Автор: Ал. В. Костюков, Е.В. Тарасов, Д.В. Двухжилов (ООО НПЦ «Динамика»); С.А. Аверьянов, В.И. Майоров (ООО «РМЗ «Газпромнефть-ОНПЗ»)
Опубликовано в журнале Химическая техника №1/2017
Развитие ремонтно-механического завода (ООО «РМЗ «Газпромнефть-ОНПЗ») неразрывно связано со становлением Омского нефтеперерабатывающего завода, который насчитывает более чем шестидесятилетнюю историю.
Ремонтно-механический завод «Газпромнефть-ОНПЗ» уникален по своим характеристикам – это единственное в Омском регионе ремонтное предприятие полного цикла.
Технологии и оборудование предприятия дают возможность выполнять широкий перечень ремонтно-восстановительных работ оборудования с получением номинальных технических характеристик.
С внедрением первых стационарных систем автоматического мониторинга и диагностики технического состояния КОМПАКС® [1] в начале 90-х годов прошлого века впервые была реализована возможность наблюдения за изменением технического состояния оборудования в реальных условиях функционирования, при воздействии деградационных и восстанавливающих факторов. Результаты применения этих систем способствовали решению ряда важнейших вопросов, связанных с эксплуатационной надежностью и ресурсом динамического оборудования. Так, было установлено, что около трети агрегатов, направляемых в плановый ремонт, в ремонте не нуждались. Более 40% агрегатов после ремонта имели такие же недопустимо высокие уровни вибрации, как и до ремонта, что требовало их демонтажа и возврата в ремонтное производство для устранения выявленных недостатков и проведения повторного ремонта.
Основные проблемы в работе динамического оборудования при этом были обусловлены следующим:
- установкой новых, но не обеспечивающих достаточный эксплуатационный ресурс подшипников;
- некачественной балансировкой роторов насосов и двигателей;
- нарушением технологии сборки агрегатов;
- некачественным монтажом на месте эксплуатации и плохой центровкой валов.
Для уменьшения влияния вскрытых проблем эксплуатации, снижения объемов повторных ремонтов, повышения качества ремонта агрегатов в 90-х годах прошлого века НПЦ «Динамика» были разработаны и внедрены стендовые системы диагностики качества производства и ремонта наиболее ответственного оборудования:
- Система вибродиагностики подшипников качения КОМПАКС®-РПП;
- Система диагностики электродвигателей КОМПАКС®РПЭ,
- Стендовая система диагностики качества сборки подшипниковых опор роторов консольных насосов КОМПАКС®-РПМ [1, 2].
Вышеперечисленные системы при разработке были оснащены автоматической экспертной системой поддержки принятия решения, реализующей уникальные алгоритмы поиска и распознавания неисправностей различной природы: механической (эксплуатационные и производственные дефекты, ошибки монтажа, недостатки проектирования), гидродинамической (насосы), электрической (электромагнитной) природы (электродвигателей).
Система вибродиагностики подшипников качения КОМПАКС®-РПП
Система вибродиагностики подшипников качения КОМПАКС®-РПП (система КОМПАКС®-РПП) предназначена для объективной оценки технического состояния подшипников качения, выявления дефектов дорожек, тел качения и сепаратора, оказывающих различное влияние на эксплуатационный ресурс подшипников [2].
В системе реализованы требования ряда стандартов ГОСТ 520–2011, ГОСТ Р 52545.1–2006, ГОСТ 32106–2013 и собственные наработки ООО НПЦ «Динамика», которые в совокупности обеспечивают высокую достоверность диагностирования.
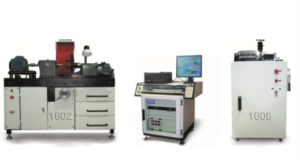
КОМПАКС®-РПП с приводами 1602, 1608
Система КОМПАКС®-РПП, эксплуатируемая в ООО «РМЗ «Газпромнефть-ОНПЗ» с 1995 г., включает две приводные установки 1602, 1608, обеспечивающие диагностику подшипников качения внутренним диаметром от 7 до 120 мм (рис. 1).
Система обеспечивает автоматическое задание рациональных условий диагностирования подшипников выбранного типа, включая условия по допустимой радиальной и осевой нагрузкам, а также по частоте вращения.
В результате диагностирования все подшипники сортируются на три категории качества, соответствующие возможным условиям их применения в оборудовании различных категорий опасности: рекомендуемые к применению на оборудовании 1-й категории опасности (с частотой вращения до 3000 об/мин и более);
- рекомендуемые к применению на оборудовании 2-й категории опасности (с частотой вращения не более 1500 об/мин);
- рекомендуемые к применению на агрегатах 3-й категории опасности (с частотой вращения не более 1000 об/мин).
За последние шесть лет системой КОМПАКС®-РПП продиагностировано более 32 000 подшипников качения, было выявлено более 8 000 дефектов – потенциальных источников брака, производственных неполадок и аварий.
На рис. 2 приведены объемы диагностируемых с помощью системы подшипников качения, а также данные по количеству бракуемых подшипников.
За весь период эксплуатации подшипников (2010– 2015 гг.) значительное уменьшение процента несоответствия наблюдается в промежутке между 2011 и 2015 гг.
В 2015 г. процент несоответствия существенно сократился (на 39%) по сравнению с 2011 г. и составил 8%.
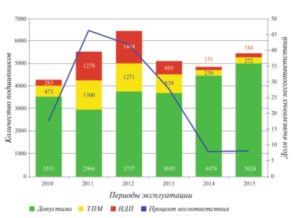
системой КОМПАКС®-РПП
Таким образом, проанализировав представленные данные, можно констатировать факт повышения качества приобретаемых подшипников качения (по объему бракуемых) в период 2011–2015 гг. более чем в 5 раз.
Проведение входного контроля подшипников качения с помощью системы КОМПАКС®-РПП позволило не только повысить достоверность оценки технического состояния, качество ремонта и надежность оборудования, но и обеспечить выпуск в эксплуатацию «невибрирующего» оборудования с минимальными погрешностями и максимальным эксплуатационным ресурсом, существенно сократить издержки, снизив к 2016 г. объем возвращаемых поставщикам подшипников до 9%.
Система диагностики электродвигателей КОМПАКС®-РПЭ
В 2016 г. на заводе внедрена Система диагностики электродвигателей КОМПАКС®-РПЭ (система КОМПАКС®РПЭ), предназначенная для вибродиагностики и контроля технического состояния электродвигателей при входном контроле и в процессе технологической обкатки его на холостом ходу при заключительных испытаниях (рис. 3).
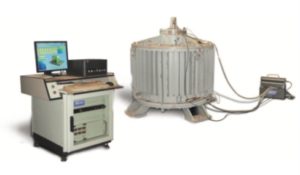
КОМПАКС®-РПЭ
Система КОМПАКС®-РПЭ обеспечивает автоматический контроль следующих параметров:
- вибрации (виброускорение, виброскорость, виброперемещение), измеряемой в плоскостях переднего и заднего подшипника двигателя в вертикальном, горизонтальном и осевом направлениях;
- тока, измеряемого по всем питающим фазам;
- температуры переднего и заднего подшипника;
- частоты вращения ротора двигателя [2].
Кроме того, в систему КОМПАКС®-РПЭ заложены требования стандартов ГОСТ 20815–93 (МЭК 34-14–82),ГОСТ Р МЭК 60034-14–2008.
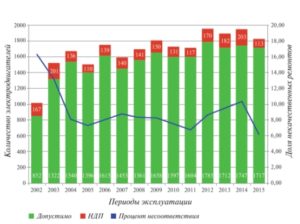
системой КОМПАКС®-РПЭ
Стендовая система диагностики электродвигателей КОМПАКС®-РПЭ эксплуатируется в ООО «РМЗ «Газпромнефть-ОНПЗ» с 1993 г. За последние 14 лет при помощи системы было продиагностировано около 24 000 единиц электродвигателей 762 различных типов, предотвращено не менее 2 100 случаев пропуска в эксплуатацию электродвигателей с недостаточным эксплуатационным ресурсом, т.е. ~160 случаев в год (рис. 4).
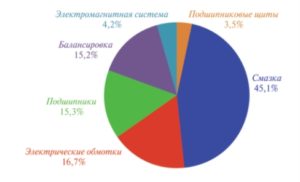
Как видно, существенное уменьшение доли ежегодно бракуемых электродвигателей произошел в период с 2003 по 2004 г. (8% в 2004 г., далее в диапазоне 7–10% с последующим спадом в 2015 г. до 6%).
Таким образом, с 2002 г. по 2015 г. доля ежегодно бракуемых системой электродвигателей снизилась на 10% и по состоянию на конец 2015 г. составила 6%, тем самым подтвердив высокое качество ремонта.
На рис. 5 представлена диаграмма распределения проблемных узлов и элементов электродвигателей, установленная на основе опыта применения системы КОМПАКС®-РПЭ на ремонтно-механическом заводе ООО «Газпромнефть-ОНПЗ».
В 2013 г. система КОМПАКС®-РПЭ была расширена подсистемой диагностики изоляции по параметрам частичных разрядов, обеспечивающая в процессе испытаний и обкатки электродвигателей после ремонта объективный контроль качества изоляции и выявление источников ухудшения электроизоляционных свойств материалов.
За 22 года эксплуатации система КОМПАКС®-РПЭ зарекомендовала себя как надежный продукт, незаменимый в ремонтном производстве и являющийся гарантом высокого качества производимого ремонта электродвигателей.
Система вибродиагностики и динамической балансировки роторов консольных насосов в собственных подшипниках КОМПАКС®-РПМ
С 1995 г. на ремонтно-механическом заводе ООО «Газпромнефть-ОНПЗ» установлена и успешно эксплуатируется Система вибродиагностики и динамической балансировки роторов консольных насосов в собственных подшипниках КОМПАКС®-РПМ (Система КОМПАКС®-РПМ), предназначенная для вибродиагностики технического состояния собранных подшипниковых опор консольных насосов, контроля качества и монтажа подшипников, входящих в состав опоры, качества и монтажа ротора с рабочим колесом и, при необходимости, проведения двухплоскостной динамической балансировки (рис. 6) [1].
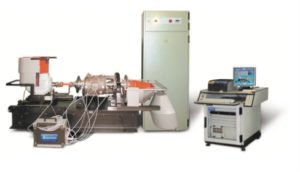
балансировки роторов консольных насосов КОМПАКС®-РПМ
В системе также заложены требования ГОСТ 22061–76, ИСО 1940, ГОСТ Р 53564–2009.
За последние 14 лет при помощи системы КОМПАКС®-РПМ продиагностировано около 4 000 единиц насосов 342 типов. По результатам диагностики не менее чем 300 насосам потребовалось выполнить динамическую балансировку с устранением дисбаланса.
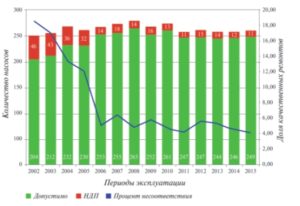
вибродиагностики и динамической балансировки роторов
консольных насосов КОМПАКС®-РПМ
Из рис. 7 видно, что доля бракуемых системой насосов ежегодно снижается и по состоянию на конец 2015 года не превышает 5%, что свидетельствует о систематической целенаправленной работе ремонтно-механического завода в направлении повышения качества ремонта насосов.
Заключение
Представленные результаты проведенного исследования о практическом применении и интеграции стендовых систем диагностики качества производства и ремонта
КОМПАКС® в технологических процессах ремонтно-механического завода позволяют произвести оценку экономической эффективности.
Каждый случай выявления несоответствия на этапе обкатки и приемо-сдаточных испытаний как минимум предотвращает пропуск оборудования с недостаточным эксплуатационным ресурсом – потенциальным источником брака, производственных неполадок и аварий в эксплуатацию. Благодаря этому снижаются эксплуатационные расходы ООО «РМЗ Газпромнефть-ОНПЗ», связанные
Рис. 5. Распределение причин браковки электродвигателей
Рис. 6. Система вибродиагностики и динамической балансировки роторов консольных насосов КОМПАКС®-РПМ
Рис. 7. Объем продиагностированных насосов системой вибродиагностики и динамической балансировки роторов консольных насосов КОМПАКС®-РПМ с транспортировкой, монтажом и опробованием оборудования на реальном производстве и производством повторного ремонта.
Если принять экономию только за счет исключения затрат на повторный ремонт 848 единиц оборудования (электродвигателей, насосов), забракованных за последние 5 лет по результатам диагностирования системами
КОМПАКС®-РПЭ и КОМПАКС®-РПМ, равной в среднем 30 000 руб. на каждую единицу оборудования, получим прямой экономический эффект не менее 5 млн. руб. в год или 50 млн. руб. в течение нормативного срока службы систем (10 лет).
Более чем за 20-летний период применения в ООО «РМЗ Газпромнефть-ОНПЗ» стендовые системы диагностики качества производства и ремонта КОМПАКС® подтвердили свою высокую эффективность, обеспечив одноразовый пуск (сдачу с первого предъявления) динамического оборудования в работу после ремонта и длительную безопасную его эксплуатацию на крупнейшем в Сибири Омском нефтеперерабатывающем заводе.
Список литературы
1. Костюков В.Н., Бойченко С.Н., Костюков А.В. Автоматизированные системы управления безопасной ресурсосберегающей эксплуатацией оборудования нефтеперерабатывающих и нефтехимических производств [АСУ БЭР – КОМПАКС®]. М.: Машиностроение, 1999. 163 с.
2. Костюков В.Н. Мониторинг безопасности производства. М.: Машиностроение, 2002. 224 с.