Авторы: Р.Х. Гафаров (Уфимский государственный авиационный технический университет), Т.Р. Гафаров, О.И. Нестерюк (ООО «Интерюнис»).
Опубликовано в журнале Химическая техника №6/2015
Любой процесс повреждения материала механических систем имеет минимальный набор доминирующих факторов и сопровождается комплексом явлений со специфическими причинно-следственными связями.
Установление характера и причин повреждения имеет фундаментальное значение, так как является основой расчетной схемы для оценки прочности и ресурса, критерием правильности выбора методов и режимов испытаний, исходной информацией для обоснования методов диагностирования, прогнозирования и совершенствования механических систем.
С позиций обеспечения надежности и долговечности механических систем изучение механизмов, кинетики и параметров повреждений необходимо не только для рационального выбора материала элемента или конструкции с учетом технологии ее изготовления, но, главным образом, и для установления критериев отказов и предельных состояний, периодичности и средств контроля и диагностики, методологии прогнозирования технического состояния, надежности и безопасности.
Как известно, химическая активность материалов под действием напряжений увеличивается, при этом в еще большей степени при цикличности напряжений. В связи с этим при исследовании прочности и долговечности материалов нельзя ограничиваться только механическими критериями. Коррозионно-механические повреждения, приводящие к разрушению элементов механических систем, являются основными причинами отказов оборудования химических, нефтехимических и нефтеперерабатывающих производств.
В соответствии с современными представлениями о природе разрушения материалов процесс повреждения рассматривается как многостадийный, статистический и многомасштабный [1], что обусловлено различием микромеханизмов повреждения, статистическими закономерностями тепловых флуктуаций во времени [2], а также одновременно протекающими явлениями на атомном, дислокационном, субструктурном и структурном уровнях.
Таким образом, применение только механических критериев при оценке прочности и долговечности в условиях совместного воздействия нагрузок и сред не гарантирует точности, не позволяет совершенствовать эти критерии и воздействовать на процесс повреждения.
Для выявления физико-механической сущности наиболее распространенных и все еще недостаточно изученных процессов повреждение материалов (коррозионное растрескивание, коррозионная усталость, механическая усталость и др.) большой практический и теоретический интерес представляют исследования причин повреждения материалов длительно эксплуатирующегося оборудования предприятий нефтехимпереработки. Такие исследования, кроме того, позволяют выявить наиболее значимые факторы, обусловливающие те или иные деградационные процессы, и идентифицировать параметры повреждения, характеризующие каждый процесс.
Исследование причин повреждения холодильника установки гидрирования НПЗ. В процессе эксплуатации произошел разрыв трубы холодильника типа труба в трубе в зоне сварных швов 1 и 2 (рис. 1). Наибольшие повреждения имели место в районе сварного шва 1, поэтому в дальнейшем приводятся материалы исследования, относящиеся к этой зоне.
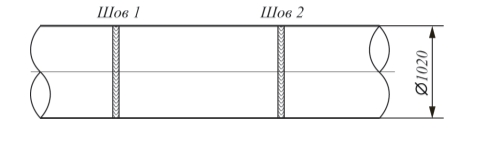
Параметры эксплуатации оборудования: давление – не более 3,2 МПа; температура на входе – не более 200°С, на выходе – 45°С; среда – керосино-газойлевая фракция. Материал трубы – сталь ЭИ 579 (20Х3МВФ) по ГОСТ 20072–74.
В зоне дефектного шва был вырезан участок трубы длиной около 800 мм для проведения дополнительных исследований (внешний осмотр, измерение твердости, металлографический и химический анализы).
Перед внешним осмотром вырезанный участок был зачищен шлифовальным кругом и протравлен «царской водкой». Установлено, что наружная поверхность подвержена сплошной язвенной коррозии глубиной ~1,5 мм.
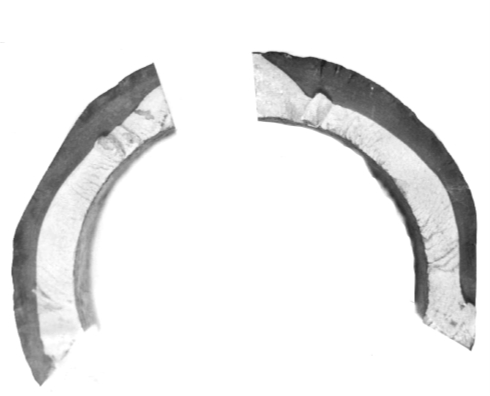
На внутренней поверхности наблюдается небольшой эрозионный износ; в околошовной зоне – нитевидная макротрещина протяженностью 2/3 периметра шва (рис. 2) максимальной глубиной до 10 мм. Зарождение трещины произошло с наружной поверхности (рис. 3).
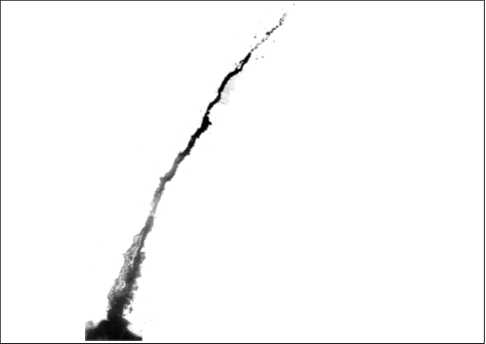
Содержание элементов, % |
|||||||||
C | Mn | Si | Cr | W | V | Mo | S | P | Ni |
Труба (Сталь 20Х3МВФ) |
|||||||||
0,20/0,20 | 0,32/0,50 | 0,25/0,37 | 2,66/2,7 | 0,56/0,8 | 0,12/0,15 | 0,53/0,7 | 0,018/0,025 | 0,027/0,03 | 0,26/– |
Сварной шов (электроды типа ХН-56) |
|||||||||
0,10/0,20 | 0,75/0,75 | 0,40/0,40 | 1,12/2,8 | –/– | 0,10/0,12 | 0,46/0,60 | 0,014/0,03 | 0,022/0,03 | 0,70/0,60 |
Примечание. В числителе приведены данные по фактическому содержанию элемента, в знаменателе – согласно МПТУ 4159 |
В ходе металлографического анализа выявлено следующее:
- металл трубы загрязнен неметаллическими включениями типа сульфидов (2,5 балла), точечных оксидов (2 балла), силикатов (1,5 балла); испытания проводили по ГОСТ 1778;
- микроструктура металла трубы – сорбитовая, сварного шва – перлитно-ферритовая, разнозернистая, в зоне термического влияния – сорбит с незначительным остаточным аустенитом;
- с наружной поверхности трубы в околошовной зоне наблюдается зародышевые коррозионные микротрещины глубиной 20 мкм (рис. 4)
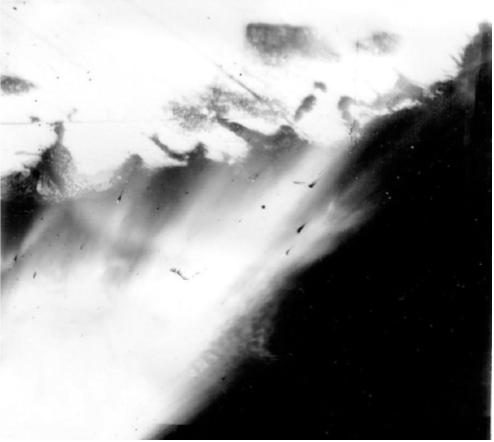
В результате химического анализа металла трубы и сварного шва был определен химический состав металлов дефектного участка (см. таблицу).
Для охлаждения гидрогенизатора использовалась оборотная вода от водоблока. Согласно данным анализа состава оборотной воды, за год до аварии в течение 1,5 месяцев наблюдалось пониженное до 5,5 значение рН (при норме 7…8,5) по причине попадания уксусной кислоты из-за пропуска трубного пучка холодильника, питаемого от того же водоблока. Химический анализ отложений на наружной поверхности трубы вывил наличие ацетат-иона (2,55%), что свидетельствует о протекании химической коррозии под действием уксусной кислоты.
Анализ всей приведенной информации позволяет сделать заключение о том, что повреждение трубы холодильника связано с коррозионной усталостью металла [3, 4].
Зарождение трещины произошло в околошовной зоне с наружной поверхности. Очагами зарождения трещины явились коррозионные микротрещины, развивавшиеся под влиянием агрессивных агентов оборотной воды в околошовной зоне с высокой твердостью (НВ 321… 388) против 270 по регламенту. Повышенная твердость свидетельствует о грубом нарушении технологии сварки (не был проведен отпуск околошовной зоны на протяжении 100 мм).
Список литературы
- Владимиров В.И. Физическая природа разрушения металлов. М.: Металлургия, 1984.
- Регель В.Р., Слуцкер А.И., Томашевский Э.Е. Кинетическая природа твердых тел. М.: Наука, 1974.
- Коррозионная стойкость оборудования химических производств. Коррозия под действием теплоносителей, хладагентов и рабочих тел. Справ. изд./ А.М. Сухотин и др./ Под ред. А.М. Сухотина. Л.: Химия, 1988.
- Охрупчивание конструкционных сталей и сплавов. Пер. с англ./ Под ред. К.Л. Брайента, С.К. Бенерджи. М.: Металлургия, 1988.