Автор: М.В. Верюгин (ООО «Сервисная Компания ИНТРА»).
Опубликовано в журнале Химическая техника №6/2018
Обслуживание болтовых соединений с контролируемым моментом затяжки или, как еще принято называть данный сервис, «болтинг», – неотъемлемая составляющая проведения ремонтных работ и планового технического обслуживания для поддержания условий эксплуатации оборудования предприятий нефтедобывающей и нефтеперерабатывающей отрасли, машиностроения, горнодобывающей индустрии, металлургии, химической, энергетической и других отраслей промышленности.
Особое внимание обслуживанию болтовых соединений уделяется в нефтегазовой отрасли, что связано со спецификой переработки и транспортировки легковоспламеняющихся и взрывоопасных сред при высоких давлениях и температурах. Соблюдение требований сборки и технологии затяжки болтовых соединений как основного крепежного элемента технологического оборудования являются важным фактором безаварийной работы и предотвращения утечек взрывоопасных углеводородов. Некачественная сборка, неравномерная и недостаточная затяжка влекут за собой:
- нарушение герметичности;
- разрушение крепежа;
- передавливание прокладки и повреждение уплотнительной поверхности фланца;
- увеличение сроков ремонта и из-за неоптимальной технологии и повторных сборок;
- потери расходных материалов: новых прокладок и крепежа взамен испорченных.
Надежность болтового соединения во многом зависит от качества применяемых материалов, правильности его сборки и подбора прокладочных изделий. При расчете момента затяжки резьбовых соединений используются математические модели и средства программной автоматизации, которые учитывают все факторы воздействия: температуру, давление среды, упругость фланца, коэффициент сжатия прокладки, вибрации, векторы напряжений, возникающие при атмосферных явлениях (ветровые нагрузки, сезонные перепады температуры и др.). На основе данных параметров выбираются требуемые материалы элементов, крепежи, прокладки и рассчитывается усилие, прикладываемое на болты (шпильки) при затяжке фланцевого соединения, которое обеспечивает в рабочих условиях давление на прокладку и герметичность соединения на весь срок эксплуатации технологического оборудования.
Критичным фактором при затяжке резьбового соединения является усилие затяжки соединяемых деталей. Крепеж в резьбовом соединении находится под постоянным механическим напряжением и устойчив к усталости. Если гайка затянута слишком слабо, то в процессе эксплуатации конструкция просто развалится под влиянием вибрации, температурных изменений и других факторов воздействия. Если перетянуть гайку, то шпилька или болт лопнут.
При закручивании крепежа происходит деформация тела. На него воздействует сила упругости, которая стремится восстановить прежние размеры и форму. Сила упругости твердых тел определяется законом Гука, в соответствии с которым напряжение в шпильке прямо пропорционально ее растяжению. При закручивании гайки по резьбе, преодолевая силы трения в резьбе и между упорной поверхностью гайки и фланца, прикладывается усилие к вытяжке шпилек. Под воздействием силы упругости крепежа соединяемые плоскости сжимаются ровно с тем же усилием, с которым он растягивается.
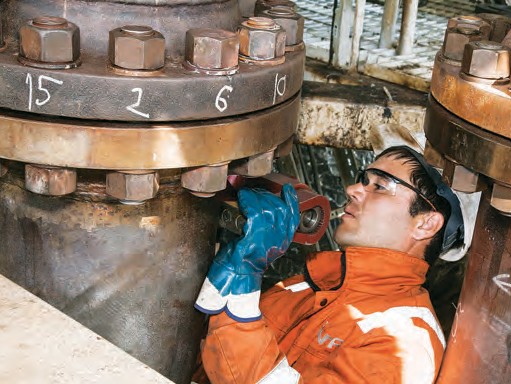
Напряжение и растяжение имеют диапазон упругих деформаций и диапазон пластических деформаций. В диапазоне упругих деформаций действует правило закона Гука: при снятии приложенной нагрузки на данном участке удлинение исчезает, и шпилька принимает свои первоначальные размеры. Когда нагрузка на крепеж превышает допустимую, он перестает вести себя как упругое тело, и наступает область пластической деформации. Деформация при пределе текучести происходит без роста напряжения, а растяжение сохраняется после снятия нагрузки, удлинившийся крепеж уже не вернется в свое начальное положение. По достижении точки предела прочности в материале начинают интенсивно рваться молекулярные связи, дальнейшее приложение нагрузки приводит к ситуации, в которой шпилька начинает разрушаться.
Более того, неравномерная нагрузка на крепеж также может привести к выходу оборудования из строя, так как одни соединения будут недогружены, а другие будут испытывать чрезмерную нагрузку. Прокладка на одной стороне будет раздавлена, а с другой стороны начнется разгерметизация.
Следовательно, надежность болтового соединения зависит от правильности выбора усилия и, соответственно, необходим постоянный контроль крутящего момента на гайке. Существует несколько методов затяжки резьбовых соединений, обеспечивающих требуемые качество и усилие затяжки резьбовых соединений:
- Метод приложения крутящего момента с применением гайковертов, динамометрических ключей мультипликаторов крутящего момента;
- Метод осевой вытяжки – предварительная нагрузка на крепежную сборку накладывается путем растяжки болта вдоль его оси при помощи специального инструмента.
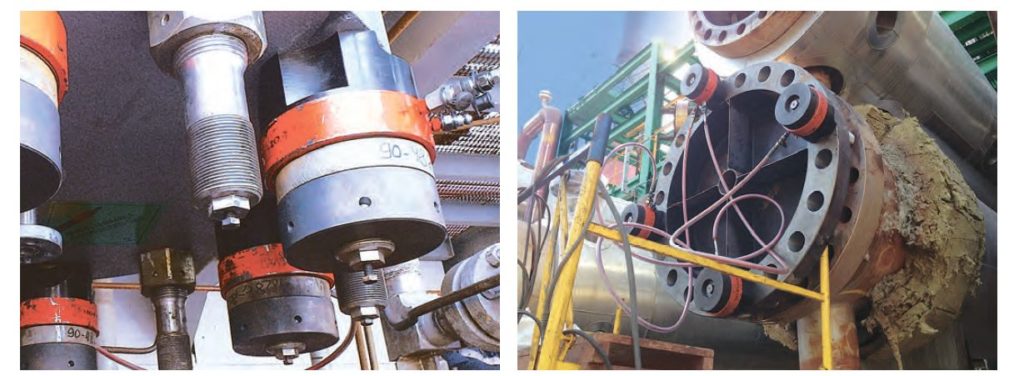
Помимо высокой точности по усилию затяжки, на герметичность сборки соединений влияет также ряд технологических аспектов подбора материала крепежа, его предварительная смазка ингибиторами коррозии, подбор уплотнительных поверхностей фланцев и другие особенности технологии осуществления болтинга. Значительную роль при выполнении болтинга играет квалификация специалистов и опыт работы.
Уже более десяти лет Сервисная компания «ИНТРА» осуществляет слесарно-монтажные работы по обслуживанию болтовых соединений помощью высокотехнологичного профессионального оборудования для затяжки зарекомендовавших себя на рынке производителей Hi-Force, Norbar, Usag, а также проводит супервайзинг сборки/разборки фланцевых соединений.
За десять лет были проведены работы на более чем 1 000 000 болтовых соединениях, при осуществлении следующего комплекса сервисов:
- сборка, разборка, демонтаж шпилек фланцевых соединений технологического оборудования нефтеперерабатывающих предприятий;
- сборка, разборка теплообменного оборудования;
- ремонт бурового и нефтедобывающего оборудования;
- ремонт турбинного оборудования на ГРЭС, АЭС, ГЭС;
- ремонт насосно-компрессорного оборудования на нефтегазовых месторождениях;
- ремонт газокомпрессорных станций; монтаж, демонтаж и обслуживание колонного оборудования химических и нефтехимических предприятий.
Работы выполняются высококвалифицированным персоналом с использованием профессионального гидравлического инструмента, позволяющего обслуживать крепеж с гайками размером от 12 до 165 мм и производить регулируемую затяжку болтовых соединений с точным контролем крутящего момента от 48 до 181 000 Н∙м, при этом погрешность затяжки составляет не более 3%.
Качественно осуществленный комплекс работ по болтингу позволяет достичь увеличения срока службы оборудования, сокращения простоев, уменьшения затрат на техническое обслуживание, при этом гарантируются:
- равномерная затяжка, обеспечение оптимального момента;
- минимизация износа крепежа, сохранение эффективного состояния прокладки;
- оптимизация сроков ремонта благодаря замене ручного труда использованием регулируемых инструментов, сборка происходит с первого раза и минимизируются потери времени при работе с большими диаметрами и фланцами со сложным расположением;
- минимизация рисков возникновения утечек;
- увеличение показателей надежности оборудования;
- безопасность выполнения работ.
195027, Санкт-Петербург, ул. Магнитогорская, 17.
Тел.: (812) 313-5092
Факс: (812) 313-5093
intra@intratool.ru