Авторы: Д.Е. Васильев, В.Д. Чугаев, С.Л. Масякин, Р.А. Евсиков, А.В. Жулин (ОАО «НОРЭ»).
Опубликовано в журнале Химическая техника №12/2015
Крановые крюки на подъемных сооружениях (ПС) применяются в самых различных сферах производства. Изготавливают крюки методом ковки или горячей штамповки с последующей механической обработкой цилиндрического хвостовика и применяют на крюковых подвесках кранов всех типов в качестве грузозахватного органа.
Наибольшая грузоподъемность кранового крюка устанавливается в зависимости от режима работы: легкого, среднего или тяжелого. Согласно грузоподъемности, крюки разделяются по нумерации от 1 (250 кг) до 26 (100 000 кг) и способу изготовления: типа А – с коротким хвостовиком и типа Б – с длинным хвостовиком (рис. 1).
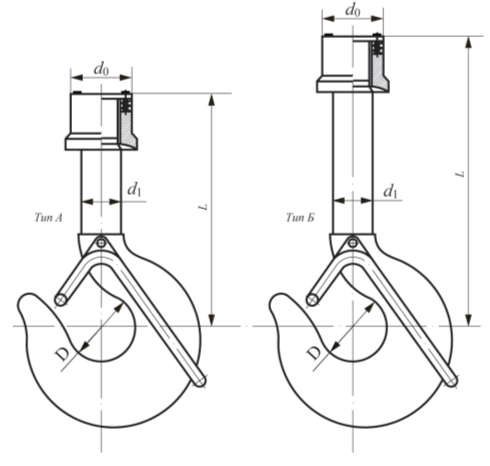
Типы А и Б в свою очередь могут быть двух исполнений: исполнение 1 – без прилива и исполнение 2 – с приливом (рис. 2).
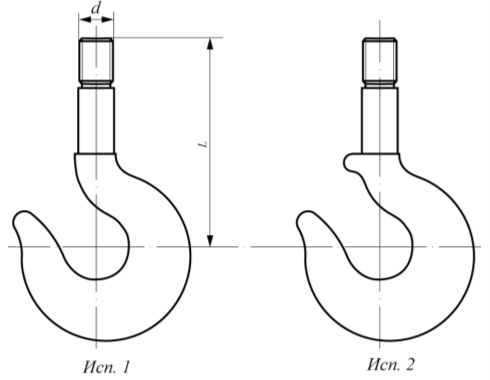
Крюки и другие грузозахватные органы должны соответствовать паспортным характеристикам и иметь соответствующие маркировки заводов-изготовителей [1].
При контроле крюков ПС используются следующие методы неразрушающего контроля: визуальный, измерительный, магнитопорошковый, ультразвуковой, цветной дефектоскопии (табл. 1).
Таблица 1
Деталь | Метод контроля | Возможные дефекты в зонах контроля |
Крюк | ВИК, УЗК,
Магнитопорошковый, Капиллярный |
Трещины любого характера
и расположения Износ зева крюка Износ отверстия под палец крюка |
Ось крюка | ВИК, УЗК,
Магнитопорошковый, Капиллярный |
Трещины любого характера и расположения. Трещины в зоне отверстий
Износ поверхности по диаметру |
Методы контроля выбирают из условия наиболее надежного обнаружения возможных дефектов.
Визуальный и измерительный контроль обязательны, они позволяют выявлять наиболее часто встречающиеся поверхностные дефекты.
Измерительный контроль кранового крюка выполняют с целью определения соответствия геометрических размеров конструкций и допустимости повреждений материала, выявленных при визуальном контроле, требованиям рабочих чертежей, ТУ, стандартов и паспортов.
Перечень контролируемых параметров, используемый инструмент, виды дефектов и нормы отбраковки при визуальном и измерительном контроле деталей крюков приведены в табл. 2.
Таблица 2
Наименование
и обозначение контролируемой детали, зона контроля |
Метод контроля, измерительный инструмент | Размеры допустимых дефектов |
Крюк:
Износ зева крюка в вертикальном сечении (рис.1) Износ по ширине зева крюка |
Измерительный – штангенциркуль ШЦ-II | Δh > 0,1h, где Δh и h – абсолютные значения соответственно износа и высоты вертикального сечения |
Измерительный – штангенциркуль ШЦ-II |
Δb > 0,1b, где Δb и b – абсолютное суммарное значение износа и ширина зева крюка | |
Ось крюка:
Износ поверхности по диаметру |
Измерительный – микрометр типа МК 150-2 ГОСТ6507 | Не более 0,002d, где d – номинальный размер по диаметру оси |
При контроле окрашенных объектов краска с поверхности в зоне контроля не удаляется, если это специально не оговорено в НТД и поверхность объекта не вызывает подозрений на наличие трещин по результатам визуального контроля [2].
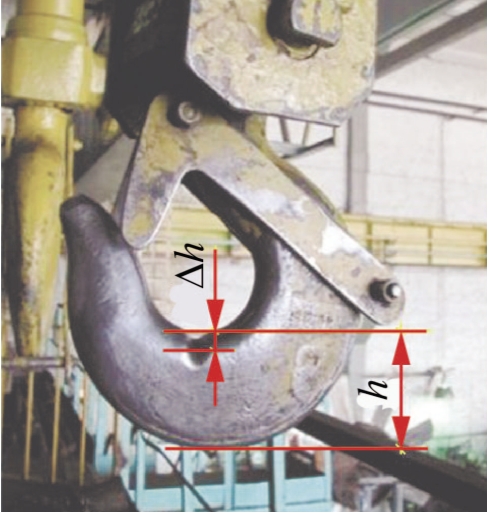
Магнитопорошковый контроль (МПД) служит для выявления поверхностных и подповерхностных дефектов залегающих на глубине до 10 мм. Этот метод применяют для контроля грузовых крановых крюков из ферромагнитных сталей. Для контроля магнитопорошковым методом применяют дефектоскопы типа ПМД-70, МД50П, МД-600; намагничивающие устройства с постоянными магнитами типа «МАГУС-М» и аналогичные им.
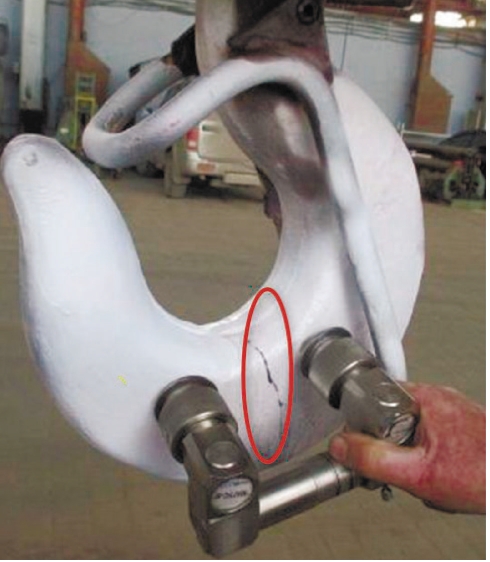
При магнитопорошковом контроле выявляются трещины шириной от 1 мкм и глубиной от 0,01 мм (рис. 4).
При контроле могут быть выявлены волосовины, неметаллические включения, расслоения, закаты, подповерхностные флокены, раковины, ковочные и штамповочные трещины, надрывы и другие дефекты, образовавшиеся при изготовлении и эксплуатации крана.
На выявляемость дефектов оказывают влияние многие факторы, связанные со свойствами объекта и принятой технологией магнитопорошкового контроля: магнитные свойства и структурные неоднородности материала, шероховатость, форма объекта контроля, его габаритные размеры, масса, наличие покрытий, их толщина и свойства, вид тока, схема намагничивания, способ контроля, а также значения таких параметров технологии контроля, как напряженность поля или сила тока [3]. Наличие покрытий толщиной до ~20 мкм практически не влияет на выявляемость дефектов. При толщине покрытия более 100…150 мкм могут быть выявлены только дефекты размером более 0,15 мм.
Масштабность применения магнитопорошкового метода объясняется его высокой производительностью, наглядностью результатов контроля и высокой чувствительностью. При правильной технологии контроля элементов конструкций и деталей этим методом обнаруживаются трещины в начальной стадии их появления, когда обнаружить их без специальных средств контроля трудно или невозможно. Условные уровни чувствительности при МПД [4] приведены в табл. 3.
Таблица 3
Условный уровень чувствитель- ности | Ширина выявляемого дефекта, мкм | Минимальная протяженность выявляемой части дефекта, мм | Шероховатость контролируемой поверхности Ra, (не грубее), мкм |
А | 2,6 | Свыше 0.5 | 2,5 |
Б | 10,0 | Свыше 0,5 | 10 |
В | 25,0 | Свыше 0,5 | 10 |
Перед проведением контроля суспензию (как приготовленную, так и повторно применяемую) проверяют на стандартном образце при заданном НТД уровне чувствительности контроля.
Дефекты проявляются и оцениваются по наличию на контролируемой поверхности индикаторного следа магнитного порошка, видимого невооруженным глазом, или с использованием луп, и воспроизводимого повторно после каждого нового нанесения магнитной суспензии или порошка. При этом длина индикаторного следа практически равна линейной протяженности выявленного дефекта [5].
Контроль акустическим (ультразвуковым) методом (рис. 5) выполняется дефектоскопом типа УД2-12, УД270, УД-13П; УД4-7; «СКАРУЧ», «УИУ-СКАНЕР»; УД2-102; А1212; УД-09; USL-48, USN-50, USK-75 и др.
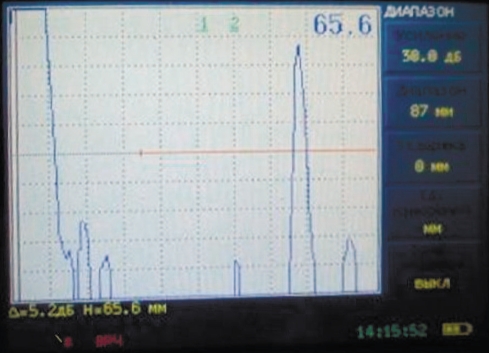
Для обеспечения акустического контакта между преобразователем и деталью подготовленную поверхность перед контролем тщательно протирают ветошью, а затем на нее наносят слой контактной смазки. Настройку дефектоскопа на заданную чувствительность производят по эталонам, а затем по испытательным образцам, для чего на поверхность ввода (поверхность контролируемой детали) наносят контактную жидкость и устанавливают преобразователь. Для УЗК деталей крюков применяют прямые (нормальные) или раздельно-совмещенные преобразователи с частотой 2,5 МГц и наклонные (призматические) преобразователи с углом наклона призмы 30°; 40°; 50° и 64° с частотой 1,8 и 2,5 МГц. Для настройки аппаратуры УЗК используются стандартные образцы СО-1, СО-2, СО-3 в соответствии с требованиями ГОСТ 14782–86 [6] и специально изготовленные испытательные образцы элементов контролируемых деталей. Для контроля деталей грузовых крановых крюков призматическими преобразователями применяются испытательные образцы с искусственным дефектом в виде зарубки [6].
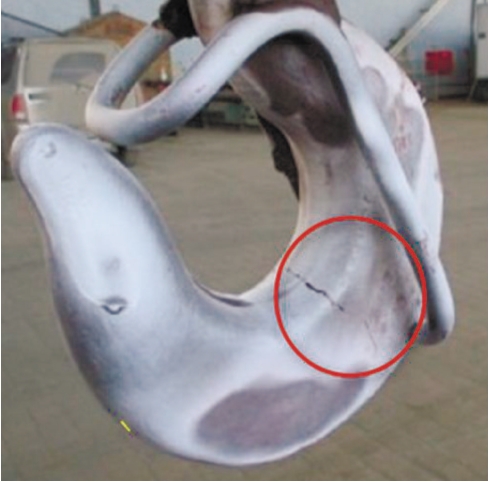
Контроль методом цветной дефектоскопии (рис. 6) выполняется на участках (зоны) контроля, длина или площадь которых должна быть установлена так, чтобы не допускать высыхания индикаторного пенетранта до повторного его нанесения. Контроль цветным методом должен проводиться при температуре от 8 до 40°С и относительной влажности не более 80%. Допускается проведение контроля при температуре от –15°С до +8°С с использованием соответствующих дефектоскопических материалов.
Выбор набора дефектоскопических материалов должен определяться в зависимости от необходимой чувствительности контроля по ГОСТ 18442–80 [8] и условий его применения (табл. 4).
Таблица 4
Класс чувствительности | Минимальный размер (ширина раскрытия) дефектов, мкм |
Толщина щупа контрольного образца, мм |
I | Менее 1 | – |
II | от 1 до 10 | 0,05 |
III | от 10 до 100 | 0,1 |
IV | от 100 до 500 | 0,5 |
Допускается использовать для обезжиривания органические растворители (ацетон, бензин) с целью достижения максимальной чувствительности или при проведении контроля в условиях пониженных температур, после чего осушить спиртом, используя сухие чистые салфетки из ткани бязевой группы. Не допускается обезжиривание керосином [7].
Время между подготовкой поверхности к контролю и нанесением индикаторного пенетранта не должно превышать 30 мин. В течение этого времени необходимо исключить возможность конденсации атмосферной влаги на контролируемой поверхности, а также попадание на нее различных жидкостей и загрязнений.
Неразрушающий контроль грузозахватных крюков осуществляется с целью повышения уровня эксплуатационной безопасности подъемных сооружений на опасных производственных объектах. Принятие правильных решений, направленных на обеспечение промышленной безопасности, напрямую связано с правильностью и обоснованностью выбора метода неразрушающего контроля при исследовании объекта контроля.
Список литературы
- ГОСТ 6627–74. Крюки однорогие. Типы. Конструкция и размеры.
- РД 03-606–03. Инструкция по визуальному и измерительному контролю.
- РД 13-05–2006. Методические рекомендации о порядке проведения магнитопорошкового контроля технических устройств и сооружений, применяемых и эксплуатируемых на опасных производственных объектах.
- ГОСТ 21105–87. Контроль неразрушающий. Магнитопорошковый метод.
- РД РОСЭК 003–97. Машины грузоподъемные. Контроль магнитопорошковый. Основные положения.
- ГОСТ 14782–86. Контроль неразрушающий. Соединения сварные. Методы ультразвуковые.
- РД-13-06–2006. Методические рекомендации о порядке проведения капиллярного контроля технических устройств и сооружений, применяемых и эксплуатируемых на опасных производственных объектах.
- ГОСТ 18442–80. Контроль неразрушающий. Капиллярные методы. Общие требования.