Автор: П.Е. Чепурнов, В.А. Кудряшов, А.Н. Бережной (АО «КНПЗ»);
В.Н. Костюков, А.В. Костюков, А.А. Синицын (НПЦ «Динамика»).Опубликовано в журнале Химическая техника №12/2015
В статье представлены результаты применения технологии безопасной ресурсосберегающей эксплуатации оборудования на основе систем диагностики и мониторинга его технического состояния в реальном времени на Куйбышевском нефтеперерабатывающем заводе. Внедрение данной технологии позволило в реальном времени автоматически получать и практически использовать достоверную диагностическую информацию о состоянии оборудования, что обеспечило высокую надежность и техногенную безопасность производства.
Введение. Снижение эксплуатационных затрат и потерь от аварий и простоев производства, связанных с внезапным выходом из строя оборудования, является основным источником повышения рентабельности нефтеперерабатывающих и нефтехимических предприятий.
Сокращения потерь до минимума можно добиться, проводя своевременное целенаправленное техническое обслуживание и ремонт оборудования, используя в полной мере заложенный в него ресурс.
Исключение внеплановых, аварийных остановок оборудования опасных производственных объектов (ОПО), существенным образом влияющих на возникновение инцидентов и соответственно вызывающих падение технико-экономических показателей производства, возможно только путем обеспечения наблюдаемости его технического состояния. Наблюдаемость ОПО, в свою очередь, реализуется с помощью мониторинга входящих в них объектов с целью определения их текущего технического состояния и прогноза их перехода в предельное состояние, что обеспечивает 100%-ное исключение аварийных ситуаций, сокращение расходов на эксплуатацию, устранение последствий аварий, поломок оборудования и убытков от простоев комплексов, о чем свидетельствуют многолетний опыт и практика [1–4].
Анализ статистики отказов нефтеперерабатывающих и нефтехимических производств показал, что более 75% отказов оборудования составляют отказы динамического оборудования, которые нередко являются причиной инцидентов, производственных неполадок и аварий технологических установок и производств [3]. Надежная и безопасная работа динамического оборудования ОПО зависит от качества его изготовления, монтажа, эксплуатации и ремонта, оптимального ведения технологического режима, т.е. от культуры производства на всех этапах жизненного цикла оборудования. Однако существующая на большинстве нефтехимических предприятий система планово-предупредительных ремонтов (ППР) не позволяет обеспечить достаточный уровень безопасности и надежности технологических комплексов предприятия.
Для решения этих проблем, начиная с 2002 г., на Куйбышевском НПЗ осуществляется внедрение технологии на основе автоматизированных систем управления безопасной ресурсосберегающей эксплуатацией и ремонтом оборудования (АСУ БЭРтм).
На сегодняшний день стационарными системами диагностики и мониторинга технического состояния (СДМ) в режиме реального времени автоматически контролируется и диагностируется техническое состояние 415 агрегатов первой и второй категории опасности (насосы, аппараты воздушного охлаждения, поршневые и центробежные компрессоры) на установках 35/11-1000, АВТ-5, АВТ-4, Висбрекинг, 24/6, 24/7 и ЛГК АО «КНПЗ» по параметрам вибрации, температуры, тока потребления, частоты вращения, радиального и осевого смещения и др. (рис. 1). В ремонтно-механическом цехе внедрен участок входного контроля подшипников качения на базе системы автоматической вибродиагностики подшипников качения, который обеспечивает входной контроль подшипников с посадочными диаметрами от 7 до 120 мм, и в эксплуатацию проходят только подшипники с максимальным потенциальным ресурсом.
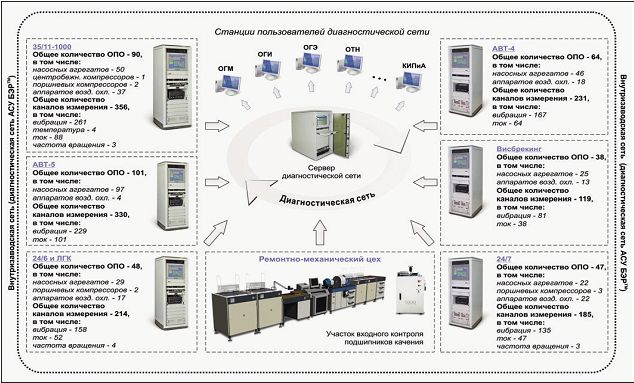
Результаты применения технологии эксплуатации оборудования на основе СДМ иллюстрирует пример 12-месячной эксплуатации динамического оборудования установки атмосферно-вакуумной перегонки нефти АВТ-5 АО «КНПЗ». Как уже указывалось, наибольшую интенсивность отказов имеет динамическое оборудование, поэтому наблюдение за техническим состоянием последнего позволяет предприятию значительно уменьшить риск отказа технологической установки в целом.
В состав динамического оборудования установки АВТ-5 АО «КНПЗ», контролируемого СДМ, входит 101 насосный агрегат.
Критичность оборудования определяет период мониторинга его технического состояния, а значит, и объем оснащения стационарными системами мониторинга состояния оборудования [5, 6]. При этом критичность оборудования определяется ответственностью технологической позиции, степенью техногенной опасности, а так же вероятностью отказа в процессе эксплуатации.
Для обеспечения безопасной ресурсосберегающей эксплуатации технологической установки в целом необходимо исключить (существенно снизить) риск отказов оборудования и возникновения по этой причине аварий и простоев. Необходимо количественно определить базовый уровень вероятности пропуска отказа с учетом числа агрегатов 1-й и 2-й категории опасности, степени и периодичности контроля их технического состояния.
При расчете базовой вероятности пропуска отказа оборудования учитываются лишь агрегаты 1-й и 2-й категории, а также степень их оснащения СДМ, которая выявляет наиболее полный спектр возможных неисправностей, приводящих к отказам в период эксплуатации, включая неисправности торцовых уплотнений по параметрам температуры, давления и уровня затворной жидкости.
Базовая вероятность пропуска отказа динамического оборудования на установке АВТ-5 АО «КНПЗ» с учетом степени оснащенности агрегатов 1-й и 2-й категории опасности составляет 15,4%. Именно внедрение системы мониторинга позволило существенно снизить базовую вероятность пропуска отказа динамического оборудования установки, так как до внедрения системы она составляла 97%, что обусловливается числом параметров, контролируемых РСУ.
Анализ базовой вероятности пропуска отказа оборудования технологических установок НПЗ очень важен на стадии проектирования и строительства, так как именно в данный период формируется стоимость их эксплуатации, а значит стоимость всего жизненного цикла технического комплекса. Если базовый уровень вероятности пропуска отказа отражает оснащенность оборудования технологического комплекса системами мониторинга, а значит, и степень управляемости надежностью оборудования на протяжении его жизненного цикла, то динамика вероятности отказа в процессе эксплуатации оборудования показывает качество проектирования, монтажа и качество самого оборудования, а также уровень технологической дисциплины персонала и достаточность мероприятий по поддержанию оборудования в допустимом техническом состоянии. Кроме того, при мониторинге риска отказа в процессе эксплуатации появляется возможность сравнивать квалификацию и качество работы разных дежурных смен к надежности эксплуатации оборудования технологического комплекса.
Вероятность отказа в процессе эксплуатации прямо пропорциональна числу агрегатов, находящихся в технических состояниях «Недопустимо» (далее по тексту «НДП») и «Требует принятия мер» (далее по тексту «ТПМ»). При переходе агрегата в состояние «НДП» персонал обязан вывести его из эксплуатации, так как в таком агрегате присутствует активно развивающийся дефект (дефекты) и его ресурс близок к 0, т.е. риск его отказа максимальный. Агрегат в состоянии «ТПМ» характеризуется тем, что на него действуют значительные деструктивные нагрузки или зарождается дефект (дефекты), развитие которого необходимо остановить путем своевременных и целенаправленных действий по снижению нагрузок или техническому обслуживанию, т.е. ресурс такого оборудования расходуется более высокими темпами, нежели в допустимом техническом состоянии и, если не предпринимать никаких мер в отношении такого оборудования, то неизбежен его переход в состояние «НДП» и отказ. В связи с этим при мониторинге вероятности отказа в процессе эксплуатации оборудования необходимо учитывать оба неблагоприятных состояния, в которых эксплуатируется оборудование.
Динамика количественных характеристик безопасности эксплуатации, которые характеризуют вероятность нахождения оборудования в технических состояниях «НДП» (Красный цвет) и «ТПМ» (Желтый цвет), представлена на рис. 2.
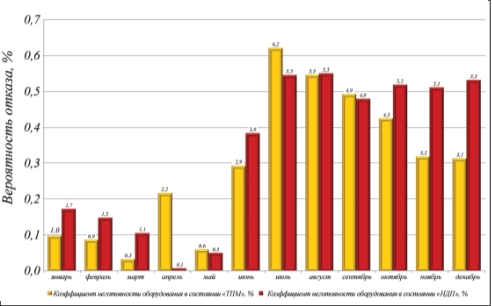
Из диаграммы видно, что уровень вероятности отказа динамического оборудования за отчетный период высокий и в среднем составляет 6,3%, а в некоторые периоды (июль 2014 г.) возрастал до 11,7% (суммарная длительность работы оборудования в состояниях «НДП» и «ТПМ»). Пробег технологической установки за период с 01.01.2014 г. по 31.12.2014 г. составил 343 суток или 94% максимально возможного времени эксплуатации из-за планового ремонта технологической установки.
Аварий и внезапных отказов агрегатов, эксплуатируемых под наблюдением СДМ, в отчетном периоде не зафиксировано.
Благодаря наличию в СДМ автоматической экспертной системы поддержки принятия решений по ближайшим неотложным действиям с оборудованием и мощного инструментария статистической обработки данных, персонал установки АВТ-5 имеет возможность анализа данных мониторинга оборудования в различных технических состояниях по автоматически сформированным диаграммам.
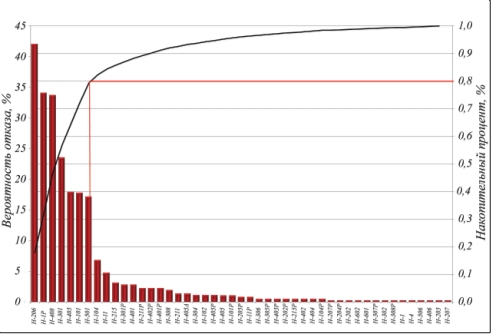
На диаграмме распределения вероятности отказа оборудования (рис. 3) видно, что первые семь агрегатов обеспечивают 80% вероятности отказа, а вероятность отказа агрегатов Н-206, Н-1Р, Н-408 максимальна. Это связано с дефектами подшипников, что соответствует предписаниям автоматической экспертной системы и подтверждено в процессе ремонтов. Это говорит о том, что на них действуют большие деструктивные нагрузки, которые, в свою очередь, сокращают ресурс агрегата.
Система позволяет сконцентрировать внимание персонала установки АВТ-5 на наиболее проблемном оборудовании, чем обеспечивает его оперативное реагирование на ухудшение состояния конкретных агрегатов в процессе эксплуатации. Ликвидация фундаментальных причин эксплуатации машинных агрегатов (первые 7 позиций на рис. 3) в опасном техническом состоянии, позволит повысить уровень безопасности по данной установке в 5 раз, кроме того, позволит сократить объем ремонтных работ, а, следовательно, и затраты на ремонт динамического оборудования установки.
Важным условием надежной работы оборудования является не только качественное, но и оперативное проведение ремонтных работ.
В результате сопоставления требуемых ремонтов по системе ППР, фактических ремонтов, зафиксированных системой и ремонтов, зафиксированных в ремонтных книгах за отчетный период, составлена диаграмма (рис. 4).

Приведенные данные показывают малоэффективность системы ППР по сравнению с эксплуатацией оборудования по фактическому техническому состоянию на основе системы мониторинга технического состояния оборудования. В 39 случаях ремонт по фактическому техническому состоянию на основе предписаний автоматической экспертной системы, позволил избежать отказов оборудования, и, как следствие, предотвратить возможные аварии и простои технологической установки.
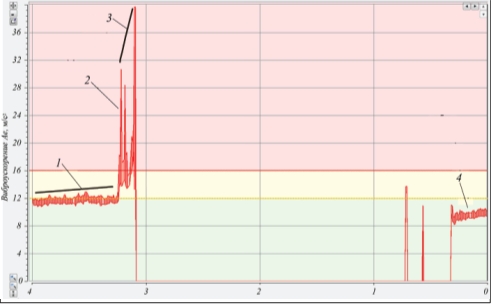
Одним из наиболее ярких примеров эксплуатации оборудования по фактическому техническому состоянию на основе предписаний автоматической экспертной системы является эксплуатация центробежного насоса Н-101 установки АВТ-5. Как видно из 4-cуточного тренда вибропараметра, отвечающего за неисправности подшипников качения, насоса агрегата Н-101, насос работает с техническим состоянием «Допустимо» с переходом в «ТПМ» (рис. 5, участок 1), при этом система выдает автоматические экспертные сообщения «Проверь внешнюю обойму подшипника», «Проверь внутреннюю обойму подшипника». Далее происходит быстрое развитие дефектов в подшипнике насоса. Значение вибропараметра достигает 30 м/с2 (см. рис. 5, участок 2), и агрегат переходит в техническое состояние «НДП», система выдает экспертные сообщения персоналу «Недопустимая скорость изменения виброускорения, Разрушение подшипника», «Проверь внешнюю обойму подшипника», «Проверь внутреннюю обойму подшипника». Последующая работа насоса сопровождается дальнейшей деградацией подшипника и быстрым ростом соответствующих вибропараметров (см. рис. 5, участок 3). Персонал оперативно провел подготовительные операции и выполнил переход на резервный агрегат, предотвратив развитие аварийной ситуации.
После проведения качественных ремонтных работ по замене подшипника и центровки агрегат был введен в работу в техническом состоянии «Допустимо» (см. рис. 5, участок 4).
Данный пример наглядно демонстрирует не только хорошую исполнительскую дисциплину персонала установки АВТ-5 АО «КНПЗ», но и своевременность, и точность выявленных системой неисправностей агрегата.
Персонал исключил развитие потенциальной аварийной ситуации. Эта потенциальная аварийная ситуация не могла быть предотвращена в рамках системы ППР, т.к. этот инцидент – ремонт – не совпал с регламентированными плановыми сроками его технического обслуживания и ремонта.
Экономическая эффективность применения АСУ БЭР™ на установке АВТ-5 АО «КНПЗ». Экономический эффект от перехода к системе управления производством на основе АСУ БЭРтм обеспечивается мониторингом состоянии основных факторов производства в реальном времени и складывается из следующих статей экономии:
- экономии от снижения потерь сырья и оборудования из-за аварий;
- экономия от снижения потерь, связанных с простоями технологического комплекса по причинам отказов оборудования;
- экономический эффект от сокращения сроков плановых остановочных ремонтов и ускорения вывода установки на технологический режим;
- экономия от снижения затрат на ремонты оборудования.
Экономия от снижения потерь сырья и оборудования из-за аварий рассчитывается в связи со снижением вероятности возникновения аварий при применении АСУ БЭР™. Благодаря системе персонал предотвратил не менее 39 случаев отказа, с последующим выводом в ремонт агрегата. Каждый из этих случаев мог привести к аварии и возможному простою технологической установки. Даже если допустить, что 1 из 100 зафиксированных системой случаев развития неисправностей агрегатов приведет к аварии, то экономия от снижения потерь сырья и оборудования на установке АВТ-5 составляет более 8 млн. руб.
Экономия от снижения потерь, связанных с простоями технологического комплекса по причинам отказов оборудования, определяется как сокращение объема добавленной стоимости, не полученной в единицу времени в результате простоя установки АВТ-5. При расчете данной экономии необходимо так же, как и в предыдущей статье экономии, скорректировать ее размер путем следующего допущения, что лишь 1 из 100 зафиксированных системой случаев развития неисправностей агрегатов приведет к снижению мощности установки и простой составит менее суток. Таким образом, экономия от снижения потерь сырья и оборудования составила около 15 млн. руб.
Экономический эффект от сокращения сроков плановых остановочных ремонтов и ускорения вывода установки на технологический режим образуется путем проведения своевременных целенаправленных и в необходимом объеме мероприятий по техническому обслуживанию и ремонту оборудования, ликвидации фундаментальных причин недостаточной производительности и отказов оборудования. Благодаря наличию
СДМ персонал не проводил ремонты динамического оборудования, контролируемого системой, в течение планового остановочного ремонта установки АВТ-5. Это позволило сократить сроки ремонта и провести пуск установки раньше планируемого срока. Экономия от сокращения сроков плановых остановочных ремонтов и ускорения вывода установки на технологический режим составила не менее 8 млн. руб.
Экономия от снижения затрат на ремонты оборудования образуется за счет исключения планово-предупредительных и внеплановых ремонтов в связи с переходом на технологию эксплуатации машинного оборудования по фактическому техническому состоянию. Следует отметить, что внедрение системы диагностики и мониторинга не отменяет проведение капитальных ремонтов по системе ППР, а позволяет отложить плановую дату капитального ремонта на максимально возможный срок в зависимости от наработки.
Внедрение СДМ на установке АВТ-5 позволило уменьшить количество и объем ремонтов, обеспечив переход от сложных и дорогостоящих капитальных ремонтов к средним и текущим.
Вследствие большого числа ремонтов насосов после остановочного ремонта расчетные затраты на ремонт были превышены ориентировочно на 600 тыс. руб., однако, это привело к большему экономическому эффекту от предотвращенных аварий на установке АВТ-5, о которых говорилось выше.
Общий экономический эффект от внедрения системы мониторинга технического состояния оборудования на установке АВТ-5 за 12 месяцев наблюдения превысил 27 млн. руб., что подтверждает окупаемость систем уже в первые годы их эксплуатации.
Выводы. Представленные данные, полученные по результатам внедрения на предприятии технологии безопасной ресурсосберегающей эксплуатации оборудования на основе мониторинга его технического состояния в реальном времени, подтверждают правильность выбранного АО «КНПЗ» подхода к управлению техногенными рисками, так как это позволило:
- полностью исключить аварийные ситуации по причине внезапного отказа оборудования;
- максимально увеличить межремонтный период эксплуатации технологических комплексов без повышения риска возникновения инцидента или аварии;
- сократить сроки плановых остановочных ремонтов, благодаря знанию фактического технического состояния значительной части оборудования;
- оптимизировать эксплуатационные расходы на техническое обслуживание и ремонт оборудования, проводя своевременные и целенаправленные мероприятия по выявлению и ликвидации фундаментальных причин отказов оборудования.
Применение АСУ БЭРтм делает прозрачными, а значит, управляемыми, процессы эксплуатации основных фондов, снижает капиталоемкость производства, увеличивает фондоотдачу и, как следствие, ведет к росту капитализации предприятия в целом. Эффективность внедрения системы для диагностики технического состояния оборудования опасных производственных объектов определяется стоимостью затрат на внедрение системы к экономии, полученной от продления срока службы основных узлов и деталей, сокращение продолжительности ремонта и простой агрегатов и некоторых других факторов. При этом значительно повышается безопасность эксплуатации ОПО на нефтеперерабатывающих и нефтехимических производствах.
Список литературы
- Костюков В.Н., Махутов Н.А., Костюков А.В. Мониторинг состояния и рисков эксплуатации оборудования в реальном времени – основа промышленной безопасности//Сб.: Федеральный справочник: Т. 26. М.: НП «Центр стратегического партнерства», 2012. С. 321–326.
- Костюков В.Н. Мониторинг безопасности производства. М.: Машиностроение, 2002. 224 с.
- Костюков А.В., Костюков В.Н. Повышение операционной эффективности предприятий на основе мониторинга в реальном времени. М.: Машиностроение, 2009. 192 с.
- Костюков В.Н., Бойченко С.Н., Костюков А.В. Автоматизированные системы управления безопасной ресурсосберегающей эксплуатацией оборудования нефтеперерабатывающих и нефтехимических производств. М.: Машиностроение, 1999. 163 с. 5. ГОСТ Р 53564–2009. Контроль состояния и диагностика машин. Мониторинг состояния оборудования опасных производств. Требования к системам мониторинга. М.: Стандартинформ, 2010. 8 с. 6. ГОСТ 32106–2013. Контроль состояния и диагностика машин. Мониторинг состояния оборудования опасных производств. Вибрация центробежных насосных и компрессорных агрегатов. М.: Стандартинформ, 2014. 5 с.