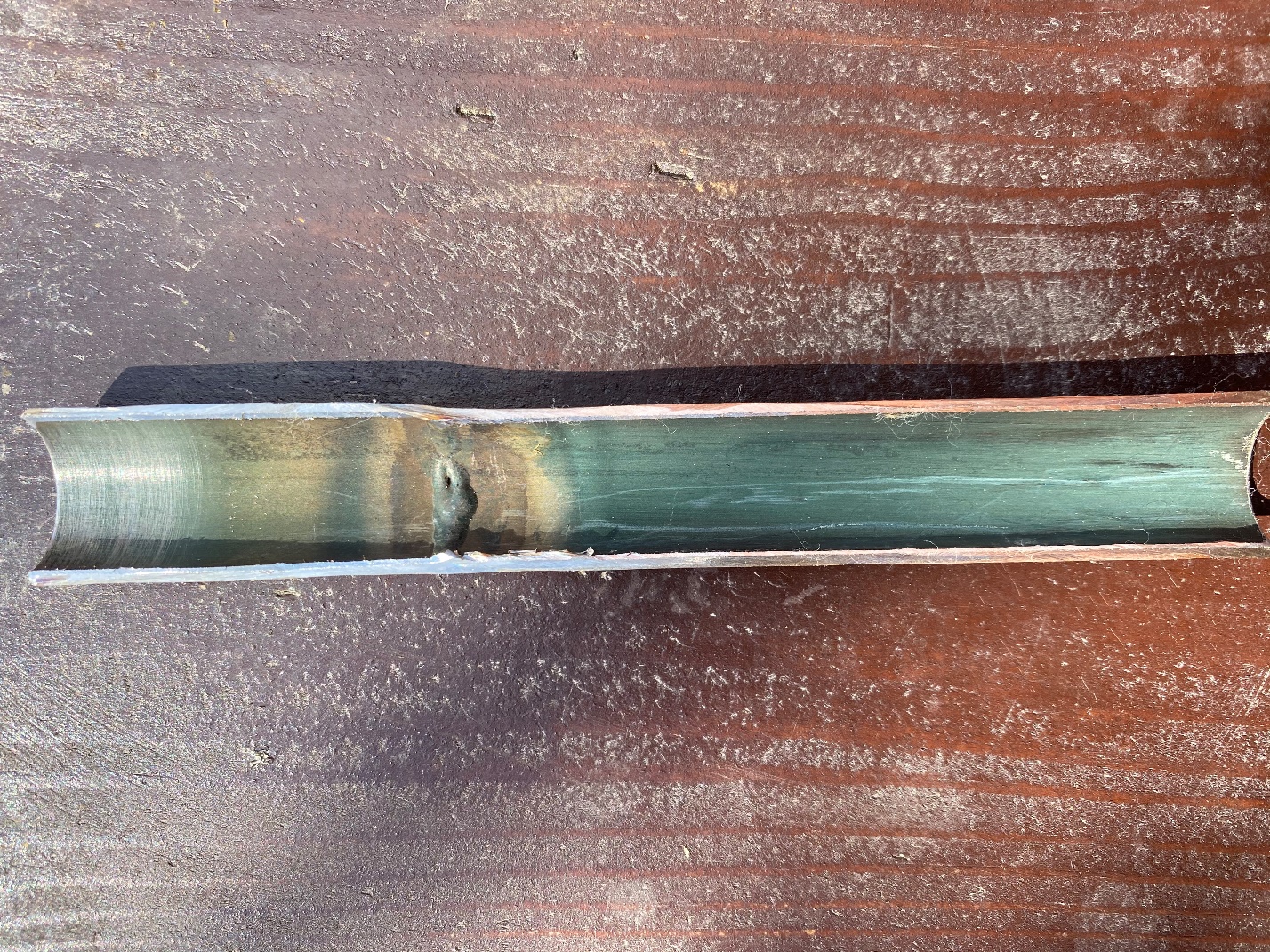
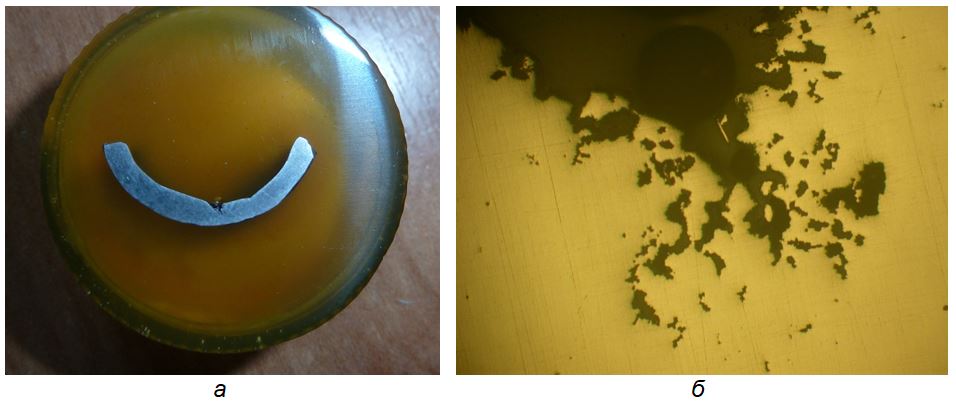
Металлография дефектного участка показала, что глубина основной части непровара составляет около 40% номинальной толщины стенки трубы, а общая глубина с учетом всех зон непровара достигает 65% (рис. 10). Этот дефект пока еще не сквозной, но через определенный период эксплуатации вполне мог бы дорасти до сквозного. Несмотря на существенную глубину, он не был обнаружен ни во время проведения инспекций теплообменника, ни при проведении исследований. И связано это в первую очередь с его расположением в сварном шве. Вариативность изменений геометрии и электрофизических свойств трубы, вызванные сварным швом, делают проблематичным применение вихретокового метода контроля с применением проходного бобинного зонда как для обнаружения подобных дефектов, так и для оценки их глубины. А учитывая случайный характер выбора труб для проведения исследований, с большой долей вероятности можно ожидать наличие подобных дефектов в сварных швах и на других трубах, в том числе и тех, которые в процессе эксплуатации давали течь.
ВЫВОДЫ
Таким образом, основной причиной разрушения теплообменных труб в данном паровом кипятильнике является перетирание труб в межтрубных перегородках и многочисленные дефекты в сварных швах. И если первый тип дефектов достаточно надежно обнаруживается вихретоковым методом контроля, то обнаружить дефекты в сварных швах этим методом не представляется возможным.
При конструировании теплообменников следует не применять теплообменные трубы, сваренные встык, а если избежать этого не удается, то уже на стадии проектирования и изготовления закладывать другие дополнительные методы контроля этих зон.
В заключение выражаю особую благодарность всем сотрудникам ОАО «НИИК», принимавшим участие в проведении исследований.
Список литературы
1. Глаголев В.Н. О достоверности вихретокового контроля теплообменных аппаратов//Химическая техника, январь 2021.