Авторы: А.Б. Жидков, Д.Е. Денисов, С.Г. Филатов, Ю.В. Малинин (ООО «Алитер-Акси»)
Опубликовано в журнале Химическая техника №11/2017
Процесс дегидрирования изобутана применяется на многих предприятиях нефтехимии для получения изобутилена, который широко используется в промышленности синтетического каучука.
Эксплуатация установок дегидрирования изобутана (УДГИБ) сопровождается частыми остановками и ремонтом (заменой) различных элементов реакторно-регенераторного блока, что приводит к длительным простоям работы, повышению эксплуатационных затрат. Несмотря на достаточно длительный период эксплуатации этих установок, только в 2007–08 годах по инициативе технических служб компании ПАО «СИБУР Холдинг» были инициированы работы по увеличению межремонтного пробега всех элементов реакторно-регенераторного блока УДГИБ.
Данная статья посвящена семилетнему опыту работы ООО «Алитер-Акси» по созданию защитных футеровок на всех основных элементах реакторно-регенераторного блока УДГИБ.
Реакторно-регенераторный блок схематично показан на рис. 1.
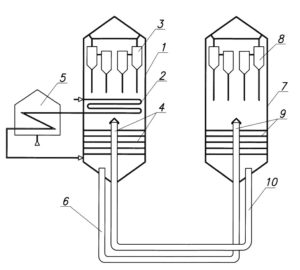
Реакция дегидрирования изобутана в изобутилен протекает в реакторе 1 при температуре 540…590 °С по следующей схеме:
Реакция протекает на пылевидном алюмохромовом катализаторе, который подается в реактор. В реакторе катализатор частично находится в кипящем слое, затем стекает по внутренним устройствам 4 реактора. Для остановки реакции дегидрирования в реактор вводится змеевик 2 с холодным сырьем, который охлаждает реакционную зону реактора. В двухступенчатых циклонах 3 реактора происходит очистка продуктов реакции, сырья от пыли катализатора. В реакторе наличие углеводородов и водорода как продукта реакции создает восстановительную среду.
Кроме основной реакции получения изобутилена, в реакторном объеме протекает еще ряд побочных реакций – дегидрирование продуктов, крекинг с образованием легких углеводородов и кокса. Образование кокса крайне негативно действует на катализатор, подавляя его активность. Закоксованный катализатор ссыпается в низ реактора и далее через переточную линию 6 попадает в регенератор 7.
Образование кокса происходит не только на поверхности катализатора, но и на внутренних стенках реактора, циклонов, внутренних устройств. При этом кокс активно образуется как на поверхности этих элементов, так и в порах металла, полузакрытых полостях, порах футеровки внутри реактора.
Регенерация катализатора проводится в регенераторе в кипящем слое. В различные части регенератора вводят воздух, азот, топливный газ для сжигания кокса, восстановления активности катализатора. Восстановленный катализатор по перетоку 10 из регенератора подается в реактор. В регенераторе процессов коксообразования не должно быть при нормальном режиме, хотя частицы кокса могут присутствовать. Среда в регенераторе слабо окислительная, в местах подачи воздуха – окислительная.
Основная проблема эксплуатации реакторно-регенераторного блока – короткий срок службы защитных покрытий стен реактора и регенератора, износ циклонов, перетоков, внутренних устройств, вплоть до образования сквозных дефектов. Срок службы между ремонтами различных элементов от полугода до четырех лет.
Факторы, воздействующие на внутренние стенки, элементы реакторно-регенераторного блока УДГИБ
Основное воздействие на внутреннюю поверхность элементов оказывают следующие факторы:
- восстановительная среда в реакторе;
- абразивное воздействие со стороны движущегося катализатора. Наиболее нагруженные участки – перетоки (особенно поворотные участки), циклоны (циклоны регенератора в несколько большей степени, так как катализатор без кокса), в меньшей степени стенки регенератора. Стенки реактора слабо подвержены абразивному износу, так как катализатор закоксованный;
- образование кокса как на поверхности внутренних элементов, так и в открытых порах, полостях всех металлоконструкций, футеровки.
Для решения проблемы стойкости в восстановительных средах футеровка не должна содержать окислов, подверженных восстановлению в данных условиях, главным образом, окислов трехвалентного железа. Этот вопрос решается просто. Несколько производителей, в том числе и ООО «Алитер-Акси», предлагают такие бетоны.
Абразивостойкость огнеупорных бетонов регулируется в широком диапазоне [1]. Имеется большой опыт работы футеровок, схем армирования в похожих условиях в установках каталитического крекинга [2]. Этот вопрос также может быть решен на профессиональном уровне.
Воздействие коксообразования на материалы (внутренние устройства из металла, футеровку) наиболее велико, изучены эти процессы не в достаточном объеме.
Найденные нами в литературе исследования [3, 4] показывают, что при активном коксообразовании на поверхности и в объеме огнеупорного бетона или изделия изменяются структура и свойства бетона: снижается пористость, увеличивается теплопроводность, модуль упругости (Юнга), коэффициент термического расширения [5]. По некоторым данным [5], давление в порах материала при отложении в них кокса достигает 5 000 МПа. Такие высокие напряжения могут привести к разрушению не только футеровки, но и металлоконструкций, при наличии в них пор после сварки или в болтовых соединениях.
Типичным механизмом разрушения футеровки циклонов и стен реактора (наблюдалось нами в установках каталитического крекинга) являются сколы, поверхностное шелушение вследствие отложения кокса в микропорах и довольно крупные отслоения, если коксообразование происходит в усадочных трещинах бетона.
Рассматривая этот вопрос, следует помнить о том, что работоспособность футеровки в равной степени зависит как от свойств применяемых огнеупорных материалов, так и от конструкции футеровки. Эти две стороны проблемы нельзя рассматривать изолированно (что часто делается). Применение вполне пригодного для эксплуатации в тех или иных условиях огнеупорного бетона не будет успешным при ошибочно выбранной конструкции футеровки.
Абразивостойкие огнеупорные бетоны
Анализ приведенных далее результатов работ невозможен без понимания различий между двумя основными типами абразивостойких бетонов. Это – классические бетоны с высоким содержанием цемента и низкоцементные бетоны.
Бетоны с высоким содержанием цемента (серия АЛКОР производства ООО «Алитер-Акси») изготавливаются на основе алюмосиликатных заполнителей и алюминаткальциевых цементов. Содержание цемента – 15–30%. После затворения водой эти бетоны твердеют вследствие гидратации алюминатов кальция, входящих в состав цемента, и образуют материал высокой прочности. При нагревании гидраты разлагаются, вода покидает бетон, образуя поры, структура бетона разрыхляется, прочность падает.
Низкоцементные бетоны производятся ООО «Алитер-Акси» в вариантах для заливки (серия АЛИКАСТ), ручной набивки (АЛИРАМ), торкретирования из пушки (АЛИГАН). Эти бетоны содержат 5–10% цемента, поэтому они лишены этих недостатков. Их состав сложен и сбалансирован: кроме зернистых заполнителей и цемента они содержат ультрадисперсные порошки, дефлокулянты, регуляторы механизма и скорости схватывания и твердения. Если для приготовления бетонов с высоким содержанием цемента в смесь необходимо добавить 9–15% воды, то для низкоцементных смесей, как правило, достаточно 4–7%.
Исходная прочность этих бетонов часто ниже, чем у бетонов с высоким содержанием цемента, однако они существенно упрочняются уже при низкотемпературной сушке, а при температуре около 500…600°С начинает образовываться керамическая связь. Они характеризуются высокой плотностью, прочностью, термостойкостью, химической стойкостью. При использовании этих бетонов в футеровке УДГИБ их чрезвычайно важными достоинствами являются низкая пористость (с преобладанием очень мелких пор размером менее 20 мкм) и высокая абразивостойкость, в несколько раз превосходящая абразивостойкость обычных бетонов с высоким содержанием цемента [1, 2]. Забегая вперед, отметим, что, по нашему мнению, только низкоцементные бетоны должны применяться в рабочем слое футеровок УДГИБ, по крайней мере на тех участках, где существует опасность коксования.
Футеровка реакторно-регенераторного блока
По аналогии с установками каталитического крекинга [2] нами проведено разделение реакторно-регенераторного блока по воздействию реакционной среды на различные участки. На рис. 2 показана схема реакторно-регенераторного блока с выделением цветом этих участков.
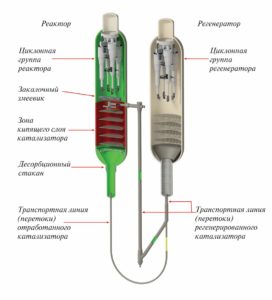
Футеровка реактора
Реактор дегидрирования изобутана представляет собой вертикальный аппарат, состоящий из распределительной решетки, провальных тарелок, «закалочного» змеевика и циклонов.
Согласно первым проектам, защиту стен реактора от повышенных температур, абразивного износа, коксообразования, химических воздействий выполняли следующим образом.
Внутри реактора выполняли внутреннюю дополнительную обечайку. Пространство между обечайкой и стенкой заполняли огнеупорными материалами, часто неконтролируемого состава и качества. В объеме этого материала активно образовывался кокс, который деформировал, выпирал листы внутренней обечайки, ломая внутренние устройства реактора. Эти воздействия требовали частых остановок работы установки (каждые 4–6 мес.), выжига кокса, ремонта защиты стен реактора, внутренних устройств.
За последние годы на пяти реакторах УДГИБ были реализованы проекты замены внутреннего защитного кожуха реактора на футеровку из огнеупорных бетонов. При этом на некоторых реакторах работы выполнялись несколько раз, использовались различные бетоны для рабочего слоя, различные материалы для теплоизоляционного слоя.
Для стен реактора применялись две конструкции футеровки:
- первый вариант – двухслойная с теплоизоляционным слоем из легковесного бетона АЛАКС-0.6-1000А толщиной 130…150 мм и рабочий слой из плотного абразивостойкого бетона АЛИРАМ-72Р на основе плотных шамотов, корундов по панцирной (шестигранной) сетке толщиной 25…30 мм;
- второй вариант – двухслойная футеровка с теплоизоляционным слоем на основе легковесного бетона АЛАКС-0.6-1000Т или волокнистой изоляции, рабочий слой из плотного бетона АЛКОР-45АТ на основе шамотов, бокситов, корундов. Толщина слоев бетона примерно одинаковая (70…80 мм каждый). Бетон армировали V-образными анкерами.
Практически все футеровки после года эксплуатации имели разрушения различной степени по высоте реактора.
В наибольшей степени разрушается футеровка в зоне закалочного змеевика. При этом именно в этой зоне реактора наблюдается интенсивное кипение катализатора, образование кокса. В этой зоне наблюдалось частичное отслаивание панцирной сетки, полное или частичное разрушение бетонов в ячейках панцирной сетки.
При использовании двухслойной футеровки без панцирной сетки эта зона также наиболее сильно разрушается. Типичные фотографии разрушения футеровки этой зоны показаны на рис. 3 и 4.
|
|
В зоне закалочного змеевика и выше футеровка стен реактора, выполненная по обеим приведенным выше схемам, работает нормально в течение трех и более лет.
Еще более надежно работает футеровка в зоне десорбционного стакана. Здесь не наблюдается серьезных разрушений.
По нашему мнению, причина разрушения футеровки в зоне кипящего слоя катализатора – активное образование кокса в порах бетона, в полостях между бетоном и ячейками панцирной сетки. При этом на режиме работы установки эта футеровка может сохранять свои свойства, оставаясь монолитной. Перед остановкой установки, на этапе коксовыжига, температура поднимается, идет расширение кокса с сопутствующим удалением большого количества газов, продуктов горения кокса, и футеровка разрушается.
Следов высокого абразивного износа бетона в реакторе мы не наблюдали. Катализатор здесь частично покрыт коксом, что значительно снижает абразивную нагрузку на футеровку.
Для повышения стойкости бетонов в средах с активным коксообразованием необходимо использовать бетоны с минимальной открытой пористостью, подбирать зерновой состав наполнителя для получения максимально плотного бетона.
Для определения наиболее стойких бетонов в зоне кипящего слоя катализатора в ООО «Алитер-Акси» изготавливались кубики бетонов, которые помещали в реактор. После полугода эксплуатации реактора кубики вынимали и испытывали на прочность. Один из протоколов испытаний приведен на рис. 5.
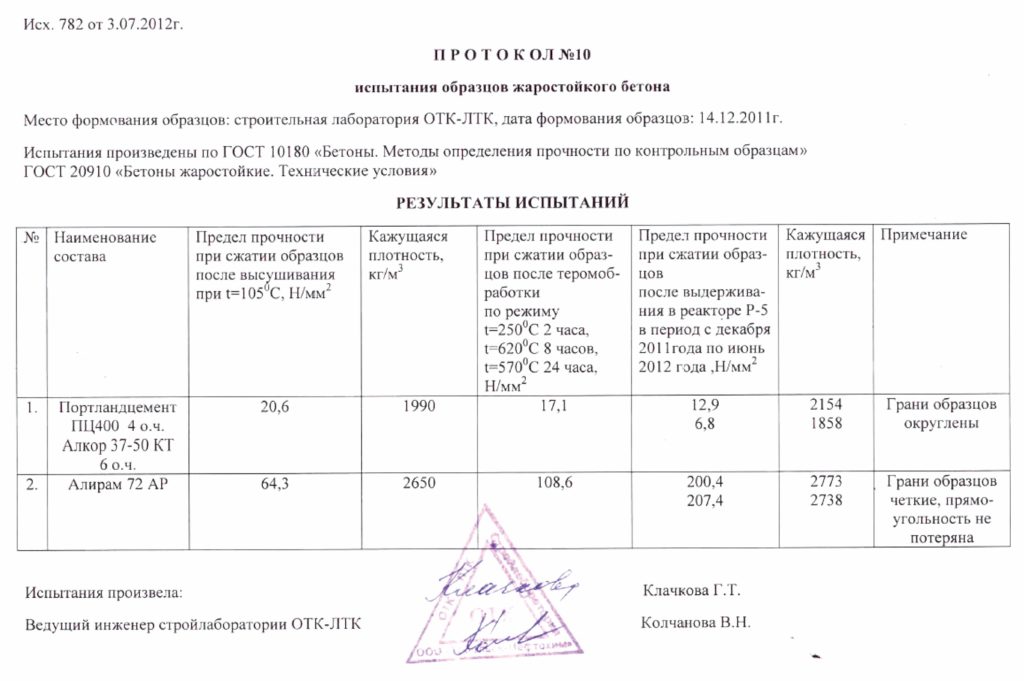
Испытания показали, что наилучшими результатами по сохранению свойств (прочность, плотность, сохранение геометрии) обладают низкоцементные смеси, имеющие высокую прочность, низкую пористость [1].
На основании этих работ мы сегодня можем рекомендовать для футеровки реакторов УДГИБ двухслойную футеровку без панцирной сетки с армированием V-образными анкерами. Такая футеровка имеет большую газоплотность, так как в ней отсутствуют микрозазоры на границах сетка–бетон и сетка–сетка. В качестве бетонов рабочего слоя необходимо использовать низкоцементные или ультранизкоцементные бетоны с беспористыми заполнителями (корунд, плотный шамот, муллит). Наиболее хорошо показали себя бетоны производства ООО «Алитер-Акси» – АЛИГАН 50/2,5 и АЛИКАСТ 50/2,3.
При хорошем качестве выполнения работ можно гарантировать межремонтный пробег в течение 1 года при условии не более двух остановок в год. Дальнейшие работы должны увеличить межремонтный пробег.
Циклоны и внутренние устройства реактора
Поверхности внутренних устройств реактора также подвержены активному коксообразованию. Особенно это касается провальных тарелок, коллектора (распределителя) подачи сырья в зону кипящего слоя. Попытки защитить эти элементы футеровкой, нанесенной по S-образным анкерам, показали неэффективность этого технического решения. Футеровка и S-образные анкеры отрывались за короткий период эксплуатации.
Мы изготавливали футерованные циклоны для четырех УДГИБ. Футеровка на основе абразивостойкой смеси наносилась по панцирной сетке, приваренной к поверхности циклона. При этом использовали как смеси своего производства АЛИРАМ-72АР, так и одну из самых абразивостойких смесей импортного производства АСТНТЕМ-85.
Несмотря на то, что циклоны реактора находятся в зоне выше закалочного змеевика (в этой зоне футеровка стен реактора работает нормально), футеровка в циклонах служит значительно меньше футеровки стен реактора. По нашему мнению, это связано со значительно более высокой концентрацией катализатора в циклонах по сравнению с общим объемом реактора. По-видимому, реакции образования кокса продолжаются в циклонах, разрушая футеровку.
На установке БК-2 ООО «Тобольск-Нефтехим» менее чем за год эксплуатации произошел отрыв панцирной сетки. На рис. 6 видно, что отрыв произошел не только по сварным швам, но и, местами, по самому «телу» панцирной сетки, что говорит о чрезвычайно высоких распорных усилиях. Авторы не видят иных причин для возникновения столь значительных напряжений, кроме образования кокса и возникновения огромных внутренних напряжений внутри металла.[/vc_column_text][/vc_column][/vc_row]
На аналогичной установке ИФ-2 ООО «Тобольск-Нефтехим» изготовленные ООО «Алитер-Акси» циклоны в 2015 г. работают и в настоящее время. Осмотр в период остановки потребовал незначительного ремонта.
Другие работы ООО «Алитер-Акси» по циклонам (ООО «Тольяттикаучук», ОАО «Уралоргсинтез») показали, что футерованные циклоны в реакторе могут работать три года и более при надлежащем качестве изготовления. Разрушение металла в циклонных группах, по-видимому, связано с технологическим нарушением режима работы реактора.
Различие срока службы циклонов реактора на различных УДГИБ связано, по нашему мнению, с различием в технологических режимах установок в части загрузки циклонов катализатором. Чем меньше катализатора проходит через циклоны в единицу времени, тем меньше его концентрация в циклонах, тем больше срок службы. Следует также обратить внимание, что разрывы металла в реакторах наблюдаются не на всех УДГИБ.
Таким образом, по нашему мнению, крайне желательно, чтобы кипящий слой катализатора не поднимался выше закалочного змеевика, а поток катализатора, поднимающегося до циклонов, был минимален. Это обеспечит более длительную, надежную работу циклонов, внутренних устройств верхней части реактора.
Краткий итог этого раздела – для участков с активным воздействием химических реакций образования кокса (весь реактор, перетоки из реактора в регенератор) достаточно обоснованным представляется следующий подход:
- в рабочем слое должны применяться только низкоцементные бетоны АЛИКАСТ (заливка), АЛИГАН (торкретирование), АЛИРАМ (ручная набивка);
- армирование однослойных или двухслойных футеровок толщиной 100 мм и более следует выполнять V-образными анкерами без применения панцирной сетки;
- армирование тонкослойных абразивостойких футеровок циклонов реактора следует выполнять S-образными анкерами без применения панцирной сетки.
Этот подход обеспечит повышение срока службы футеровки реактора, но оптимизация технологического режима работы установки и проведения процесса в реакторе с целью уменьшения интенсивности образования кокса также крайне необходимо для обеспечения длительной работы УДГИБ.
Футеровка регенератора, циклонов регенератора
Как уже отмечалось во введении к данной работе, в регенераторе идет удаление кокса, т.е. среда слабоокислительная, процессов коксообразования нет. Катализатор очищается от кокса, грани зерна окиси алюминия – очень сильный абразив. Абразивное воздействие при температурах до 650°С хорошо изучено [2].
На циклонах регенератора мы применяем абразивостойкую смесь собственного производства АЛИРАМ-72АР. Срок службы циклонов – пять и более лет. При ремонтах на циклонах наблюдаются следы сильного абразивного износа.
Работы по замене футеровки стен регенератора нами не выполнялись. Существующее решение – внутренний защитный кожух и засыпка огнеупорного материала между стенкой регенератора и защитным кожухом – работает хорошо. При необходимости эту работу можно выполнить, заменив существующие конструкции однослойной футеровкой из бетона средней плотности АЛАКС-1.4-1300 толщиной 120…140 мм. Эта футеровка будет работать надежно длительный период – 10 и более лет.
Перетоки (транспортные линии) отработанного и регенерированного катализатора
В перетоках отработанного катализатора (из реактора в регенератор) движется плотный поток закоксованного катализатора и остатки сырья из реактора. Процессы коксообразования на поверхности стен и в объеме футеровки продолжаются в разной степени активности.
На основе опыта и анализа работы УДГИБ, обсуждения задач с заказчиками были реализованы два варианта футеровок:
- однослойная по V-образным анкерам с применением бетона АЛИКАСТ 37\2,5 толщиной 125 мм;
- однослойная по панцирной сетке с применением бетона АЛИРАМ-72АР толщиной 25 мм.
На трех УДГИБ перетоки работают успешно, некоторые уже более трех лет. При этом лучше работает футеровка относительной большой толщины без применения панцирной сетки, армированная V-образными анкерами.
В ООО «Тольяттикаучук» перетоки с футеровкой по панцирной сетке признаны неудачными. Происходит отрыв панцирной сетки и потеря футеровки. Связано это, по-видимому, как с конструкцией футеровки, так и с различным режимом работы установок, различными катализаторами и их активностью. Возможно, имеются различия в количестве сырья, которое захватывается катализатором из реактора в переток.
Несмотря на успех трех наших работ, необходимо отметить, что этот участок проблемный, и необходимы дальнейшие работы по разработке более плотной беспористой футеровки, которая обеспечит значительное увеличение межремонтного пробега этих элементов.
На линиях регенерированного катализатора ситуация намного лучше. В настоящее время эти линии служат три и более года. Процессов образования кокса здесь нет, наблюдается сильный эрозионный износ, как и на циклонах регенераторов, но защиту от эрозии наши бетоны обеспечивают на пять и более лет.
Общие выводы по работе футеровок внутренних устройств и корпусов реакторно-регенераторного блока УДГИБ
Использование футеровки для защиты стенок реактора, перетоков (транспортных линий) отработанного катализатора, защиты циклонов позволяет в большинстве случаев обеспечить межремонтный пробег от одного года до пяти лет.
По воздействию реакционной среды на различные элементы реакторно-регенераторного блока можно выделить следующие зоны.
Реактор:
- зона кипящего слоя – зона наиболее активного коксообразования, воздействия химических реакций образования кокса на стены реактора, внутренние устройства, находящиеся в этой зоне;
- зона выше закалочного змеевика – зона снижения скорости химических реакций, удовлетворительной работы футеровки;
- циклоны реактора – зона активного коксообразования, умеренной нагрузки на футеровку;
- десорбционный стакан – зона снижения скорости химических реакций, удовлетворительной работы футеровки.
Транспортная линия (переток) отработанного катализатора – зона достаточно активных реакций образования кокса, воздействия на футеровку.
Регенератор, циклоны регенератора – зона повышенного абразивного износа. Процессов коксообразования нет. Проблемы защиты от абразивного износа решаются на хорошем уровне;
Транспортная линия (переток) регенерированного катализатора – зона повышенного абразивного износа. Проблемы защиты от абразивного износа решается на хорошем уровне.
Для повышения срока службы элементов с активным воздействием химических реакций образования кокса (зона кипящего слоя катализатора в реакторе, циклоны реактора, перетоки из реактора в регенератор) необходимы дальнейшие работы по применению максимально плотных беспористых низкоцементных бетонов с минимальной системой армирования (без панцирной сетки) на стенах и внутренних устройствах реакторов.
Процессы коксообразования во многих случаях приводят к разрыву внутренних металлоконструкций по сварным швам. Для обеспечения работы металлоконструкций внутри реактора необходимо повысить требования к сварке (по полному отсутствию пор).
В регенераторе, транспортных линиях регенерированного катализатора разработанная ООО «Алитер-Акси» футеровка эффективно работает три и более года.
Наблюдаются различия в службе футеровки одних и тех же элементов (циклоны, перетоки реактора) на различных УДГИБ. Необходим анализ технологического режима работы установок.
Список литературы
- 1. Денисов Д.Е., Жидков А.Б., Власов В.В. Абразивостойкие бетоны и футеровки//Промышленная энергетика. 2005. №8. С. 11–16.
- 2.Жидков А.Б., Власов В.В., Денисов Д.Е. Опыт изготовления и эксплуатации абразивостойких элементов установок каталитического крекинга//Химическое и нефтегазовое машиностроение. 2003. №2. С. 15–17.
- 3.M.S. Crowley, C.A. Schacht. A comparison of the thermo-mechanical properties of «as installed» vs «coke filled» refractories for FCCU//UNITECR-1997. Р. 1643–1652.
- 4.L.R.M. Bittencourt, M.R. Fernandes, S.L. Caralda da Silva. The effect of coke deposition on the mechanical and thermomechanical properties of dense and insulating castable used in FCCU//UNITECR-2003.
- 5.P. Tassot, E. Bachman, R.C. Johnson. The influence of reducing atmospheres on monolithic refractory linings for petrochemical service//UNITECR-2001.
[/mpc_textblock]