Автор: Д.С. Бирюков (ООО «ГК «ИНТРАТУЛ»).
Опубликовано в журнале Химическая техника №3/2018
Как и в любой сложной системе, в технологических процессах нефтепереработки и нефтехимии есть свои критические точки, в которых к элементам системы управления предъявляются повышенные требования по эксплуатационным параметрам, надежности и безопасности. Соответственно, сферу разработки и производства запорно-регулирующей арматуры (ЗРА) для таких применений принято называть критическим инжинирингом (critical engineering).
Как правило, производители ЗРА для критических применений ограничивают свою номенклатуру достаточно узким набором процессов и критических точек применимости, совершенствуя конструкцию механической и приводной части десятилетиями. В настоящей статье предлагается обзор четырех таких процессов и особенностей использования ЗРА в критических точках.
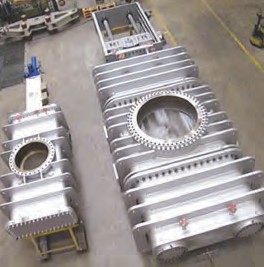
Среди процессов нефтепереработки рассмотрим два: замедленное коксование (delayed coking) и каталитический крекинг (catalytic cracking).
Процесс замедленного коксования в необогреваемых камерах предназначен для получения крупнокускового нефтяного кокса как основного целевого продукта, а также легкого и тяжелого газойлей, бензина и газа.
Сырьем для коксования служат малосернистые атмосферные и вакуумные нефтяные остатки, сланцевая смола, тяжелые нефти из битуминозных песков. Эти виды сырья дают губчатый кокс. Для получения высококачественного игольчатого кокса используют более термически стойкое ароматизированное сырье, например, смолу пиролиза, крекинг-остатки и каталитические газойли.
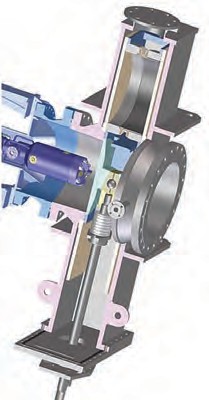
По мере заполнения коксовых камер готовым коксом производится процесс эвакуации кокса, в который вовлечены задвижки верхних и нижних люков, обеспечивающие безопасную и быструю очистку камер с помощью гидродолот и гидрорезаков высокого давления.
В конструкции задвижек коксовых камер исторически использовалась конструкция с запорным элементом в виде одного диска, что позволяло ограничить массу задвижки (до 35 т), но не обеспечивало в должной мере плотность затвора в закрытом положении. Более прогрессивная двухдисковая конструкция по сравнению с однодисковой обеспечивает низкий уровень потребления пара и увеличивает срок эксплуатации устройства. Давление пара в пространстве между двумя дисками позволяет создать дополнительное усилие уплотнения. При этом опасность для оператора исключается – все операции осуществляются удаленно посредством электрического или гидравлического привода. Размеры такой задвижки составляют порядка 7 м строительной длины, а масса 35…65 т.
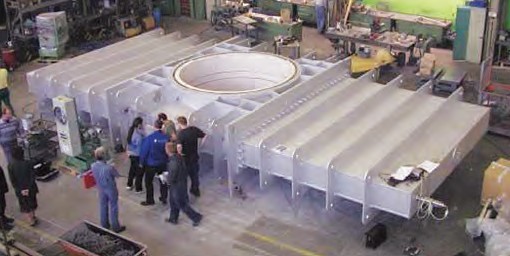
В ряде случаев используется и прогрессивная конструкция с интегрированным диском, позволяющая понизить массу до 42 т (применительно к тем же рабочим параметрам).
Еще более жесткие требования предъявляются к критическим узлам процесса флюид-каталитического крекинга – изолирующим очковым задвижкам для защиты персонала (для отсечения линии топливного газа или котла-утилизатора) и двухдисковым задвижкам отсечения реактора или фракционирующей колонны. Температура в этих точках процесса достигает 1100°С, а проходное сечение трубопровода – до 5000 мм. К тому же задвижкам приходится работать с газовой средой, содержащей частицы пыли и катализатора, что предъявляет повышенные требования к качеству уплотнительных поверхностей.
Производство олефинов, как правило, являющееся частью большого комплекса производства полиолефинов, включает разнообразные установки синтеза этилена и пропилена (пиролиза нефтяного сырья, каталитического крекинга вакуумного газойля, каталитического дегидрирования пропана-бутана и т.д.). Значительная часть всей мировой продукции пропилена (~35%) вырабатывается на предприятиях, где пропилен является побочным продуктом производства бензина и дистиллятов методом флюидкаталитического крекинга, а газы каткрекинга используются в качестве сырья.
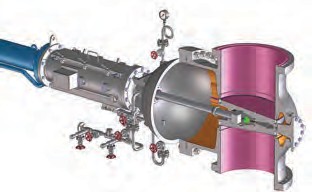
В процессе синтеза этилена ключевым моментом является непрерывность работы реактора, в котором осуществляется реакция крекинга углеводородов с помощью горячего пара. Реактор требует периодического раскоксовывания без остановки процесса, и здесь на помощь приходят разгрузочные двухдисковые полнопроходные задвижки. Фактически такой узел функционирует как две задвижки в одной (основная и резервная), обеспечивая непревзойденный уровень безопасности.
Для наплавки уплотнительных поверхностей задвижки используются сплавы высокой твердости, позволяющие использовать задвижку в течение трех лет без обслуживания.
При производстве пропилена методом каталитического дегидрирования пропана (процессы Catofin, STAR, Oleflex и др.) находят свое применение задвижки с раздвижным клином (wedge-within-wedge).
Эта конструкция исключает риск заклинивания дисков в экстремальных эксплуатационных условиях. При открытии сначала освобождается несамоблокирующийся внутренний клин, за счет чего освобождаются диски задвижки. Герметичность и упругость обеспечиваются за счет прижатия дисков шаром, расположенным между внутренними клиньями.
Следуя своей миссии – нести инновации для повышения эффективности производства – группа компаний INTRATOOL предоставляет своим клиентам комплексные решения по поставке специальной арматуры, запасных частей и сервисному обслуживанию. В сотрудничестве с ведущими производителями с более чем 100-летним опытом конструирования и производства ЗРА для критических применений наши специалисты готовы решать самые серьезные задачи по оснащению современных нефтехимических производств.
При подготовке статьи использованы материалы компаний IMI Z&J, Paul Wurth, Kubota.