Авторы: Г.С. Яицких, С.С.Демченко, К.П.Кулаков (АО «ИПН»);
М.Н. Потылицын, А.В. Кабаев (ООО «СТИМ»)
Опубликовано на портале «Химическая техника», март 2025
В последние годы в большинстве стран наблюдается значительный рост цен на энергоносители, связанный с переделкой мирового рынка углеводородов. Это негативно сказывается на экономике многих промышленных предприятий, особенно стран –импортёров нефти и газа. Многие предприятия сокращают объёмы производства, сотни закрываются. Пока в меньшей степени, но всё-таки это сказывается и на заводах, расположенных в странах – экспортёрах углеводородов, хотя со временем этот негативный эффект по объективным причинам будет возрастать. Своевременно принятые меры по сокращению потребления энергоносителей в производственных процессах могут позволить обеспечить профитабельность промышленных предприятий и победить в конкурентной борьбе.
Сегодня в России на заводах по переработке нефти и газа, химических производствах удельное потребление энергоносителей значительно превышает этот показатель у аналогичных предприятий технологически более развитых стран (в среднем на 20–40%). Сегодня на большинстве предприятий созданы и функционируют департаменты повышения операционной эффективности, которые разрабатывают и реализуют некоторые мероприятия повышения энергоэффективности производств. Однако, как показывает практика, зачастую отдельные мероприятия далеко не в полном объёме позволяют реализовать имеющиеся потенциальные технические возможности и лишь частично решают проблему оптимизации энергопотребления.
Высокий уровень энергоэффективности технологических установок должен закладываться уже на стадии проектирования новых производств или реконструкции старых.
Примечательно, что при разработке заданий на проектирование новых производств в России заказчиками за последние 30 лет ни разу не прописывались требования, лимитирующие удельные (на 1 т сырья или 1 т товарной продукции) расходы топлива, электроэнергии, водяного пара, оборотной воды и др. По этим «неполноценным» заданиям производились и производятся конкурсные процедуры выбора проектной организации без учёта основных технических, технологических и конструктивных решений будущей установки, которые может предложить тот или иной участвующий в конкурсных процедурах контрагент-проектировщик с целью оптимизации капиталовложений и минимизации эксплуатационных затрат. В некоторых случаях заказчик просит просто повторить проект 30–40-летней давности и выбирает проектировщика по минимально предложенной цене выполнения проектных работ. Зачастую, экономя всего несколько десятков миллионов рублей на проектировании, например, при строительстве установки ЭЛОУ-АТ мощностью 3 млн. т в год, заказчик, выбрав дешёвую, но недостаточно компетентную в части современного оборудования и современных технологических решений проектную организацию, может переплатить на стадии строительства ориентировочно 1…1,2 млрд. руб., а потом переплачивать ежегодно по 600…800 млн. руб. за перерасход энергоносителей. К сожалению, это типичная стратегическая ошибка инвесторов-застройщиков.
Почему это происходит?
В условиях рынка движение финансовых потоков промышленных предприятий, операционные затраты, стоимости сырья, товарной продукции, энергоносителей и другая информация являются коммерческой тайной и зачастую у технических специалистов заводов нет возможности проанализировать, сравнить энергетическую и экономическую эффективность работы собственной технологической установки с аналогичными установками конкурирующих предприятий. А ведь нередко неиспользованный потенциал снижения эксплуатационных затрат на производство реально составляет до 600…800 млн. руб. в год только на покупку энергоносителей и только на одну из технологических установок завода! В этом неоднократно убеждались заказчики АО «ИПН» после выполнения многочисленных работ по техперевооружению старых технологических установок, когда после реконструкции установок на 20–40% снижалось потребление энергоресурсов.
Что делать?
Давно пора при проведении конкурсов на выполнение проектных работ делать следующее:
- В задания на проектирование новых технологических установок или реконструкцию старых вводить требования по предельным удельным расходам энергоносителей – топлива, электроэнергии, водяного пара, оборотной воды (или работа без оборотной воды) и др.;
- На стадии рассмотрения технической части предложений претендентов на выполнение проектных работ учитывать умение и практический опыт применения претендентом креативных современных и надёжных технических решений, собственных запатентованных разработок, которые обеспечат оптимальные капиталовложения и минимальные операционные затраты, в частности на энергоносители;
- Только после отбора наилучших технических предложений, приступать к оценке стоимости проектных работ отобранных в первом туре претендентов.
Основные технические решения, обеспечивающие энергоэффективность технологической установки
Наибольшая энергоэффективность технологической установки может быть достигнута только применением комплекса следующих технологических и технических решений:
- оптимизация схемы теплообмена;
- минимизация или отказ от использования оборотной воды;
- минимизация применения воздушных холодильников, затрат электроэнергии на вентиляторы;
- максимально возможное использование холодного потенциала сырья для финишного охлаждения нефтепродуктов;
- частотное регулирование электроприводов насосов и вентиляторов;
- использование «бросового» тепла технологических установок для технических и бытовых нужд;
- применение современного и надёжного теплообменного оборудования;
- применение эффективных и энергетически экономичных электродегидраторов;
- применение колонн с вертикальной разделительной стенкой (DWC колонны) вместо устаревших конструкций ректификационных колонн прошлого века.
Приступая к разработке технологической схемы установки, необходимо иметь в виду, что удельные затраты на охлаждение нефтяных фракций (продуктов, полупродуктов) на выходе с установки в денежном эквиваленте нередко могут превосходить удельные затраты на нагрев сырья в начальной стадии технологического процесса. В связи с этим нужно стремиться к тому, чтобы в первую очередь максимально использовать тепло выводимых с установки потоков для нагрева сырья, с одной стороны, и максимально использовать относительно низкую температуру сырья на установках. В частности, на установках ЭЛОУ-АВТ, ЭЛОУ-АТ для охлаждения и конденсации паров бензина с верха ректификационных колонн АО «ИПН» в своих работах вместо оборотной воды применяет нефть температурой 18…24 оС для охлаждения бензиновых фракций [1].
Это техническое решение позволяет:
- исключить капиталовложения на строительство градирни и операционные расходы на её эксплуатацию;
- уменьшить потребность в свежей воде на технологические нужды;
- снизить операционные затраты на очистку сточных вод;
- экономить электроэнергию на воздушных холодильниках;
- значительно снизить нагрузку на печи нагрева сырья (в отдельных случаях до 40%) за счёт дополнительной утилизации тепла, а также уменьшить затраты на топливо и плату за загрязнение окружающей среды (уменьшение объёмов дымовых газов).
Применение эффективных электродегидраторов производства ООО «ЭК ЭИП», оборудованных экономичной системой электропитания ИПМ-35/15 (25/15), позволяет снизить удельное потребление электроэнергии до 0,02…0,05 КВт ч на 1 т нефти, что в 3–5 раз меньше по сравнению с другими аналогами.
В последнее время всё большее применение в производственных процессах находят установки с вертикальной разделительной стенкой (DWC колонны). Данная технология не является новой, первые колонны DWC начали внедрять в производство еще в 1980-х годах прошлого столетия. Пионером данной технологии является компания BASF, которая до 2000 года внедрила около ста DWC колонн на свои производства. В начале 2000-х годов к разработке решений по применению колонн DWC активно подключились такие компании как Sulzer, Koch-Glitsch, Lurgi и многие другие. В результате в период с 2000 по 2010 год было внедрено еще 200 колонн DWC, а самая большая колонна DWC для процесса Фишера–Тропша на заводе Sasol в ЮАР имеет диаметр 5200 мм и высоту 102 м. Таким образом, в мире сейчас не существует каких-либо технических преград по внедрению колонн DWC в различные технологические процессы.
DWC колонны имеют ряд преимуществ перед двухколонной схемой:
- снижение капитальных затрат на 30–40%;
- снижение эксплуатационных затрат на 25-40%;
- увеличение числа теоретических ступеней контакта до 40%;
- уменьшение площади установки до 40%;
- снижение выбросов вредных газов за счет экономии топлива, что в свою очередь позволяет уменьшить размеры санитарно-защитной зоны предприятия.
В настоящее время DWC колонны применяются более чем в 100 различных технологических процессах. В нефтепереработке колонны DWC нашли свое применение в следующих процессах: каталитический крекинг, риформинг бензинов, ректификация ароматических углеводородов, изомеризация легких углеводородов. В процессе изомеризации легких углеводородов применение в схеме колонны DWC позволяет не только снизить энергопотребление (эксплуатационные затраты), но и повысить октановое число изомеризата на 2–3 пункта, что позволяет НПЗ увеличить выпуск высокооктановых бензинов.
АО «ИПН» имеет все необходимые компетенции для выполнения проектов различных технологических установок с применением DWC колонн. В 2024 г. специалисты АО «ИПН» разработали и запатентовали технологический процесс отпарки кислых стоков в DWC колонне вместо двухколонной схемы [2].
На экономические показатели технологической установки в значительной степени влияет правильный выбор типа применяемого теплообменного оборудования. Широко используемые на старых технологических установках кожухотрубные теплообменники с гладкими трубными пучками в последние годы уступают место более современным по конструкции и эксплуатационным характеристикам кожухотрубным теплообменникам с витыми трубными пучками, поставляемые ООО «СТИМ» (рис. 1).
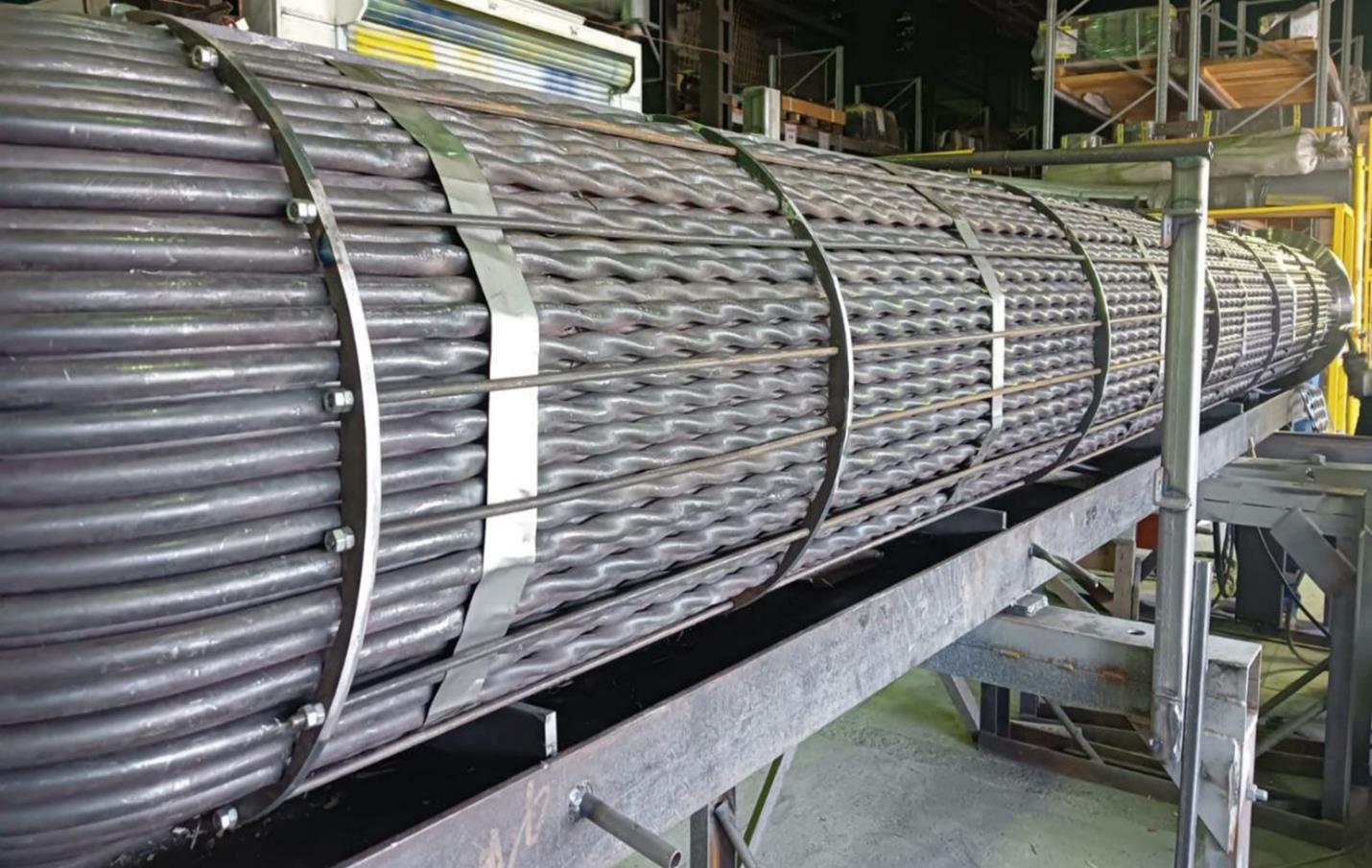
Такое конструктивное решение пучка отвечает всем требованиям к современному теплообменному оборудованию, что позволяет решать следующие ключевые задачи:
- значительно снизить капитальные затраты и затраты в процессе эксплуатации теплообменного оборудования;
- повысить эффективность теплообмена за счет более высокого значения коэффициента теплопередачи;
- высокую надежность и качество теплообменных аппаратов;
- возможность модернизации существующего оборудования без изменения обвязки путем замены трубных пучков с улучшением рабочих характеристик (повышение мощности, снижение гидравлических потерь, увеличение цикла непрерывной работы).
Указанные преимущества технологии витых труб дают возможность повышения производственных показателей и надежности теплообменной аппаратуры при одновременном сокращении капитальных и производственных затрат. Необходимо отметить, что данные аппараты успешно зарекомендовали себя на нефтеперерабатывающих предприятиях Российской Федерации и обеспечивают заданные характеристики и заявленные эффекты при эксплуатации на производственных объектах.
На рис. 2 приведена оценка эффективности витых труб (ТВТ) по сравнению с гладкими трубами (ГТ).
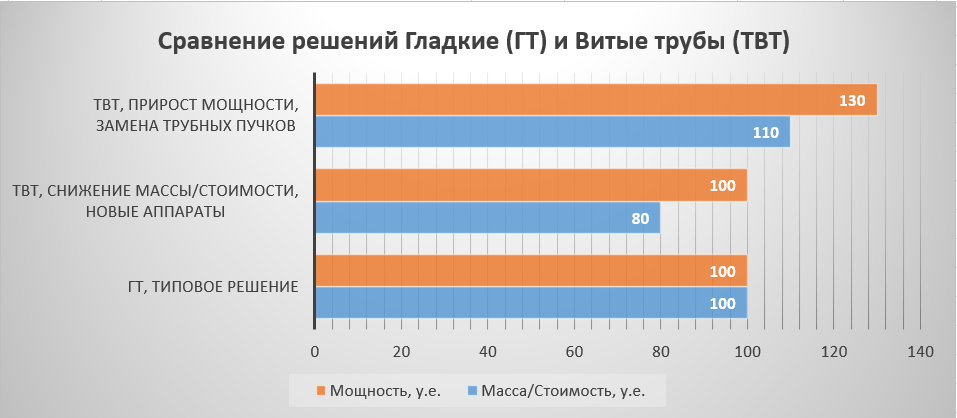
Еще одним эффективным решением для нефтеперерабатывающих и промышленных предприятий являются проволочные интенсификаторы (ПИ), обеспечивающие повышение эффективности кожухотрубных теплообменников и аппаратов воздушного охлаждения (рис. 3).
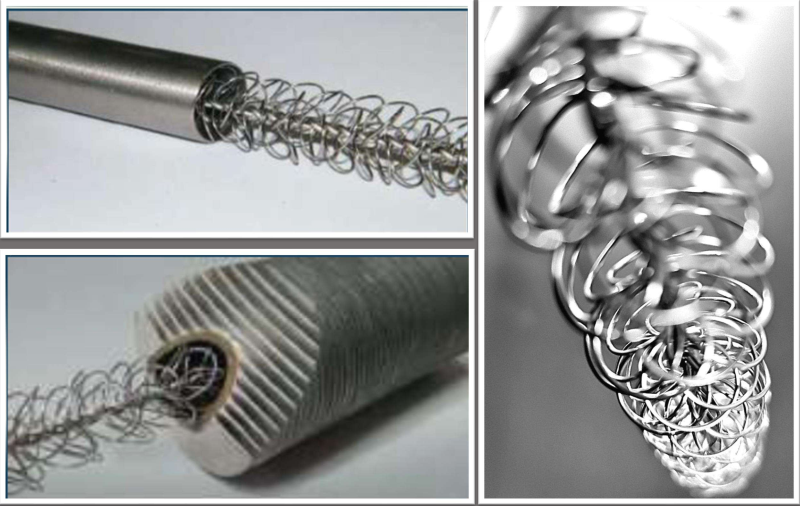
Применение ПИ позволяет:
- увеличить коэффициент теплопередачи со стороны труб;
- создать турбулентный поток внутри труб и тем самым значительно повысить стойкость против загрязнений, а также обеспечить длительный, стабильный температурный график;
- уменьшить массогабаритные характеристики при проектировании и изготовлении нового оборудования, что позволяет снизить капитальные затраты при новом строительстве, а также в проектах модернизации предприятий и установок;
- сократить затраты на энергоресурсы, а в некоторых случаях увеличить выработку готовой продукции в результате увеличение доли конденсации паров углеводородов на выходе из ректификационных колонн и последующего более глубокого охлаждения потока, особенно в летний период времени.
Представленные технические решения и отдельные виды оборудования в комплексе позволяют проектировать новые технологические установки и реконструировать старые, достигая каждый раз всё более высокого уровня технико-экономических показателей при реализации новых проектов. Повторение технологических схем установок прошлого века, использование старого малоэффективного технологического оборудования в новых проектах неизбежно приводит к многомиллиардным убыткам предприятий в ближайшей перспективе.
Список литературы
- Пат. на изобретение АО «ИПН» RU 2581360 «Установка первичной перегонки нефти».
- Пат. на изобретение АО «ИПН» RU 2824117 «Способ отпарки кислой воды в ректификационной колонне с вертикальной разделительной стенкой».