Автор: А.М. Добротворский, А.В. Копыльцов, М.А. Добротворский (ЗАО «НПО «Ленкор»).
Опубликовано в журнале Химическая техника №1/2017
Введение
Технологическое оборудование нефтеперерабатывающей и нефтехимической промышленности эксплуатируется в условиях совместного воздействия повышенных температур, давлений, взрывоопасных и агрессивных технологических сред, а также механических нагрузок разного характера. В подобных условиях неизбежны отказы оборудования, которые приводят к временной остановке производства, а также к инцидентам и авариям, сопряженным с большими материальными потерями и человеческими жертвами. Причинами отказов могут стать дефекты изготовления оборудования, металлургические дефекты конструкционных сталей, различные виды коррозионного поражения металла, из которого изготовлено оборудование.
Установление причин отказов, анализ механизмов разрушения оборудования – актуальная научно-техническая задача. Результаты соответствующих исследований отражены во многих специализированных изданиях, а также в технических отчетах по расследованию причин аварий.
Особое значение приобретает наряду с исследованием причин отказов оборудования, проработавшего длительные сроки эксплуатации, исследование инцидентов, связанных с оборудованием, проработавшим сроки, существенно меньшие проектных (месяцы, иногда дни и даже часы с начала эксплуатации).
За рубежом созданы специальные анонимные (без указания предприятий и организаций) базы данных по причинам выхода из строя технических устройств, которые служат справочным материалом для инженеров, эксплуатирующих оборудование опасных производственных объектов. Вопрос о создании единой федеральной базы данных по инцидентам, связанным с эксплуатаций технических устройств, был поставлен нами на заседании секции безопасности объектов нефтегазового комплекса НТС Ростехнадзора.
Для выявления причин отказов в ряде случаев бывает достаточно применения стандартных методов неразрушающего контроля и оптической металлографии.
Но в большинстве случаев установление причин отказов требует применения современных физических и физикотехнических методов исследования. Их использование становится совершенно необходимым для представления рекламаций заводам-изготовителям и, особенно, зарубежным поставщикам оборудования, так как их аргументация часто основана на аналогичных исследованиях, проводимых на уровне мировых стандартов.
Методы
Далее приведены возможности современных физических и физико-химических методов, которые в настоящее время применяются в практике работ выявления причин отказов ЗАО «НПО «Ленкор».
Современные методы химического анализа. Рентгенофлуоресцентная спектроскопия позволяет проводить химический экспресс-анализ сталей в полевых условиях для проверки его соответствия маркировке. Атомно-эмиссионная спектроскопия дает точный количественный анализ сталей и сплавов (включая углерод).
- Оптическая микроскопия в совокупности с программными комплексами типа Тиксомет (Thixomet) позволяет проводить автоматический анализ структуры металлов, в том числе с определением распределения зерен по размерам и среднего размера зерна в соответствии с ГОСТ 5639.
- Растровая электронная микроскопия (РЭМ) позволяет исследовать структуру металлов с разрешением, на несколько порядков превосходящим оптическую микроскопию.
- Рентгеновский микроанализ. Этот метод применяется в совокупности с растровой электронной микроскопией и позволяет производить химический анализ отдельных элементов микроструктуры металла, а также «картографировать» распределение элементов в выделенных областях металлических шлифов.
- Атомно-силовая микроскопия позволяет исследовать структуру металла в тех же и больших разрешениях, что и РЭМ. С помощью этого метода можно производить микроскопические исследования рельефа шлифов и определять твердость различных участков металла.
- Рентгенофазовый анализ в современном приборном исполнении позволяет производить тонкие исследования фазового состава металла, неметаллических включений на межзеренных границах, коррозионных отложений.
- Метод термодесорбции в совокупности с масс-спектрометрическим контролем выявляет состав газовых примесей в металлах, в том числе водорода, что особенно актуально при исследовании отказов оборудования, работающего в водородсодержащих средах.
Примеры исследований
Примеры исследований причин отказов технологического оборудования НПЗ, осуществленных ЗАО «НПО «Ленкор» с применением указанных методов, показывают, какова роль применения современных физических и физико-химических методов в выявлении причин отказов.
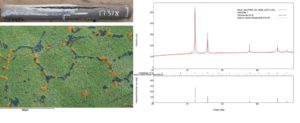
а – общий вид трубы после разгерметизации; б – данные РЭМ с картограммой распределения химических элементов
в основном металле (оранжевый цвет – кремний, никель и ниобий, зеленый – железо, серый (темно-зеленый) –
обогащенная хромом фаза); в – результаты ренгенофазового анализа состава образца сплава НК-40
Разгерметизация реакционной трубы установки получения водорода (рис. 1). По данным РЭМ, рентгеновского микроанализа и рентгенофазового анализа в микроструктуре металла разрушенной трубы под действием высокой температуры произошли необратимые изменения – выпадение карбидов хрома и силицидов ниобия по границам зерен, что привело к ослаблению межзеренной когезии, т.е. к охрупчиванию металла. Толчком к развитию хрупкой трещины послужил локальный перегрев трубы в зоне уплотнения и разрушение катализатора, частицы которого сохранились на внутренней поверхности трубы в зоне разрушения. В силу образования уплотнения могли происходить также скачки давления в трубе, что явилось дополнительным фактором малоциклового динамического воздействия внутреннего давления, способствовавшему разрушению.
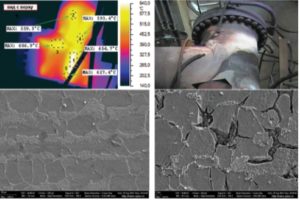
установки УПВ: данные тепловизионного контроля
работающего коллектора (а) и его внешний вид (б); структура
образца металла коллектора печи (×3000)
в объеме стенки (в) и на внутренней стороне
стенки в месте перегрева с характерными
признаками водородной коррозии (г)
Перегрев коллектора конвертированного газа установки УПВ (рис. 2). По данным РЭМ, локальные перегревы в корпусе коллектора, возникшие в зонах несплошности футеровки, привели к развитию водородной коррозии углеродистой стали на участках возникновения прямого контакта металла с горячим синтез-газом. Микроструктура металла этих коллекторов характеризуется практически полным распадом перлита. Выявляемые процессы воздействия коррозионно-активной среды являются необратимыми и могут привести к резкому изменению механических характеристик металла.
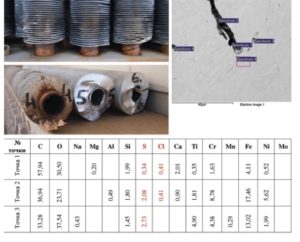
установки ЭЛОУ-АВТ-7:
а, б – общий вид дефектных трубок с трещинами;
в, г – данные РЭМ и рентгеновского микроанализа
с замером химического состава в различных областях
окрестности трещины
Разгерметизация трубок воздушных холодильников установки ЭЛОУ-АВТ-7 (рис. 3). По данным рентгеновского микроанализа, в вершинах образовавшихся трещин присутствуют хлор и сера. Это позволило сделать вывод о том, что образование трещин и разрушение труб (сталь 10Х17Н13М2Т) аппаратов воздушного охлаждения произошло вследствие стресс-коррозии – хлоридного растрескивания аустенитной стали под действием неизбежного сочетания внутренних и приложенных напряжений, обусловленных технологией изготовления труб и конструкцией аппарата в соответствии с действующими стандартами. Присутствие сероводорода усиливает интенсивность растрескивания. Полная разгерметизация труб явилась результатом движения магистральных трещин в зоне наибольшего риска развития стресс-коррозии – на входе в трубную систему секций, где реализуется совокупность негативных факторов, способствующих коррозионному растрескиванию: наличие хлоридов в водяном конденсате, повышенная температура среды, максимальный уровень напряжений.
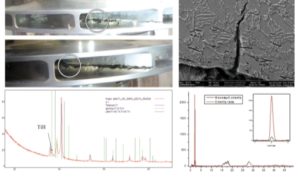
компрессора:
а, б – внешний вид разрушившегося колеса и
микроструктура вблизи поверхности дефектного участка
(×2500); в – рентгенодифракционный спектр металла
из области разрушения с гидридным пиком;
г – термодесорбционный пик водорода
образца дефектного металла
Разрушение колес титанового ротора, проработавшего в штатном режиме всего несколько часов (рис. 4).
Исследования методом рентгеновской дифракции позволило установить наличие фазы гидрида титана в наиболее поврежденных участках колеса. Данные термодесорбционного исследования показали, что концентрация водорода в приповерхностном слое на этих участках соответствует массовой доле гидрида 10%. Был сделан вывод, что причиной разрушения стало гидридное растрескивание в условиях контакта металла с сухим водородом. Разрушение лопаток рабочего колеса компрессора произошло под действием высоких напряжений, возникающих при вращении вала. Разрушению подверглись зоны металла, претерпевшие значительную деградацию механических свойств (прочности и пластичности) из-за насыщения их водородом.
Заключение
Приведенные примеры показывают, что без применения современных физических и физико-химических методов невозможно было бы со всей убедительностью выявить причины отказов. Подобные данные могут предъявляться поставщикам оборудования в досудебных разбирательствах, а также выноситься на рассмотрение арбитражных судов.