Автор: С.Е. Степанов (АО «Гипрогазцентр»).
Опубликовано в журнале Химическая техника №9/2018
В соответствии с отраслевыми нормативными документами все магистральные газопроводы (МГ) Российской Федерации относятся к промышленным объектам повышенной опасности [1–3] и независимо от режимов работы электроприводных компрессорных станций (КС) с каждым годом федеральными техническими документами ужесточаются требования обеспечения повышенной надежности и безаварийности работы всего оборудования. Это обусловлено не только объективными причинами (устаревшее оборудование, ненадежное электроснабжение КС и т.п.) [4–6], но и наличием неквалифицированного обслуживания и внешними возмущениями различной природы [7–10], несмотря на прогноз коррозионного состояния [11–13] и электроизолирующие покрытия [14, 15].
В этой связи в соответствии с Энергетической стратегией России на период до 2030 года и СТО Газпром 2-3.5-454–2010, разработка универсальных систем мониторинга надежности нефтегазовых объектов, действующих в режиме реального времени и позволяющих осуществлять контроль и управление при различных уровнях и в масштабах систем, является задачей первого приоритета по повышению надежности и безопасности систем энергетики. Кроме того, пункты 4.11.1, 4.11.2 и 4.11.6 правил СТО Газпром 2-3.5-454–2010 регламентируют осуществление контроля работоспособности, надежности и безопасности оборудования КС с помощью технических и программных средств мониторинга и диагностики. Они должны с требуемой достоверностью производить оценку технического состояния оборудования КС и прогнозировать его изменение не менее чем за период до следующего проведения измерений. Установка систем мониторинга и диагностики должна обеспечиваться при новом строительстве и реновации КС, а также в процессе модернизации эксплуатируемых КС. Вводимые в эксплуатацию полнофункциональные системы должны обеспечивать эксплуатацию КС с учетом фактического состояния каждого конкретного объекта диагностируемого оборудования.
Более того, в новой Программе ПАО «Газпром» содержатся основные положения по системам диагностики. В части электроприводных газоперекачивающих агрегатов (ЭГПА) как основных агрегатов КС общим является проведение следующих видов работ:
- полномасштабная комплексная многопараметрическая диагностика и обследование всего электрооборудования ЭГПА, включая вибродиагностику, диагностику методом измерения частичных разрядов (ЧР) в изоляции, термографию с целью определения фактического состояния и оценки остаточного ресурса, а также установление очередности проведения восстановительных работ по КС и отдельным агрегатам;
- адаптация АСУ КС к системам постоянного мониторинга и диагностики элементов ЭГПА, системам постоянного тока и системе электроснабжения КС.
Кроме того, в стандарте ассоциации «Росэкспертиза» сформулированы основные технические требования к комплексным системам мониторинга, предназначенным для оценки технического состояния и прогноза ресурса оборудования опасных производственных объектов в реальном масштабе времени без их остановки, разборки и вывода из эксплуатации.
В настоящее время разработка и внедрение мониторинга и прогнозирования технического состояния в составе АСУ КС реализуется в основном для газотурбинных ГПА. Надежность ЭГПА в целом значительно выше надежности газотурбинных ГПА (средняя наработка на отказ ЭГПА составляет около 4000 ч; газотурбинных ГПА–1300 ч). Однако необходимо учитывать, что вынужденная или аварийная остановка любого агрегата ведет не только к большим затратам на ремонтно-восстановительные работы, но и к снижению (при отсутст-вии необходимых резервов на КС) производительности магистрального газопровода в целом, потерям пускового и топливного газа, электроэнергии, ГСМ и др.
В зависимости от типа ЭГПА имеют наработку 1500… 3000 ч/год и вывести их из работы для плановой диагностики не всегда представляется возможным. Поэтому необходим их оперативный контроль в режиме on-line. Однако все известные системы не рассчитаны на определение технического состояния приводного высоковольтного электродвигателя и иных наиболее ответственных частей оборудования ЭГПА.
Структура ЭГПА как объекта мониторинга
На КС ЕСГ России эксплуатируется сегодня 725 ЭГПА различных типов и мощностей. Однако наиболее распространенной машиной до сих пор является синхронная СТД-12500-2Р [16–18]. Функциональная базовая схема ЭГПА-12,5 показана на рис. 1.
Главными элементами ЭГПА-12,5, как показано на рис. 1, являются: центробежный нагнетатель типа Н-235-21-3 (Н); повышающий редуктор (Р); синхронный электродвигатель типа СТД-12500-2Р (ЭД) с тиристорной щеточной системой возбуждения (ТВУ), щеточно-контактным аппаратом (ЩКА) и подшипниками скольжения (ПСЭД); согласующий трансформатор (СТР); токоограничивающий реактор (РБУ); высоковольтный выключатель (ВВ); системы автоматического управления (САУ), технологических и электрических защит (ТЭЗ); маслосистемы низкого (МСНД) и высокого давления (МСВД).
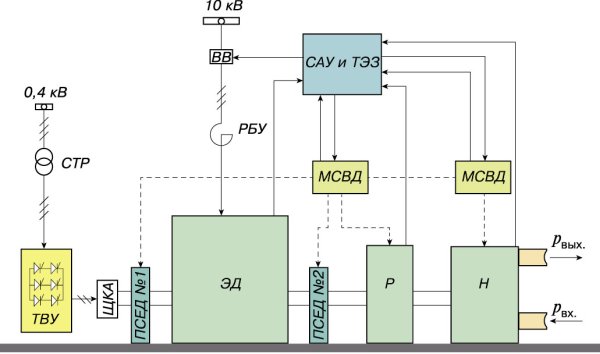
Следовательно, современный ЭГПА как объект диагностирования представляет собой сложную и прост-ранственно-распределенную техническую систему. Она состоит из большого множества различных взаимосвязанных узлов и механизмов (электронных, электротехнических, механических и гидравлических), отличающихся принципами действия, типоразмерами и уровнями надежности. Однако независимо от этого выход из строя любого элемента, как правило, приводит к возникновению аварийной ситуации и выходу из строя ЭГПА в целом.
Основные причины выхода из эксплуатации ЭГПА [19–22]:
Электрооборудование (40%):
- внешнее электроснабжение 220кВ 20%
- система возбуждения 35%
- вспомогательное электрооборудование 0,4 кВ 25%
- высоковольтные узлы 15%
- статор приводного СД 5%
- САУ и КИП (элементная база САУ;
- программное обеспечение; датчики) 30%
- Механические узлы (подшипники; ротор СД; сис-тема уплотнения 25%
- Действия персонала (оперативного, ремонтного) 5%
Наиболее тяжелым отказом ЭГПА является выход из строя статора приводного синхронного электродвигателя (СД), аварии которого в большинстве случаев возникают вследствие пробоя корпусной или пазовой изоляции. В связи с этим разработка новых методов неразрушающего контроля, диагностики и прогнозирования эксплуатационной надежности высоковольтных СД с учетом электрических и механических свойств изоляции и изменения их под воздействием различных факторов представляет наибольший практический интерес.
Работа всех элементов ЭГПА, отличающихся значительной установленной мощностью, стоимостью и массогабаритными показателями, должна контролироваться встроенной системой мониторинга и прогнозирования (ВСМП) технического состояния (ТС) в режиме on-line. При этом проектирование ее должно производиться параллельно с проектированием всех остальных систем диагностики КС. Ведущиеся в настоящее время разработки в области технической диагностики ЭГПА не отвечают пока требованиям оперативности обнаружения и принятия решений и не предполагают единого теоретически обоснованного подхода ко всем элементам электрооборудования, и поэтому не адекватны на практике. Это, как правило, переносные или автономные однопараметрические системы, фиксирующие наличие уже самого факта неисправностей или отказов. Данные локальные средства контроля и диагностики решают только частные задачи, не обеспечивая функций достоверного предупреждения наступления аварий, автоматического выявления их причин и быстрого восстановления штатных режимов, а также комплекса проблем автоматизации современного дорогостоящего оборудования КС. Анализ крупнейших аварий и нештатных ситуаций электроэнергетического оборудования в последнее время и принятые нормативные акты РФ дополнительно стимулируют поиск инновационных технологий мониторинга и достоверности прогноза технического состояния приводов нагнетателей для повышения надежности и удобства обслуживания ЭГПА и в целом КС и линейных участков МГ.
Для выявления наиболее существенных эксплуатационных факторов, влияющих на надежность СД, необходимо предварительно выполнить комплексный анализ условий эксплуатации ЭГПА на характерных и типичных КС, включающий систематический сбор и обработку достоверной информации о повреждаемости основных узлов СД; анализ режимов его работы в номинальных режимах работы и при режимных возмущениях питающей сети на КС МГ России.
Общий анализ эксплуатационной надежности ЭГПА
В настоящее время на компрессорных станциях МГ ОАО «Газпром» используется периодическое диагностирование выведенных в ремонт ЭГПА. По программе диагностирования производятся следующие испытания:
- визуальный осмотр состояния статора и ротора СД;
- оценка состояния изоляции листов активной стали и выявление местных коротких замыканий в сердечнике статора электромагнитным методом;
- оценка вибрационного состояния электродвигателя путем измерения размаха колебаний, среднеквадратического состояния виброскорости и виброускорения на подшипниках, фундаментной плите и середине статора;
- оценка состояния изоляции обмотки статора на основе визуального и инструментального обследования, а также измерения уровня частичных разрядов в изоляции при подаче переменного напряжения от постороннего источника (0,7…1,0 Uф);
- тепловизионный контроль состояния паек стержней обмотки в лобовых частях при подаче тока от постороннего источника.
Известно, что численное определение критических параметров и постоянный контроль над ними позволяют повысить эффективность диагностирования и прогнозировать изменение технического состояния СД. Однако в условиях реальной эксплуатации не всегда удается выполнить весь комплекс испытаний и измерений, кроме того, периодичность выполнения диагностики на одном ЭГПА составляет 3–4 года. В связи с этим необходим анализ эксплуатационной надежности, результат которого может установить наиболее уязвимые элементы СД.
Для выявления наиболее существенных эксплуатационных факторов, влияющих на надежность электродвигателей, выполнен комплексный анализ условий эксплуатации ЭГПА, включающий сбор и обработку информации о повреждаемости двигателей; анализ режимов работы электродвигателей в номинальных режимах работы; анализ режимов работы электродвигателей при режимных возмущениях питающей сети.
Характерные примеры повреждений статоров электродвигателей СТД-12500-2 ЭГПА-12,5 в ООО «Газпром трансгаз Нижний Новгород» приведены на рис. 2.
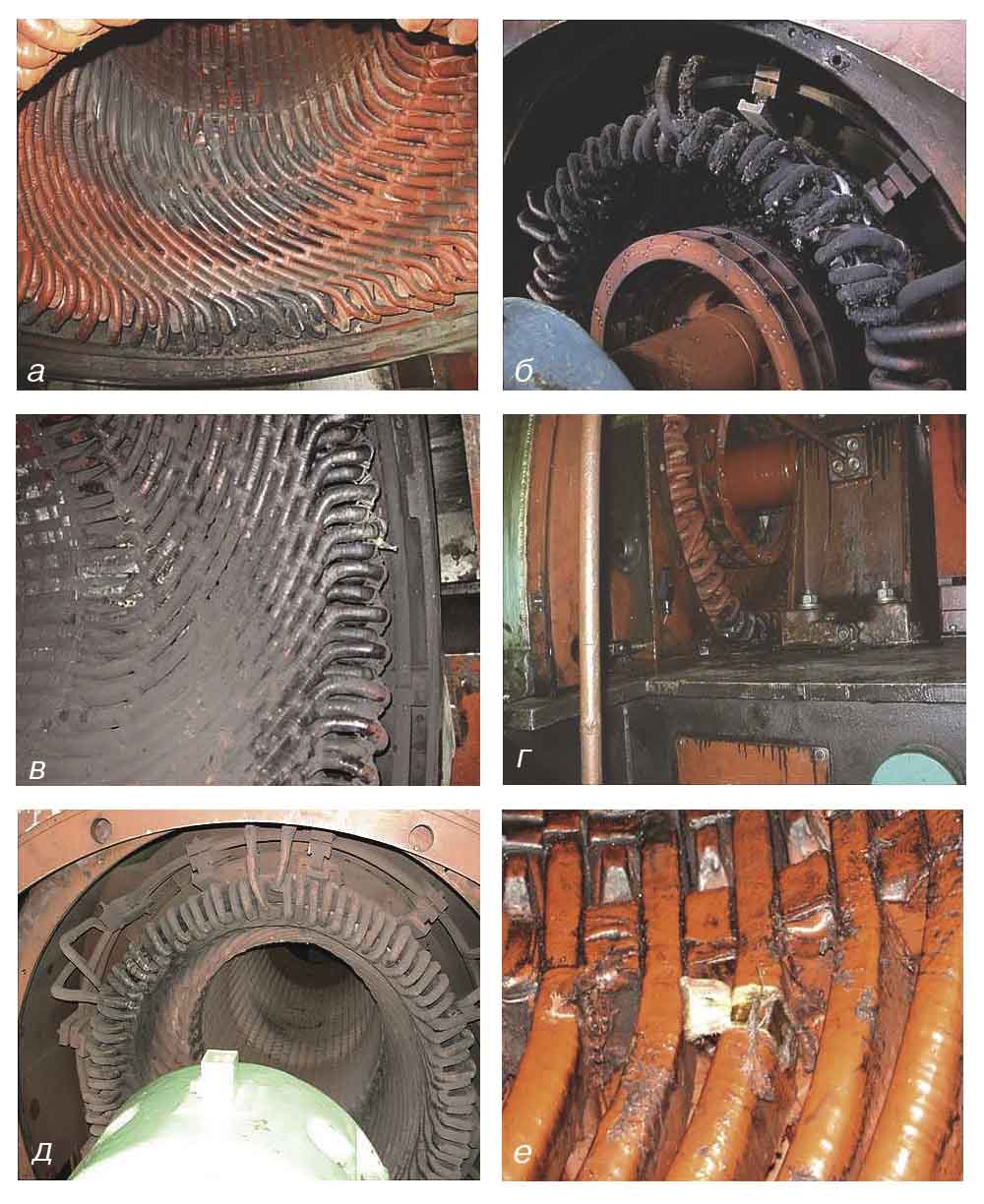
а – ЭГПА5 Ямбург–ЗГ КС«Сеченовская»; б – ЭГПА2 Ямбург-Елец-2 КС«Сеченовская»; в – ЭГПА4 Ямбург-Елец-2 КС«Помары»; г – ЭГПА7 Уренгой-Центр-2 КС «Починки»; д – ЭГПА4 Ямбург-Елец-2 КС«Помары»; е – ЭГПА7 Уренгой-Центр-2 КС «Починки»
Наработку на отказ статоров электродвигателей ЭГПА можно определить исходя из их повреждаемости в процессе эксплуатации (рис. 3).
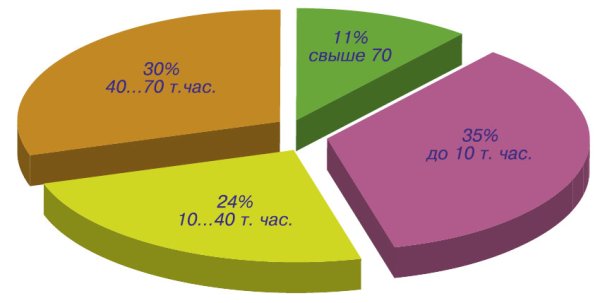
Как показали результаты анализа данных рис. 3, повреждаемость приводных СТД не зависит от их наработки в процессе эксплуатации, а определяется в основном условиями их эксплуатации. Общие статистические данные по выходу из строя приводных высоковольтных электродвигателей типа СТД-12500-2 и СДГ-12500-2 с 1985 по 2010 г. на КС ООО «Газпром трансгаз Нижний Новгород» представлены на рис. 4 [5, 13–16]. Всего же с момента ввода в эксплуатацию зафиксировано 62 случая выхода из строя электродвигателей типа СТД-12500-2 и СДГ-12500-2 при средней аварийности СД из-за повреждений обмоток статора составляет 2,7 в год.
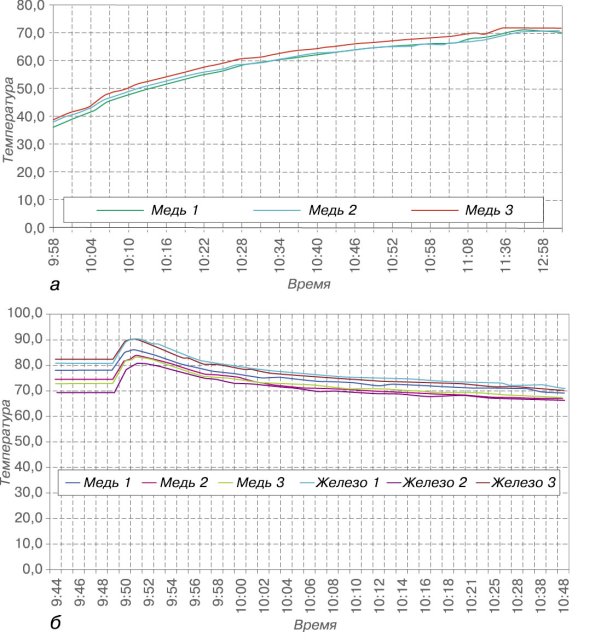
Для определения максимальных отклонений в температуре статора при изменении режимов работы ЭГПА выполнены измерения температуры при пуске и останове, а также изменении потребляемой мощности при перестроении режима работы газопровода. Измерения выполнены с интервалом 2 ч в течение 6 суток на КС «Починковская» и КС «Сеченовская» (рис. 4).
Анализ результатов измерений показал, что колебания температуры статора в летнее время связано с суточными изменениями температуры охлаждающего воздуха. Зимой же перепады температуры наружного воздуха не оказывают влияния на изменение температуры СД, и его температура в основном зависит от числа ЭГПА, одновременно работающих в КС. При останове ЭГПА за короткий промежуток времени происходит рост температуры обмоток на 10…15 С° выше температуры, предшествующей отключению СД, и может превышать максимально допустимые значения для изоляции данного класса.
Типовая схема электроснабжения электроприводного компрессорного цеха (КЦ) приведена на рис. 5.
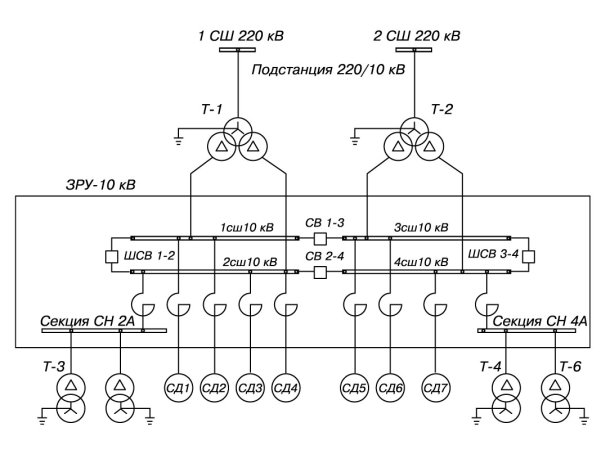
Т-1, Т-2 – трансформаторы типа ТРДЦН-63000/220; СД1–СД7 – электродвигатели ЭГПА типа СТД 12500-2; ШСВ1-4 – шиносоединительные выключатели; СВ1-4 – секционные выключатели; Т3-Т6 – трансформаторы 10/0,4 кВ питания КС
Из рис. 5 видно, что СЭС КЦ осуществляется от двух трансформаторов 220/10 кВ с расщепленными обмотками. Электрооборудование 10 кВ размещено в ЗРУ-10 кВ. В связи с невозможностью по технологическим причинам осуществлять самозапуск ЭГПА-12,5 АВР выведен из работы. Схема отличается от стандартных ЗРУ наличием ШСВ для быстрого запуска ЭГПА и снижения просадки напряжения на секциях шин 10кВ.
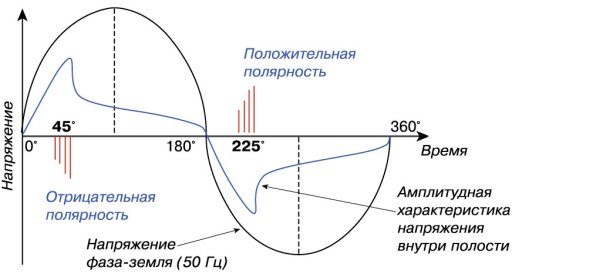
Основными параметрами импульсов ЧР являются:
- время нарастания импульса порядка 1…5 нс, соответствующее частоте в диапазоне 50…250 МГц;
- амплитуда импульсов прямо пропорциональна размерам полости, а число ЧР соответствует количеству пустот и полостей, т.е. степени разрушения высоковольтной изоляции;
- полярность и фаза импульсов ЧР по отношению к первой гармонике питающего напряжения позволяет определить место их возникновения в расточке статора и, соответственно, доминирующий разрушающий механизм (рис. 6);
- ЧР начинают проявляться при напряжениях более 3 кВ/мм, и наиболее опасна для пробоя динамика увеличения амплитуды и частоты ЧР.
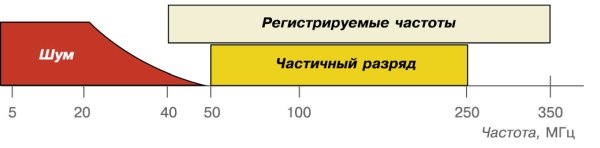
Для выделения истинного значения импульсов ЧР и отделения их от шумов по частоте производятся (рис. 7):
- выделение полосы спектра, содержащей импульсы ЧР с помощью емкостных датчиков;
- разделение импульсов ЧР и шума, используя метод установки и калибровки датчиков на основе анализа параметров импульса;
- цифровой метод обработки информации, используя приборы-анализаторы и специализированное ПО.
Эффективность оценки технического состояния изоляции СД методом анализа ЧР доказывает сопоставление результатов замеров параметров ЧР до (рис. 8, а) и после (рис. 8, б) перемотки статорной обмотки одного из двигателей СТД-12500. Измерения выполнены с помощью аппаратуры фирмы IRIS POWER (Канада) с эпоксидно-слюдяными датчиками 80 пФ на напряжение 16 кВ.

Таким образом, использование системы мониторинга ЧР высоковольтной изоляции СД ЭГПА в режиме on-line может позволить:
- адекватно оценить техническое состояние машины;
- автоматизировать процесс регистрации и локализации повреждений,
- интегрировать результаты мониторинга ЧР в АСУ КС,
- организовать удаленное управление сбором данных о состоянии СД.
Следовательно, для реализации эффективных и адекватных систем оперативной диагностики и прогнозирования технического состояния приводных двигателей ЭГПА необходимо разработать структуру и алгоритмы обработки информации о параметрах рассмотренных эксплуатационных факторов в реальном времени.
Список литературы
- Милов В.Р., Суслов Б.А., Крюков О.В. Интеллектуализация поддержки управленческих решений в газовой отрасли//Автоматизация в промышленности. 2009. №12. С. 16–20.
- Бабичев С.А., Захаров П.А., Крюков О.В. Мониторинг технического состояния приводных электродвигателей газоперекач. агрегатов//Контроль. Диагностика. 2009. №7. С. 33–39.
- Милов В.Р., Шалашов И.В., Крюков О.В. Процедуры прогнозирования и принятия решений системе технического обслуживания и ремонта//Автоматизация в промышленностити. 2010. №8. С. 47–49.
- Kryukov O.V. Intelligent electric drives with IT algorithms//Automation and Remote Control. 2013. Т. 74. №6. С. 1043–1048.
- Петров Н.Г., Долганов М.Л., Запевалов Д.Н. Развитие отраслевого комплекса нормативных документов «Защита от коррозии»//Территория Нефтегаз. 2009. №12. С. 38–39.
- Запевалов Д.Н., Маянц Ю.А., Елфимов А.В. Актуальные вопросы совершенствования нормативной документации для объектов нефтегазового комплекса//Научно-технический вестник ОАО «НК «Роснефть»». 2016. №2. С. 90–93.
- Запевалов Д.Н., Копьев И.Ю. Оценка внешних коррозионных воздействий при прогнозе технического состояния магистральных газопроводов//Наука и техника в газовой промышленности. 2012. №4 (52). С. 91–99.
- Ашарин С.Н., Сирота Д.С., Запевалов Д.Н. Оценка степени влияния свойств электролита и механического состояния СТ.3 на ее коррозионное поведение в диапазоне концентраций NaCl от 0,3 до 3%//Трубопроводный транспорт: теория и практика. 2016. №3 (55). С. 21–24.
- Запевалов Д.Н. Повышение эффективности систем защиты от коррозии подземных магистральных газопроводов//Газовая промышленность. 2015. №6 (724). С. 67–70.
- Захаров П.А., Крюков О.В. Принципы инвариантного управления электроприводами газотранспортных систем при случайных возмущениях//Вестник Ивановского государственного энергетического университета, 2008. №2. С. 98–103.
- Нефедов С.В., Запевалов Д.Н. Система оценки и прогноза коррозионного состояния магистральных газопроводов//Газовая промышленность. 2008. №7. С. 69–73.
- Петров Н.Г., Долганов М.Л., Запевалов Д.Н. О методах оценки реальной защищенности магистральных трубопроводов в экстремальных условиях//Коррозия: материалы, защита. 2008. №3. С. 42–47.
- Кривдин А.Ю., Лисин В.Н., Запевалов Д.Н. Алгоритм оценки коррозионного состояния МГ и оптимизации работы средств ЭХЗ//Газовая промышленность. 2003. №11. С. 94–96.
- Алимов С.В., Петров Н.Г., Запевалов Д.Н. Электроизолирующее соединение для защиты трубопроводов от коррозии с учетом новых требований ОАО «Газпром»//Газовая промышленность. 2010. №11. С. 72–76.
- Ашарин С.Н., Сирота Д.С., Запевалов Д.Н. Контроль коррозионного состояния и состояния защитных покрытий трубопроводов с многослойными и утяжеленными покрытиями//Трубопроводный транспорт: теория и практика. 2016. №2 (54). С. 5–9.
- Крюков О.В., Титов В.В. Разработка АСУ автономными энергетическими установками//Автоматизация в промышленности. 2009. №4. С. 35–37.
- Серебряков А.В., Крюков О.В. Оптимизация управления автономными энергетическими установками в условиях стохастических возмущений//Промышленная энергетика. 2013. №5. С. 45–49.
- Крюков О.В., Серебряков А.В., Васенин А.Б. Диагностика электромеханической части энергетических установок//Електромеханiчнi I енергозберiгаючi системи. 2012. №3 (19). С. 549–552.
- Серебряков А.В., Крюков О.В., Васенин А.Б. Нечеткие модели и алгоритмы управления энергетическими установками//Материалы конференции «Управление в технических, эргодических, орг. и сетевых системах». 2012. С. 467–469.
- Крюков О.В., Серебряков А.В. Метод и система принятия решений по прогнозированию технического состояния ЭГПА//Электротехнические системы и комплексы. 2015. №4 (29). С. 35–38.
- Крюков О.В. Интеллектуальные электроприводы с IT-алгоритмами//Автоматизация в промышленности. 2008. №6. С. 36–39.
- Серебряков А.В., Крюков О.В. О новых возможностях технологий Smart Grid//Электрооборудование: эксплуатация и ремонт. 2013. №2. С. 47–48.