Авторы: И.Л. Золотарев, В.Р. Ржевкин, А.Б. Самохвалов (ООО «ДИАПАК»), Е.И. Копалиди (OOO «ЛУКОЙЛ-НИЖЕГОРОДНЕФТЕОРГСИНТЕЗ»).
Опубликовано в журнале Химическая техника №3/2015
Для управления планами обследований оборудования и оценки результатов обследований требуется огромное количество данных. Программное обеспечение контроля оборудования на базе рисков разработано специально для управления надежностью и предназначено для различных отраслей промышленности, где особенно актуально снижение риска аварий, в первую очередь нефтеперерабатывающей и нефтехимической. Одним из мировых лидеров программного обеспечения (ПО) такого рода является программный пакет PCMS (Plant Conditions Management Software), который позволяет собирать, анализировать, упорядочивать и документировать информацию об оборудовании завода, необходимую для поддержания работоспособности оборудования и создания планов будущих обследований, исходя из трех принципов планирования:
- на базе фиксированных интервалов обследований (традиционный метод);
- на базе расчетов скоростей коррозии и оценок ресурса;
- на базе оценки рисков (RBI).
ПО представляет собой реляционную базу данных, в которую записываются и затем анализируются данные по обследованиям оборудования; определяются скорости коррозии, даты последующих обследований, предельные сроки снятия с эксплуатации; обозначаются подозрительные области, нуждающиеся в дополнительных обследованиях.
В ПО также входят внутренние таблицы, перечни и справочники, отражающие международные и национальные стандарты, например, таблицы механических параметров марок сталей, свойства жидкостей, газов и др.
Ключевые структурные модули ПО
Модуль контроля коррозии является средством для записи, хранения и анализа информации о коррозионном состоянии оборудования.
Функции модуля:
- анализирует коррозионное состояние оборудования с целью предотвращения незапланированных остановок и аварий;
- документирует изменение толщин стенок;
- вычисляет минимально допустимую толщину стенки компонентов оборудования различных геометрических форм (калькулятор Тмин) на базе стандартов ANSI, ASME, API, E N и ГОСТ;
- дает оценку общей и локальной коррозии;
- указывает проблемные области, чтобы сузить круг проведения обследований;
- вычисляет сроки будущих обследований на основе многоуровневого анализа;
- устанавливает, вычисляет и документирует сроки вывода из эксплуатации.
Модуль позволяет выявить проблемные области и места мониторинга состояния (в частности, места замеров толщин), которые наиболее близки к пределу отбраковки.
Модуль оценки рисков (RBI). Основная цель RBI – гарантировать безопасность и надежность оборудования в условиях увеличенного пробега установок. Подход RBI фокусирует внимание на оборудовании и механизмах изнашивания, представляющих наибольший риск для эксплуатации. Путем оценки рисков и способов их снижения подход RBI реализует жесткую связь между механизмами, которые приводят к отказам оборудования, и планированием обследований, которые приводят к снижению риска.
База данных обследований, предоставляет текущую информацию о скорости коррозии, которая оценивается количественно при анализе RBI. Эти данные, связанные с оценками вероятности отказа и его последствиями, обеспечивают систематическое отслеживание риска.
Когда данные оценок по методике RBI изменяются, ПО автоматически обновляет события и расписания.
Оценки RBI соответствуют нормам API 571 и API 581.
Как известно, риск определяется как произведение вероятности события (в нашем случае – отказа) на последствия (обычно выражаемые в денежном эквиваленте): R = PC, где P – вероятность отказа; C – последствия отказа.
Рассмотрим подробнее оба этих параметра, определяющие риск.
Последствия. Оценка последствий нарушения целостности оборудования базируется на оценке экономических последствий, последствий для здоровья и экологических последствий.
Общие последствия = Экономические последствия + Последствия для здоровья людей + Ущерб окружающей среде.
Основным фактором экономических последствий являются потери от простоя, которые, как правило, превышают потери на затраты по ремонту. В ПО вводится параметр снижения производительности установки при ремонте в процентах, а также число дней, требующихся для ремонта, которые определяют потери продукции за счет простоя.
Таким образом:
Экономические последствия = = Число дней ремонта × Прибыль (в сутки) × Снижение производительности при ремонте.
Ущерб окружающей среде оценивают по количеству технологической среды, содержащейся в оборудовании, и ее составу. В таблице свойств технологических сред ПО отыскивается показатель токсичности для окружающей среды для каждого компонента жидкости (газа), содержащегося в технологическом потоке. Количество среды, которое может быть выброшено из оборудования рассчитывается как
Объем выброса = Объем оборудования × Плотность компонента × Процентное содержание компонента.
В значение объема оборудования вводится количественный коэффициент выброса. Если количественный коэффициент выброса не задан, то считается, что среда из оборудования выбрасывается полностью.
Предусматриваются три уровня токсичности для окружающей среды: высокий, средний и низкий. ПО группирует все компоненты технологической среды по уровню воздействия на окружающую среду, суммирует запасы по всем трем уровням, затем рассчитывает величину последствий.
Последствия для здоровья людей оценивают по худшему из трех сценариев аварийности: «Токсичный выброс», «Пожар» и «Взрыв паров».
Сценарий токсичного выброса рассчитывается исходя из характеристик потока среды и ее концентрации. Если поток является много компонентным, то ПО сначала рассчитывает сценарий выброса токсичности для каждого компонента, затем суммирует их и пересчитывает в денежное выражение.
Сценарий пожара базируется на характеристиках возгорания, а также на запасе технологической среды.
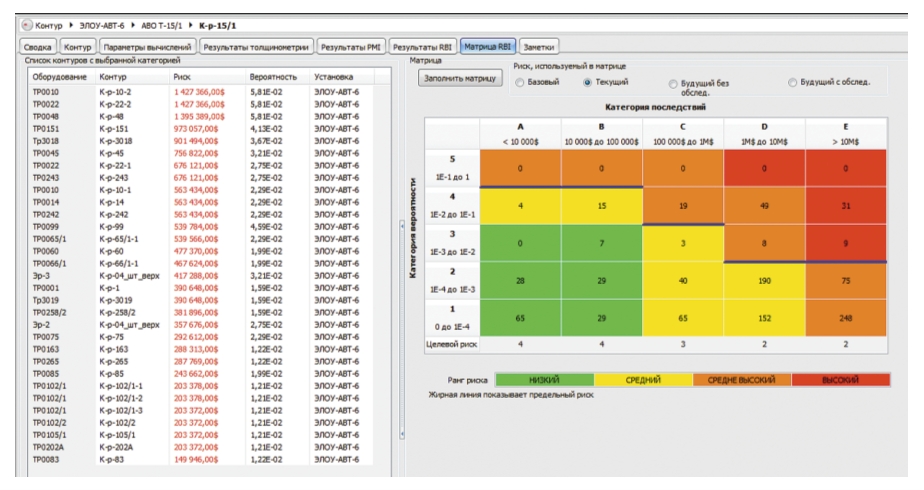
Если поток является многокомпонентным, то ПО сначала группирует все компоненты технологической среды по уровню возгораемости, суммирует запасы по всем трем уровням (низкому, среднему и высокому), а затем оценивает сценарий воспламеняемости и рассчитывает величину последствий.
Сценарий взрыва паров анализируется путем оценки запасов, скорости испарения и класса горючести технологической среды. Если технологическая среда является многокомпонентной, то все компоненты группируются по классу взрыва, суммируются запасы по всем уровням (низкому, среднему и высокому), затем оценивается сценарий взрыва парового облака и рассчитывается величина последствий.
Вероятность отказа. Для расчета вероятности отказа используются обобщенные вероятности разрушения из стандарта API 581 с модифицирующими коэффициентами («подфакторами»), учитывающими скорость развития поврежденности или восприимчивости материала к определенным механизмам разрушения.
База данных обобщенных вероятностей разрушения основана на анализе и сборе всех доступных записей из истории отказов оборудования. Данные записи могут быть получены из различных источников.
Обобщенная частота отказов оценивается на основе данных по каждому типу оборудования и для каждого диаметра трубопроводов. «Технический» подфактор – его оценка базируется на анализе механизмов разрушения, описанных в стандарте API 571. Кроме того, используются некоторые подробные модели, приведенные в API 581 и в методике Tischuk T-OCA.
Механизмы разрушения сгруппированы по четырем категориям разрушения:
- FIT – внутренняя потеря толщины;
- FET – внешняя потеря толщины;
- FEC – растрескивание, вызванное средой;
- FMF – металлургическое и механическое разрушение.
Технический подфактор рассчитывается для каждой категории разрушения. ПО по определенным правилам отфильтровывает те механизмы повреждения, к которым материал не является восприимчивым, и затем рассчитывает технический подфактор для каждого действующего механизма. Результирующий технический подфактор для каждого повреждения принимается равным максимальному подфактору, определенному из анализа действующих механизмов повреждения.
Наконец, технический подфактор принимается равным максимальному подфактору, определенному для четырех категорий режимов повреждения: FT = Max (FIT, FET, FEC, FMF).
Окончательная вероятность отказа определяется как произведение обобщенной частоты отказа на технический подфактор.
Когда вероятности и последствия аварий становятся критичными, заказчики могут соответственно повысить критерии обследований, снизив тем самым текущий риск.
Процесс RBI устанавливает критичность состояния каждого оборудования, которая ранжируется соответственно по вероятности возник новения отказа и величины последствий этого отказа. Таким образом, формируется матрица рисков, пример которой представлен на рисунке.
Синяя линия на матрице обозначает предельный риск. Оборудование, попавшее в ячейки выше синей линии, является критичным и для снижения риска отказа такого оборудования необходимо проведение обследования, в результате которого будет выявлено истинное состояние.
Планы обследований автоматически обновляются, предоставляя пользователю полную картину истории обследований как традиционных, так и основанных на анализе риска. С помощью ПО можно легко проследить процесс обследований и определить сроки обследований на основе анализа риска или на базе традиционных методик.
Несколькими щелчками мыши пользователь может выбрать, проверить и обновить информацию RBI:
- установить приоритет обследований на базе рисков;
- определить соответствующий план обследований, основанный на традиционных методиках или на данных анализа риска;
- сфокусировать усилия персонала на объектах наибольшего риска, согласно данным RBI;
- уменьшить время простоя благодаря сниженияю объемов обследований объектов меньшего риска.
Модуль обследований обеспечивает организованный подход к сбору данных, оценке, документированию и планированию визуальных и инструментальных обследований. Модуль содержит архив данных всех обследований любой единицы оборудования, включая прикрепленные документы и рекомендации. Основные функции модуля следующие:
- отслеживает и сохраняет историю обследований вместе с вносимыми изменениями в конструкцию и заменами оборудования завода;
- устанавливает уровни утверждений обследований различного типа;
- создает стандартизованные листы проверок и полную отчетность;
- отслеживает заявки/выполнение ремонтов, рекомендаций и генерирует напоминания о необходимости обследований и обслуживаний;
- вычисляет даты следующих обследований на базе заложенных в систему принципов;
- составляет расписания обследований, используя данные нормативных документов.
Если в результате обследования потребуется проведение ремонтных работ, то в рамках ПО может быть создан автоматизированный запрос в информационную систему SAP на их проведение и сопровождения для «замыкания цикла между обследованием и обслуживанием». К запросам на обслуживание могут быть присоединены отчеты, чертежи, фотографии, и др.
Подробные технологические карты обследований легко могут быть созданы в PCMS и использованы при проведении обследований. Можно распечатать бланки контрольных листов обследований либо вывести подробные формы на дисплей.
Следует отметить, что планирование на основе риска по методик RBI для большинства оборудования показывает более позднюю дату следующего обследования, чем дата по установленным нормативам; для критичного оборудования с высоким риском аварии дата обследования по RBI значительно ближе, чем требуемая по нормативам. Таким образом, если следовать рекомендациям RBI, то можно сконцентрировать ресурсы на наиболее критичных объектах и получить экономию средств при снижении риска аварии.
Модуль связи PCMS с SAP включает два подмодуля: «Синхронизация оборудования» и «Заявки на Работы».
С помощью «Синхронизации оборудования» можно «централизовать» все данные по оборудованию. Изменения, сделанные в SAP по функциональному расположению и параметрам оборудования, автоматически отображаются в ПО.
Контроль «Заявок на Работы» (ЗНР) помогает замкнуть цикл между обследованиями и обслуживанием.
Связь по ЗНР позволяет убедиться в том, что работы по обслуживанию закончены, прежде чем оборудование будет пущено в эксплуатацию.
Связь с SAP обеспечивается в реальном масштабе времени и дает следующие преимущества:
- предотвращает двойной ввод данных об оборудовании и ЗНР в ПО и SAP;
- хранит историю обследований, подготавливает даты будущих обследований, наряды на работы SAP;
- состояние ЗНР, обрабатываемых внутри SAP, постоянно обновляется в ПО: таким образом, обследования не могут быть утверждены, прежде чем все работы будут закончены.
Дополнительные модули ПО
Помимо обсужденных основных модулей программы, определяющих ее функциональное назначение, существует ряд дополнительных сервисных модулей:
Модуль «Импорт/Экспорт» данных позволяет выгружать/загружать данные из/в ПО из программ общего назначения, таких, как Microsoft Excel, Microsoft Access, что обеспечивает удобство при манипуляциях с большими объемами данных и их проверку;
Модуль «Отчет» – мощное средство создания разнообразных отчетов, перерабатывающее огромное количество данных для создания планов обследований на основе различных критериев, а также наглядно показывающее состояние и параметры оборудования;
Модуль «Связь с AutoCAD» используется для автоматического отображения текущих данных по коррозии на эскизах оборудования и трубопроводов. Цифровые данные, отображенные на эскизах, автоматически изменяются при их изменении в базе данных ПО;
Модуль «Права пользователей» – PCMS имеет детализованную структуру доступа пользователей к данным. Программа дает возможность владельцу определить уровни доступа (права) к тем или иным данным и затем присвоить эти права определенным пользователям. Разграничение прав может касаться отдельных технологических установок и единиц оборудования, а также типов оборудования;
Модуль «Аудит» позволяет регистрировать все сделанные изменения в базе данных PCMS с указанием даты и пользователя, сделавшего эти изменения.
Опыт внедрения PCMS на российских предприятиях
Специалистами ООО «ДИАПАК» совместно со специалистами крупнейших российских нефтеперерабатывающих предприятий проделана большая работа по внедрению систем управления надежностью оборудования на основе оценки рисков с использованием специального программного обеспечения PCMS.
Внедрение началось в 2009 г. с пилотного проекта в ООО «ЛУКОЙЛ-Нижегороднефтеоргсинтез», С тех пор системы внедрены на всех российских и болгарском нефтегазоперерабатывающих заводах ОАО «ЛУ-КОЙЛ», а также на Московском НПЗОАО «Газпром нефть» (ОАО «Газпром нефть–МНПЗ»).
Опыт внедрения в компании «ЛУКОЙЛ». В 2009 г. в ООО «ЛУКОЙЛ-Нижегороднефтеоргсинтез» в целях повышения надежности работы статического оборудования, работающего под избыточным давлением, было реализовано в качестве одного из решений внедрение системы управления рисками и надежностью оборудования (СУРНО) на базе методологии инспектирования статического оборудования с учетом факторов риска (RBI).
Поскольку подобного рода решение преследует многоступенчатые цели в рамках одной программы, для достижения планируемой эффективности в масштабах компании в целом, а не одного отдельного предприятия, методология RBI была поэтапно внедрена практически на всех НПЗ, ГПЗ ННХП группы «ЛУКОЙЛ».
Система СУРНО построила тесные взаимосвязи между подразделениями внутри предприятий отрасли для достижения на высоком уровне показателей по надежной и безаварийной работе поднадзорного оборудования в течение его расчетного срока эксплуатации.
Безусловно, для достижения желаемого результата уже сейчас ведется сложная и достаточно кропотливая работа в этом направлении, в которой главным образом задействованы отделы технического надзора на каждом предприятии. Привлечены и обучены лучшие специалисты по направлениям деятельности в рамках своей компетенции.
Сегодня можно сказать, что на начальном этапе внедрения указанной методологии система СУРНО позволила начать формировать эффективную стратегию технического обслуживания статического оборудования с учетом действующих норм и правил в области технического диагностирования (освидетельствования) поднадзорного оборудования.
Данная стратегия заключается в эффективном планировании необходимого объема обследований и применения эффективных методов контроля для статического оборудования в нужное время и в нужном месте, основываясь на критичности оборудования и последствиях отказа его работоспособности.
Выстраиваемая таким образом стратегия позволила более объективно подойти к реализации программ по техническому освидетельствованию статического оборудования, применяемых на опасных промышленных объектах компании.
Если говорить в целом, то данная стратегия позволила выявлять дефекты, которые имели тенденцию проявляться на протяжении определенного периода эксплуатации или в течение всего периода в определенных местах, обусловленных сложностью технологического процесса, спецификой работы технического устройства, агрессивностью технологической среды.
Достаточно эффективно данная методология показала себя на введенных в эксплуатацию новых процессах переработки углеводородного сырья, где отсутствовали по понятным причинам история ремонтов этих технологических объектов и понимание того, где и как необходимо в ближайший первый капитальный ремонт искать возможные проявления развивающихся дефектов. Внедрение позволило запланировать действенные мероприятия по выявлению дефектов на основании полученных рекомендаций по RBI-анализу, который проводился заблаговременно до начала ремонта, чтобы иметь возможность реализовать программу надежности на малоизученных процессах переработки углеводородного сырья.
Преимущества и смысл применения методологии RBI
Промышленность сталкивается со все более жесткими правилами по безопасности, защите окружающей среды и механической целостности оборудования. RBI является решающим фактором управления эксплуатационным риском с помощью эффективной технологии и наилучшего планирования обследований и обслуживаний. Подход RBI дает наивысшую выгоду среди других методологий обследований. RBI позволяет существенно снизить затраты на обслуживание и в то же время увеличить надежность завода.
Смещение усилий по излишним обследованиям некритичного оборудования в сторону критичного оборудования с более высоким риском обеспечивает снижение общего риска и увеличивает безопасность и надежность. Увеличение объема обследований в процессе эксплуатации снижает длительность остановок и их стоимость. Определяются возможности замены в некоторых случаях внутренних обследований менее дорогостоящими – наружными.
Методологии RBI позволяет определять действующие механизмы повреждений; получать информацию, подсказывающую стратегию замены оборудования; определять приоритетные усилия по обследованиям и обслуживанию, устанавливать возможность обоснованного выбора применяемых методов, сроков и объемов обследований.
Если соответствующие контролирующие органы понимают и принимают методологию RBI, то имеется возможность увеличения интервала обследований
Список литературы
- Лапкин С.А., Кузнецов С.Ю., Петерсен Т.Б., Ржевкин В.Р., Самохвалов А.Б. Анализ результатов применения программы RCMS/RBI на примере типовой технологической установки НПЗ. Проблемы эксплуатации оборудования и пути повышения надежности технологических установок риформинга, гидроочистки и гидрокрекинга. Материалы совещания. М.: ООО «НТЦ при Совете главных механиков». 2013.
- Ржевкин В.Р., Самохвалов А.Б., Шемякин В.В. PCMS – программное обеспечение для управления состоянием завода на основе оценки риска//В мире НК. 2012. №1 (55).