Авторы: С.В. Кислов, П.В. Балаш (ООО «НПЦ «Технологии минеральных покрытий»), В.Г. Кислов (ООО «НПО «Геоэнергетика»), А.В. Сказочкин (Калужский филиал РАНХиГС).
Опубликовано в журнале Химическая техника №8/2016
В последние годы активно развивается промышленное применение минеральных покрытий, придающих высокие антикоррозионные, износостойкие, противоабразивные, антифрикционные свойства деталям, устройствам и механизмам, работающих в различных отраслях промышленности. Во многих случаях именно свойства металлической поверхности детали дают возможность длительного и надежного функционирования деталей. Активная практика последних пяти лет позволила накопить значительный объем информации по применению многофункциональных минеральных покрытий на деталях пар трения, используемых предприятиями различных отраслей (судостроение, металлургия, нефтегазодобыча, машиностроение, энергетика и др.).
Основа оригинальной технологии минеральных покрытий для повышения износостойкости металлических деталей была создана в России в период 2009–2013 гг. [1]. После экспериментального и эксплуатационного подтверждения свойств минеральных покрытий, созданных в НПЦ «Технологии минеральных покрытий» (НПО «Геоэнергетика»), специалистами из Федерального института исследования и тестирования материалов (ВАМ, Германия) [2], РГУ нефти и газа имени И.М. Губкина, МИЭМ НИУ ВШЭ [3–5] начался этап активного использования технологии промышленными предприятиями России и ЕС.
Суть технологии заключается в создании модифицированного слоя (глубиной 5…50 мкм от поверхности металла) путем пластического деформирования поверхности с использованием ультразвукового, механического и другого вида воздействия, сопровождающего диффузию ультрадисперсных частиц минералов природного происхождения в объем металла [2, 3].
Практические преимущества технологии минеральных покрытий очевидны:
- технология не изменяет геометрические размеры деталей;
- минеральные слои могут быть созданы на поверхности локально;
- в процессе создания слоев не происходит нагрев детали;
- все технологические операции проводятся на воздухе при комнатной температуре [3].
Минеральные покрытия значительно повышают износостойкость пар трения, осуществляют антикоррозионную и противоабразивную защиту, уменьшают коэффициент трения. В процессе практического применения минеральные покрытия были созданы на поверхности деталей из различного вида сталей, титана, чугуна, бронзы, меди. Кроме того, оказалось, что детали с минеральными слоями хорошо работают, демонстрируя преимущество над всеми существующими в настоящее время покрытиями, в морской воде, соляном тумане, абразивной пыли, сероводороде, при повышенной влажности, в присутствии различных кислот и других агрессивных сред; при высокой температуре (до 1100°С), а также при термоциклических нагрузках в широком диапазоне температур.
Эти достоинства технологии обусловили создание специалистами НПЦ «Технологии минеральных покрытий» (НПЦ ТМП) минеральных покрытий на металлических деталях, которые успешно работают на таких объектах, как спецтехника Военно-морского флота России; плавучая атомная электростанция «Академик Ломоносов»; Камчатская (Мутновская) геотермальная станция; ТЭЦ ОАО «Мосэнерго»; несколько металлургических комбинатов.
В настоящее время выполнены экспериментальные исследования и используются около 80 видов минеральных материалов для создания многофункциональных минеральных покрытий.
Основные виды минеральных материалов, используемых при создании покрытий [6]
Число разновидностей
Серпентиниты Mg6[Si4O10](OH)8 | 28 |
Ряд SiO2 | 18 |
Ряд Al2O3 | 10 |
Жадеит NaAlSi2O6 | 4 |
Графит | 2 |
Алмазы | 3 |
Слюды [например, KMg3AlSi3O10(OH)2] | 4 |
Циркон Zr[SiO4] | 2 |
Бадделеит ZrO2 | 1 |
Эвдиалит | 1 |
Оливин Mg1,8Fe0,2[SiO4] | 3 |
Ряд форстерита Mg2SiO4 | 4 |
Комбинированные вещества | 10 |
Можно выделить специфику природных материалов, которые, возможно, способствуют достижению уникальных параметров деталей с минеральными покрытиями [6]:
- минералы сформировались под воздействием высоких давлений и температур, которые недостижимы при промышленном получении;
- минералы получают из горных пород, содержащих значительное количество примесей, которые в ряде случаев могут быть полезными и улучшать свойства природного материала;
- минералы содержат до сотни различных атомов различных веществ в одной молекуле, при этом атомы могут быть объединены в группы, которые могут менять свои аллотропические состояния при различном воздействии на поверхность детали при эксплуатации.
Учет конкретных характеристик таких веществ затруднен, что вызывает необходимость в специальных приемах при определении и прогнозировании их физикохимических свойств.
Отбор и переработка горной породы производится НПЦ «Технология минеральных покрытий» по многим параметрам, включающим как оценку вещественного состава породы, так и ее различные физико-химические и механические характеристики, влияющие на свойства создаваемых минеральных покрытий.
Вопросы теоретического объяснения эффектов, возникающих при легировании металлов ультрадисперсными частицами минералов природного происхождения, пока носят характер предположений. Помимо причины, указанной выше, еще одной из причин является изменение свойств минералов при измельчении [6]:
- увеличение удельной поверхности, повышение поверхностной активности;
- переход вещества в новую модификацию;
- морфизация кристаллических веществ;
- дегидратация и гидратация.
Еще один из возможных вариантов механизма действия природных минеральных материалов в узлах трения был предложен в работе [7]. Он касается использования серпентинитов как наиболее распространенных модификаторов поверхностей пар трения для решения проблемы водородного изнашивания металла и заключается в следующем. В силикатных материалах типа серпентина имеются силоксановые (мостиковые) связи Si–O–Si, при разрыве которых вследствие разрушения (измельчения) минерала образуются нескомпенсированные связи Si–O, являющиеся активными акцепторами водорода в виде Н+ или Н0. При их взаимодействии образуются скомпенсированные силанольные группы Si–OH. Таким образом, при введении в смазку (или при легировании поверхности) серпентина ультрадисперсного помола, обладающего большой удельной поверхностью и большим числом оборванных силоксановых связей, технология минеральных покрытий создает условия для связывания находящиеся у поверхности в зоне трения активного водорода, т.е. препятствует его взаимодействию с металлом и предотвращает водородное изнашивание последнего. В работе [7] делается предположение о том, что силикаты с оборванными связями Si–O–Si являются эффективными адсорбентами, поглотителями, акцепторами активного водорода, и, следовательно, могут применяться для решения проблемы водородного изнашивания металла в узлах трения.
Как показала практика, использование слоистых силикатов типа серпентинита особенно эффективно в узлах трения с экстремальными нагрузками, в том числе при высоких температуре и давлении (в НПЦ ТМП и НПО «Геоэнергетика» имеются протоколы эксплуатации деталей с минеральным покрытием прокатного стана). В этом случае можно предположить, что термическое разложение серпентина приводит к образованию более высокоэнергоплотных и твердых фаз по сравнению с исходным серпентином. Также можно предположить, что тонкодисперсный материал продуктов разложения серпентина (по-видимому, в значительной степени аморфизированный) заполняет микропоры, микротрещины, различного рода дефекты, вакансии на поверхностях узла трения, что приводит к их упрочнению [8] и значительному повышению износостойкости.
Приведем результаты стендового испытания стойкости резьбы З-133 комплекта резьбового соединения труб из стали Magnadur с минеральным покрытием и без покрытия, выполненного в 2016 г. НПЦ ТМП совместно с ООО «ПКФ-ГазНефтеМаш» и ООО «Ковровский завод бурового оборудования». Информация об испытании была представлена в выступлениях авторов настоящей статьи на III Международном Форуме Valve Industry Forum& Expo’2016 – Промышленная трубопроводная арматура для нефти, газа, энергетики, химии и ЖКХ в Москве.
Детали испытаний
Бурильная труба из немагнитной стали Magnadur 501 производится на сталелитейных заводах Германии и предназначена для создания осевой нагрузки на долото, повышения жесткости и устойчивости нижней части бурильной колонны при бурении наклонно-направленных и горизонтальных скважин, а также для исключения влияния ферромагнетизма при использовании телеметрических систем внутри трубы.
Состав стандартной стали Magnadur 501: 13,0–16,0% Cr, 18,5–22,0% Mn, 0,25–0,5% Ni, 0,3–0,6% Si, 0,35–0,60% Mo, 0,32–0,40% N, < 0,04% C, < 0,006% S, < 0,03% P, остальное – Fe.
Сопротивление нержавеющей стали коррозии напрямую зависит от содержания хрома: при его содержании 13% и выше сплавы являются нержавеющими в обычных условиях и в слабоагрессивных средах, более 17% – коррозионно-стойкими и в более агрессивных окислительных и других средах. Причина коррозионной стойкости нержавеющей стали объясняется, главным образом, тем, что на поверхности хромсодержащей детали, контактирующей с агрессивной средой, образуется тонкая пленка нерастворимых окислов. Однако образование защитной пленки окислов на поверхности создает проблемы при создании надежных износостойких покрытий традиционными способами.
К тому же стоимость трубы из немагнитной стали Magnadur 501 довольна высока, а, по данным статистики, число поломок, например насосно-компрессорных труб (НКТ), в ряде случаев достигает 80% общего числа аварий оборудования для бурения скважин. При этом в большинстве случаев (~50%) возникают отказы НКТ, связанные с резьбовым соединением [9, 10]. Все это свидетельствует об актуальности проблемы повышения износостойкости и долговечности труб, в частности нефтяного и газового сортамента.
При проведении испытаний износостойкие минеральные покрытия были созданы на комплектах образцов ниппель–муфта соединения труб из стали Magnadur 501.
В экспериментах использовали образцы с минеральным покрытием и без покрытия.
Цель настоящей работы – определение ресурса работы комплекта ниппель-муфта соединения труб из стали Magnadur 501 с минеральным покрытием по сравнению с комплектом без минерального покрытия.
Перед испытанием на все резьбовые соединения была нанесена резьбо-уплотнительная смазка РУСМА Р-14 ТУ 0254-068-46977243–2009, затем образцы (рис. 1) свинтили вручную с использованием воротка длиной 0,4 м.
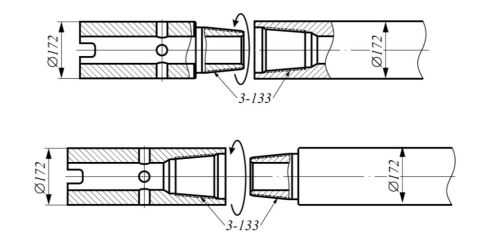
Процедура испытаний
Детали транспортировали к муфтонаверточному станку МС-4 и устанавливали в станок (рис. 2). Отмечали положение маховика относительно неподвижной станины (точка 0), свинчивали до упора и развинчивали до точки 0.
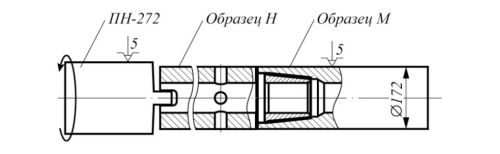
Условия свинчивания:
- скорость свинчивания – 6 об/мин;
- число свинчиваний – 400 циклов;
- момент свинчивания – не более номинального момента крепления замковой резьбы по ТУ 1324-00186528288–2010.
Так, для трубы D = 168 мм, d = 83 мм, с резьбой 3-133 номинальный момент крепления равен 31,8 кНм.
На станке МС-4 установили следующие моменты свинчивания:
- первое свинчивание – 10 кНм (1000 кгс);
- второе свинчивание – 21 кНм (2000 кгс);
Результаты испытаний
Первый комплект [образец Н (ниппель) без покрытия – образец М (муфта) без покрытия] выдержал 30 свинчиваний и развинчиваний, затем произошло заклинивание. После разворачивания видны следы залипания резьбы (разрушение резьбы по четвертой нитке, рис. 3).
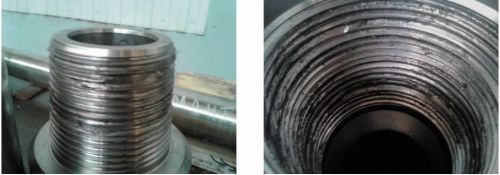
Второй комплект [образец Н с минеральным покрытием – образец М с минеральным покрытием] выдержал планируемое число циклов испытаний – 400 свинчиваний и развинчиваний. После развинчивания установлено, что повреждены были только упорные торцы образцов (рис. 4).
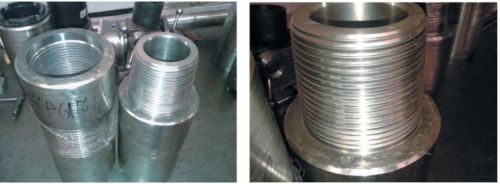
Можно сделать вывод, что износостойкие антифрикционные минеральные покрытия могут быть успешно созданы на сложной поверхности резьбового соединения.
Результат испытаний комплекта образцов трубы (ниппель –муфта) из стали Magnadur 501 показал, что с минеральным покрытием число циклов свинчивания–развинчивания более чем на порядок больше, чем у комплекта образцов из этой же стали без минерального покрытия.
Учитывая состояние резьбы с минеральным покрытием после проведения 400 циклов свинчивания–развинчивания, можно прогнозировать хорошее состояние этой пары и после 1000 циклов.
Рекомендуется при планировании большого числа операций свинчивания–развинчивания (более 100 циклов) создавать износостойкие минеральные покрытия и на торцовых поверхностях этих деталей.
Минеральные покрытия представляют собой перспективный технологический инструмент для повышения износостойкости различных деталей, узлов и механизмов, в том числе из хромсодержащих коррозионно-стойких сталей для использования в различных отраслях промышленности, в том числе в арматуростроении, компрессорной технике и нефтегазовой отрасли.
Список литературы
- Патент РФ №2421548. Способ формирования комбинированного минерального поверхностного слоя на металлических деталях, защищающего их от воздействия агрессивных сред и с заданными триботехническими свойствами.
- Kislov S., Kislov V., Ostrovsky P. and Woydt M. Localized hardening and structuring of steel by a simple process//53 Tribologie Fachtagung «Reibung, Schmierung und Verschleiβ» der GfT in Gottingen, Gottingen, 24.09–26.09.2012, Herstellung: Druckservice Zillekens, Band 2, p.49/1–49/7.
- Кислов С.В., Кислов В.Г., Сказочкин А.В., Бондаренко Г.Г., Тихонов А.Н. Эффективные минеральные покрытия для упрочнения поверхности металлических материалов//Металлы. 2015. №4.
- Кислов С.В., Кислов В.Г., Балаш П.В., Сказочкин А.В., Бондаренко Г.Г., Тихонов А.Н. Повышение износостойкости резьбового соединения стальных насосно-компрессорных труб при нанесении минерального покрытия//Нефтегазовое дело. 2015. №4. Электронный доступ: [http://ogbus.ru/years/42015/]/
- Kislov S.V., Kislov V.G., Balasch P.V., Skazochkin A.V., Bondarenko G.G. and Tikhonov A.N. Wear resistance of a metal surface modified with minerals//Materials Science and Engineering/IOP Conf. Series: Materials Science and Engineering 110 (2016). Электронный доступ: [http://iopscience.iop.org/article/10.1088/1757899X/110/1/012096/pdf].
- Грушев В.В., Лазарев С.Ю. Промышленное применение минеральных покрытий и ультразвуковой обработки. Чита: ЗабГУ, 2012.
- Хайнике Г. Трибохимия. М.: Мир, 1987.
- Юшкин Н.П. Механические свойства минералов. Л.: Наука, 1971.
- Прокофьев А.А. Технологическое повышение коррозионной стойкости резьб насосно-компрессорных труб. Дис…. канд. техн. наук. М.: Мос. гос. индустр. ун-т, 2013.
- Сароян А.Е., Субботин М.А. Эксплуатация колонн насосно-компрессорных труб. М.: Недра, 1985.