Автор: А.Н. Монахов (НПП ООО «Корсистем»)
Опубликовано на портале «Химическая техника», октябрь 2019
Высокие экономические потери, вызванные воздействием коррозии на оборудование в нефтеперерабатывающей и нефтехимической промышленности, обусловлены значительными объемами производства и большой металлоемкостью (~32 кг на каждую 1 т перерабатываемой нефти). Наметившаяся в последнее время тенденция к возрастанию объема переработки сернистых и высокосернистых нефтей позволяет поднять вопрос о необходимости применения современных подходов к оценке коррозионного воздействия на металл на основе новых критериев, современных средств контроля и управления коррозионных процессов в реальном времени. Основная часть технологических установок введена в эксплуатацию в 1960-1970 г. и в настоящее время устарела как морально, так и физически [1].
Достаточно отметить, что образующиеся на теплообменном оборудовании отложения толщиной от 0,2 до 1 мм увеличивают расход тепловой энергии на 3–7 %, кроме того, в результате уменьшения полезного сечения труб повышается гидравлическое сопротивление в трубах теплообменника. Считается, что проще предупредить, чем потом устранять последствия. В настоящее время безопасность работы оборудования напрямую зависит от эксплуатационной надежности, эффективности технического обслуживания на основе рационального планирования и повышения производительности и более быстрого реагирования на отклонения от технического регламента. В табл. 1 и рис. 1, 2 представлены статистические данные об авариях на объектах нефтехимических, нефтеперерабатывающих производств и нефтепродуктообеспечения за 2004–2015 гг. [4].
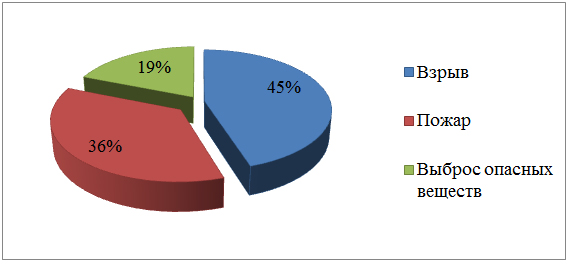
Согласно прогнозам Транснефти, состав нефти может в настоящее время существенно измениться, при этом доля тяжелых и высокосернистых поступающих на НПЗ нефтей возрастет (рис. 3) [6].
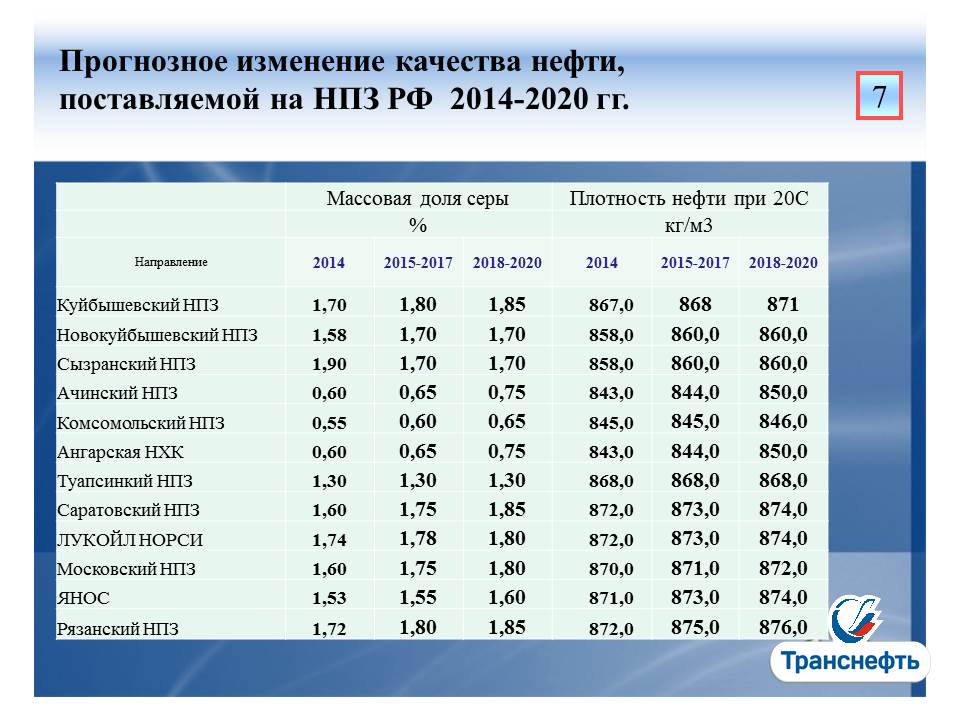
Вышеуказанные обстоятельства усугубляются особенностями эксплуатации установок на каждом предприятии, к которым можно отнести:
- неритмичность загрузки основных мощностей;
- изменение состава перерабатываемой нефти.
- наличие коррозионно-активных отложений на теплообменном оборудовании, приводящие как к коррозионному изнашиванию метала, так и к перерасходу теплоэнергетических ресурсов;
- изношенность оборудования и необходимость в модернизации устаревших производств;
- простои оборудования при проведении ремонтных работ.
Комплексного подхода к моделированию коррозионных процессов при переработке нефти и определения вероятного производственного риска в зависимости от состава рабочей среды, при этом обычно не осуществляется. Решение задач по снижению коррозионного воздействия на оборудование НПЗ невозможно без проведения детального анализа коррозионных источников на технологических установках как при регламентных режимах, так и отличающихся от них. Такие комплексные исследования отсутствуют и являются весьма актуальными для нашей страны в связи с создавшейся в настоящее время ситуацией с переработкой нефти на отечественных НПЗ. Учесть влияние всех параметров, которые играют существенную роль в механизмах коррозионных процессов, чрезвычайно сложно, а чаще всего невозможно при использовании традиционно применяемых средств контроля и анализа. Компания Nalco, применяя систему контроля 3D Trasar на НПЗ в штате Техас в 90-х годах прошлого века, зафиксировала существенные расхождения между полевыми и лабораторными данными, полученными при контроле ионов хлора в автоматическом режиме в шлем-линии атмосферных колонн при первичной переработке нефти и в аналитической лаборатории [2] (рис. 4).
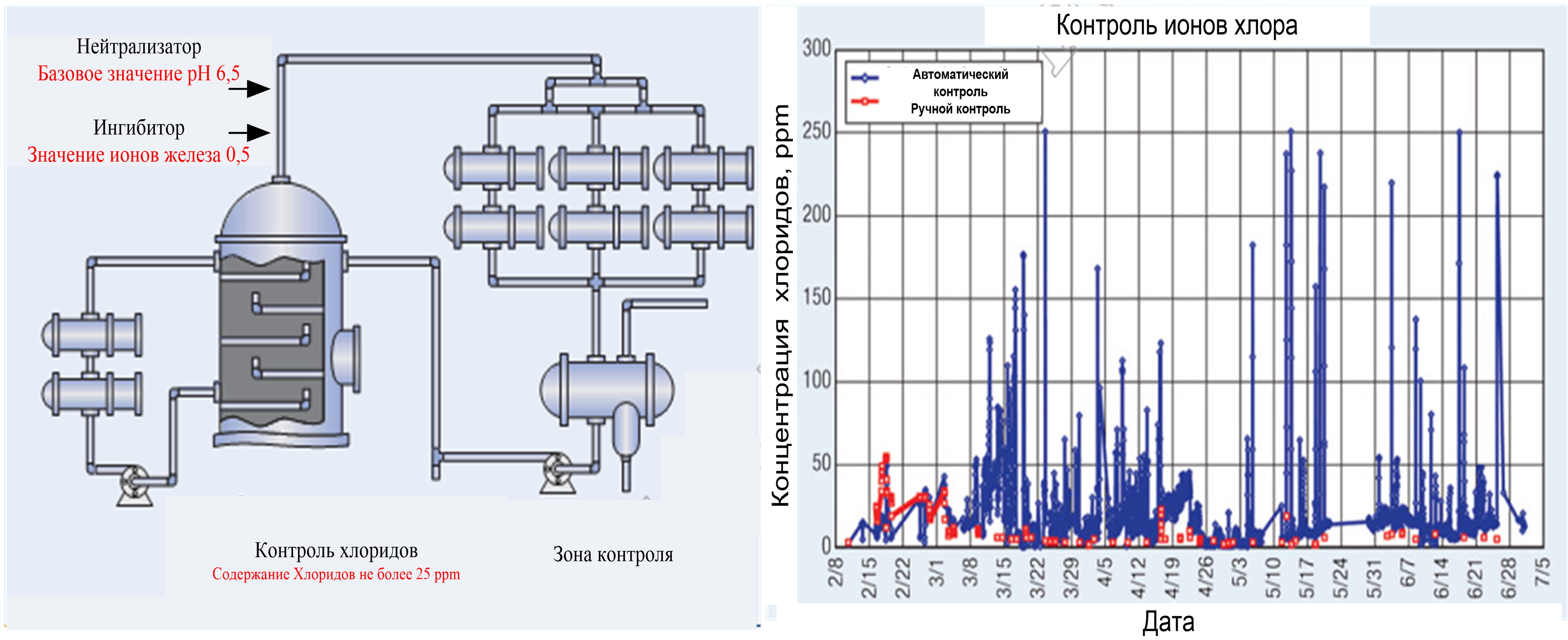
Не менее показателен результат, полученный специалистами ООО «Коррсистем» с применением мультиэлектродных датчиков коррозии по технологии CMAS на АВТ-3 АО «Газпромнефть-НПЗ». На рис 5 представлены тренды, полученные на шлем-линии колонн К-1 и К-2 в мае 2014 г. Как видно, при скорости общей коррозии 0,02…0,03 мм/год в определенные периоды времени скорость питтинговой коррозии превышала общую в десятки раз. Если учесть, что традиционные методы контроля (ER, LPR, гравиметрический) позволяют измерить только общую скорость коррозии, то данные, получаемые датчиками коррозии по технологии CMAS, позволяют совершенно по-новому взглянуть на динамику и вид коррозионных процессов при переработке нефти.
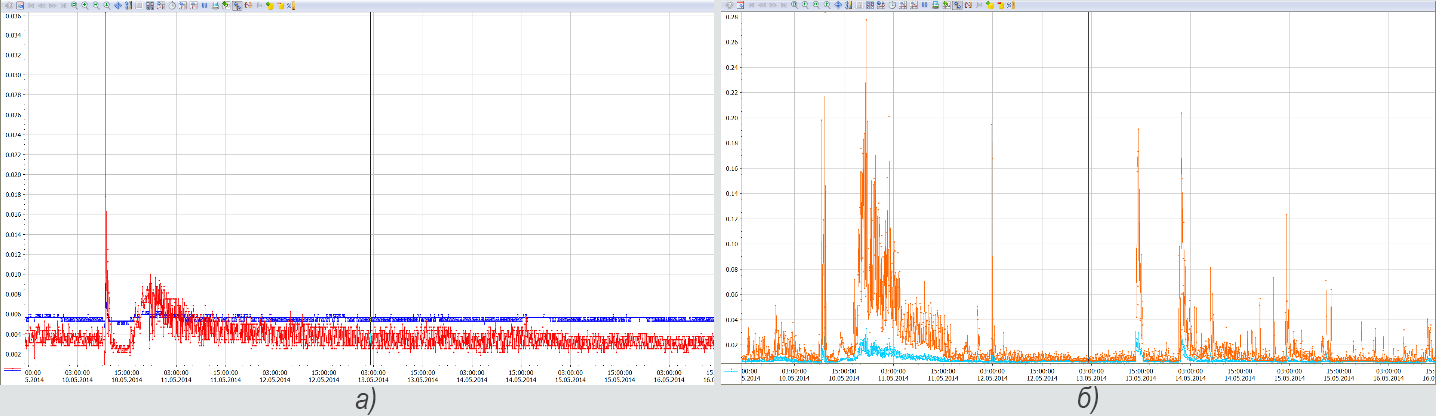
а – колонны К-1 (синий – общая коррозия, красный – питтинговая коррозия); б – колонны К-2 (голубой – общая коррозия, оранжевый – питтинговая коррозия)
Локальная (питтинговая) коррозия, в настоящее время играет существенную роль в отказах оборудования при первичной переработке сернистой нефти[3]. Однако оценка локальной коррозии в условиях эксплуатации установок часто игнорируется, отчасти из-за того, что ни один из широко используемых сегодня методов не может обеспечить реалистичный и эффективный мониторинг коррозии. Объективная, достоверная и своевременная информация о коррозионном износе оборудования жизненно необходима для обеспечения безопасных условий эксплуатации производственных объектов. В настоящее время применяемые технологии контроля коррозии на установках первичной и вторичной переработки нефти на регламентных режимах не позволяют оптимизировать процесс дозирования реагентов в условиях нормирования, ибо коррозионный процессы зависят от концентрации коррозионно- активных элементах в рабочей среде, а не от производительности установок . Необходимо отметить, что при исследовании причин локальных коррозионных поражений оборудования НПЗ традиционно учитывается агрессивность технологических сред в рабочем режиме. В связи с этим особое значение приобретают гибкие технологии ХМЗ и средств контроля в режиме реального времени, особенно в условиях изменения состава рабочих сред и концентрации коррозионно-активных элементов.
Необходимо учитывать, что на управление коррозией оказывают влияние следующие факторы: человеческий, несовершенство нормативной и методической документации, несовершенство технологии контроля и регулирования (рис. 6). При этом особую роль играет человеческий фактор, который может существенно повлиять на формирование управленческих решений. Как видно из рис. 6, правильность управленческих решений зависит от квалификации сотрудников, регламента, качества проектных решений и прочих факторов, которые создаются в основном специалистами при выполнении работ от проектирования до эксплуатации.
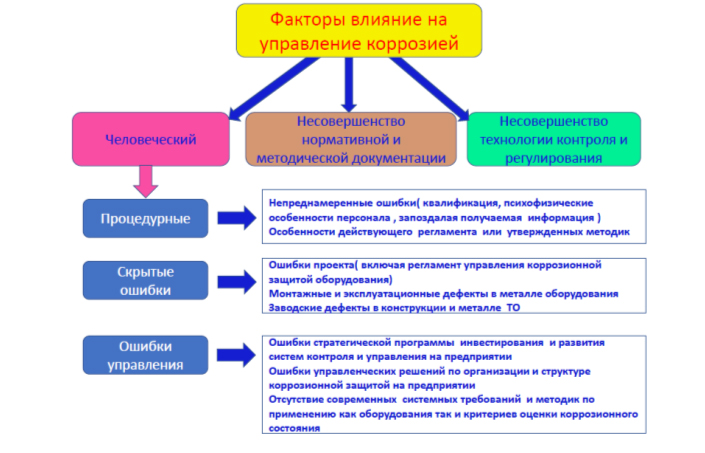
В связи с этим следует рассматривать три направления: оптимизацию антикоррозионных мероприятий, оптимизацию общих затрат и программу по развитию Системы управления коррозии на предприятии:
- оптимизация антикоррозионных мероприятий позволяет оценить правильность управленческих решений и выбора средств контроля при антикоррозионных мероприятиях, а также определить эффективность выбранной стратегии;
- оптимизация общих затрат позволяет оценить и установить критерии решений и алгоритмы функциональности применяемых средств контроля и управления химико-технологической защитой;
- при формировании Программы по развитию Системы управления коррозией следует оценить и определить необходимые и достаточные ресурсы для реализации этапов программы, а также установить их значимость.
Бесспорно, важным моментом при разработке Программы по развитию Системы управления коррозии является определение следующих факторов:
- источников и ресурсов финансирования, необходимых для реализации стратегической программы;
- количественные, качественные и экономические параметры, показатели результативности и эффективности результатов;
- организацию и управление системой.
Программа по развитию Системы управления коррозии должна включать:
- определение необходимых и достаточных ресурсов в организационной и функциональной структуре управления коррозией для реализации выбранной стратегии;
- взаимодействие и сбалансированность модели управления системы, а также делегирование задач, прав и ответственности по формированию анализа и управления коррозией на предприятии;
- определение рисков и погрешностей системы с учетом человеческого фактора;
- бизнес-проект инфраструктуры, рабочих мест, методик и технологий;
- управление организацией ресурсами применяемые при антикоррозионных мероприятиях согласно бизнес-планам, оценивание и формирование информации по мониторингу измерений и анализу полученных результатов и их эффективности. Оптимизация действий, рисков и экономических затрат.
- определение маржинального дохода и прибыли при реализации стратегии программы на основе выбранной ресурсной стратегии и тактики;
- анализ фактических показателей результативности и эффективности для установления факторов (или причин) отклонений для получения информации, используемой в дальнейших решениях;
- оптимизация ресурсной системы для рационального привлечения ресурсов и достижения эффективной деятельности системы.
В связи с ухудшением финансово-экономического положения многие компании начинают панически снижать расходы. Руководство компаний в этом видит один из главных рецептов выживания в период кризиса. В связи с этим в погоне за экономией начали «срезаться» без разбора затраты на поддержание вспомогательных производств, обеспечивающие непрерывную и ритмичную эксплуатацию основных производств. Снижая затраты на НИОКР или химико-технологическую защиту, следует оценить дополнительные коррозионные риски в условиях неритмичности загрузки основных мощностей, изменения состава перерабатываемой нефти и коррозионно-активных отложений на оборудовании, что порой не делается. Необдуманное уменьшение расходов, «затягивание ремней» может привести к негативным стратегическим последствиям и тактическим потерям. При принятии скороспелых решений по уменьшению объема затрат часто также упускаются из виду категории «хороших» или высокопродуктивных расходов, приносящих компании огромный мультипликационный экономический эффект.
Список литературы
- Бурлов В.В. Методы защиты от коррозии установок переработки нефти при эксплуатации в различных режимах. Дис. … д-ра техн. наук. СПб: АООТ «ВНИИНефтехим», 2000.
- Nalco 3D Trasar for crude overhead systems.Automated analyzer. www.ecolab.com.
- Bo Yang. Real Time Localized Corrosion Monitoring in Refinery Cooling Water Systems//Corrosion 98.22-27 March. San Diego, California 1998.
- Производственная надёжность нефтеперерабатывающих заводов и возможности больших данных. 20.07.2017. Рон Бек (RonBeck), директор по маркетингу в энергетической отрасли. AspenTechhttps://avtprom.ru/news/2017/07/20/proizvodstvennaya-nadezh
- Информация об авариях, произошедших на предприятиях, подконтрольных территориальным органам Федеральной службы по экологическому, технологическому, атомному надзору // Ростехнадзор-[Электронный ресурс] http://www.gosnadzor.ru/public/law%20enforcement/
- Качал И.Н. О качестве нефти в системе магистрального транспорта ОАО «АК «Транснефть». 20.06.2014. https://www.transneft.ru/pressroom/docs8/?print=1/
- Баширов М.Г. Система диагностики металлических конструкций. 2014. Филиал ФГБЩУ ВПО УГНТУ. http://900igr.net/prezentacija/meditsina/g-bshirov-iaty-162196/-5.html/