Автор: С.В. Афанасьев (ОАО «Тольяттиазот»), С.П. Сергеев (ОАО «ГИАП»).
Опубликовано в журнале Химическая техника №8/2015
Центробежнолитые трубы из жаропрочных сталей и сплавов находят широкое применение во многих отраслях техники. Это – радиационные трубы в термических печах с защитной атмосферой, подовые ролики в проходных термических и нагревательных печах металлургических заводов, ролики в агрегатах непрерывного отжига и др.
В настоящее время для этих целей используют стали типа Х25Н20 и сплавы типа Х25Н35, Х26Н33, Х28Н49 с повышенным содержанием углерода и дополнительным легированием кремнием, ниобием и в ряде случаев молибденом, вольфрамом, кобальтом.
Вопрос о возможности повышения рабочих параметров процесса высокотемпературной конверсии природного газа на агрегатах аммиака и метанола является весьма важным, поскольку повышение температуры и давления не только увеличивает производительность установок, но и снижает себестоимость продукта, позволяет получить водород более высокой степени чистоты.
В связи с изложенным в последнее время ведется работа по совершенствованию составов используемых сталей типа Х25Н35С2 путем их дополнительного легирования.
В случае высокоуглеродистого аустенитного сплава, состоящего из 25% мас. хрома, 35% мас. Ni достигается максимальное значение прочности на разрыв, а добавление 1% мас. Nb существенно улучшает сопротивление ползучести. Ввод минимального количества титана и циркония способствует дополнительному улучшению длительной прочности. В присутствии указанных добавок, особенно при наличии редкоземельных металлов, улучшаются такие характеристики сталей, как сопротивление окислению и науглероживанию при повышенных температурах, а повышенное содержание хрома обеспечивает необходимую коррозийную стойкость.
С целью повышения надежности работы реакционных труб, являющихся одним из самых ответственных и самых металлоемких элементов в установках конверсии углеводородов, был предложен новый базовый сплав на железоникелевой основе типа ХН33БС, легированный микродобавками [1, 2]. Он включает хром, никель, ниобий, церий, кремний, марганец, ванадий, титан, алюминий, вольфрам и железо при обязательном соблюдении двух дополнительных условий: %Ni + 32%С + 0,6%M
n +%Cu = 40,08 – 46,870%; %Cr + 3%Ti + %V + %Mo + 1,6%Si + + 0,6%Nb = 21,322 – 26,39% .
Заявляемый сплав является чисто аустенитным, так как его структура сохраняется при нагревании. Он не упрочняется термообработкой, т.е. не склонен к дисперсионному твердению, выплавляется только в индукционных печах с основной футеровкой и использованием преимущественно чистых шихтовых материалов. Специфика плавления металла в индукционных печах за счет использования высокочастотного способа нагрева обеспечивает хорошее диспергирование компонентов сплава в процессе выплавки, а также позволяет получать сплав с низким содержанием газов и избежать науглероживания, как это происходит в электродуговой печи [3].
Указанный сплав относится к строго литейным и для него не требуется дополнительных мер по ограничению содержания вредных примесей, таких, как сера и фосфор.
В указанных количествах они позитивно влияют на обрабатываемость сплава резанием.
Расширенные испытания изделий из нового жаропрочного сплава были выполнены во ФГУП ЦНИИчермет.
Среднюю величину зерна определяли в окуляре металлографического микроскопа на матовом стекле (ГОСТ 5639. Сталь. Методы выявления и определения величины зерна). Экспериментально установлено, что средняя величина зерна у заявляемого сплава составляет 250 мкм, что несколько больше, чем у сплава-прототипа (215 мкм).
Однородность структуры оценивали с помощью коэффициента неоднородности
А = Rmax/Rmin, где Rmax, Rmin – соответственно максимальный и минимальный линейный размер зерен в структуре сплава.
В известном сплаве-прототипе А = 1,13… 1,17, а для заявляемого сплава А = 1,08…1,12, что свидетельствует о более высокой однородности его структуры.
Испытания на длительную прочность были проведены при температуре 960°С на образцах типа ДП-5 с рабочей частью диаметром 5 мм, длиной 25 мм с прямым нагружением образцов в соответствии с ГОСТ 10145. На основе полученных данных был построен график зависимости времени до разрушения от уровня растягивающих механических напряжений.
Установлено, что испытанные образцы после разрыва слабо окислены, удлинение и уменьшение площади поперечного сечения равны нулю. Значение предела длительной прочности нового сплава при температуре 960°С за 100 000 ч, полученное методом экстраполяции, составляет 17,4 Н/мм2, что на 26% выше данных по жаропрочности сплава 45Х25Н35ВС.
Высокий уровень механических свойств сплава был подтвержден при температурах 20 и 960°С на образцах с рабочей частью диаметром 5 мм, длиной 25мм по ГОСТ 9651 (табл. 1). Это позволяет уменьшить толщину стенок реакционных труб и улучшить тем самым их теплофизические свойства.
Таблица 1
Механические свойства сплава ХН33БС
Температура испытания, °С | sв, Н/мм2 | s0,2, Н/мм2 | d, % | y,% |
20 | 480…580 | 240…300 | 9,9…14,3 | 8,5…13,8 |
960 | 110…128 | 105…119 | 18,0…21,5 | 29,0…39,0 |
Металлографическое исследование сплава, проведенное на образцах, вырезанных из темплетов центробежнолитых труб, взятых от различных плавок, показало сходную структуру: наличие равноосных зерен твердого раствора Fe-Cr-Ni и фаз нескольких видов. В наибольшем количестве присутствует эвтектическая фаза, содержащая карбид типа Cr7C3 и имеющая пластинчатое строение.
Измерение температур солидуса (конец кристаллизации) и ликвидуса сплава выполнено методом ДТА на образцах массой 1,8 г с применением образца сравнения (эталона) из молибдена, используемого для калибровки прибора (рис. 1).
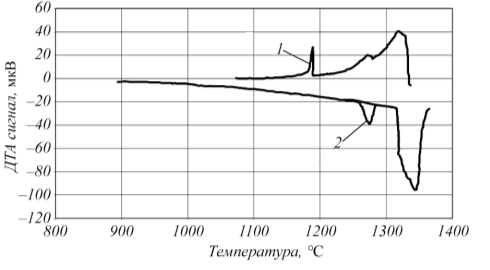
1 – линия солидус, 2 – линия ликвидус
Из анализа кривой определены температуры фазовых превращений сплава. Результаты представлены в табл. 2.
Таблица 2
Результаты определения температур фазовых превращений (выполнено во ФГУП ЦНИИчермет под руководством А.Ф. Шевакина)
Температура, характеризующая изменение фазового состояния, °C | Температуры фазового превращения сплава | |
При нагревании | При охлаждении | |
Температура солидуса ТS | 1 313 | – |
Температура ликвидуса ТL | 1 343 | 1 332 |
Температура | ||
кристаллизации эвтектики Тэвт | – | 1 276 |
Температура растворения | ||
карбидов ниобия Тэвт | 1 250 | 1 189 |
Параметры удельной теплоемкости приведены в виде температурной зависимости измеренных значений удельной теплоемкости (рис. 2). Они достаточно хорошо коррелируют с расчетными значениями, найденными с использованием формулы, имеющей общий вид для аустенитных сплавов разного состава. Наряду с рассмотренным базовым сплавом созданы низкоуглеродистый и высокоуглеродистый хромоникелевые сплавы аустенитной структуры, что позволило изготавливать полный ассортимент комплектующих изделий для печей риформинга [4, 5]. Эти сплавы запатентованы [3 –6].
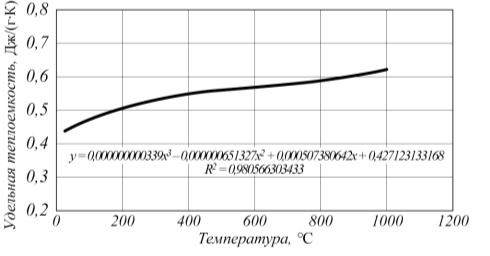
Благодаря выполненным разработкам в ОАО «Тольяттиазот» организован промышленный выпуск реакционных труб с меньшей толщиной стенок и большим внутренним диаметром. Их внедрение на агрегатах аммиака типа АМ-76 и Кемико повысило производительность печей риформинга более чем на 30% и существенно снизило расходные нормы по природному газу [7].
Список литературы
- Афанасьев С.В, Рощенко О.С. Структура и физические свойства жаропрочного сплава для центробежнолитых труб//Сборник конкурсных докладов VI Всеросс. Молодеж. Науч. Конф. «Микромеханизмы пластичности, разрушения и сопутствующих явлений» и V Междунар. школы «Физическое материаловедение». (Тольятти, 26 сентября – 1 октября 2011 г.). 2011. С. 246–249.
- Патент РФ на полезную модель RU №85844. МПК B22D 13/04. Установка центробежного литья жаропрочных труб.
- Патент РФ RU №2393260. МПК C22C 30/00, C22C 38/50. Жаропрочный сплав.
- Патент РФ RU №2446223. МПК С22С 30/00, С22С 38/00, С 22С 19/05.Жаропрочный хромоникелевый сплав с аустенитной структурой.
- Патент РФ RU №2485200 России. МПК C22C 30/00, C22C 38/50. Жаропрочный хромоникелевый сплав с аустенитной структурой.
- Патент РФ RU №2533072 России. МПК C22C 30/00, C22C 38/50. Жаропрочный сплав.
- Патент РФ RU №2355826 России. МПКС01В 3/38, В01J 23/55. Способ получения синтез-газа путем паровой конверсии углеводородов.