Автор: Г.А. Павлова, А.Г. Марков, А.М. Жиганьшин (ООО «МЕТАМ»).
Опубликовано в журнале Химическая техника №3/2014
Современное предприятие химической либо нефтеперерабатывающей отрасли невозможно представить без принудительной вентиляции.
Прекращение работы вентиляционного оборудования влечет остановку всего технологического комплекса предприятия, прекращение работы всех машин и механизмов. От надежной и безотказной работы систем вентиляции зависит безопасность, а зачастую и жизнь людей, поэтому вопрос технического состояния вентиляционного оборудования является актуальным. Его решение находится в основном в следующих направлениях: постоянном мониторинге и установлении технического состояния оборудования на основе применения современных методов неразрушающего контроля с оценкой остаточного ресурса и определением срока последующей безопасной эксплуатации.
Так как основные фонды взрывоопасных и химически опасных производств и объектов введены в эксплуатацию 40–50 лет назад, а реконструкция производств и объектов происходит низкими темпами, ~70% технических устройств на предприятиях уже отработали установленный ресурс безопасной эксплуатации, что чревато возможностью возникновения инцидентов и аварий.
К наиболее тяжелым последствиям, приносящим материальный ущерб и возникновение групповых несчастных случаев, приводят аварии на взрывопожароопасных производствах, которые присущи большинству промышленных предприятий. По количеству аварий, связанных с взрывами и пожарами, объекты химии и нефтепереработки находятся на первом месте. За последние годы число аварий остается на высоком уровне (рис. 1).
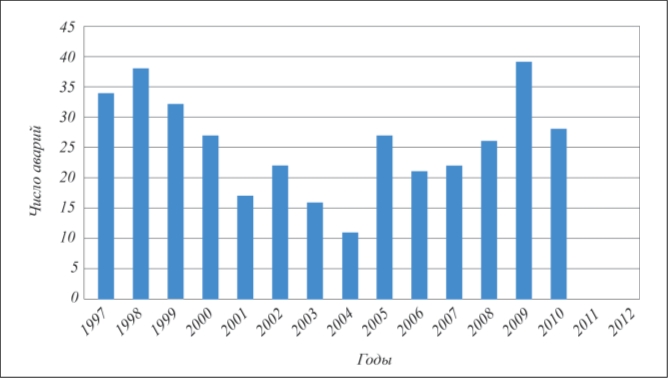
Удельные показатели аварийности и травматизма со смертельным исходом за период 1997–2012 гг., приведенные на рис. 2, также свидетельствуют о том, что за последние годы на химических и нефтеперерабатывающих предприятиях не прослеживается тенденции к снижению аварийности, несмотря на изменение общего объема производства.
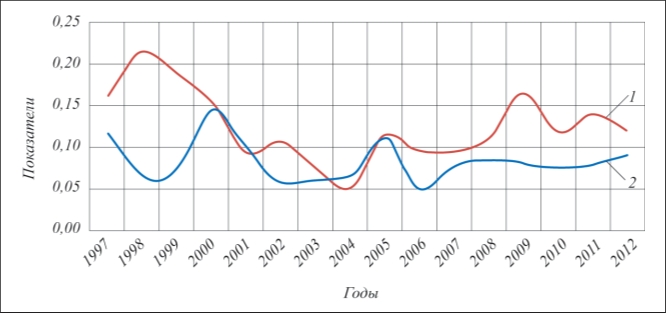
1 – удельный показатель аварийности, аварий/млн. т;
2 – удельный показатель смертельного травматизма, чел./млн. т
Учитывая большую изношенность оборудования и высокую агрессивность сред, контроль реального технического состояния вентиляционного оборудования является одним из основных методов, обеспечивающих безопасность производства в целом.
Методом, позволяющим получить до 70% информации о техническом состоянии вентиляционного оборудования, является визуальный и измерительный контроль, проводимый с целью выявления степени изнашивания, коррозии, локальной деформации, трещин и других дефектов, образовавшихся в процессе изготовления, транспортировки, эксплуатации и ремонтов. Визуальному контролю подвергаются внутренняя и наружная поверхности элементов оборудования. Наиболее типичными дефектами, обнаруженными при проведении диагностирования с помощью осмотра, являются механические и коррозионные повреждения корпуса вентилятора, разрушения рабочих колес, гибких вставок, креплений вентилятора к фундаменту. Некоторые из этих дефектов показаны на рис. 3.
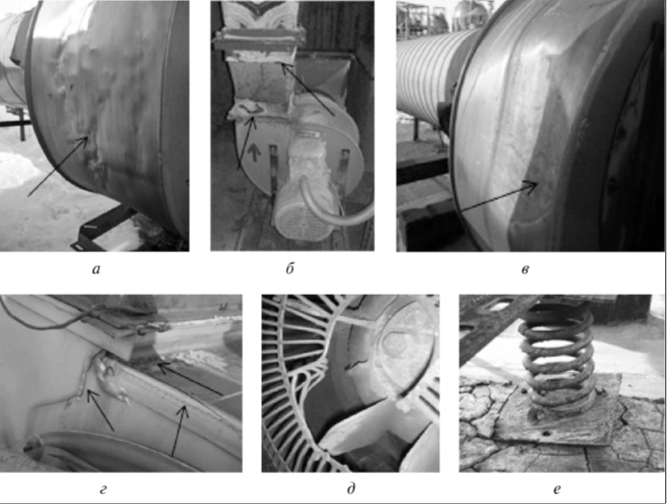
а, в – механические повреждения корпуса; б – следы коррозионного воздействия среды; г – трещины корпуса; д – разрушение лопасти крыльчатки электродвигателя вентилятора; е – отсутствия крепления к фундаменту
Контроль, осуществляемый на базе анализа основных параметров, к которым относятся параметры вибрации, является наиболее информативным. Известно, что при работе любого динамического оборудования возникают колебания, вызванные остаточным дисбалансом, расцентровкой, зазорами и т.п., которые и являются основными источниками диагностической информации, характеризующими его текущее состояние. В настоящее время теория и практика анализа сигналов вибрации достаточно хорошо разработаны, что позволяет получать достоверную информацию практически по любому дефекту, возникшему в процессе эксплуатации.
Основные дефекты, выявляемые с помощью вибродиагностического метода контроля:
- дисбаланс рабочего колеса;
- несоосность вала, повреждения вала;
- трещины в раме или корпусе;
- ослабление затяжки фундаментных болтов;
- разрушение лопаток;
- дефекты подшипников.
Величина вибрации позволяет косвенно судить о работоспособности вентиляционного оборудования.
Для динамического оборудования измеряемая и нормируемая величина – это средняя квадратичная виброскорость в диапазоне частот 10…1000 Гц. Точки измерения вибрации назначаются в местах передачи энергии вибрации от источника на упругое основание или другие части системы (плоскости опорных подшипников и опорные поверхности). Датчики вибрации устанавливаются в трех взаимно перпендикулярных плоскостях относительно оси ротора. Оценка средней квадратичной виброскорости проводится в соответствии с НТД.
При проведении измерений агрегат работает на номинальной нагрузке. При виброобследовании производятся измерения общего уровня средней квадратичной виброскорости в диапазоне частот 10…1000 Гц и спектральный анализ вибрации оборудования.
При исследовании спектра частот вибрации устанавливаются различные дефекты, сопровождающие работу оборудования. Результаты вибрационного контроля определяют дальнейший объем работ обследования.
По результатам вибрационного контроля определяются дефектные детали и в случае необходимости, если требуется принятие мер, проводится осмотр в целях выявления коррозии, локальной деформации, трещин и других дефектов на наружных поверхностях деталей.
При осуществлении периодической вибродиагностики осуществляются обнаружение и идентификация дефектов от момента их зарождения, определяется скорость их развития во времени и на основе анализа полученных данных прогнозируется остаточный ресурс.
Таким образом, основой системы обеспечения надежной работы вентиляционного оборудования, кроме системы технического обслуживания и ремонта оборудования, построенной по системе планово-предупредительных ремонтов, разработанной в 1960–1970 гг., является периодическое диагностирование, позволяющее с учетом различной наработки, неодинаковых коэффициентов нагрузки и, следовательно, различного изнашивания оборудования принять правильное решение либо о необходимости вывода его в ремонт, либо о продлении эксплуатации на определенный период.
Компания «МЕТАМ» неоднократно осуществляла данные виды контроля в составе работ по экспертизе промышленной безопасности динамического оборудования на предприятиях холдинга «СИБУР». В ходе первичного вибрационного обследования оборудования, предшествующего его полной разборке для диагностирования, в 8% случаев была обнаружена повышенная вибрация, превышающая допустимые нормы.
Это позволило выявить при детальном обследовании такие дефекты, как повышенный износ подшипников, изменение геометрии вала (увеличенная кривизна, зазоры), разбалансировка рабочего колеса, и провести своевременный ремонт данного оборудования. Таким образом, сочетание периодического мониторинга и своевременное выполнение графика планово-предупредительных ремонтов позволяют повысить надежность и безопасную работу динамического оборудования.