Автор: Е.Ю. Курило, П.Е. Панютина (Санкт-Петербургский политехнический университет Петра Великого), Д.В. Нижегородцев, А.С. Харламова (Санкт-Петербургский государственный архитектурно-строительный университет).
Опубликовано в журнале Химическая техника №1/2018
В химической промышленности зачастую возникает проблема разделения несмешивающихся жидкостей, которые образуются в процессе производства конечного продукта. Например, такая ситуация возникает при выщелачивании нефтяных (керосиновых, газойлевых и соляровых) фракций. При этом остаются отходы, в состав которых входят нафтеновые кислоты – ценные продукты, использующиеся в производстве мылонафта и эмульсола. При очистке нефтепродуктов нафтеновые кислоты извлекают щелочью в виде водного раствора натриевых мыл [1, 2].
Для улучшения качества продуктов, содержащих нафтеновые кислоты, щелочные отходы обезмасливают – промывают керосином. Для этого в резервуар с водным раствором остатков через маточник, расположенный в нижней части резервуара, подается чистый керосин [3–5]. Поднимаясь вверх через слой водного раствора нафтенатов в виде диспергированных струй, керосин удаляет избыточное количество неомыляемых веществ.
После окончания промывки и дополнительного двухчасового отстоя двухфазной системы керосин–водный раствор необходимо тщательно отделить жидкости друг от друга.
Обычно в устройствах для разделения несмешивающихся жидкостей применяется гравитационный принцип – они предназначены для выделения компонентов из движущегося потока [6–12]. Для этого используются отстойники [11], гравитационные сепараторы [7–10, 12], центрифуги и вихревые сепараторы [4], которые заменили ранее применявшиеся флорентийские сосуды и сепараторы Шмида [3]. Отметив высокую эффективность современных аппаратов для разделения, следует учесть, что сложность их конструкции и высокую стоимость.
Для случая, когда требуется разделить керосин и водный раствор, находящиеся в резервуаре мылонафтной установки, задача упрощается, так как оба жидкостных слоя находятся в статичном состоянии. Простой слив водного раствора нерационален, так как его объем намного превосходит объем керосина, находящегося сверху.
Более рациональным технологическим решением является слив керосина с помощью подвижной трубы, верхний конец которой находится в слое нефтепродукта, а нижний – закреплен шарнирно и связан с выходным штуцером резервуара.
Подобная система удаления керосина существует, например, на мылонафтной установке АО «Краснодарский нефтеперерабатывающий завод – Краснодарэконефть» (АО «КНПЗ-КЭН») [13], однако ее конструкция, состоящая из цилиндрического поплавка и поднимаемой им трубы, не является оптимальной, так как при высоте слоя керосина менее 0,5 м в сливную трубу начинает перетекать водный раствор.
Таким образом, существует задача конструирования такой системы разделения несмешивающихся жидкостей, при которой входное отверстие сливной трубы будет постоянно находиться в слое менее плотной жидкости независимо от высоты этого слоя в резервуаре.
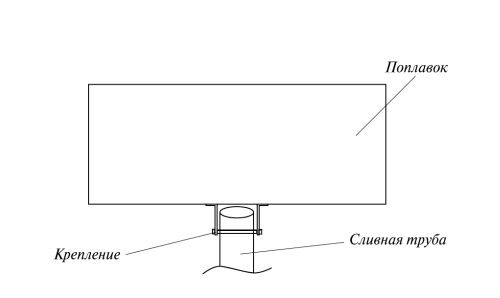
На рис. 1 показано принципиальное устройство существующей поплавковой системы слива. На основании данных, полученных от АО «КНПЗ-КЭН», было установлено, что при высоте слоя керосина 0,5 м входное отверстие трубы находится на линии раздела слоев жидкостей, и в этот момент в нее попадает вода. Следовательно, размещение среза трубы на уровне нижней точки поплавка будет невыгодным. Для того, чтобы решить эту проблему, следует разместить точку слива вблизи горизонтальной оси поплавка, что позволит удалить керосин практически полностью.
Предлагаемая в данной работе конструкция – плавучая система состоит из двух одинаковых цилиндров, соединенных между собой тонким стержнем по центральной оси. В этом случае можно произвольно менять положение точки слива. На рис. 2 показана предлагаемая конструкция двойного поплавка.
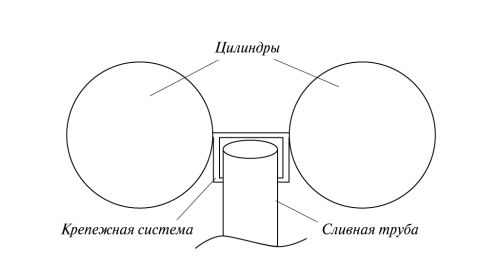
Для того, чтобы определить уровень, на котором следует установить срез трубы, необходимо установить зависимость между высотой слоя менее плотной жидкости и глубиной погружения поплавков. Значения центральных углов AOB и COD, показанные на рис. 3, позволяют установить такую связь.
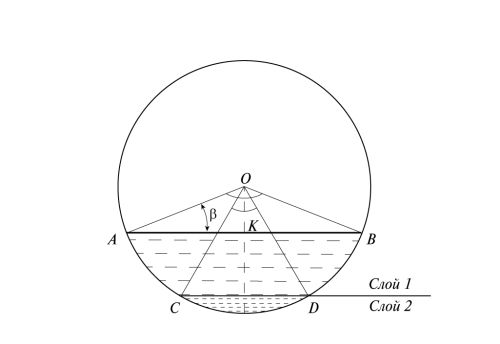
На рис. 4 показаны силы, действующие на систему труба–поплавок, которая находится в равновесии в том случае, когда силы тяжести и силы Архимеда уравновешиваются.
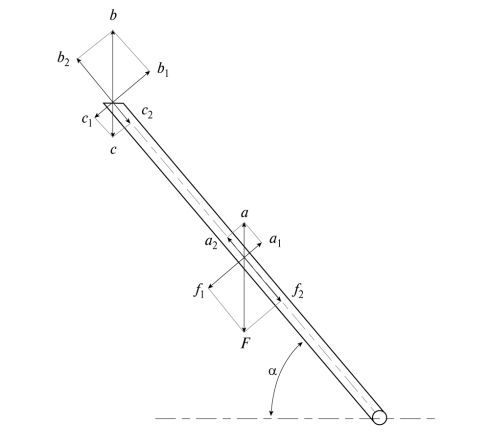
F – сила тяжести, действующая на трубу; a – выталкивающая сила, действующая на трубу; b – выталкивающая сила, действующая на цилиндр; c – сила тяжести,
действующая на поплавок
Момент, вращающий трубу против часовой стрелки,
M1 = (f1 – a1)l/2.
Момент, вращающий трубу по часовой стрелке,
M2 = (b1 – c1)l.
Равенство моментов – условие равновесия: (f1 – a1)l/2 = (b1 – c1)l; (Fcosα – acosα)l/2 = (bcosα – ccosα)l; (F – a)/2 = (b – c). (1)
Когда поплавок находится на границе раздела двух жидкостей, труба оказывается заполненной менее плотной жидкостью, а выталкивающая сила действует на плавучую систему со стороны обеих жидкостей. В этом случае формула (1) примет вид (mтр – Vρ1)/2 = V1ρ1 + V2ρ2 – mрасч, (2) где mтр – масса сливной трубы; V – объем трубы; V1, V2 – часть объема цилиндра, которая находится в слое соответственно 1 и 2; ρ1 и ρ2 – плотности жидкости слоя соответственно 1 и 2; mрасч – суммарная масса плавучей системы.
Отсюда получаем выражение, связывающее массу плавучей системы с переменными V1 и V2: mрасч = V1ρ1 + V2ρ2 – (mтр – Vρ1)/2. (3)
Часть объема одного цилиндра, погруженная в более плотную жидкость, определяется из формулы
V2 = S2
l = r 2(α2 – sinα2)l/2, (4) где α2 – угол AOB (см. рис. 3).
Общий объем цилиндра, погруженный в жидкости,
Vпогр = r 2(α1 – sinα1)l/2, (5) где α1 – угол COD (см. рис. 3).
Часть объема цилиндра, погруженная в менее плотную жидкость,
V1 = Vпогр – V2 = r 2[(α1 – sinα1) – (α2 – sinα2)]l/2. (6)
Подставляя формулы (4) и (6) в выражение (3) и учитывая при этом оба цилиндра и массу крепежной системы mкс, получаем окончательную формулу для расчета α1 и α2: mрасч = r 2l[ρ1(α1– sinα1 – α2 + sinα2) + + ρ2(α2 – sinα2)] – (mтр – Vρ1)/2 + mкс. (7)
Для того, чтобы найти зависимость между высотами hобщ, h1, h2, задаемся набором величин в диапазоне от 0 до r и для каждого заданного значения h1 осуществляем следующий алгоритм поиска h2: 1.Принимаем предварительные параметры плавучей системы: размеры цилиндров, крепежной системы, и материал; 2.Рассчитываем действительную массу плавучей системы mд = 2mц + mкс (здесь mц – масса одного цилиндра); 3.Задаем глубину погружения плавучей системы в более плотную жидкость h2 и рассчитываем α2 из формулы cos(α2/2) = 1 – h2/r ; 4.Рассчитываем величину a = r – h2 – h1 (отрезок OK на рис.3); 5. Определяем угол β из формулы sinβ = a/r ; 6. Определяем угол α1 = π – 2β; 7. Вычисляем массу плавучей системы mрасч по формуле (7) и проверяем совпадение полученного значения с действительной массой mд. 8. Если совпадения нет, то повторяем расчет до совпадения рассчитанной и заданной массы.
На основании этого алгоритма была разработана программа на языке PASCAL, позволяющая получить зависимость высоты погружения предложенной плавучей системы в слои несмешивающихся жидкостей от геометрических размеров цилиндров, суммарной массы системы и плотностей жидкостей. На рис. 5 приведена блоксхема программы.
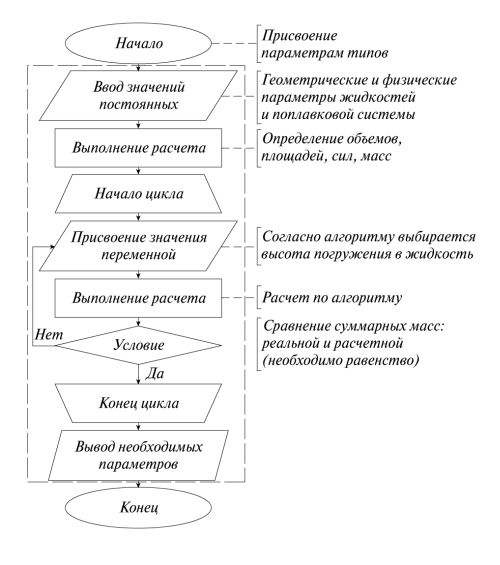
Для примера был произведен расчет плавучей системы в резервуаре, заполненном водой и керосином, для цилиндров разного диаметра (250; 300 и 350 мм).
На рис. 6 приведены зависимости глубины погружения плавучей системы в жидкость от высоты слоя керосина.
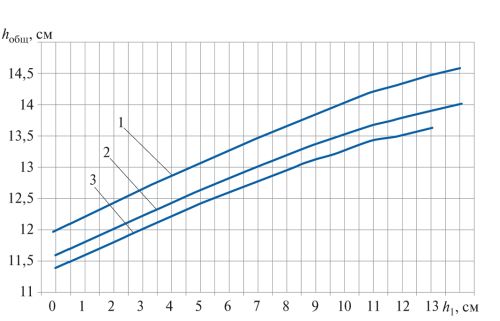
Как видно, для поплавка любого диаметра начальный линейный участок сменяется асимптотическим с увеличением толщины слоя керосина. Рис. 7 иллюстрирует, как зависит от высоты слоя керосина расстояние от центра поплавка до поверхности жидкости.
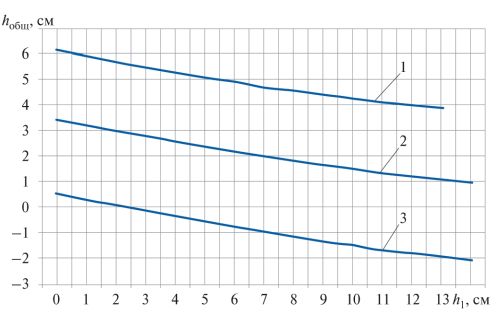
Предложенная в данной работе плавучая система разделения несмешивающихся жидкостей позволяет установить любое положение входного отверстия сливной трубы. Программа, написанная на языке PASCAL, дает возможность уточнить наиболее рациональное положение отверстия для того, чтобы обеспечить удаление максимально возможного объема менее плотной жидкости из резервуара. Таким образом, в рассмотренной системе разделения жидкостей достигается необходимая эффективность при прежней простоте и низкой стоимости конструкции (по сравнению с другими аналогичными устройствами.
Список литературы
- ГОСТ 13302–77. Кислоты нефтяные. Технические условия (с Изменениями №1–4). Введ. с 01.01.1979.
- Наметкин Н.С., Егорова Г.М., Хамаев В.Х. Нафтеновые кислоты и продукты их химической переработки. М.: Химия, 1983. 184 с.
- Плановский А.Н. Специальная аппаратура промышленности органических полупродуктов и красителей. М-Л.: Государственное научно-тех. изд-во химической литературы, 2012. 446с.
- Лекае В.М., Лекае А.В. Процессы и аппараты химической промышленности. М.: Высшая школа, 1977. 256 с.
- Воронцов И.И. Полупродукты анилинокрасочной промышленности. М.: Государственное научно-тех. изд-во химической литературы, 1955. 580 с.
- Бесчастнов М.В. Взрывобезопасность и противоаварийная защита химико-технологических процессов. М.: Химия, 1983. 472с.
- Зиберт Г.К., Седых А.Д., Кащицкий Ю.А., Михайлов Н.В., Демин В.М. Подготовка и переработка углеводородных газов и конденсата. Технологии и оборудование. Справ. пособ. М.: ОАО «Недра-Бизнесцентр», 2001. 316с.
- Пат. SU 20239. Способ выделения мылонафта.
- Пат. РФ 2374220. Способ разделения смеси нафтеновых кислот.
- Пат. РФ 2294787. Способ разделения несмешивающихся жидкостей.
- А.С. №1429375. Устройство для разделения трехфазной смеси.
- Пат. РФ RU 2253500. Установка для разделения несмешивающихся жидкостей.
- Технический паспорт резервуара Р-1. Главзаказнефтепереработка. Краснодарский нефтеперерабатывающий завод. 1954. 14 с.