Автор: Е.А. Хухрин, П.В. Козлов (ООО «Алитер-Акси»).
Опубликовано в журнале Химическая техника №6/2014
Продление срока межремонтного пробега оборудования сегодня является одной из важнейших задач любого современного нефтеперерабатывающего производства. Эта проблема актуальна и для печного парка, поскольку печи наряду с прочим оборудованием являются важной частью технологического процесса. Проблематике продления межремонтного пробега трубчатых нагревательных печей уже посвящены публикации наших авторов в различных изданиях [1–3]. Тем не менее, в данной публикации остановимся еще на некоторых аспектах, связанных с продлением межремонтного пробега печного парка отечественных НПЗ.
На сегодняшний день большинство российских НПЗ переведено на двух-трехлетний безостановочный цикл эксплуатации (межремонтный пробег). Во многих компаниях есть планы дальнейшего увеличения срока межремонтного пробега, что связано с резким повышением надежности оборудования и качества применяемых материалов, надежности систем контроля и управления, качества проводимых ремонтных мероприятий, с усилением контроля при ремонтах и эксплуатации, а также зависит от внешних факторов.
В общем случае можно выделить несколько групп факторов, от выполнения которых зависит продление времени эксплуатации любой печи на срок более двух лет:
- подготовка сырья и топлива перед поступлением в печной блок и прочие внешние факторы;
- конструктивные особенности печного блока;
- физическое состояние печи;
- надежность оборудования печи;
- организационные мероприятия.
Подготовка сырья перед поступлением в печной блок и внешний факторы
К мероприятиям по данной группе факторов следует отнести установку и включение в технологическую схему современных аппаратов фильтрации, механической очистки и разделения, теплообменной аппаратуры и прочих подготовительных аппаратов. Все это призвано стабилизировать и добиться постоянства физико-механических свойств поступающих в печь потоков, что положительно сказывается на надежности и сроке безостановочной эксплуатации печи или отдельных ее агрегатов.
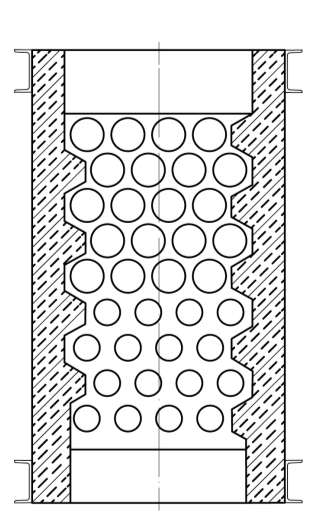
с футеровкой, имеющей выступы
Добиться постоянства химических свойств потоков практически невозможно, поскольку эти свойства напрямую зависят от поступающего на предприятие сырья и работы всей технологической цепочки НПЗ.
Здесь можно говорить только о допустимых пределах, в которых должны находиться свойства любого потока, поступающего в печь. Критическим показатель становится тогда, когда химические свойства выходят за пределы установленных допусков.
Например, изменение химического состава поступающего в змеевик сырья, в частности утяжеление нефтяных фракций или изменение соотношения водородсодержащий газ (ВСГ)/сырье, может привести к коксообразованию или аварийной ситуации и вызывает необходимость остановки и ремонта печи.
К прочим внешним факторам следует отнести природные явления (ветер, осадки, землетрясения и др.), а также техногенные, вызванные отказом или авариями смежного оборудования. Воздействие внешних факторов может привести к останову печи. В этом случае можно говорить о циклах работы (включение и выключение), что тоже может негативно сказаться на надежности печи или отдельных ее элементов. Например, термические циклы (охлаждение/нагрев) негативно влияют на надежность и долговечность службы футеровки печи, в металле труб змеевика могут появляться усталостные напряжения и т.д.
Конструктивные особенности печного блока
Данная группа факторов должна в первую очередь быть продумана на стадии проектирования печи. Конструкция печи должна быть подвергнута всестороннему анализу для возможности мониторинга, демонтажа, ремонта, очистки и т.п. максимального числа элементов оборудования печи.
В качестве примера можно привести конструкцию футеровки камеры конвекции (см. рисунок). Как видно, футеровка камеры конвекции имеет выступы для интенсификации теплообмена. Все более широкое применение этой конструкции вызвано требованиям компаний по увеличению КПД печей и указанием нормативных документов [5].
В данном случае мы получаем эффективную в плане теплообмена, но менее ремонтопригодную конструкцию. Если при отсутствии выступов футеровки пакет конвекции можно демонтировать через верх камеры и провести механическую (пескоструйную) или химическую (промывка водой, растворами или реактивами) очистку, то при наличии выступов этого сделать невозможно. В случае наличия выступов необходимо вынимать каждую трубу змеевика отдельно, срезая сварные швы змеевика.
Другим способом очистки труб в камере конвекции является применение аппаратов парообдувки или газоимпульсной очистки (ГИО).
Парообдувка и система ГИО позволяют проводить очистку труб при работающей печи.
Мерами по подготовке сырья и применением рациональных конструкций, описанных в данном разделе, добиваются стабильной работы камеры конвекции. Следовательно, не возникает необходимости сжигать дополнительное топливо для увеличения тепловой нагрузки на камеру радиации, что положительно сказывается на сроках службы труб и футеровки, времени межремонтного пробега. Описанные меры также позволяют повысить КПД печи.
В новых проектируемых печах должен быть заложен запас по тепловой мощности горелочных устройств, достаточный для того, чтобы без ущерба для процесса нагрева можно было отключать какую-либо горелку с целью ремонта или проведения профилактических мероприятий.
При проектировании узлов утилизации теплоты отходящих дымовых газов (УУТ) должны быть рассмотрены схемы дублирования или выбран рациональный режим работы тягодутьевого оборудования, само оборудование должно иметь запас по мощности.
Физическое состояние печи
Не секрет, что многие печи при переходе на двухгодичный или больший цикл межремонтного пробега уже имеют определенную наработку. Зачастую в силу этого невозможно перевести печь на более длительный цикл. Лимитирующими факторами являются, прежде всего, срок эксплуатации труб змеевика (наработка змеевика), во вторую очередь – футеровка и прочее оборудование, в меньшей степени – состояние обшивки печи и самого каркаса. В случае со змеевиком, для которого срок эксплуатации составляет 100 000 ч (12,5 лет), если наработка составляет уже более половины этого времени, то переход на межремонтный пробег, равный (или более) трем годам, может быть опасен и неосуществим. При этом во время плановых ремонтов необходимо произвести замену труб, толщина стенки которых приближается к минимально допустимому значению и которые могут выработать свой ресурс до будущего межремонтного периода.
На некоторых типах печей устаревших конструкций (шатровые печи, печи риформинга постройки шестидесятых – семидесятых годов) увеличение срока межремонтного пробега сопряжено с определенными трудностями. Например, наличие подземной системы отвода дымовых газов (борова) зачастую требует постоянного ежегодного ремонта, поскольку борова подтапливаются атмосферными осадками и грунтовыми водами, вследствие чего происходит обрушение кирпичной кладки. Таким образом, перевод печей устаревших конструкций на длительные сроки межремонтного пробега должен сопровождаться не только ремонтом, но и реконструкцией, а в идеальном варианте – полной заменой печи более современной.
Надежность оборудования печи
Надежность оборудования, установленного в печи, зависит как от качества изготовления этого оборудования (горелки, тягодутьевое оборудование, первичные приборы КИП и А и др.), так и от режимов его эксплуатации. В проектной и рабочей документации, как правило, не содержится требований к надежности оборудования. Частично проблему надежности решает запас по мощности и дублирование. Тем не менее, от производителей необходимо требовать увеличения срока гарантии, межремонтного пробега и безотказной эксплуатации.
Следует отдельно отметить систему управления и мониторинга оборудования. Система управления является важной составляющей надежной безостановочной работы.
От надежности и правильности реализованных алгоритмов во многом зависит долговечность оборудования.
Правильно отрегулированные горелки не позволяют «набрасывать» факел на змеевики печи, что обеспечивает увеличение срока службы труб.
Наличие поверхностных термопар позволяет определить локальные перегревы экрана, вовремя принять меры по обеспечению равномерности нагрева и избежать закоксовывания труб, тем самым также продлить его срок службы.
Наличие специального основания и системы мониторинга вибрации тягодутьевого оборудования позволяет продлить срок эксплуатации вентиляторов и дымососов.
На стадии проектирования необходимо предусматривать ручное дублирование отдельных алгоритмов и блокировок для возможности оперативного перехода на ручной режим и замену отдельных элементов оборудования печи. При этом в обязательном порядке должны быть соблюдены все требования нормативных документов [4].
Организационные мероприятия
К данному разделу следует отнести мероприятия по следующим направлениям:
- планирование работ. Это может быть как финансовое планирование, так и составление графиков ремонтов и сроков межремонтного пробега. Следует отметить, что время проведения ремонта при переходе на трехгодичный и более длительные циклы работы установки может увеличиваться в связи с износом труб змеевика и оборудования печи (увеличение объемов ремонтных работ). Особенно это становится актуально на третьем и последующих межремонтных циклах;
- контроль качества. Контроль качества необходимо осуществлять на предприятиях-изготовителях, а также усиливать входной контроль, поступающих материалов, изделий и оборудования;
- контроль производства работ при ремонтах, в том числе пооперационный;
- контроль за работой печного блока в процессе эксплуатации.
Все перечисленные мероприятия требуют усиления ответственности всех инженерных служб предприятиязаказчика, монтажных и ремонтных организаций. В первую очередь это относится к механикам и инженерам отдела технического надзора.
Возможно также привлечение сторонних контролирующих организаций.
Таким образом, в данной статье проанализированы факторы, от которых зависит продление срока безостановочной эксплуатации любого печного агрегата, и возможные проблемы, возникающие в результате подготовки и перехода на длительные сроки безостановочной эксплуатации. Предлагается учитывать данные факторы при планировании мероприятий по продлению срока межремонтного пробега.
Список литературы
- Жидков А.Б. Опыт и перспективы ремонта по техническому состоянию технологических печей на предприятиях нефтепереработки и нефтехимии//Материалы отрасл. совещ. гл. механиков. Кириши, 2008.
- Жидков А.Б., Ванслов А.В., Егоренко Б.М., Тупицын К.К. Парк многокамерных печей риформинга. Перспективы ремонта и реконструкции//Химия и технология топлив и масел. 2005. №4.
- Жидков А.Б. Увеличение межремонтного пробега многокамерных печей установок каталитического риформинга. Капитальный ремонт. Реконструкция//Материалы отрасл. совещ. гл. механиков. Кириши, 2004.
- ПБ 09-540–03. Общие правила взрывобезопасности для взрывопожароопасных химических, нефтехимических и нефтеперерабатывающих производств. М.: ПИО ОБТ, 2003.
- ГОСТ Р 53682–2009. Установки нагревательные для нефтеперерабатывающих заводов. Общие технические требования. М.: Стандартинформ, 2011.