Авторы: С.В. Панченко, В.Н. Степанов, Г.В. Катышева, С.Л. Масякин, С.В. Дьяконов (ОАО «НОРЭ).
Опубликовано в журнале Химическая техника №12/2015
Технологические среды, обращающиеся в производстве карбамида, обладают высокой коррозионной активностью по отношению к большинству конструкционных сталей. Одна из наиболее значимых проблем, с которой сталкиваются производители карбамида, – обеспечение достаточной долговечности оборудования технологических линий. В связи с этим задачей настоящего исследования было определение причин выхода из строя элемента оборудования задолго до окончания планируемого срока эксплуатации.
В производстве карбамида, работающего по схеме с использованием жидкостного рецикла углеаммонийных солей, трубопровод выхода газовой фазы от стриппера-дистиллятора, предназначенного для отгонки непрореагировавших аммиака и углекислого газа из раствора карбамида, неоднократно подвергался ремонту из-за ускоренного коррозионного изнашивания участков, прилегающих к выходу из аппарата. В ходе последнего ремонта была выполнена замена первого по ходу газа секторного отвода трубопровода. После ~10 мес. эксплуатации произошло сквозное коррозионное разрушение отвода.
Рабочая температура газов дистилляции, выходящих из стриппера, составляет 130°С, рабочее давление – 2,5 МПа.
Отвод – сварной, выполнен из труб диаметром 219×10 мм и состоит из трех секторов. Два крайних выполнены из стали 03Х17Н14М3, средний – из стали ТР 316 L. Наибольший коррозионный износ зафиксирован в околошовной зоне со стороны среднего сектора (сквозное отверстие), обнаружено также расслоение основного металла с внутренней стороны среднего сектора отвода (рис. 1, 2, 3).


Коррозионная стойкость сталей, используемых в производстве карбамида, обеспечивается за счет пассивации металла и образования на его наружной поверхности окисной пленки.

На рис. 3 видно, что поверхность металла крайнего сектора имеет темно-серый цвет, характерный для стабильно пассивированного металла, поверхность среднего сектора – серебристого оттенка, характерного для металла, подвергавшегося многократной перепассивации и соответственно интенсивной коррозии.
В соответствии с проектом трубопровод должен быть изготовлен из стали марки 03Х17Н14М3. Для изготовления среднего сектора отвода была использована сталь марки ASTM A 240 TP 316L, которая является аналогом стали 03Х17Н14М3 по химическому составу. В таблице приведены сведения, касающиеся требований технических условий стандартов к химическому составу сталей.
Сталь |
Химический состав (min/max), % | ||||||||
C | Si | Mn | Сr | Ni | P | S | Mo | Fe | |
ТР 316L (по ASTM A 240 | -/0,03 | -/1,0 | -/2,0 | 16,0/18,0 | 10,0/15,0 | -/0,045 | -/0,03 | 2,0/3,0 | Остальное |
03Х17Н14М3 (по ГОСТ 7350) | -/0,03 | -/0,4 | 1,0/2,0 | 16,8/18,3 | 13,5/15,0 | -/0,03 | -/0,02 | 2,2/2,8 | Остальное |
Выполненный количественный химический анализ среднего сектора отвода подтвердил соответствие химического состава требованиям стандарта ASTM A 240 к материалу TP 316L (%):0,02 С; 0,69 Si; 1,26 Mn; 17,52 Сr; 11,27 Ni; 0,029 Р; 0,016 Si; 2,2 Mo; остальное Fe.
Однако следует отметить, что содержание легирующих элементов, определяющих коррозионную стойкость стали, в стали 316 L по стандарту и по результатам химического анализа материала ниже, чем по стандарту в стали 03Х17Н14М3.
Так, в стали средней части отвода содержание никеля – 11,27%, тогда как в стали 03Х17Н14М3 по стандарту – не менее 13,5% (при одинаково низком содержании углерода).
Содержание же хрома и молибдена в исследованном образце соответствует нижней границе стандарта на отечественный аналог.
Металлографические исследования микроструктуры материала среднего сектора отвода, выполненные с наружной (неповрежденной) стороны не выявили технологических дефектов микроструктуры основного металла (рис. 4).
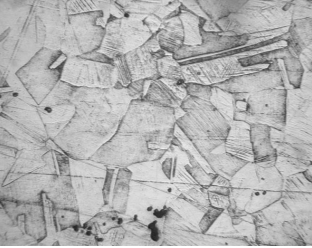
Опыт применения стали ТР316L показывает, что она обладает удовлетворительной коррозионной стойкостью в жидких средах, содержащих карбамид, при достаточном содержании в технологической среде кислорода, необходимого для пассивации стали. Технологической схемой предусмотрено дозирование воздуха в узел дистилляции, однако функционирование узла дозирования, как показал опрос производственного персонала, не всегда осуществляется должным образом из-за кристаллизации продукта на выходе из штуцера подачи воздуха.
Таким образом, причиной выхода из строя участка отвода, выполненного из стали ТР316L, стало сочетание воздействия ряда неблагоприятных факторов:
- при работе стриппера-дистиллятора происходит постоянное забрасывание аэрозоля раствора карбамида в трубопровод газовой фазы, являющееся следствием несбалансированной гидродинамики технологического процесса (высоких скоростей движения потоков);
- пониженное содержание кислорода не обеспечивает удовлетворительной пассивации стали с меньшей степенью легирования.
Появление сквозного коррозионного дефекта именно в околошовной зоне объясняется тем, что в зоне термического влияния сварки при нагреве происходит выделение феррита, наличие которого в микроструктуре аустенитной стали снижает коррозионную стойкость в средах, содержащих карбамид, и приводит к дополнительному увеличению скорости коррозии.
Заказчику работ было рекомендовано при ремонте трубопровода выхода газовой фазы со стрипперадистиллятора использовать стали «карбамидного» класса с содержанием никеля не менее 13,5%, молибдена – не менее 2,2%, углерода – не более 0,03%.