Автор: А.Б. Жидков (ООО «Алитер-Акси»).
Опубликовано в журнале Химическая техника №9/2014
Расходы на топливо и эксплуатацию трубчатых нагревательных печей в процессе переработки нефти – одна из наиболее заметных статей расходов современных НПЗ. Вопросам энергоэффективности эксплуатации этих объектов посвящена данная статья.
По нашему мнению, энергоэффективность работы печи определяется не только расходом топлива на единицу нагреваемого продукта. В это понятие необходимо включать также расходы на эксплуатацию, поддержание заданных проектных параметров во время межремонтного пробега и многое другое.
В общем случае на энергоэффективность влияют следующие факторы.
- расход топлива на нагрев продукта (полнота использования) или коэффициент полезного действия печи;
- энергозатраты на поддержание работы печного блока;
- затраты на ремонт и межремонтный пробег;
- экологические показатели (шум, выбросы СО, NOx,SO2);
- уровень безопасности эксплуатации,
- соответствие системы управления печью нормам Ростехнадзора.
Рассмотрим более подробно эти факторы.
Первый показатель, на который сегодня обращают наибольшее внимание, – расход топлива.
Факторы, влияющие на расход топлива в печи:
- коэффициент полезного действия (КПД) печного блока;
- теплопотери печи через наружные стенки;
- работа горелочных устройств;
- состояние наружной и внутренней поверхностей змеевика камер конвекции и радиации.
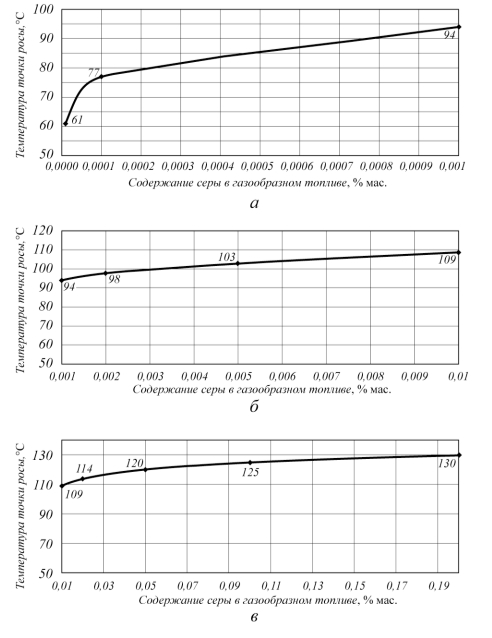
(природный газ) в различных диапазонах концентраций:
а – 0–0,001% мас.; б – 0.001 – 0.01% мас.; в – 0,01 – 0,2% мас.
В этом разделе мы рассматриваем более простой и широко применяемый топливный КПД печи [1], т.е. процент использования тепла сгорания топлива для теплопередачи продуктам в сырьевых змеевиках печи и системе утилизации тепла (подогрев воздуха, выработка пара, теплофикационной воды и т.п.). Термический КПД печи [1] рассмотрим в следующем разделе.
Топливный КПД фактически определяется температурой выходящих дымовых газов из печного блока (печь и узел утилизации тепла). Чем ниже температура, тем выше КПД. Выполнить проект печи с температурой выходящих дымовых газов, близкой к наружной температуре окружающей среды, используя системы утилизации тепла (котел-утилизатор, нагрев теплофикационной воды, воздухоподогреватель и т.п.), не представляется сложным. Основная проблема на пути реализации этих проектов – конденсация паров воды и кислых серусодержащих веществ из дымовых газов и их последующая утилизация.
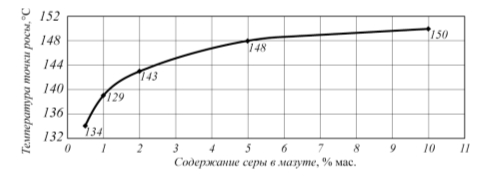
Подавляющее большинство современных печей (находящихся в эксплуатации и вновь проектируемых) для обеспечения надежной работы печи имеют на выходе температуру дымовых газов выше температуры конденсации (температура точки росы). Для определения максимально возможных значений КПД печи при таком требовании на рис.1 и 2 представлены зависимости температуры точки росы от содержания серы в природном газе и жидком топливе (мазут).
Для обеспечения условий эффективного теплопереноса и отсутствия конденсации на поверхности труб на выходе из печи (котла-утилизатора, воздухоподогревателя и т.п.) минимальную температуру стенки труб поддерживают на уровне 10…20°С выше температуры точки росы, температуру уходящих газов – на 40…60°С выше температуры стенки наиболее холодной трубы (поверхности теплообмена в пластинчатых и иных теплообменниках).

при различной разнице температуры уходящих дымовых газов и минимальной температуры стенки труб 40 (1); 50 (2)
и 60°С (3):
а – 0–0,001% мас.; б – 0,001 – 0.1% мас.; в – 0,1–0,2% мас.
Исходя из этих условий, на рис. 3 показаны кривые зависимости максимально возможного КПД печи на топливе – природном газе – в зависимости от содержания серы в топливе при температуре стенки трубы на 15°С выше температуры точки росы и температуре уходящих газов температуры стенки на 40; 50 и 60°С. Из этих графиков следует, что при обеспечении режима «сухих» труб на газообразном топливе максимально разумный топливный КПД печного блока 92–91%. Причем, при повышении содержания серусодержащих веществ до 0,01 – 0, 02% КПД печного блока необходимо снижать для обеспечения данного режима.
При использовании в качестве топлива мазута или других жидких топлив максимально разумный КПД находится в диапазоне 89–87% (рис. 4). Данный режим обеспечивает работу теплообменных поверхностей на выходе из печи «сухими» (без конденсации).
Если ставится задача достижения более высоких КПД, то необходимо использовать на выходе из печного блока системы утилизации тепла с коррозионно-стойкими теплообменными поверхностями и системы промывки теплообменных поверхностей от кислого конденсата с последующей утилизацией. Такие аппараты хорошо известны. Например, есть реализованные проекты с воздухоподогревателями со стеклянными секциями, с чугунными секциями, с секциями из металлических труб с покрытием эмалями или глазурями на основе стекла. Поверхности теплообмена в таких аппаратах со стороны дымовых газов периодически орошаются водой для очистки.
Данные системы позволяют увеличить КПД печного блока до 95–96%. Но они достаточно дорогие, а их эксплуатация сопряжена с дополнительными расходами на утилизацию кислых отходов. В связи с этим при принятии решения по реализации этих систем необходимо определять экономическую эффективность с учетом остальных факторов энергоэффективности. Эти расчеты не представляют сложности для специализированных организаций в области проектирования печей. В общем случае можно отметить, что применение систем утилизации тепла с КПД выше 92% целесообразно на печных блоках мощностью более 70…80 МВт.
Теплопотери печи
Теплопотери печи можно рассчитать, если выполнить тепловизорную съемку кожуха печи, воздухоподогревателя. Но в общем случае потери тепла с поверхности печи при нормальной футеровке и температуре поверхности не выше нормативной (60°С ) находятся в диапазоне 1,5–2,5% [1, 2], что не является не большой величиной.
Значительно больше топлива тратится на нагрев избытка воздуха в печи, полученного за счет неорганизованных подсосов. При этом даже, если оператор отрегулировал горелки по датчику избытка кислорода на выходе из печи до 3–4%, но содержание моноокиси углерода высокое (более 0,2–0,5%), это покажет, что воздух поступает в печь не через горелку (смешиваясь с топливом и обеспечивая нормальное горение), а через неплотности в печи.
Практически во всех печах на российских НПЗ подсос воздуха происходит через негерметичные окна, неплотности при проходе продуктовых труб через стены и др., что приводит к избытку в печи воздуха от 5 до 200%.
В связи с этим обеспечение герметичности кожуха печи, окон и других элементов печи – важная часть обеспечения как энергоэффективности, так и организации горения топлива.
Работа горелочных устройств
Работа горелочных устройств – важная составляющая энергоэффективности. Качество смешения газообразного топлива и воздуха, жидкого топлива, пара и воздуха обеспечивает полноту сгорания. Сегодня большинство заказчиков настаивают на импортных горелках, которые имеют лучшие экологические и шумовые показатели.
Однако применение импортных горелок повышает требования к герметичности печи, параметрам (давление, температура, состав) топлива, к диапазону регулирования мощности горелки. Обеспечение этих параметров не всегда возможно, поэтому сегодня на каждом втором заказе есть технические проблемы в работе импортных горелок.
В целом можно констатировать: наладка работы горелок, регулирование соотношения топливо – воздух, топливо – пар – воздух позволяет экономить от 1 до 5% топлива на работу печи.
Состояние внутренней и наружной поверхности змеевиков
В процессе эксплуатации на наружной поверхности змеевика образуются различные типы отложений – окислы железа, сернистые соединения железа, других элементов, сажевые. Наиболее активно образование наружных отложений наблюдается в камере конвекции.
В камере радиации при горизонтальном расположении труб также наблюдаются отложения в верхней части трубы. При вертикальном расположении труб в основном имеются окисные отложения. При эксплуатации печи более полугода без очистки наружной поверхности змеевиков, особенно на жидком топливе, температура выхода дымовых газов увеличивается на 50…80°С, КПД уменьшается на 10% и более.
Для очистки наружной поверхности труб камеры конвекции в настоящее время используются три метода:
- парообдувка;
- газоимпульная очистка;
- химическая очистка змеевика.
Для очистки наружной поверхности труб камеры радиации на ходу работы установки применяется только химическая очистка змеевика.
Более подробно эти методы описаны в работе [3].
Таблица 1
Температура дымовых газов на выходе из камеры конвекции
Тип печи | До пуска системы ГИО, °С | После пуска системы ГИО, °С |
Печи П-1, П-101
установки изомеризации |
311 | 259 |
Печь 04В-F01 блока разделения риформинга | 389 | 312 |
В табл. 1 представлены данные по эффективности использования газоимпульсной очистки (ГИО) змеевиков на двух печных блоках. Данные установки были запущены в эксплуатацию без работающей системы ГИО.
За 6–8 месяцев эксплуатации температура дымовых газов на выходе из печи поднялась на 60…70°С. После подключения системы ГИО и отработки 20 циклов очистки параметры работы печи вернулись к проектным.
Сегодня широко рекламируются методы покрытия поверхности змеевиков камеры радиации составами на основе керамики, которые защищают поверхность от образования окалины, повышают теплопередачу.
В ООО «Алитер-Акси» не имеется подобного положительного опыта. Подавляющее большинство известной керамики имеет теплопроводность намного меньше теплопроводности металла, без химического взаимодействия материала покрытия и металла трубы эффективная теплопередача невозможна. Но такое взаимодействие вызовет изменение свойств металл (твердость, ударная вязкость и т.п.), что недопустимо.
При эксплуатации печей во многих процессах внутри змеевика образуется кокс, который препятствует теплообмену, может снизить тепловую мощность печи, остановить технологический процесс. Сегодня практически нет эффективных систем очистки внутренней поверхности змеевика от коксовых отложений во время работы установки.
В печах установок замедленного коксования очистку внутренней поверхности труб производят путем поъема температуры стенки трубы на 20…25°С выше, чем требуется по технологическому режиму. При этом стенки змеевика расширяются больше, чем на рабочем режиме, слой кокса раскалывается. В змеевик со скоростью более 100 м/с подается относительно холодный пар, который вымывает частички кокса. Для реализации процесса очистки нагрузку на печь вначале снижают, подачу сырья отключают, увеличивают подачу пара. Очистка змеевика занимает до 20 ч, фактически печь выводится из технологического процесса на короткий период времени без остановки работы печи. Поскольку процесс замедленного коксования – циклический, увеличивается время на переключение печи на реакционную камеру на время очистки змеевика от кокса. Данная технология реализована с участием специалистов ООО «Алитер-Акси» на Волгоградском НПЗ и эффективно работает более двух лет.
Удаление кокса на печах в других процессах (гидроочистка, печи вакуумных процессов и др.) проводится коксовыжигом с выведением печи из эксплуатации.
На скорость образования кокса влияют такие факторы, как скорость движения сырья в змеевике, тепловая напряженность и равномерность распределения тепла в топочном пространстве, объем, параметры, место подаваемого турбулизатора (пар), геометрия змеевика, расположение горелок и др. Наиболее реальный путь борьбы с отложениями кокса внутри змеевика сегодня – это подбор (расчетным и опытным путем) технологического режима работы печи.
Таким образом, подводя итог самого большого раздела статьи, можно сделать вывод о том, что задачу снижения расхода топлива на нагрев продуктов следует решать комплексно: от проектирования печи с разумным КПД, состояния кожуха, футеровки, организации работы горелочных устройств до поддержания наружной и внутренней поверхности змеевиков в рабочем (чистом) состоянии.
Энергетические затраты на поддержание работы печного блока
Для обеспечения работы печного блока необходимо использовать внешние источники энергии, которые также являются частью энергетического баланса печи.
Основные затраты:
- расход заводского пара или электроэнергии на подогрев топлива;
- расход пара или электроэнергии на предварительный подогрев воздуха (в печь или воздухоподогреватель);
- расход заводского пара на распыл жидкого топлива;
- расход электроэнергии на работу тягодутьевого оборудования;
- расходы на сбор и утилизацию жидких кислых отходов с поверхности труб воздухоподогревателя или котлаутилизатора при работе в зоне кислотной температуры точки росы.
Если учесть все эти расходы и привести их к единым единицам измерения (кВт или кДж), то можно рассчитать термический (общий) коэффициент полезного действия печи. Он окажется значительно ниже топливного КМД.
Расчет термического КПД печи необходимо выполнять для оценки энергоэффективности печного блока при принятии решения об установке системы утилизации тепла, разумного КПД печного блока, замены печи, реконструкции. В конечном счете термический КПД можно перевести в экономические показатели, сопоставить с затратами на реконструкцию, новое строительство и принять правильное решение.
Экологические показатели работы печного блока
Сегодня раздел экологии обязателен при реализации любого проекта. Увеличение выбросов вредных окислов в процессе горения (NOx, CO) приходится компенсировать мероприятиями по увеличению высоты дымовой трубы. Иногда реализация проекта может остановиться.
При решении задачи повышения энергоэффективности работы печного блока необходимо учитывать, что повышение температуры воздуха на 100°С, подающегося на горение при использовании воздухоподогревателя, повышает концентрацию выбросов указанных газов в 2–4 раза [4]. Особенно это важно при реализации проектов на жидком топливе. Увеличение выбросов окислов азота при увеличении температуры дутьевого воздуха может быть непреодолимой преградой при прохождении экологической экспертизы.
Следующий фактор – содержание моноокиси углерода (СО). При уменьшении содержания окислов азота снижается максимальная температура факела, температура перевала печи. Снижение температуры перевала приводит к резкому повышению содержания моноокиси азота в дымовых газах. Эти противоречия не всегда удается решить даже с привлечением зарубежных компаний – разработчиков горелочных устройств.
Важный показатель работы печного блока – уровень шума. Сегодня идет работа по снижению шума от работы горелок до 70…75 дБ. Реализация этого требования приводит к удорожанию горелок с шумовой защитой, использованию дутьевого воздуха независимо от наличия воздухоподогревателя, дополнительных расходов на эксплуатацию воздуходувки.
Уровень безопасности, соответствие системы управления печью нормам Ростехнадзора
Этот раздел наиболее простой. На вводимых объектах проблем с контролем со стороны Ростехнадзора не возникает. Печи, построенные до 2000 г., необходимо в период ремонта приводить к нормам Ростехнадзора.
В противном случае вводить эксплуатирующая организация будет постоянно нести дополнительные расходы (штрафы, реализация предписаний).
В данном случае этот раздел важен, чтобы показать следующее: в процессе приведения печного блока к нормам наиболее удобно заменить горелки, оснастить печь приборами контроля ведения процесса, состава дымовых газов, выполнить ремонт кожуха, футеровки, установить систему очистки труб. После такого ремонта энергоэффективность печного блока резко повысится.
В табл. 2 показаны результаты по экономии топлива, полученные на одном из заводов России после выполнения комплекса работ по приведению печей к нормам и выполнению мероприятий по регулированию процессов горения топлива.
Таблица 2
Суммарное потребление энергоресурсов печей установок 24/6, 24/7, ТК-1, 24/600, 35-11/100, АТ-6 за месяц эксплуатации до и после выполнения мероприятий по энергоэффективности
Энергоноситель | 2011 год | 2012 год | Процентное соотношение |
Пар, Гкал | 71183 | 54100 | –24% |
Топливный газ, тыс. т | 51000 | 42624 | –16,4% |
Жидкое топливо, тыс. т | 4383 | 3753 | –14,4% |
Природный газ, тыс. т | 2477 | 2652 | +7,1% |
Таким образом, задача повышения энергоэффективности работы печей является комплексной проблемой, включающей оптимизацию технологического режима работы печи, качество футеровки и кожуха печи, выбора и наладки работы горелочных устройств, оптимизацию энергозатрат на обеспечение работы печного блока.
Важное место в этом вопросе занимают экологические показатели, соответствие системы управления печью требованиям Ростехнадзора.
Список литературы.
- ГОСТ-Р 53682–2009. Установки нагревательные для нефтеперерабатывающих заводов. Общие технические требования. Москва, Стандартинформ, 2011. 69 с.
- Шарихин В.В., Коновалов А.А., Скороход А.А. Трубчатые печи. .Самара: ООО «Офорт», СамГТУ, 2005. 444 с.
- Жидков А.Б., Логинов И.А., Козлов П.В. Методы очистки наружной поверхности змеевиков трубчатых печей//Химическая техника. 2012. №12. С. 32–34.
- The John Zink. Combustion handbook. Edited by Charles E.Baukal, Jr. CRC Press LLC, 2001. 750 р.