Автор: А.В. Буканин (ООО «Арсенал Групп»).
Опубликовано в журнале Химическая техника №6/2014
Про повышение эффективности в промышленности РФ, в том числе в нефтепереработке, нефте-и газохимии, в СМИ сказано немало. Тема модернизаций, реконструкций или технического перевооружения печей РФ стоит особняком. Довольно долго ее не обсуждали в силу разных причин. Теперь положение может измениться в лучшую сторону и для этого есть основания. Как ни странно, но в очередной раз проблему повышения эффективности в нефтепереработке, нефте-и газохимии поднимает правительство РФ.
На прошедшем 26 мая 2014 г. экономическом форуме в Санкт-Петербурге Кремль представил план технологической революции; шестым шагом этого плана предусмотрена разработка механизма поддержки компаний, применяющих в работе наилучшие доступные экологически чистые технологии. Производство оборудования, соответствующего принципам наилучших доступных технологий, будет локализовано, для этого будут созданы условия (из выступления Президента РФ В.В. Путина). Для компаний, работающих на старом оборудовании и применяющих устаревшие технологии, будут введены санкции в виде дополнительной налоговой нагрузки.
Проводником идей Кремля будет Минприроды – ведомство, ранее предлагавшее увеличить в несколько раз ставки экологических платежей, которые заставили бы модернизировать производство.
Зачем нужно заниматься повышением эффективности работы печей?
Технологические печи в нефтепереработке, нефте-и газохимии, как правило, стоят в «голове» сложного технологического процесса и в большинстве случаев являются основными центрами энергозатрат производства наряду с компрессорами и системами ректификации.
Печи и паровые котлы – главные потребители топлива, доля топливного газа для различных технологических процессов составляет 15–40% всех энергозатрат предприятия.
Снижение доли затрат топливной составляющей в себестоимости повышает конкурентоспособность продукции. Прогноз роста тарифов на энергоресурсы (рис. 1) является очевидным стимулом к повышению эффективности и энергосбережению.
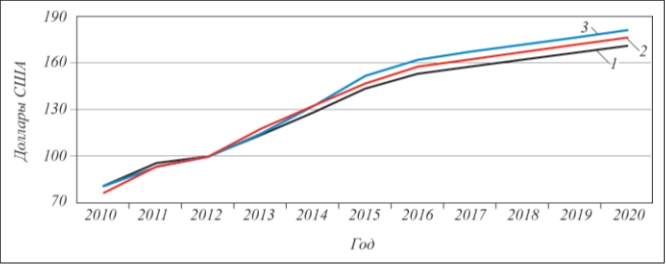
Существующие длительный срок низкие тарифы на газ, в том числе топливный, тормозят активное техническое перевооружение старых технологических печей. Вопросы выбросов и экологии печей по-прежнему не в приоритете в производственных программах предприятий. Всего этого нет в развитых промышленных странах, где и за газ, и за экологию нужно платить высокую цену, поэтому и вопросами повышения эффективности, в том числе и печей, там занимаются уже давно и серьезно.
Доля печей-долгожителей со сроком эксплуатации 25–35 лет на Западе ничтожно мала, старые печи либо давно законсервированы и демонтированы, либо проданы под грифом «secondhand » в страны с менее развитой экономикой. В России, к великому сожалению, доля «возрастных» печей очень велика и составляет 80–90% всего эксплуатируемого парка печей.
Для того, чтобы построить новую современную эффективную печь, нужны немалые инвестиции, срок окупаемости такой печи при существующих низких тарифах на топливо составляет не менее 10 лет. Вот и получается, что бизнесу по-прежнему выгодно эксплуатировать старые неэффективные печи. Однако все может измениться уже в недалекой перспективе, когда будут введены новые повышенные штрафы за экологию, санкции в виде дополнительной налоговой нагрузки, высокие тарифы на газ. Правительство РФ методом кнута и пряника заставит компании и отдельные предприятия повернуться в сторону реконструкции и к строительству новых печей.
Какие печи эксплуатирует современная Россия?
Наша страна эксплуатирует более 700 печей в производствах средней и крупной мощности в нефтепереработке, нефте-и газохимии.
В компании «СИБУР» эксплуатируется 125 печей, эта компания является лидером по этому показателю в РФ. Основная масса печей РФ была построена в годы развитого социализма по проектам 70-х–80-х годов двадцатого века.
В современной России новым строительством энергоэффективных печей в большей мере занимаются компании нефтегазового комплекса: ЛУКОЙЛ, РОСНЕФТЬ, Газпромнефть, Нижнекамскнефтехим и ряд других.
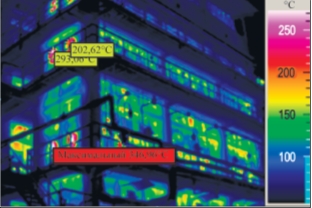
В России доля эффективных печей от лучших мировых производителей – не более 10%. Отставание старых печей в РФ от мирового уровня в отношении эффективности работы составляет 10–35% в разных технологиях.
Фактическое состояние «старых» неэффективных печей РФ
Почему происходит снижение КПД печи с увеличением срока эксплуатации? В этом разделе мы не будем комментировать проекты и работу новых эффективных печей от лучших мировых производителей (этой теме нужно посвятить отдельную статью), а дадим анализ только старым неэффективным печам РФ. Известно, что при базовом проектировании КПД печи не может быть выше 92%. Причинами этого являются потери теплоты в атмосферу через стенку печи – до 2% (температура наружной поверхности стенки 55…60°С) и потери теплоты с уходящими в атмосферу дымовыми газами (продукты сгорания топлива), достигающими 6–10% (температура выбросов дымовых газов 110…300°С) в зависимости от степени утилизации теплоты в зоне конвекции печи. По опыту длительной эксплуатации старых печей (более 20 лет) установлено, что КПД меняется в сторону его снижения. Причин снижения КПД печей, как это ни странно, несколько. Они могут быть вызваны следующими факторами.
Эксплуатация старой футеровки. Снижение КПД на 2–10% (рис. 2, 3).
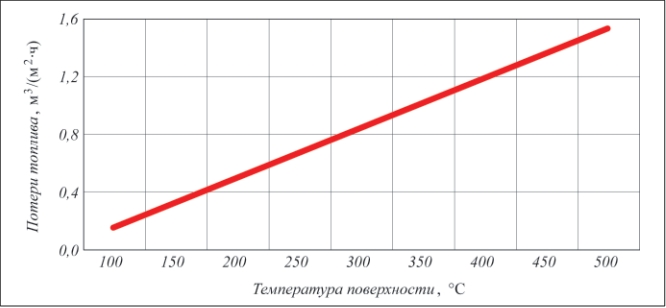
В процессе длительной эксплуатации старой кирпичной огнеупорной футеровки в зоне радиации печи и тяжелых марок бетона, в зоне конвекции происходит ее растрескивание и разрушение. Горячие дымовые газы через дефекты в футеровке контактируют с наружной стенкой печи, температура которой поднимается от проектных значений 55…60°С до 150…300°С. Постоянный мониторинг температуры стенки печи при помощи тепловизора помогает определить фактические потери топлива и отследить ежегодное снижение КПД печи от проектного показателя.
В отдельных случаях потери топлива в печи могут достигать 10%. Реализация инвестиционных проектов по замене старой футеровки новой с применением современных эффективных огнеупорных материалов со сроком окупаемости 3–7 лет (в зависимости от фактического состояния футеровки печи и связанных с этим потерь топлива) является логичным шагом в техническом перевооружении печи.
Снижение степени утилизации тепла дымовых газов (снижение КПД до 3%). В процессе эксплуатации печи происходит загрязнение оребрения поверхности змеевиков, расположенных в зоне конвекции печи продуктами разрушения огнеупорной футеровки, сажей от химического недожога топлива на горелках.
В ряде случаев производится отключение отдельных трубок змеевиков вследствие выявленных дефектов (брак при изготовлении, водородная коррозия, перегрев труб змеевиков при пусках и остановах, низкая квалификация персонала и т.п.). Постоянный мониторинг температуры дымовых газов на выходе из зоны конвекции печи при помощи АСУТП, РСУ позволяет определить потери топлива и отследить снижение КПД печи от проектного показателя. Увеличение температуры дымовых газов на 20…25°С от проектного значения снижает КПД печи на 1%. В отдельных случаях, когда загрязнения змеевиков очень велики, потери топлива в печи могут достигать 3–5%.
Можно привести отдельные лучшие практики эксплуатации печей крупнотоннажных агрегатов аммиака ТЕС, ГИАП, CLE, когда удалось поднять КПД печей на 1–2% за счет установки в зону конвекции двух змеевиков природного (сырьевого) газа (рис. 4). Температура дымовых газов с проектных 250°С была снижена до 210…220°С.
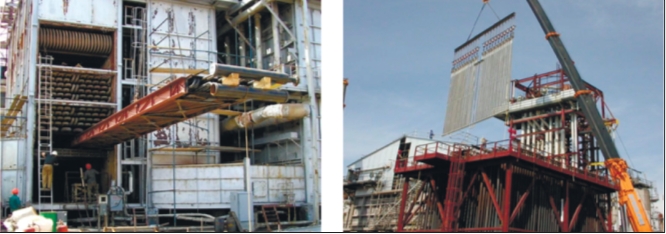
Некоторым предприятиям стоит подумать над проблемой повышения степени утилизации теплоты дымовых газов, установкой дополнительного теплообменного оборудования или увеличением площади поверхности теплообмена старых змеевиков за счет нанесения оребрения. Это может реально поднять КПД печи на 1–2% и снизить потребление топлива. В качестве организационного, низкозатратного мероприятия можно порекомендовать ежегодно инспектировать состояние чистоты поверхностей трубных змеевиков зоны конвекции и при необходимости производить очистку оребрения.
Эксплуатация старых инжекционных горелок (снижение КПД печи на 3–5%). Уровень проектирования и изготовления газовых инжекционных горелок как зарубежных, так и отечественных, в 60-х–80-х годах двадцатого века (именно о них идет речь в этой статье) соответствует уровню горелок первого поколения.
Низкие тарифы на газ, существующие в то время в мире и в СССР, отсутствие жестких норм в экологии печей были фактом. После громкого энергетического кризиса страны
Запада получили новые цены на газ и новые экологические требования к эксплуатации печей, но все это не задело СССР.
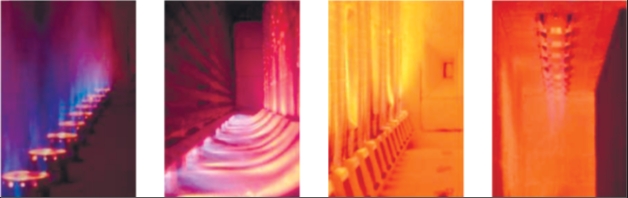
а – круглое пламя; б – плоское пламя; в – плоское пламя (пиролиз этилена);
г – направленное вниз пламя (паровой риформинг аммиака, метанола, водорода)
Сегодня в мире появилась большая линейка газовых инжекционных горелок для печей уже третьего поколения (рис. 5). Мировым лидером продаж горелок вот уже не одно десятилетие остается компания John Zink, которая трансформировалась в 2012 г. и теперь называется John Zink Hamworthy Combustion.
Неэффективное использование топлива старыми инжекционными горелками характеризуется следующим:
- работой при повышенном давлении газа с увеличенным факелом (возможен «отрыв» пламени) на уже достигнутых мощностях;
- химическим «недожогом» топлива и, как следствие, перерасходом топлива при эксплуатации печи;
- высокой эмиссией NОx, необходимостью очистки дымовых газов от NOx;
- конструктивным отсутствием запаса в регулировании первичного и вторичного воздуха регистрами горелок.
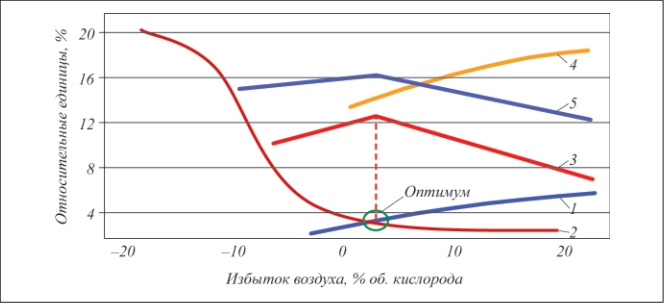
1 – содержание О2 в дымовых газах; 2 – кривая потерь топлива по показателям СО+СН4; 3 – содержание СО2; 4 – содержание NOx; 5 – линия эффективности сжигания топлива
Это обусловливает невозможность достижения новой увеличенной мощности печи и технологии в целом на старых инжекционных горелках.
Преимущества новых эффективных инжекционных горелок в нефтепереработке, нефтеи газохимии:
- повышенная до 5–10% мощность новых инжекционных горелок;
- улучшенная конструкция шиберов подачи первичного и вторичного воздуха, полное сжигание топлива;
- низкая эмиссия NОx, отсутствует необходимость в очистке дымовых газов;
- пороговые значения выбросов СО или их полное отсутствие в дымовых газах;
- улучшенное распределение топлива в форсунке горелки, формирование устойчивого факела, отсутствие риска отрыва пламени при пуске и нормальной эксплуатации;
- отсутствие риска перегрева существующей амбразуры горелки и ее разрушения, снижение тепловых потерь через футеровку свода, пода или боковой стены печи;
- возможность замены старых инжекционных горелок новыми без реконструкции свода печи (используются штатные места), низкие затраты на СМР и ПНР;
- удобное обслуживание горелок во время эксплуатации, простая замена или ремонт горелки;
- быстро окупаемые затраты при замене старых инжекционных горелок на существующих печах (до 2 лет), экономия топлива 2–3%, в отдельных случаях до 5–7%;
- снижение теплового изнашивания реакционных труб в зоне радиации, увеличение срока службы, снижение риска аварии печи.
Замена старых горелок эффективными новыми – стратегическая задача для собственников печей РФ, пора от слов переходить к реальным внедрениям.
Отсутствие или наличие старых газоанализаторов (снижение КПД печи на 1–3%). В процессе эксплуатации печи важным фактором всегда является фактор эффективного использования топлива. Без оптимальной подачи воздуха невозможно добиться качественного горения.
Кроме газовых горелок при этом важную роль выполняют газоанализаторы (кислородомеры) на потоке дымовых газов из печи (рис. 6).
В РФ без таких газоанализаторов продолжают эксплуатировать более 25% печей (установка газоанализаторов не была предусмотрена проектом). Эта ситуация не должна существовать в принципе. Факты показывают, что установка газоанализаторов на печах, отработавших более 20 лет без контроля содержания кислорода в дымовых газах, дает в отдельных случаях до 5% экономии топлива. Примером может служить печь П-4, эксплуатируемая на ОАО «Уралоргсинтез».
После 25 лет эксплуатации печи без газоанализатора (его не было в проекте) в 2013 г. такой газоанализатор был установлен, технологический персонал настроил работу печи с оптимальным содержанием О2 в дымовых газах (3% об.), в результате чего была получена экономия топлива в 5,5%, срок окупаемости мероприятия составил 9 месяцев. Это можно назвать лучшей практикой и рекомендовать к применению тем предприятиям, которые этого еще не сделали.
Постоянное совершенствование ведущими зарубежными и отечественными производителями газоанализаторов, которые помимо О2 могут определять СО и NOx, служит хорошим стимулирующим фактором для технического перевооружения печей. Отдельным предприятиям, в том числе аммиачным, водородным, метанольным производствам, следует заменить старые штатные газоанализаторы (которые определяют только О2) новыми эффективными и многофункциональными.
Можно также предложить дополнительную установку газоанализатора (газоанализаторов) после зоны радиации печи, после вспомогательного котла (в аммиачных установках). Мониторинг состава дымовых газов в разных зонах печи поможет персоналу правильно понять процесс горения и внести в него нужные коррективы. Здесь не следует экономить на установке нового оборудования, эффект может превзойти все ожидания. Важно помнить, что наиболее оптимальным содержанием кислорода в дымовых газах являются 3% об. Любые отклонения от этой цифры приводят к перерасходу топлива (см. рис. 6).
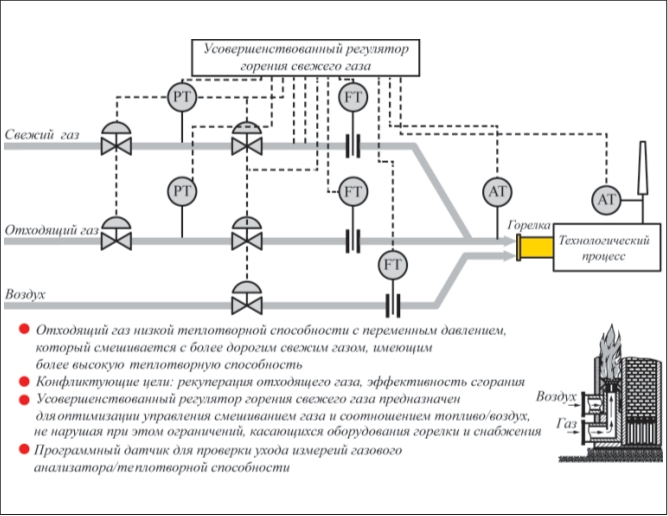
При низком содержании кислорода (недостаток воздуха на горение) происходит химический недожог топлива, в дымовых газах наблюдается увеличение содержания СО, иногда происходит «проскок» СН4, при высоком содержании кислорода (избыток воздуха на горение) – происходит внесение в зону радиации избыточного «холода», избыточный объем холодного атмосферного воздуха от стехиометрического значения приводит к разбавлению тепла в зоне радиации, для восстановления теплового баланса печи требуется сжигать дополнительный объем газа.
Использование старых средств КИП (снижение КПД печи до 2%).
Работа печей на старых проектных схемах КИП без внедрения современных АСУТП и РСУ – это наихудшая практика, которую можно только придумать для технологических печей. Как невозможно безопасно и эффективно управлять дальнемагистральным авиалайнером без приборов навигации, так и работа печей с ограниченным числом параметров уже невозможна в современных условиях. Точный технический учет и контроль параметров всей печи является основой повышения эффективности и надежности ее работы.
Новым направлением в повышении эффективности работы печи может служить внедрение системы АРС (Advanced Process Control), которая представляет специализированное программное обеспечение, реализующее стратегию оптимального управления технологической установкой (цехом, производством) при минимальном вмешательстве операторов. Использование системы АРС в технологическом процессе позволяет повысить нагрузку до 2–5 %, увеличить извлечение ценных продуктов и снизить энергопотребление в отдельных технологических процессах. Увеличение КПД технологических печей может составлять до 1–2 %. Внедрением систем АРС на печах достигается следующее:
- точная балансировка технологических потоков по змеевикам печи (печей);
- поддержание температуры заданных потоков с точностью до 1°С;
- поддержание оптимального соотношения газ/воздух на газовых горелках печи;
- поддержание оптимального разряжения в зоне радиации печи и кислорода в дымовых газах;
- снижение доли влияния человеческого фактора на процесс горения, более оперативное регулирование.
Наличие подсосов холодного воздуха в печи (снижение КПД на 1–2%).
В процессе эксплуатации печей в ряде компаний и предприятий из-за сниженных требований к ремонту и обслуживанию в силу разных причин, связанных с человеческим фактором, происходит следующее.
Нарушается полная герметичность в зонах радиации и конвекции печи.
На рис. 8 представлены характерные примеры подсоса воздуха в печах.
Небрежно закрытый или неотремонтированный смотровой лючок, незакрытое штатное отверстие для розжига горелки, негерметичный люк-лаз или зазор между гильзой и трубой в своде или поде печи, негерметичные стены в местах расположения трубных змеевиков конвекции и др. – все это вызывает нарушение теплового баланса печи и приводит к перерасходу топлива на горение. Только тот воздух, который поступает на газовую горелку через штатные шиберы и регистры, выполняет созидательную роль в процессе горения, весь остальной воздух, попадающий в печь через разного рода неплотности, является контрпродуктивным и снижает КПД печи. Это должен помнить весь персонал, занимающийся эксплуатацией, ремонтом и сервисом печи.
В качестве примера можно привести такой факт: подсос воздуха через отверстие площадью 0,0025 м2 (размер одного спичечного коробка или просто один незакрытый смотровой лючок) при разрежении минус 5 мм. вод. ст. в зону радиации печи попадает 6,9 м3/ч холодного наружного атмосферного воздуха, нарушается тепловой баланс печи, для восстановления которого необходимо дополнительно сжечь 1,33 м3/ч газа. Годовой перерасход топлива составит 11,2 тыс. м3 (44,8 тыс. руб.).
Случаев эксплуатации печей без подсосов воздуха в практике практически нет. В действительности на каждой печи при желании можно обнаружить несколько таких подсосов. Важно их вовремя зафиксировать и принять меры к устранению потерь топлива. По большей части это потери организационного характера, их устранение не требует инвестиций. Как говорится, копейка рубль бережет.
Человеческий фактор (снижение КПД печи до 2%). В процессе эксплуатации печей очень важен человеческий фактор, направленный как на безопасную эксплуатацию печи, так и на ее эффективную работу. Безопасность при эксплуатации печи достигается проектом, наличием современных АСУТП и РСУ, продуманной системой блокировок, актуальными регламентом и инструкцией, приобретенным опытом. Эффективность работы печи достигается наличием эффективного оборудования (новые горелки, новые газоанализаторы, новые трубные змеевики, новый катализатор, новая РСУ, новая АРС и т.д.). Поддержание оптимального разрежения, тонкая и эффективная регулировка горения топлива, ряд других приобретенных навыков и лучших практик помогают оператору эксплуатировать печь с наивысшим КПД. Этого не происходит, если отсутствует системное обучение персонала эффективным методам работы, не осуществляется обмен опытом среди родственных предприятий в учебных центрах или на выездных совещаниях (часто из-за желания соблюсти коммерческую тайну и т.п.). Необученный персонал не сможет организовать эффективный технологический процесс в печах, потери топлива будут определяться низкой квалификацией ИТР и персонала. Только высокий профессионализм, высокая дисциплина и ответственность, продуманная система мотивации помогут персоналу вести безопасную и эффективную эксплуатацию печи на существующем оборудовании.
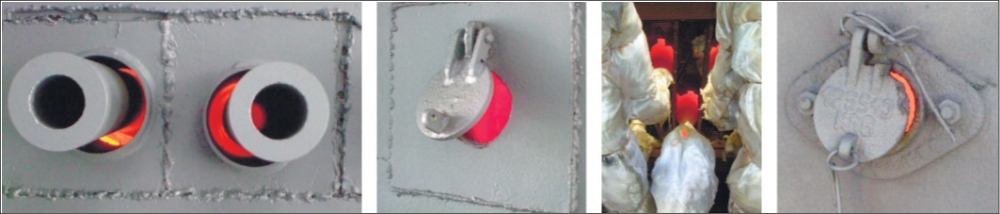
а – в гильзах труб пода печи; б – в незакрытый смотровой лючок; в – в гильзах труб пода печи; г – в незакрытый смотровой лючо
Таким образом, перечисленные факторы снижения (очень редко повышения) проектного КПД печи (печей) могут быть весьма существенными, иногда сумма факторов вызывает снижение КПД печи на более чем 10%. Это приводит к неоправданным затратам на топливо в балансе всех затрат на энергоресурсы предприятия, возрастает себестоимость продукции, падает ее конкурентно-способность. Чтобы понимать, на каком фактическом энергоэффективном уровне находится ваша печь (печи), необходимо провести их комплексное целевое обследование опытными экспертами-профессионалами с опытом эксплуатации и инжиниринга, но об этом поговорим в наших следующих публикациях.
Безопасность печи, новые материалы, методы диагностирования
Данная тема многогранна, она охватывает широкий круг вопросов.
В данной статье, посвященной эффективности работы печей, она не обсуждается. Это – тема для отдельной публикации.
Организация обучения передовым методам и лучшим практикам
Только отдельные компании и предприятия имеют собственные учебные центры в которых производится подготовка персонала для обслуживания печей, в том числе с применением обучающих тренажеров и других инструментов. Основная масса предприятий не проводит системную работу в данном направлении, персонал этих предприятий проходит обучения в рамках знания регламента и инструкции. За последние годы не проведено ни одного масштабного совещания по повышению эффективности работы печей в рамках всех компаний РФ в области нефтепереработки, нефтеи газохимии. Тематических публикаций и докладов по теме повышения эффективности печей крайне мало, узнать об этом очень сложно, а зачастую и невозможно. В современной России нет общего координатора, который бы мог возглавить данный процесс в масштабах всей страны. Тема повышения эффективности печей очень актуальна для РФ, она должна быть изучена в правительстве РФ.
Все мы ждем новых идей и практических действий.
Актуализация Правил ПБ-09-563–03
Правила ПБ-09-563-03 были разработаны для печей нефтехимии и нефтепереработки. В дальнейшем эти Правила были спроецированы Ростехнадзором и на все печи газохимии. Данные Правила уже давно требуют масштабной и качественно новой переработки, они не соответствуют современным критериям проектирования, строительства, эксплуатации, эффективности, ремонта, диагностики и безопасности.
Ростехнадзор в силу ряда причин не имеет компетентных экспертов и специалистов, которые бы смогли разработать абсолютно новые всеобъемлющие Правила отдельно для печей нефтепереработки и нефтехимии, а также отдельно для печей газохимии, используя уже накопленный отечественный опыт и лучший мировой опыт зарубежных инжиниринговых фирм.
В рамках ежегодных НИОКР Ростехнадзору следует привлечь к разработке новых Правил лучших экспертов, ученых и специалистов, которые несомненно есть в России, их надо только выявить и привлечь к работе по данной тематике. Это задача первостепенной важности, она способна изменить отношение к печам госорганов, вывести Россию на новый эффективный уровень.
В данной статье автор с более чем тридцатилетним опытом эксплуатации и инжиниринга печей нефтепереработки, нефте-и газохимии высказал свою точку зрения относительно существующего положения дел с печами в РФ. Проблемы печей, особенно в части их эффективности, есть, и их надо решать. Надеемся, что данная тема не оставит читателей равнодушными, и мы будем все вместе создавать сообщество «печников» РФ и решать проблемы с эффективностью печей компаний, предприятий и России в целом. Компания «Арсенал Групп» намерена опубликовать в журнале «Химическая Техника» серию статей, посвященных эксплуатации печей и факельных систем. Ждем ваших отзывов, предложений, идей.