Авторы: О.В. Горчатов, Б.П. Пилин (ВНИКТИнефтехимоборудование).
Опубликовано в журнале Химическая техника №11/2018
При проведении экспертизы промышленной безопасности технологического оборудования нефтеперерабатывающей, нефтехимической, газовой и других отраслей промышленности обязательной операцией является ультразвуковая (УЗ) толщинометрия стенок сосудов и аппаратов высокого давления. Цель такой операции – определение фактической толщины стенки корпуса аппарата, оценка величины коррозионного или эрозионного износа стенок и фактической скорости коррозии. При этом часто сталкиваются с ситуацией, когда обнаруживают толщиномерами, что толщина стенок этих сосудов и аппаратов намного меньше проектной (в несколько раз!), тем самым как бы не обеспечивается требуемая по расчетам прочность корпуса сосуда и его дальнейшая безопасная эксплуатация. При этом подчас экспертные организации принимают поспешные решения о забраковке данного сосуда или колонны (которая стоит многие десятки миллионов рублей) или о высверливании или вырезке образца из стенки корпуса с целью подтверждения обнаруженного утонения стенки. Как правило, после выполнения указанных «решений» выясняется, что толщина стенки аппарата оказывается близкой к проектной, а в средней части по толщине стенки обнаруживаются какие-то несплошности в металле корпуса (рис. 1). И тут же встают вопросы: допустимы или недопустимы обнаруженные несплошности? Как квалифицированно заделать отверстие в стенке корпуса, если обнаруженные несплошности допустимы? Может ли данный аппарат быть допущенным к дальнейшей эксплуатации после проведения ремонтных работ по заделке отверстия?
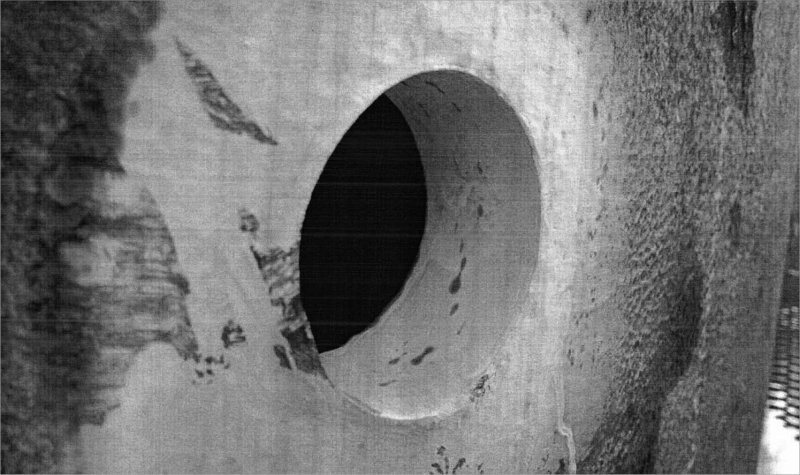
Почему так часто происходят подобные случаи?
ВНИКТИнефтехимоборудование занимался упомянутыми вопросами и решил их еще в 70-е годы прошлого столетия. Дело в том, что УЗ толщиномеры обладают высокой чувствительностью и способны принимать и регистрировать сигнал от несплошности эквивалентной площадью s = 1 мм2! При этом толщиномер после излучения зондирующего импульса принимает и регистрирует первый пришедший отраженный сигнал, который приходит к УЗ преобразователю от ближайшей несплошности. Прибор срабатывает от этого сигнала и показывает расстояние до этой несплошности, не реагируя потом на сигналы от более глубоко залегающих несплошностей, в том числе и от задней (противоположной) стенки корпуса аппарата, соответствующей истинной толщине корпуса.
А какова же природа возникновения несплошностей?
В большинстве случаев несплошности в листах имеют металлургическое происхождение. В нарезанных из отливок заготовках листов при их прокате, особенно из участков слитка, расположенных вблизи его усадочной раковины, часто встречаются газовые поры, различные включения (сульфидные, оксидные, шлаковые и т.п., особенно для сталей типа ГС), находящиеся вблизи нижней час-ти усадочной раковины слитка. В результате проката в листах располагаются эти уже раскатанные несплошности параллельно плоскости листа обычно в средней трети его толщины и ближе к одному из краев в направлении листового проката (но не обязательно!). В случае крупных газовых пор при прокате в листах могут образовываться существенные расслоения, также ориентированные параллельно поверхности листа. Они тоже располагаются чаще всего в средней трети листа. При проведении УЗ толщинометрии, как указывалось выше, прибор измеряет расстояние от контролируемой поверхности листа только до ближайшей границы раздела основной металл – ближайшая несплошность. Отсюда и получают значения толщин стенки корпуса намного меньше фактической.
Возможно появление и развитие опасных несплошностей в стенках сосудов и аппаратов при их длительной эксплуатации, если они работают в углеводородных или сероводородных средах при определенных давлениях и температурах [1]. Происходит это в результате водородной или сероводородной коррозии, как правило, в местах расположения металлургических микронесплошностей за счет накапливания в них атомарного водорода и перехода его в молекулярный, занимающий много больший объем, чем атомарный. Постепенно, по мере накопления молекулярного водорода, идет рост давления водорода в этих несплошностях, в результате чего происходит их развитие и слияние в одну общую несплошность. При этом, если несплошности расположены на разной глубине по толщине стенки, то между ними могут возникать перемычки, сигнализирующие о развитии дефекта, дальнейшее увеличение расслоений до вздутий на стенке корпуса – «блис-теров» (рис. 2, а, б) и в конечном итоге происходит разрушение стенки корпуса.

Как же подходить к оценке качества корпуса эксплуатируемого сосуда при обнаружении в нем несплошностей в результате УЗ толщинометрии?
Директивным документом при изготовлении и эксплуатации сосудов, работающих под давлением, является действующий в настоящее время ГОСТ Р 54803–2011 «Сосуды стальные сварные высокого давления. Общие технические требования» [2], в котором (см. п. 6.2.5.) указывается, что для контроля качества металла и оценки допустимости или недопустимости выявленных несплошностей в металле корпуса сосуда основным документом по оценке качества металла корпуса является ГОСТ 22727–88 «Прокат листовой. Методы ультразвукового контроля» [3] с нормой оценки для класса сплошности I.
ГОСТ 22727–88 предписывает проводить контроль УЗ эхо-методом, прямым УЗ преобра-зователем (ПЭП) на частоте 2,5… 5 МГц дефектоскопом с разверткой типа А при предельной чувст-вительности (минимальном выявляемом дефекте) – плоскодонном отражателе диаметром 5 мм (s = 20 мм2), т.е. чувствительность при УЗ дефектоскопии (УЗД), выраженная через площадь минимально выявляемого дефекта, в 20 раз меньше, чем чувствительность УЗ толщиномеров, и несплошности эквивалентной площадью менее s = 20 мм2 вообще не принимают во внимание.
Представляется целесообразным при УЗ контроле корпуса методически руководствоваться разработанными в 1988 г. ВНИКТИнефтехимоборудование «Рекомендациями по проведению ультразвукового контроля основного металла технологического оборудования предприятий отрасли» [4]. В этих «Рекомендациях…» последовательно изложены технология УЗ контроля (дефектоскопии) и алгоритм оценки выявленных несплошностей по результатам УЗД в полном соответствии с требованиями ГОСТ 22727–88 для класса сплошнос-ти I. Схема алгоритма приведена на рис. 3.
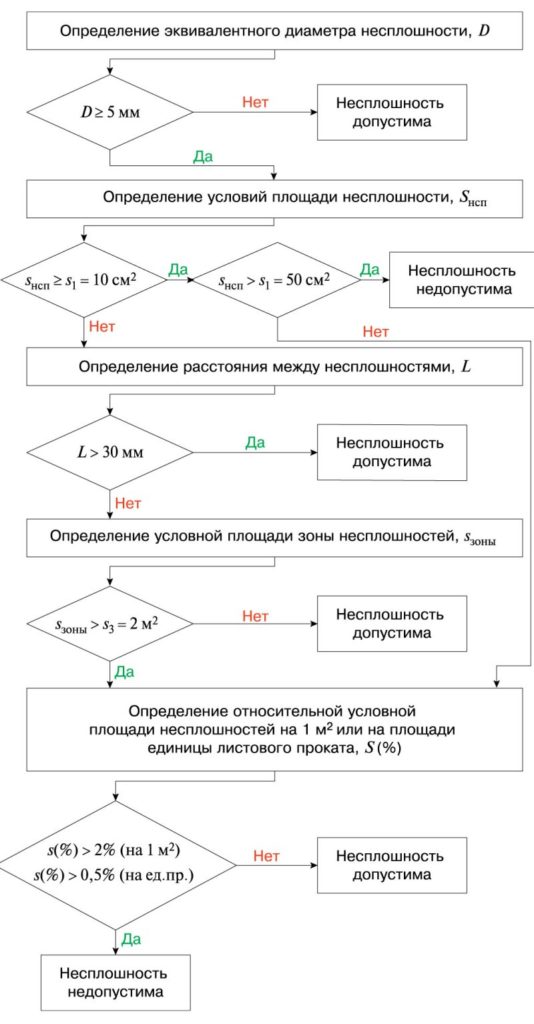
В случае подозрения на возможную водородную или сероводородную коррозию следует при УЗ контроле убедиться в отсутствии перемычек между соседними несплошностями, расположенными на разной глубине по толщине стенки, путем сканирования наклонными ПЭП во взаимно противоположных направлениях относительно направления проката. Эти перемычки могут свидетельствовать о развитии несплошностей из-за коррозии. Выявляются перемычки с помощью наклонных УЗ ПЭП с углами ввода последовательно 45° и 60° (или 70°, в зависимости от толщины стенки) на тех же частотах, что и для прямых ПЭП, при предельной чувствительности, соответствующей чувствительнос-ти при контроле сварных швов той же толщины, что и стенка корпуса аппарата. При этом следует обращать внимание на наличие или отсутствие сигналов от наклонных ПЭП по границам несплошностей. Особенно внимательно надо контролировать участки, примыкающие к сварным швам обечаек, если несплошности выходят на сварной шов. При этом надо фиксировать амплитуды эхо-сигналов и под каким углом УЗ луча лучше всего выявляются эти сигналы.
В случае обнаружения перемычек наклонными ПЭП и подозрении, что расслоения вызваны водородной коррозией, следует провести акустико-эмиссионный (АЭ) контроль сосуда. Контроль этот должны выполнять высококвалифицированные специалисты АЭ метода. Особенно надо быть внимательными после окончания выдержки на предельном (Pисп) давлении и начавшемся сбросе давления, так как обычно считают, что сосуд выдержал испытательное давление, выключают АЭ аппаратуру и производят сброс давления. А именно на сбросе наилучшим образом проявляют себя дефекты металла в виде расслоений, вызванных именно водородной или сероводородной коррозией. Если АЭ контроль не выявил развивающихся (растущих) дефектов, то считают, что сосуд выдержал испытания и может быть допущен к эксплуатации.
Если при АЭ контроле в местах расположения выявленных несплошностей обнаружены сигналы, соответствующие источникам I или II класса опасности по «Правилам организации и проведения АЭ контроля…» ПБ 03-593–03 [5], на давлении, равном или больше рабочего, то в этих местах следует после АЭ испытаний произвести снова УЗ контроль наклонными ПЭП.
Если амплитуды УЗ сигналов в этих местах не превышают более чем на 2…4 дБ сигналы от предельно допустимых дефектов для сварных швов той же толщины, что и толщина корпуса обечайки, и угол ввода УЗ луча, обеспечивающий наилучшую выявляемость обнаруженных ранее в этих местах дефектов, не изменился, сосуд или аппарат может быть допущен к эксплуатации с периодическим (через 3–6 месяцев) УЗ контролем отмеченных мест с целью наблюдения за поведением этих дефектов.
Если амплитуды УЗ сигналы превышают на 6 и более дБ предельно допустимые дефекты для сварных швов или изменился угол наилучшей выявляемости несплошностей в местах, проконтролированных УЗД до испытания АЭ методом, сосуд должен подлежать ремонту или отбраковке.
В местах, где АЭ сигналы соответствуют классу опасности III и более, зарегистрированы при давлении ниже рабочего и подтверждены затем УЗ контролем, сосуд однозначно подлежит отбраковке и возможному ремонту.
В некоторых случаях при обследовании сосудов возникает необходимость в вырезке образцов, чтобы убедиться в наличии или отсутствии водородной коррозии, и на этих образцах определить реальные прочностные механические свойства металла корпуса сосуда с целью оценки возможности его дальнейшей эксплуатации. Но при этом встает вопрос: каких размеров надо делать вырезку и как потом заделывать в сосуде образовавшееся отверстия, учитывая при необходимости термообработку в месте заварки отверстия, чтобы сосуд мог эксплуатироваться дальше?
ВНИКТИнефтехимоборудование в 1977 г. (в то время Нижне-Волжский филиал ГРОЗНИИ) была разработана и разослана по предприятиям нефтепереработки и нефтехимии «Инструкция по вырезке образцов и заделке отверстий реакторов установок каталитического риформинга и гидроочистки из углеродистых и низколегированных марганцовистых сталей» [6]. В этой инст-рукции подробно изложены все требования по вырезке образцов минимальных размеров, но позволяющих получить из них стандартные образцы для проведения всех необходимых по действующим ГОСТам механических испытаний металла, а также изложен порядок изготовления пробок и заделки отверстий в корпусе сосуда. Выполнение всех положений инструкции гарантирует, как показала практика, достаточность количества металла для механических испытаний, надежную заделку отверстий и дальнейшую безопасную эксплуатацию сосуда.
Следует отметить, что имеющийся практический опыт показывает, что при отсутствии водородной коррозии могут длительно эксплуатироваться сосуды (колонны) с площадью расслоений, намного больших указанных в ГОСТ 22727–88.
Известна длительная эксплуатация колонны с обнаруженным через несколько лет расслоением в средней части толщины листа в виде равнобедренного треугольника с основанием 800 мм, выходящим на вертикальный сварной шов обечайки, и высотой треугольника расслоения 2000 мм при длине всего листа обечайки (по горизонтали) 5000 мм и ширине листа обечайки (по вертикали) 2000 мм. После успешного гидроиспытания колонны с указанным расслоением на прочность и плотность в сопровождении АЭ метода, при последующем затем УЗ контроле отсутствовали УЗ сигналы от наклонных ПЭП по всему периметру указанного расслоения, кроме участка стыковки со сварным швом, где УЗ сигналы превышали не более, чем на 2…4 дБ предельно допус-тимые дефекты для сварных швов той же толщины. Колонна была допущена к дальнейшей эксплуатации до очередного капитального ремонта с заменой данного листа обечайки корпуса в планируемый ремонт, что и было потом сделано.
Таким образом, изложенный в данной статье подход к оценке качества металла корпусов колонн, сосудов и аппаратов при обнаружении разнотолщинности их стенок по данным ультразвуковой толщинометрии исключает возможность неоправданной забраковки работоспособных аппаратов и вывод их из эксплуатации. .
Список литературы
- Феоктистов В.А., Аюян Г.А., Ватник Л.Е., Чернова Г.А. Особенности расслоения металла сборников сжиженного пропана//Химия и технология топлив и масел. 1985. ¹8. С. 13–15.
- ГОСТ Р 54803–2011. Сосуды стальные сварные высокого давления. Общие технические требования.
- ГОСТ 22727–88. Прокат листовой. Методы ультразвукового контроля.
- Рекомендации по проведению ультразвукового контроля основного металла технологического оборудования предприятий отрасли. Волгоград: ВНИКТИнефтехиоборудование, 1988.
- ПБ 03-593–03. Правила организации и проведения акустико-эмиссионного контроля сосудов, аппаратов, котлов и технологических трубопроводов. М.: Госгортехнадзор России, 2003.
- Инструкция по вырезке образцов и заделке отверстий реакторов установок каталитического риформинга и гидроочистки из углеродистых и низколегированных марганцовистых сталей. Волгоград: НВФ ГРОЗНИИ, 1977.