Авторы: А. Р. И. Аль-хаиали, Ф.И. Паршин, Д.В. Зубов,М.Ю. Беляевский, Г.М. Беляевский (Университет машиностроения, Москва).
Опубликовано в журнале Химическая техника №10/2016
В связи с продолжающимся увеличением мощностей установок по переработке нефти требуется улучшать теплои массообменные характеристики оборудования, так как обеспечивать производительность только увеличением геометрических размеров (диаметр, высота) уже сложно в связи с большими капитальными затратами и значительным усложнением монтажа. В связи с этим актуальным является разработка и тестирование новых конструкций массобменного оборудования – массообменных тарелок, насадок, клапанов и т.д.
Для изучения массообменных и гидравлических характеристик массобменного оборудования был разработан лабораторный стенд [1], на котором проведены исследования новых ректификационных тарелок с трапециевидным клапаном, которые соответствуют массообменным устройствам ведущих мировых фирм, и ряд других работ.
Стенд состоит из колонного аппарата, в который снизу подается воздух из воздуходувки (максимальная производительность до 6 000 м3/ч). Поток воздуха проходит через узел ввода сырья с равномерным распределением по сечению и взаимодействует с жидкостью, подаваемой из сливного кармана на барботажную тарелку.
На стенде измеряется перепад давления на массообменном устройстве (при помощи дифманометра), расход воздуха (первичный преобразователь – трубка Пито, вторичный – дифманометр), расход воды (при помощи частотного преобразователя на насосе подачи воды).
Для изучения теплообменных характеристик стенд оснащен датчиками температуры. Все данные с датчиков поступают в SCADA-систему, выполняющую функции первичной обработки данных для предоставления их оператору, архивирования и т.д.
Стенд с успехом используется в исследованиях, однако с течением времени стали проявляться некоторые проблемы, связанные с используемыми в подсистеме информации первичными преобразователями.
В качестве первичных преобразователей в данной статье будут рассмотрены термопары и преобразователи дифференциального давления. Выбранные для рассмотрения датчики находят широчайшее применение как в промышленности, так и в научных исследованиях.
Однако они со временем изменяют свои характеристики, в частности из-за отложения осадков на поверхности термопреобразователя или на термогильзе, из-за образования пустот между термогильзой и термопреобразователем, из-за накопления осадков и пленок на мембранах преобразователя давления, накопления пузырьков газа и т.д. Перечисленные явления увеличивают время реакции датчика, в том числе оно может увеличиться в несколько раз, что само по себе ухудшает измерительные характеристики стенда, а если учесть, что интересующие нас коэффициенты теплои массопередачи, коэффициенты гидравлического и пневматического сопротивлений рассчитываются на основе пространственно разнесенных точек отбора импульсов, то несогласованное изменение времен реакций датчиков приведет к появлению заметных погрешностей (в динамических режимах) и существенного увеличения времени на исследование оборудования (в стационарных режимах).
Для определения актуальных значений времени реакции первичных преобразователей можно провести их поверку или калибровку, но эти процедуры подразумевают демонтаж, перенос изучаемых преобразователей в метрологическую лабораторию, работу с ними там, последующий монтаж, что приводит к непроизводительным простоям стенда, большим трудозатратам и может оказаться малоэффективно в случае неквалифицированного монтажа.
Более перспективным методом обнаружения изменения характеристик датчиков являются методы, не требующие демонтажа и даже, в некоторых случаях, приостановления работы стенда [2]. Рассмотрим некоторые из них.
Испытание реакции на ступенчатое изменение контурного тока (РСКТ)
Испытание основано на нагревании датчика (не интеллектуального) электрическим током, подаваемым на жилы датчика со стороны щита преобразователей, т.е. в схеме коммутации щита предусматривается при инициировании рассматриваемого режима отключение жил, идущих на блок ввода контроллера (т.е. на АЦП измерительной подсистемы стенда), и одновременное подключение этих жил к источнику питания. Для термосопротивлений рекомендуется использовать малый постоянный ток порядка 40…80 мА, а для термопар – переменный ток ~0,2 А.
При прохождении электрического тока чувствительный элемент датчика (проволока у термометров сопротивления и королек у термопар), нагревается выше температуры окружающей его технологической среды, и при возврате к штатной схеме коммутации (источник питания отключен, блок ввода подключен) начинается переходный процесс охлаждения чувствительного элемента, при этом его температура измеряется системой обычным образом. Для термосопротивлений возможен мониторинг переходного процесса и в течении приложения постоянного тока.
Данное испытание выявляет влияние защитной гильзы (в случае ее использования), зазора между датчиком и защитной гильзой и всех воздействий режимов технологического процесса, таких, например, как скорость потока жидкости, температура и т.д. при нормальном режиме работы или при близких условиях.
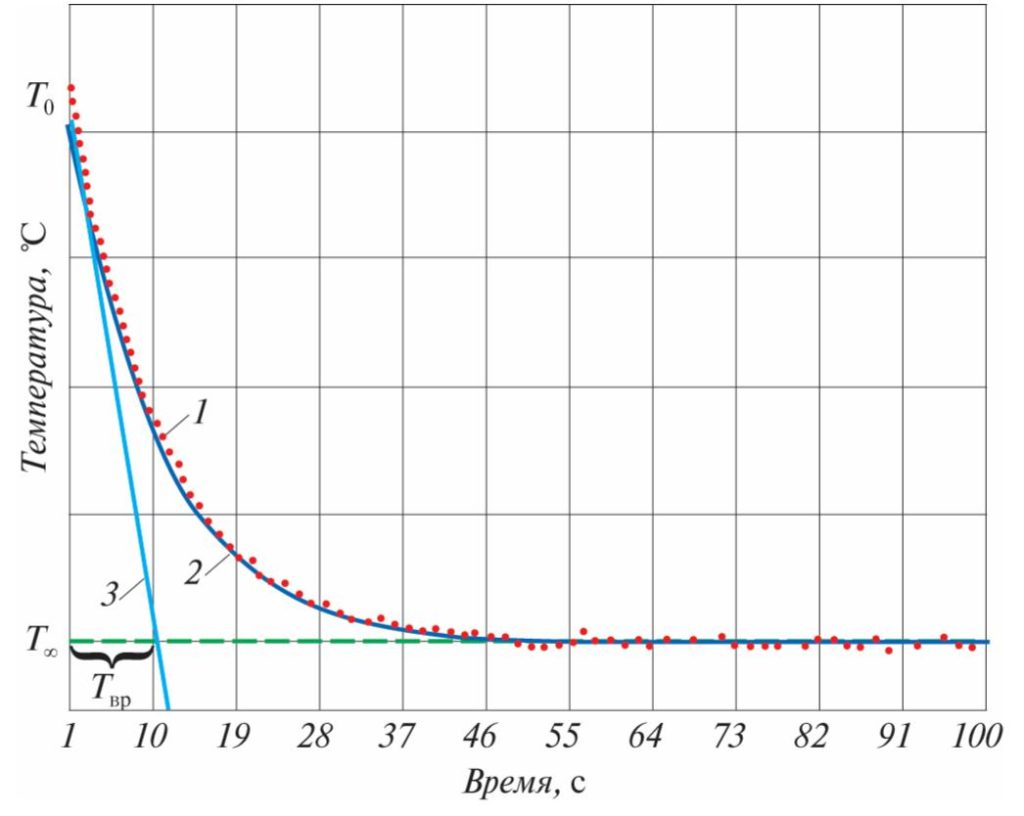
1 – экспериментальное значение температуры;
2 – аппроксимация;
3 – касательная к линии аппроксимации в точке, соответствующей начальному моменту времени
Для анализа полученных в ходе РСКТ данных можно разработать модель сенсора и на ее основе получить время реакции. Нами разработана упомянутая модель при следующих допущениях:
- теплофизические параметры (теплоемкости, плотности, коэффициенты теплопередачи как материала термопреобразователя, так и окружающих его веществ) принимаются постоянными;
- температура, тепловой поток от датчика практически не влияет на температуру среды вокруг датчика;
- закон теплопереноса (теплопередача излучением считается пренебрежимо малой) – линеен;
- чувствительный элемент принимается за объект с режимом идеального смешения (температура в каждой точке королька одна и та же);
- теплопередача по жилам пренебрежимо мала.
Предлагаемый алгоритм определения постоянной времени термопреобразователя
1. Пропускаем через термопреобразователь электрический ток.
2. После отключения электрического тока фиксируем температуру с периодом опроса 1 с.
3. Через 2 мин. опрос термопреобразователя переводим в нормальный режим, начинаем анализ полученных данных.
4. Данные последней минуты усредняем – вычисляем среднее арифметическое и принимаем за T∞.
5. Первые три измерения также усредняем и принимаем за T0.
6. Выбираем три идущих подряд измерения, соответствующие половине интервала, также усредняем и принимаем за Ti.
7. Вычисляем оценку постоянной времени
Алгоритм фактически сводится к аппроксимации экспериментальных данных апериодическим звеном первого порядка и нахождению его постоянной времени. На рисунке приведена иллюстрация применения алгоритма.
Если оказывается, что экспериментальные данные скорее указывают на применимость звена второго порядка, то возможно дальнейшее усовершенствование алгоритма. При существенном превышении значения Tвр над нормативными значениями требуется принять меры к замене термопреобразователя.
Метод анализа шумов
Для диагностики преобразователей давления можно применить метод котроля шумов, основанный на контроле естественных флуктуаций, которые существуют на выходе датчиков давления. Упомянутые шумы обусловлены турбулентностью, вызванной потоком среды и другими естественными явлениями.
Для проведения испытания [2] диагностируемый датчик давления начинают опрашивать с частотой не менее 100 Гц в течение 1 ч и затем анализируют полученные данные. Поскольку обычные АЦП блоков ввода не рассчитаны на такой режим, то следует предусмотреть перекоммутацию жил интерфейса 4…20 мА на высокоскоростной блок ввода, например производителей National Instruments или «Актаком», имеющий выход на компьютерные интерфейсы USB. Помехи извлекают из выходного сигнала датчика с помощью режекторного фильтра.
Если обнаружится, что время реакции датчика давления ухудшилось или время его реакции превышает допустимый предел, то следует в отдельном исследовании определить причину этого.
Метод анализа шумов нельзя использовать для испытания времени реакции датчиков уровня жидкости в баке и датчиков с небольшими технологическими шумами или не имеющих их вовсе. Для этих датчиков входные шумовые данные часто могут быть сгенерированы искусственно с помощью генератора механических шумов, включающего преобразователь тока в давление.
Рассмотренные методы позволяеют оценить состояние первичных преобразователей температуры и давления без из демонтажа и таким образом обечпечить продолжительность нормальной работы исследовательского стенда.
Список литературы
- Беляевский М.Ю., Колмогоров Г.Ю., Заика А.И., Беляевский Д.М., Бабарыкин Н.М. Определение гидравлического сопротивления и эффективности массообменных тарелок//Нефтепереработка и нефтехимия. Научно-технические достижения и передовой опыт. 2014. №1.
- Хашемиан Х. Датчики технологических процессов. Характеристики и методы повышения надежности. М.: Бином, 2008.