Авторы: С.П. Сергеев (Российский химико-технологический университет),
С.В. Афанасьев (ПАО «Тольяттиазот»)
Опубликовано на портале «Химическая техника», август 2019
Считается общепринятым, что совершенствование промышленного способа получения синтез-газа, обогащенного водородом и монооксидом углерода, в трубчатых реакторах с использованием катализаторов определенной конструктивной формы весьма актуально на крупнотоннажных производствах аммиака, метанола, уксусной кислоты и водорода.
При осуществлении указанного процесса реализуются следующие эндо- и экзотермические реакции:
СnHm + nH2O → nCO + (n +m/2)H2 (–ΔHо298 < 0); (1)
CO + H2O ↔ CO2 + H2 (–ΔHо298 = 41 кДж/моль); (2)
CH4 + H2O ↔ CO + 3H2 (–ΔHо298 = –206,4 кДж/моль). (3)
Промышленный паровой риформинг проводят в присутствии никельсодержащего катализатора в виде гранул различных размеров и форм, которыми заполняют трубы реактора. В контактных аппаратах указанного типа (печи риформинга) необходимая для протекания химического процесса теплота передается из зоны сжигания топлива путем ее конвективного и излучательного переноса на внешние поверхности реакционных труб. Благодаря высокой теплопроводности металла труб тепло аккумулируется газовой фазой и гранулами катализатора. Температура последних, как правило, на 100 °С ниже (особенно в центральной части слоя катализатора) температуры внутренней стенки трубы.
Указанный способ производства синтез-газа имеет следующие характерные недостатки:
– необходимость поддержания более высокой температуры наружных стенок труб по сравнению с температурой слоя катализатора, что приводит к повышенному расходу энергоносителей и сокращению срока эксплуатации реакционных труб;
– выбор оптимальных размеров гранул катализатора зачастую не согласуется с диаметром трубы, вследствие чего могут возникать неоднородности полей температур и скоростей газа по сечению труб [1–4].
Авторам работы [4] удалось преодолеть большинство из них. Предложенный ими усовершенствованный способ получения синтез-газа, обогащенного водородом и монооксидом углерода, основан на каталитическом риформинге углеводородсодержащего сырья, подаваемого в смеси с водяным паром в обогреваемые трубы реактора с загруженным катализатором. При этом впервые в мировой практике катализатор представляет собой гранулы сферической формы с отношением их диаметра к высоте загруженного слоя 1,0·10-3–2,0·10-3, в которых имеются цилиндрические каналы размером в 2–10 раз меньше, чем диаметр шаров. Содержание никеля в катализаторе составляет 9–25 % мас. в пересчете на монооксид никеля, а в качестве материала для изготовления шаров используют глинозем определенной марки.
Узким местом в указанном процессе получения синтез-газа является повышенный перепад давления по высоте реакционных труб, что препятствует наращиванию мощности агрегатов аммиака.
С целью оптимизации паровой конверсии углеводородов предложено вести её в реакционных трубах с пониженной толщиной стенок, что может быть достигнуто повышением активности катализатора, снижением газодинамического сопротивления, улучшением эксплуатационного ресурса реакционных труб и снижением расхода топливного газа [5–8].
Внедрению рассмотренных и других известных технических решений препятствует повышенное потребление энергии, удельные затраты которой являются мерой термодинамического совершенства процесса [8 риформинг 10].
Определённый прогресс достигается путем комбинирования каталитического парциального окисления и автотермического каталитического риформинга, включающего следующее:
а) использование в заданных пропорциях потоков углеводородов, содержащих кислородсодержащие среды и технологический пар;
б) введение указанных потоков в зону каталитического парциального окисления для получения предварительного продукта;
в) подачу этого предварительного продукта и второго потока, содержащего кислород, на стадию парциального окисления путем осуществления реакции в пламени;
г) проведение дальнейшего процесса парциального окисления в реакционной зоне парового риформинга с целью получения синтез-газа;
д) отделение потока синтез-газа для предотвращения парциального окисления, таким образом, устанавливая, двухступенчатый процесс автотермического риформинга.
Однако и в рассматриваемом случае не устранены отмеченные недостатки.
Предлагаемое техническое решение основано на том, что дымовой газ, получаемый от сжигания топлива с окислителем, используют в качестве теплоносителя для снабжения энергией стадии каталитического риформинга углеводородов, направляя его в каскад реакторов: сначала в первый реактор, в котором теплообмен происходит преимущественно за счет радиационной составляющей, а затем – во второй и последующие реакторы, в которых теплообмен происходит преимущественно за счет конвективной составляющей коэффициента теплоотдачи.
Подача дымового газа под давлением позволяет увеличить интенсивность радиационного теплопереноса в первом реакторе и конвективного теплопереноса во втором.
В табл. 1 и 2 приведены значения радиационных коэффициентов теплоотдачи αр и их суммы с конвективными коэффициентами αк применительно к схеме, показанной на рисунке.
Таблица 1
Коэффициенты теплоотдачи (Вт/(м2∙К)) для первого реактора (давление греющего дымового газа 1 ат)
Температура конвертированного газа, °С | Температура греющего газа, °С | αр+αк | αр |
799,37 | 1086,8 | 51,782 | 31,838 |
798,41 | 1087,9 | 51,765 | 31,818 |
797,94 | 1089,0 | 51,813 | 31,864 |
797,76 | 1090,2 | 51,843 | 31,891 |
797,79 | 1091,3 | 51,880 | 31,926 |
797,96 | 1092,5 | 51,918 | 31,962 |
798,24 | 1093,6 | 51,959 | 32,000 |
798,58 | 1094,8 | 52,001 | 32,039 |
798,99 | 1095,9 | 52,046 | 32,082 |
799,43 | 1097,1 | 52,090 | 32,123 |
799,90 | 1098,2 | 52,135 | 32,166 |
800,38 | 1099,4 | 52,180 | 32,209 |
800,87 | 1100,6 | 52,226 | 32,252 |
801,37 | 1101,8 | 52,272 | 32,296 |
801,88 | 1102,9 | 52,318 | 32,339 |
802,40 | 1104,1 | 52,365 | 32,383 |
802,91 | 1105,3 | 52,411 | 32,428 |
Таблица 2
Коэффициенты теплоотдачи (Вт/(м2∙К)) для первого реактора (давление греющего дымового газа 28 ат)
Температура конвертированного газа, °С | Температура греющего газа, °С | αр+αк | αр |
803,60 | 1090,2 | 157,56 | 137,58 |
804,19 | 1093,1 | 158,33 | 138,34 |
804,97 | 1096,1 | 158,89 | 138,90 |
805,94 | 1099,1 | 159,47 | 139,47 |
807,04 | 1102,1 | 160,04 | 140,04 |
808,23 | 1105,1 | 160,62 | 140,61 |
809,50 | 1108,1 | 161,20 | 141,19 |
810,81 | 1111,2 | 161,79 | 141,77 |
812,16 | 1114,3 | 162,38 | 142,36 |
813,55 | 1117,5 | 162,98 | 142,96 |
814,97 | 1120,6 | 163,59 | 143,56 |
816,41 | 1123,8 | 164,20 | 144,17 |
817,87 | 1127,0 | 164,82 | 144,78 |
819,35 | 1130,3 | 165,45 | 145,40 |
820,86 | 1133,6 | 166,08 | 146,03 |
822,38 | 1136,9 | 166,71 | 146,66 |
823,92 | 1140,2 | 167,36 | 147,30 |
Приведенные данные характеризуют соотношение интенсивности обоих видов теплопередачи в первом реакторе каталитического парциального окисления 1 с преимущественно радиационным подводом тепла в зону реакции при давлениях дымового газа 1 и 28 атм. В табл. 3 приведены аналогичные данные для второго реактора каталитического парциального окисления 2 с преимущественно конвективным подводом тепла в зону реакции при давлении дымового газа 28 атм.
Таблица 3
Коэффициенты теплоотдачи (размерность Вт/(К∙м2)) для второго реактора (давление греющего дымового газа 28 ат)
Температура конвертированного газа, °С | Температура греющего газа, °С | αр+αк | αр |
477,77 | 551,09 | 277,78 | 17,363 |
479,07 | 551,84 | 277,86 | 17,413 |
480,35 | 552,58 | 277,94 | 17,462 |
481,60 | 553,33 | 278,02 | 17,511 |
482,83 | 554,06 | 278,10 | 17,560 |
484,04 | 554,80 | 278,18 | 17,608 |
485,23 | 555,52 | 278,26 | 17,655 |
486,40 | 556,25 | 278,34 | 17,703 |
487,55 | 556,97 | 278,42 | 17,750 |
488,69 | 557,69 | 278,49 | 17,796 |
489,80 | 558,40 | 278,57 | 17,842 |
490,90 | 559,11 | 278,65 | 17,888 |
491,98 | 559,81 | 278,72 | 17,934 |
493,04 | 560,51 | 278,80 | 17,979 |
494,09 | 561,21 | 278,87 | 18,024 |
495,12 | 561,91 | 278,95 | 18,068 |
496,13 | 562,60 | 279,02 | 18,113 |
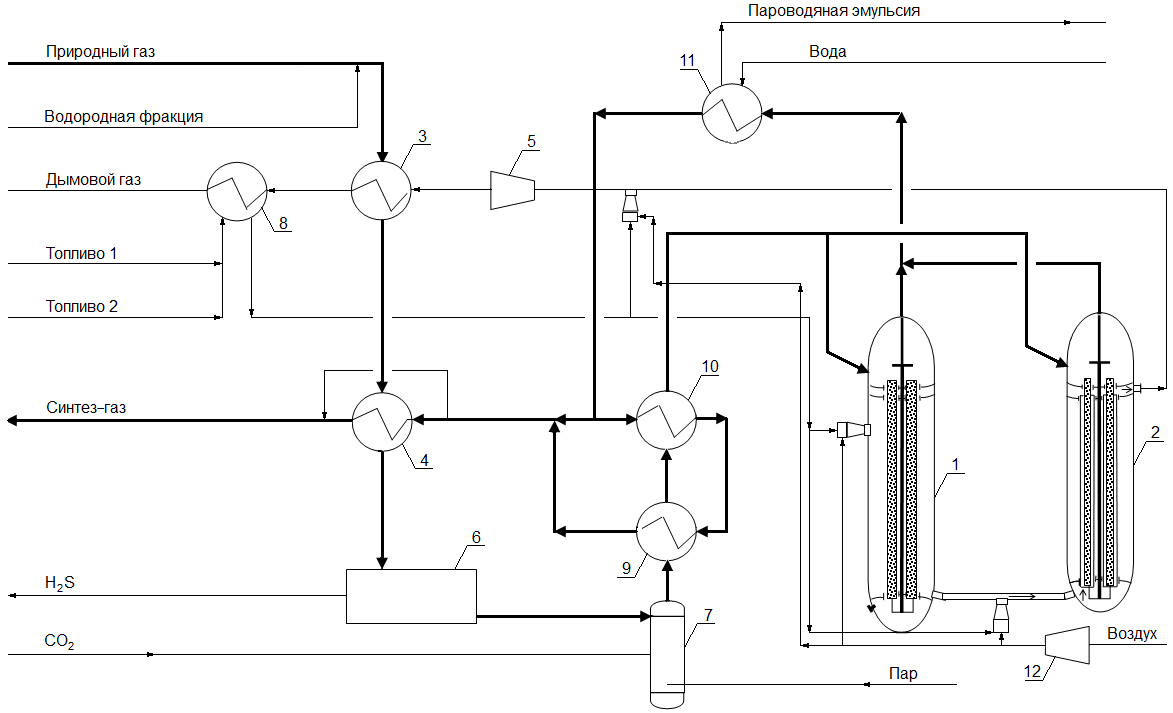
Процесс реализуется следующим образом, Природный газ смешивают с водородной фракцией и направляют для предварительного теплообмена в теплообменники 3 и 4, В теплообменнике 3 газовая смесь нагревается отходящим дымовым газом, расширенным в газовой турбине (экспандер) 5, а в 4 – частью конвертированного газа и направляется в аппараты сероочистки 6, в которых освобождается от сернистых соединений. Очищенный газ поступает в коллектор – делитель, в котором от него отделяют технологическую фракцию «1» (используемую для процесса) и топливную фракцию «2» (сжигаемую в горелках). Топливная фракция по описываемую техническому решению очищается от сернистых и других химических соединений, являющихся катализаторными ядами. Это позволяет получать дымовой газ от сжигания этой фракции также свободным от указанных соединений. В результате дымовой газ может быть использован в технологическом процессе, в том числе как питание для каталитических реакторов. К топливной фракции с целью уменьшения расхода основного топлива допускается добавка любых видов дополнительных топлив, подогреваемых теплообменником 8. Поток топлива может разделяться на несколько частей, Основная часть сжигается в главных горелках первого реактора 1, остальные части используют для управления процессом и при пусковых операциях, сжигая их во вспомогательных горелках турбины и второго реактора 2. В очищенную технологическую фракцию в смесителе 7 добавляют пар. Парогазовую смесь после подогрева в теплообменниках 9 и 10 в зависимости от интенсивности теплообмена в реакторах 1 и 2 делят на две части в пропорции, обеспечивающей минимальную концентрацию метана в конвертированном газе, поступающем в теплообменник 11. Первая часть поступает в реактор 1, а вторая – в реактор 2. В обоих реакторах протекают эндотермические реакции риформинга с водяным паром и/или с диоксидом углерода. Источником тепла, обеспечивающим протекание эндотермических реакций, служит дымовой газ, получаемый в основных Г1 и вспомогательных горелках Г2 и Г3 путем сжигания топливной части природного газа с воздухом. Дымовой газ из основных горелок поступает в межтрубное пространство первого реактора 1, отдает часть тепла, а затем поступает в межтрубное пространство второго реактора 2. Второй реактор снабжен вспомогательной пусковой горелкой, которая при необходимости используется для управления процессом в нём. Первый и второй реакторы отличаются тем, что в первом из них теплопередача в основном осуществляется радиационным теплообменом (80–97 %), а во втором определяющим фактором является конвективный теплообмен. На долю радиационного теплообмена во втором реакторе приходится 5–20 % переданного тепла. Второй реактор может содержать одну или более ступеней с целью увеличения степени конверсии и использования тепла дымового газа,
В результате в реакторах 1 и 2 образуется смесь газов при температуре 873°С и давлении 26,9 ата следующего состава, % об : CO2 – 5,48, CO – 8,37, Н2 – 47,49, N2– 0,331, H2O – 35,68, СН4 – 2,64, Ar – 0,003.
Для снижения температуры синтез-газа при необходимости его поток пропускают через теплообменник 11.
Описанный способ позволяет более чем в 2 раза увеличить использование теплоты дымового газа (теплоносителя) для протекания эндотермических реакций.
Дымовой газ получают следующим образом. Сжатый в компрессоре 12 воздух разделяют на несколько частей. Первая часть – технологический воздух. Этот воздух используется, например, если описываемый унифицированный способ генерации синтез-газа является частью технологической схемы производства аммиака. Две другие части применяют для сжигания топлива в главных горелках Г1 первого реактора 1 и во вспомогательных горелках турбины Г2 и горелках Г3 второго реактора 2. Таким образом, по образующемуся дымовому газу все использующие его объекты соединены последовательно и параллельно. Дымовой газ, получаемый на всех ступенях сжигания топлива после использования теплоты в реакторах с температурой ~540 оС поступает в коллектор турбины, из которого часть дымового газа при необходимости можно отбирать для технологического использования,
Работа от расширения дымового газа в экспандере 5 используется для привода компрессора воздуха или для иных целей. Остаточную теплоту расширенного в экспандере дымового газа используют для предварительного подогрева технологического газа в теплообменнике 8. Выходящий из теплообменника дымовой газ (состав, %. об: CO2 – 8,19 %, N2 – 71,58 %, O2 – 2,71 %, H2O – 16,66 %, Ar – 0,854 %) температурой ~150 оС выбрасывается в атмосферу.
Отсутствие в дымовом газе оксидов серы и его относительно низкая температура значительно уменьшают экологически опасное воздействие на окружающую среду.
Применительно к производству аммиака может быть рекомендована рассмотренная схема получения синтез-газа, дополненная реактором автотермического риформинга (вторичный риформинг). В него подают конвертированный газ из реакторов 1 и 2 унифицированной схемы, а также технологический воздух от компрессора 12. Дополнительно в реактор направляют часть дымового газа, отбираемого из коллектора экспандера 5.
Теплоту конвертированного газа, выходящего из реактора вторичного риформинга, используют в котлах-утилизаторах для получения пара, а оставшуюся теплоту – для подогрева технологических потоков. Затем конвертированный газ подвергают обработке по стандартной схеме, включающей средне- и низкотемпературную конверсию СО, метилдиэтаноламинную очистку, метанирование, систему использования теплоты и охлаждения вплоть до получения азотоводородной смеси стехиометрического состава для синтеза аммиака. Кроме того, технологическая схема, построенная по данному способу, позволяет сбалансировать производительность по аммиаку и диоксиду углерода для создания комплекса производств аммиак – карбамид путем извлечения диоксида углерода из части дымового газа под давлением технологического процесса.
Для этого в реактор вторичного риформинга подают смесь газов из реакторов 1 и 2, как описано в рассмотренном примере, а также смесь воздуха и дымового газа в соотношении 0,773/1. В результате получают синтез-газ со стехиометрическим соотношением для синтеза аммиака следующего состава, % об.: H2 – 74,00, N2 –24,64, Ar – 0,353, СН4 – 0,673.
Реализация способа получения синтез-газа по данному методу дает возможность создать производство аммиака со следующими показателями:
1. Энергопотребление. Природный газ: нм3/ч: топливо (23 %), на технологию – 77 %, итого: 798 нм3 (856,46 ст. м3, 760 мм рт. ст,, 20 оС) на 1 ту аммиака.
При низшей теплотворной способности (по метану) 7969,29 ккал/ст. м3 энергопотребление по природному газу составит 6,825 Гкал/т NH3. Лучшая мировая технология дает энергопотребление по природному газу 881,12…918 нм3 или 7,1…7,4 Гкал на 1 т аммиака;
2. Экологическая составляющая. Выбросы дымового газа в атмосферу – 2420 нм3 на 1 т NH3. У лучшей из известных технологий с температурой подогрева воздуха горения до 440…600 оС – 2660 нм3 на 1 т NH3, у наиболее распространенной стандартной схемы – 4470 нм3 на 1 т NH3 или в 1,847 раза больше.
Технологическая схема получения синтез-газа для производства водорода отличается от описанной тем, что в автотермический реактор вторичного риформинга вместо смеси воздуха и дымового газа подают только воздух или окислитель (например, чистый кислород), Кроме того, конвертированный газ с оптимальными параметрами аммиачного агрегата может быть непосредственно использован для получения водорода путем выделения его методами короткоцикловой адсорбции
Реализация предложенного способа получения синтез-газа даёт возможность создать производство водорода со следующими показателями:
1. Энергопотребление. Природный газ (в пересчете на метан) – 388,3нм3 на 1000 нм3 Н2. Энергетический эквивалент – 3,153 Гкал/1000 нм3 Н2. Известные мировые технологии – 484,3…496,4 нм3 на 1000 нм3 Н2, или в 1,247 раза больше.
2. Экологическая составляющая. Выбросы дымового газа в атмосферу – 1254 нм3 на 1000 нм3 природного газа или на ~25 % меньше, чем в известных технологиях.
Для получения синтез-газа, пригодного для производства спиртов и альдегидов, а также синтетических жидких углеводородов в автотермический реактор подают газ из реакторов 1 и 2, как описано в унифицированной схеме производства аммиака, а также смесь диоксида углерода и кислорода. При этом стадию конверсии оксида углерода с водяным паром используют для поддержания требуемого соотношения Н2/СО.
Список литературы
- Гартман В.Л., Обысов А.В., Дульнев А.В., Афанасьев С.В. Новая базовая форма катализаторов для реакторов конверсии углеводородов//Катализ в промышленности (Сatalysis in Industry). 2012. № 3. С. 57–61.
- Сергеев С.П., Майдуров Н.П., Афанасьев С.В., Рощенко О.С. Теплообмен и гидравлика для течения газа в подъемной трубе трубчатой печи первичного риформинга//Химическая промышленность сегодня. 2014. №4. С. 35–41.
- Обысов А.В., Круглова М.А., Дульнев А.В., Афанасьев С.В. Разработка высокоэффективного катализатора для процессов очистки технологических газов//Тезисы докладов II Российского конгресса по катализу «Роскатализ». 2–5 октября 2014. Самара, Т. 2. С. 150.
- Патент РФ 2535826. Способ получения синтез-газа паровой конверсией углеводородов.
- Афанасьев С.В., Рощенко О.С., Дульнев А.В., Обысов А.В. Влияние типа катализатора на надежность работы печей риформинга агрегатов аммиака// Вектор науки Тольяттинского государственного университета. 2011. № 4 (18). С. 25–28.
- Патент РФ 2357919. Способ получения синтез-газа, обогащенного водородом и монооксидом углерода, путем каталитического риформинга углеводородсодержащего сырья.
- Афанасьев С.В., Трифонов К.И. Физико-химические процессы в техносфере. Учебник. Самара: Изд-во Сам. Научн. центра РАН, 2014. 195 с.
- Афанасьев С.В., Сергеев С.П. Каталитический способ получения синтез-газа паровой конверсией углеводородов// Материалы межд. научно-прак. Конф. «Нефтегазопереработка-2017». Уфа, 23 мая 2017. ГУП Институт нефтепереработки РБ. 2017. С. 21–22.
- Афанасьев С.В., Рощенко О.С., Сергеев С.П. Технология получения синтез-газа паровой конверсией углеводородов// Химическая техника. 2016. № 6. С. 30–32.
- Патент РФ 2664526. Энергосберегающий унифицированный способ генерации синтез-газа из углеводородов.