Авторы: В.И. Бурлаков, А.М. Кузнецов, К.А. Кузнецов, М.А. Васильев, А.И. Бондаренко (АО «ИркутскНИИхиммаш»)
Опубликовано на портале «Химическая техника», август 2019
В статье приведен пример реализованной возможности продления безопасной эксплуатации подогревателя питательной воды после выявленных в нем в процессе эксплуатации недопустимых повреждений в виде трещин, и их устранения посредством разработанных инженерных решений, направленных на обеспечение работоспособного состояния указанного аппарата. Описывается общий порядок и содержание выполненного ремонта, согласно разработанным технологическим решениям и действующим нормативным документам, качество реализации которого подтверждены проведенными комплексным контролем и испытаниями.
При эксплуатации подогревателя агрегата синтеза аммиака в сварных соединениях кольцевого шва приварки обечайки к трубной решётке, швов вварки штуцеров А1 и В1, а также швов приварки перегородки к обечайке и трубной решётке распределительной камеры высокого давления обнаружены недопустимые повреждения в виде трещин.
Подогреватель питательной воды (далее по тексту – подогреватель) изготовлен в сентябре 2014 г. в одной из зарубежных фирм и поставлен на нефтеперерабатывающее предприятие нашей страны.
Корпус распределительной камеры высокого давления трубного пространства (Dвн = 1290 мм, толщина стенки 135 мм), трубная доска (Dнар = 1560 мм, толщина 446 мм), фланец и крышка выполнены из стали ASME SA-336 Gr.F22.Cl.3 (C = 0,09 %, Si = 0,18 %, Mn = 0,33 %, Cr = 2,07 %, Mo = 0,96 %, Ni = 0,31 %, Cu = 0,12 %, Al = 0,029 %, V = 0,012 %, P = 0,007 %, S = 0,004 %, твердость НВ 205).
В корпус распределительной камеры вварены два штуцера А1 и В1, изготовленные из стали ASME SA-336 Gr.F22.Cl.3.
Для корпуса межтрубного пространства (Dвн = 1260 мм, толщина стенки 70 мм) c полусферическим днищем (Dвн = 1260 мм, толщина стенки 34 мм) применена сталь ASME SA516/70. В корпус межтрубного пространства вварены два штуцера А2 и В2 из стали ASME SA-105. Вид и конструкция аппарата представлены на рис. 1.
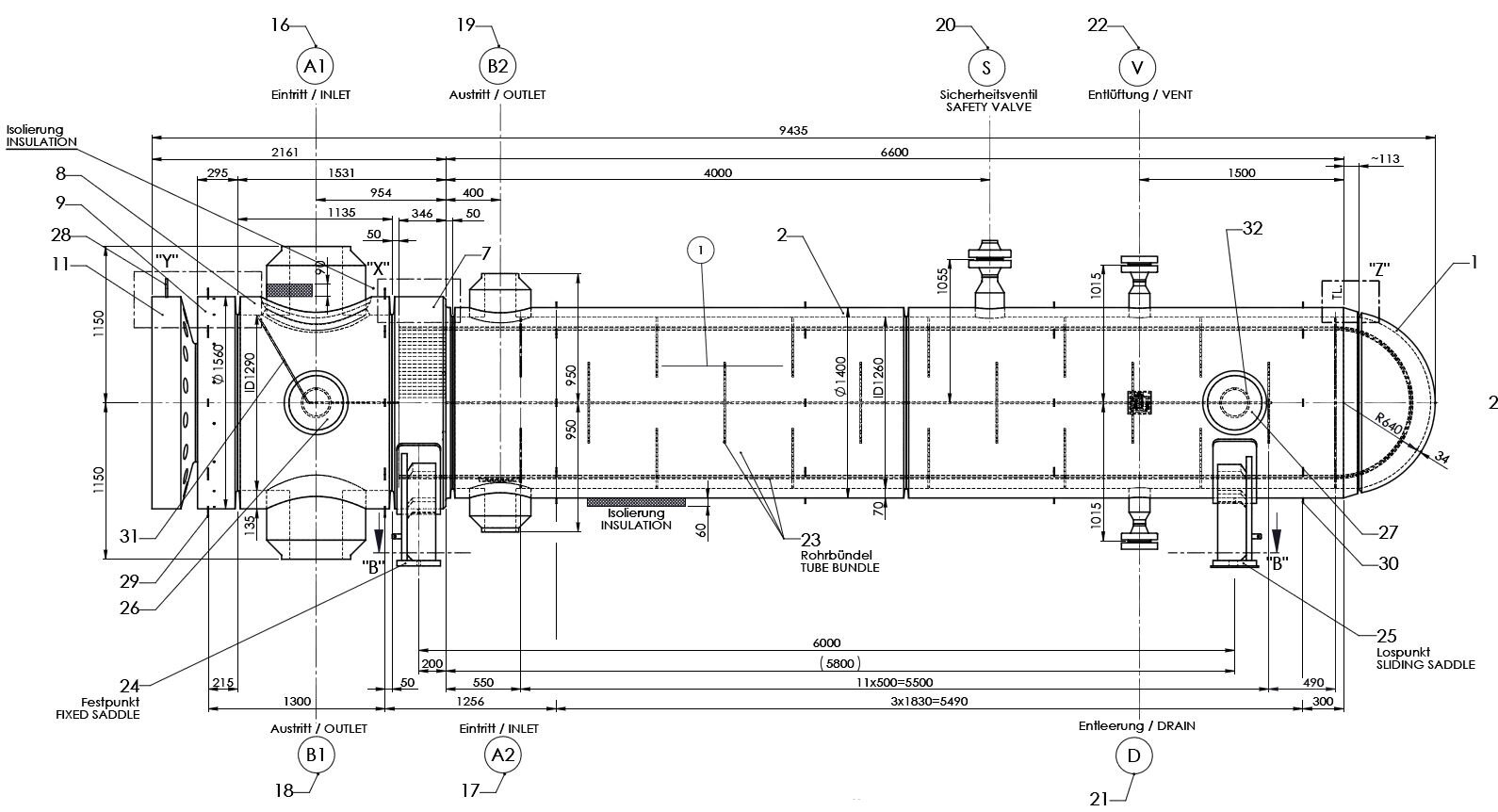
Подогреватель эксплуатируется при следующих рабочих параметрах:
- в распределительной камере высокого давления: р = 20,68 МПа, Т = 275/183 °С, среда – синтез газ, класс опасности 4, взрывоопасная, пожароопасная;
- в межтрубном пространстве корпуса: р = 11,0 МПа, Т = 132/243 0С, среда – питательная котловая вода.
В соответствии с ПБ 03-584-03 [1] подогреватель относится к первой группе.
После двух лет эксплуатации подогревателя в кольцевом шве, соединяющем трубную решётку с обечайкой распределительной камеры трубного пространства, выявлена сквозная трещина длиной ~50 мм по наружной поверхности, ориентированная поперек шва.
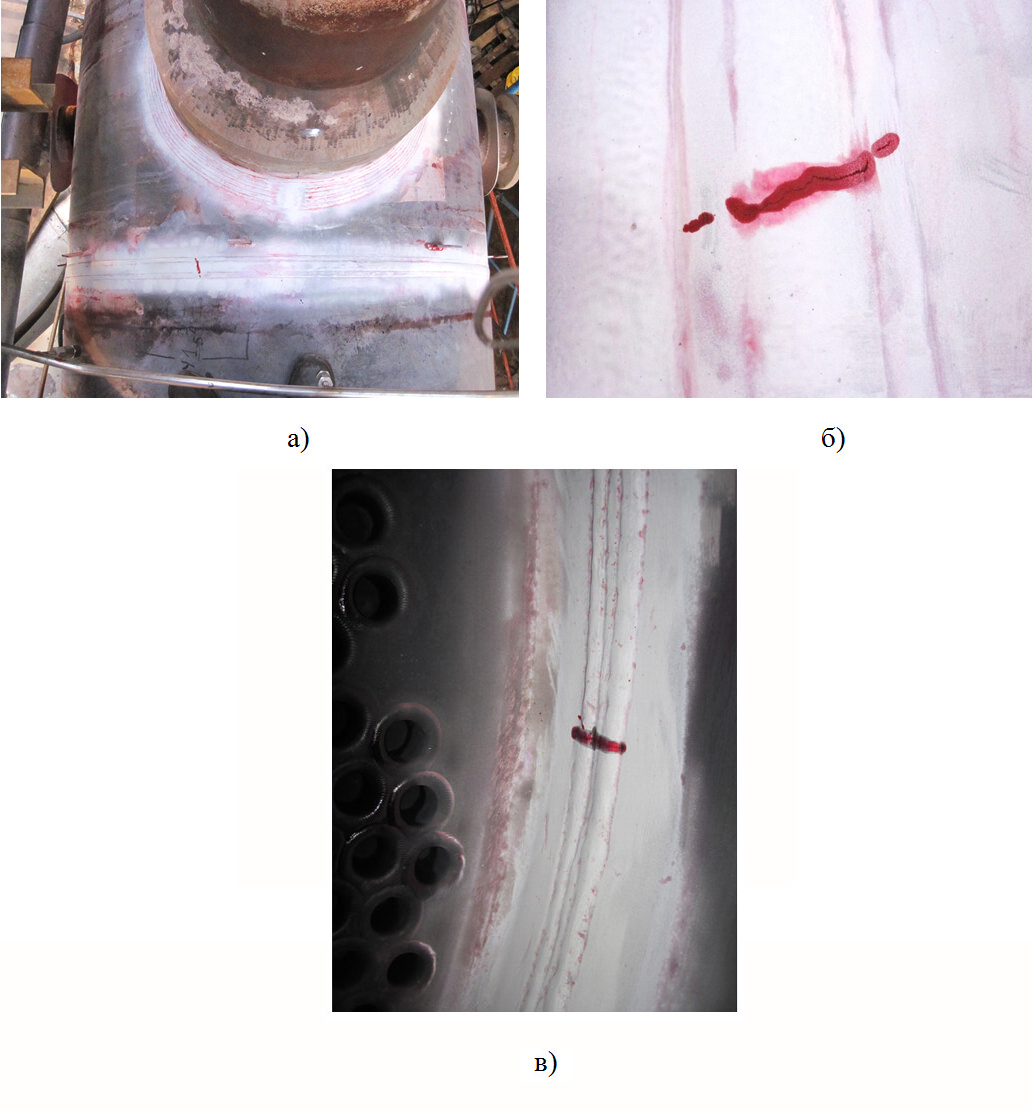
а, б – вид трещины по наружной поверхности; в – вид трещины с внутренней поверхности
При вскрытии крышки корпуса распределительной камеры на внутренней её поверхности при ВИК к ПВК и УК в кольцевом шве дополнительно выявлено четыре поперечные трещины на участке шва длиной около 250 мм и две трещины в верхней части шва (рис. 3), а в шве вварки верхнего штуцера А1 на впуске – 10 поперечных трещин, протяженных по толщине стенки и на различном удалении друг от друга (рис. 5). В сварном соединении вварки нижнего штуцера В1 на выходе обнаружено четыре участка шва с поперечными трещинами (рис. 6). Кроме того, в швах приварки перегородки (см. рис. 1, поз. 31) распределительной камеры к обечайке и трубной доски также выявлено 32 участка шва с поперечными трещинами (см. рис. 4, 6). Все трещины ориентированы поперёк шва.
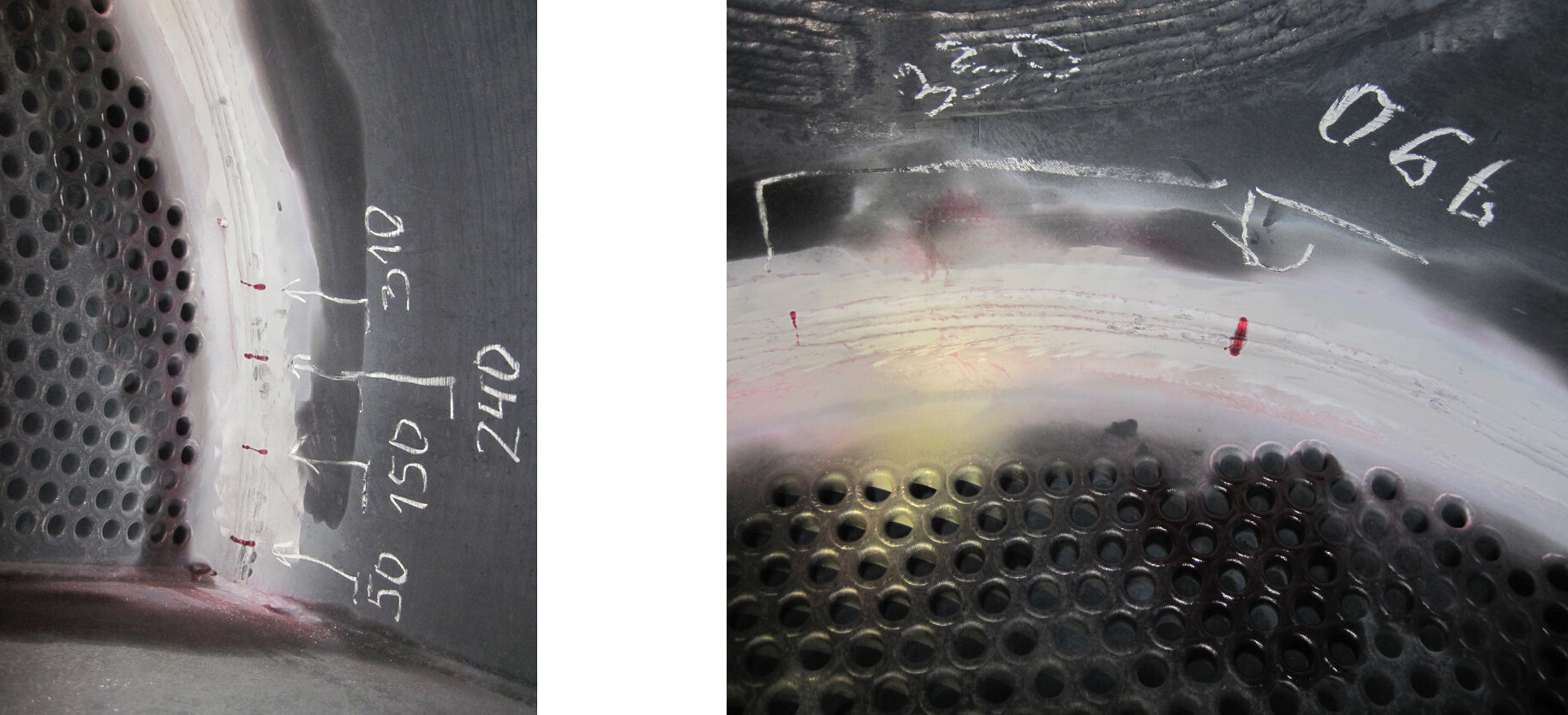
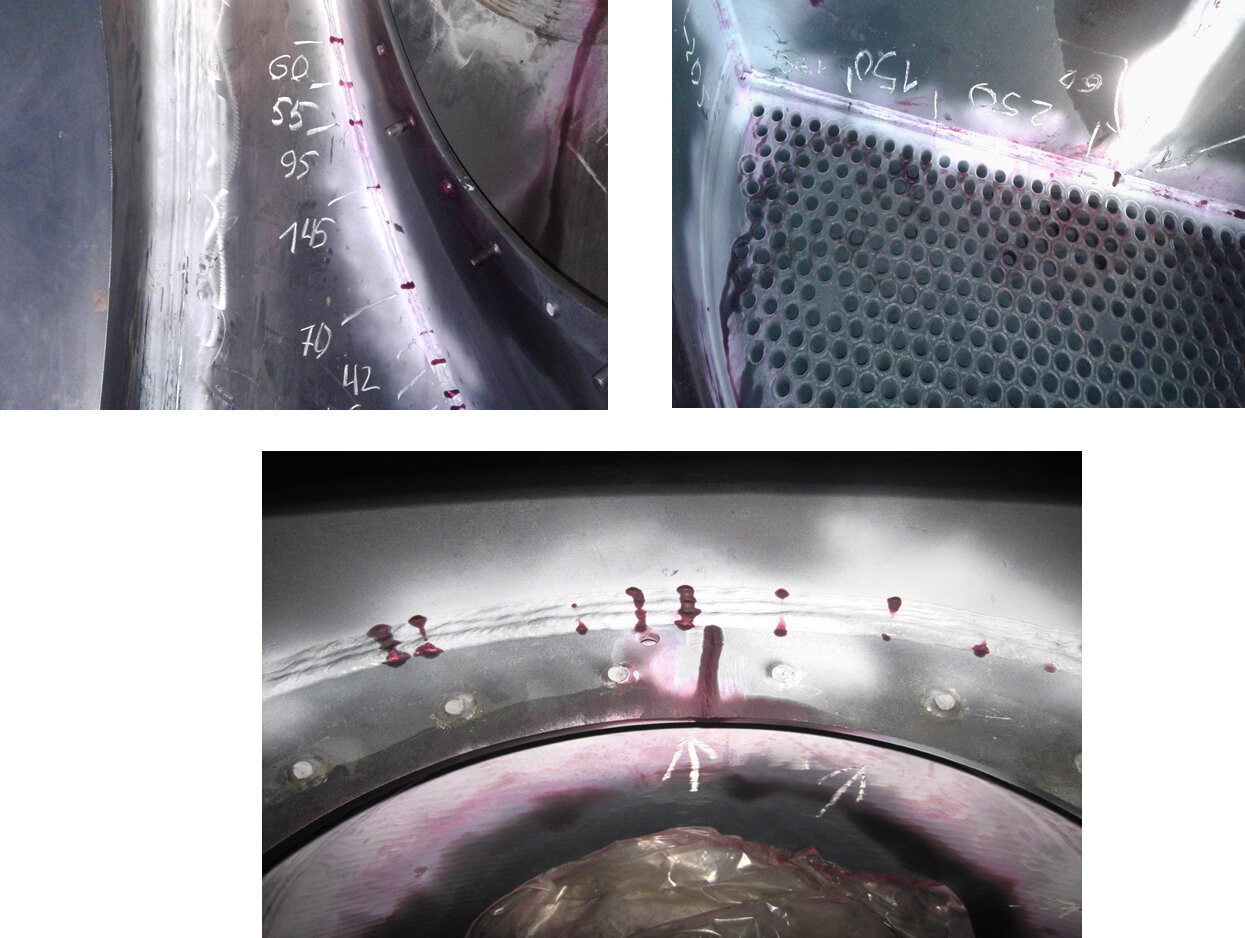
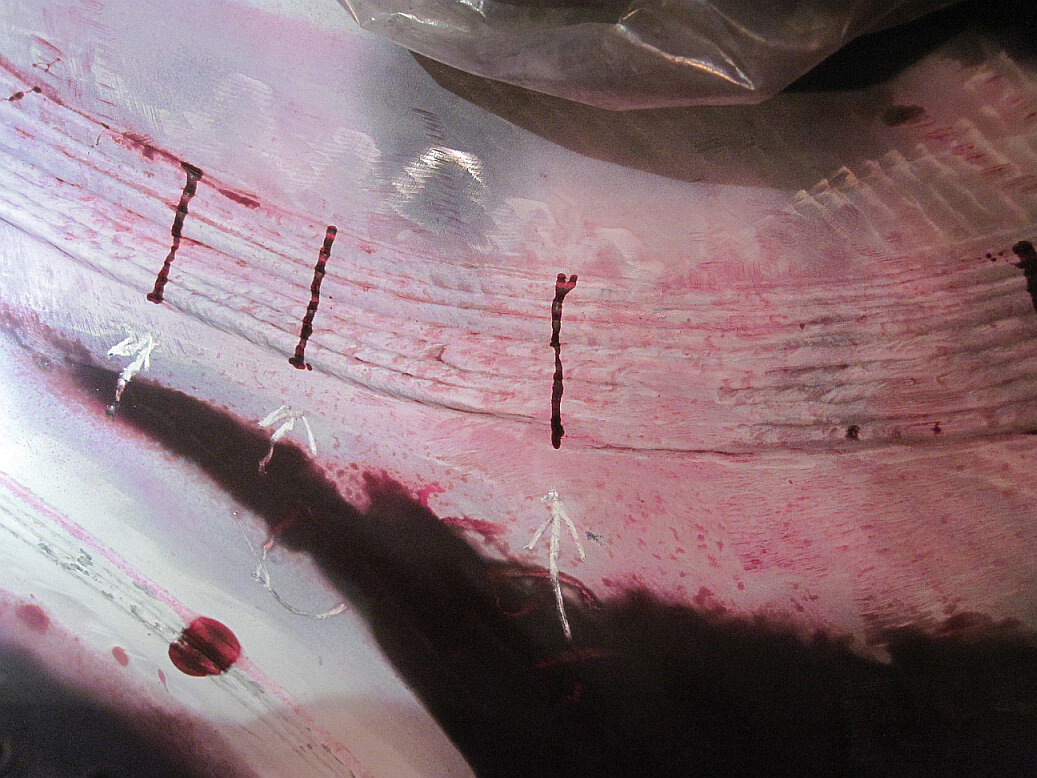
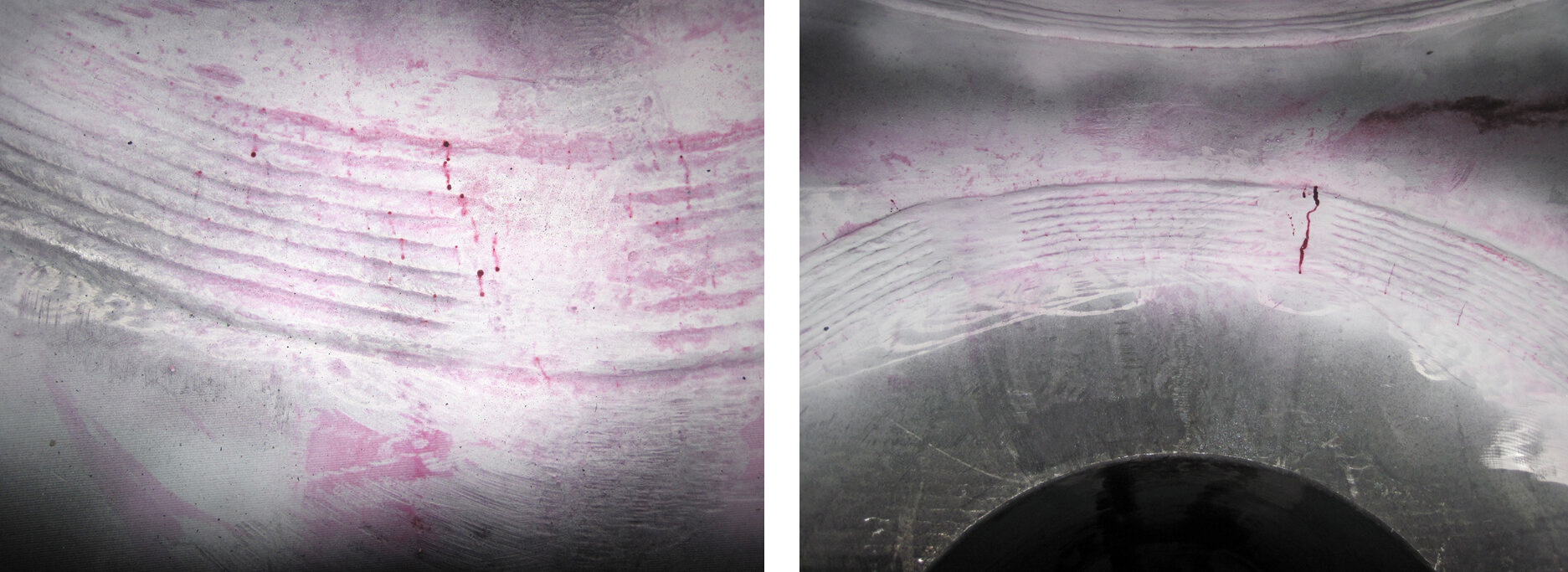
На основании анализа результатов контроля и выявленных дефектов в сварных соединениях совместно с техническими специалистами службы главного механика и службы ремонта нефтехимического предприятия было принято решение о необходимости ремонта корпуса распределительной камеры высокого давления подогревателя в следующем порядке:
- в кольцевом сварном соединении приварки обечайки к трубной решётке распределительной камеры, в шве вварки нижнего штуцера В1 участки металла шва с трещинами и в швах приварки перегородки распределительной камеры к обечайке и трубной решётке вышлифовать механическим способом или высверлить и/или выфрезеровать до полного их исчезновения с формированием разделки кромок в выборке. Выборки заварить ручным электродуговым способом с применением аустенитных электродов с высоким содержанием никеля (ОЗЛ-25Б по ТУ 1273-101-36534674-98 или ОК-92.45 по классификации ENiCrMo-3/AWS A5.11), без проведения послесварочной термообработки. Сквозную трещину в кольцевом шве высверлить, а в полученное отверстие (диаметром 53 мм – ширина металла шва, пораженного трещиной) вварить глухой стакан, изготовленный из поковки сталь 22Х3М;
- в верхнем шве вварки штуцера А1, имеющем десять глубоких трещин, вышлифовку дефекта осуществлять с внутренней и наружной поверхностей корпуса камеры, а выборки заварить перлитными электродами марки BÖHLER FOX CM 2Kb, или марки Phoenix SH Chromo 2KS, или марки ОК 76.28 с последующей местной термообработкой шва. Для проведения термообработки ремонтных участков шва вварки верхнего штуцера А1 была привлечена организация, специализирующаяся на термической термообработке сосудов и аппаратов.
Ремонт корпуса подогревателя выполнялся в соответствии с требованиями ФНП [2, 3], ПБ [1], ГОСТ Р 54803-2011 [4], СТО 00220227-005-2009 [5] и разработанных технологических рекомендаций.
Форма и размеры разделки кромок в выборке после удаления дефектного участка шва в сварных соединениях подогревателя приведены на рис. 7.
Заварка выборок в шве вварки штуцера А1 на внутренней поверхности выполнялась поочерёдно на диаметрально противоположных участках шва (рис. 7, г). С наружной поверхности шва вварки штуцера А1 сварка осуществлялась одновременно двумя сварщиками на диаметрально противоположных участках ремонтируемого шва.
В процессе заварки чашеобразных и эллипсообразных выборок (рис. 7, е) направление сварки в каждом последующем слое менялось на взаимно-перпендикулярное относительно нижележащего слоя. По завершению заварки выборки облицовочные слои накладывались вдоль ремонтируемого шва.
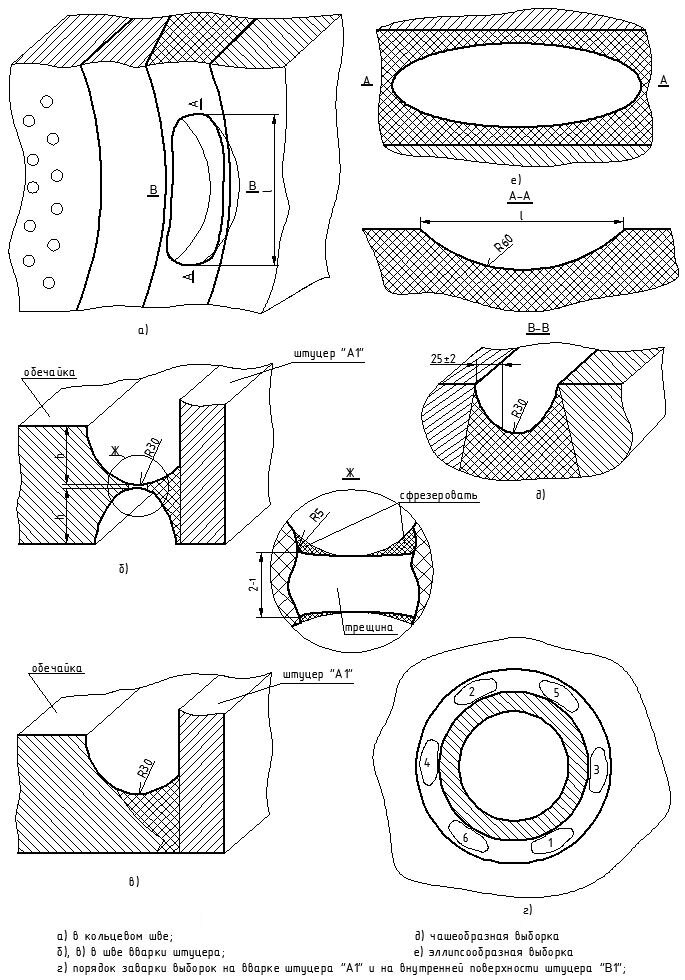
После заварки всех выборок с наружной и внутренней поверхности ремонтное сварное соединение вварки штуцера А1 в корпус подогревателя было подвергнуто местной термической обработке – высокотемпературному отпуску (Т = 710….730 °С, время выдержки – 6…7 ч). Термическая обработка производилась непосредственно после окончания сварки, при этом не допускалось снижение температуры подогрева.
В кольцевом шве распределительной камеры в шве вварки штуцера В1, а также в местах шва приварки перегородки к обечайке и трубной решётке механическим способом удалялись участки шва с трещинами. При удалении дефектного участка шва в выборке также формировалась чашеобразная или эллипсообразная выборка, где больший диаметр эллипса располагался вдоль шва, а малый – по ширине шва с заходом в основной металл обечайки или с разделкой кромок в выборке под сварку в соответствии с рис. 7. При подготовке кромок в выборках и в разделке после механической обработки обеспечивалась поверхность шероховатостью Rz 40 по ГОСТ 2789-73 [6] .
В процессе удаления участка шва с трещиной проводились ВИК и ПВК с целью подтверждения полноты удаления трещины на боковых поверхностях выборки. Глубина выборки была на 1…2 мм больше глубины распространения трещины.
В кольцевом шве приварки обечайки к трубной решётке с наружной поверхности в средней части длины сквозной поперечной трещины (см. рис. 2, 3) по ширине шва с трещиной 51 мм выполнена зацентровка участка и последующая засверловка (сверло диаметром 20…25 мм) на полную толщину стенки обечайки. Полная высверловка металла с трещиной до получения сквозного отверстия диаметром 53 мм выполнена путём последовательной замены свёрл меньшего диаметра сверлами больших диаметров через каждые 4…5 мм в шве.
После высверловки в отверстии механическим способом выполнена подготовка кромок под сварку в соответствии с рис. 8 и произведён ПВК поверхности кромок и отверстия на отсутствие дефектов в виде трещин, расслоений.
При положительных результатах контроля подготовленных поверхностей кромок и отверстия глухой стакан устанавливали в отверстие (рис. 8) с закреплением сборки тремя равноудалёнными прихватками длиной 10…15 мм и высотой 2,5…3 мм. Вварка стакана в корпус распределительной камеры с наружной и внутренней поверхности производилась ручной дуговой сваркой на постоянном токе обратной полярности с применением высоконикилевых электродов марки ОЗЛ-25Б по ТУ 1273-101-36534674-98 (допускается ОК-92.45 по классификации ENiCrMo-3/AWS A5.11) без последующей термообработки.
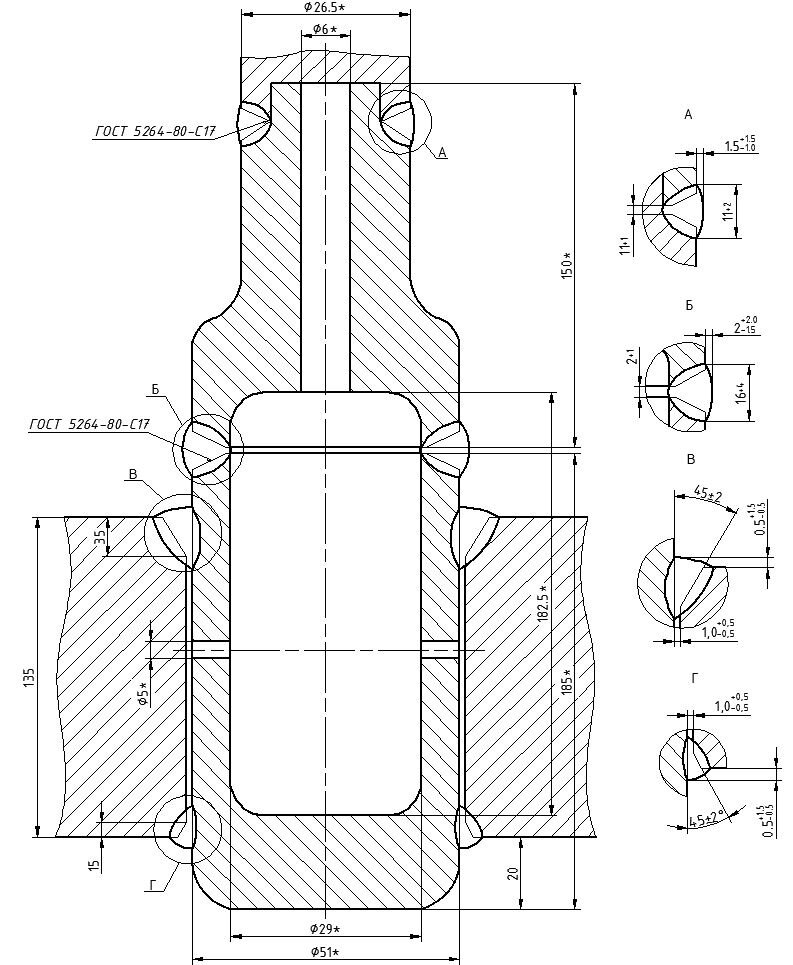