Авторы: В.В. Буренин, М.И. Степанов, А.В. Николаев (МАДИ).
Опубликовано в журнале Химическая техника №7/2015
Загрязнение окружающей воздушной среды недостаточно очищенными и обезвреженными производственными пылегазовоздушными выбросами промышленных предприятий, в том числе предприятий химического и нефтехимического комплекса, в настоящее время представляет глобальную экологическую проблему.
Пылегазовоздушные выбросы этих предприятий, содержащие индустриальную пыль и различные газовые примеси, перед выбросом их в атмосферный воздух должны быть очищены и обезврежены до предельно допустимых концентраций вредных веществ, чтобы не оказывать негативное воздействие на организм человека, животных и растительность. Защита атмосферного воздуха, который необходим для сохранения жизни на Земле, от вредных примесей является одной из важнейших проблем современности.
Наиболее эффективным способом защиты воздушного бассейна Земли от загрязнения вредными пылегазовыми веществами является внедрение в производство безотходных технологий. Однако по техническим и экономическим соображениям создание полностью беструбных и бессточных промышленных предприятий, полная утилизация отходов производства станут всеобъемлющей основой производственной деятельности только в более или менее отдаленном будущем. В связи с этим в настоящее время очень актуальна очистка и обезвреживание промышленных пылегазовоздушных выбросов с помощью эффективных фильтров-пылегазоуловителей [1].
В последние годы заметно повысился интерес российских и зарубежных фирм по производству техники для очистки и обезвреживания промышленных пылегазовоздушных выбросов к созданию новых фильтров-пылегазоуловителей с высокими технико-экономическими показателями. В зависимости от агрегатного состояния вредных примесей, содержащихся в производственных пылегазовоздушных выбросах, очистительное (фильтрующее) оборудование подразделяется на пылеулавливающее (фильтры-пылеуловители), газоочистительное (фильтры-газоуловители) и пылегазоочистительное (фильтры-пылегазоуловители).
Для очистки производственных пылегазовоздушных выбросов от пыли применяются фильтры-пылеуловители, которые по принципу действия делятся на механические и силовые. В механических фильтрах-пылеуловителях очистка пылегазовоздушных выбросов от пыли достигается за счет использования различных жестких или гибких фильтрующих перегородок или насыпных слоев фильтрующего материала.
Конструктивно фильтрующие перегородки (кроме стационарных) оформляют в виде сменных патронов, кассет, рукавов; неподвижного, движущегося или псевдоожиженного слоев зернистых частиц.
Фильтрующие перегородки, а также насыпные слои бывают сухие и мокрые. В качестве фильтрующих материалов используют природные, синтетические, минеральные, металлические волокна или ткани; пористые листовые материалы из резины или пластмассы, нетканые волокнистые материалы из войлока, фетра или картона и т.д. (для гибких перегородок); пористую керамику, пластмассы, спеченные или спрессованные порошки металлов, керамики и др. (для жестких перегородок); гравий, кварцевый песок, кокс, древесные опилки, адсорбенты и т.д. (для насыпных слоев).
Очистка производственных пылегазовоздушных выбросов от пыли в силовых фильтрах-пылеуловителях осуществляется за счет использования силовых полей: электрического, инерционного, гравитационного, магнитного и т.д.
В силовых электрических фильтрах частицы пыли, содержащиеся в пылегазовоздушных выбросах промышленных предприятий, проходя через электростатическое поле, получают электрический заряд, а затем осаждаются на противоположно заряженных электродах.
Существующие промышленные системы электрического пылеулавливания (электростатическое осаждение частиц пыли из потока газа) позволяют обрабатывать значительные объемы (порядка сотен тыс. м3/ч) потока пылегазовоздушных выбросов, имеющего высокую температуру и агрессивность; КПД таких систем достаточно высок.
Вместе с тем, электростатическому осаждению частиц пыли из пылегазовоздушного потока присуща некоторая избирательность в отношении извлекаемых из газа частиц загрязнений, которые должны обладать невысоким удельным электрическим сопротивлением. Однако этот недостаток можно компенсировать предварительной обработкой пылегазовоздушного потока химическим, физическими и другими методами для понижения удельного электрического сопротивления. Кроме высокой стоимости изготовления к недостаткам электрофильтров также относятся: снижение степени очистки при изменениях параметров очищаемых пылегазовоздушных выбросов, например, при увеличении количества или входной запыленности очищаемого газа и др.; высокая чувствительность процесса электрической очистки к точности изготовления и монтажа основных элементов электрофильтра и др.
Для пылегазовоздушных выбросов промышленных предприятий от вредных паров, газов и токсичных веществ используют сорбционные, химические, термические, биохимические и другие способы очистки и обезвреживания.
К наиболее распространенным способам очистки и обезвреживания промышленных пылегазовоздушных выбросов от вредных и токсичных веществ относятся сорбционные способы (адсорбция и абсорбция). При этом либо происходит процесс физической сорбции, либо сорбент вступает в химическое взаимодействие с сорбируемым компонентом (химическая сорбция).
Способ адсорбции основан на физическом свойстве некоторых твердых тел (адсорбенты) с ультрамикроскопической структурой селективно извлекать и концентрировать на своей поверхности отдельные компоненты из промышленных пылегазовоздушных выбросов.
В то время, как абсорбция представляет собой процесс, при котором происходит разделение пылегазовоздушных выбросов на составные части путем поглощения одного или нескольких компонентов жидким поглотителем (абсорбент) с образованием раствора.
Достоинствами адсорбционного и абсорбционного способов очистки пылегазовоздушных выбросов от вредных примесей являются: глубокая степень очистки при правильном подборе адсорбентов и абсорбентов; селективность извлечения примесей, что дает возможность их вторичного использования. Однако эти способы малопроизводительны, требуют больших капитальных затрат, дороги при эксплуатации. В случаях, когда механические фильтры с гибкими или жесткими перегородками, а также с насыпным слоем используют не только для улавливания пыли, но и для очистки газовоздушных выбросов от вредных веществ (фильтры-пылегазоуловители), на фильтрующие перегородки наносят слой сорбента, а насыпной слой выполняют из материалов, способных поглощать вредные компоненты.
Высокой эффективностью при улавливании высокоабразивной пыли с повышенным удельным электрическим сопротивлением из пылегазовоздушного потока отличается фильтр-пылеуловитель [2], состоящей из электростатического (электрического) фильтра и механического фильтра с фильтрующими рукавными элементами (рис. 1). Пылегазовоздушный поток высокой запыленности поступает на очистку в корпус 1 фильтра-пылеуловителя через диффузор 2, равномерно распределяется по сечению корпуса 1 за счет газораспределительной решетки 3, после чего подвергается предварительной очистке в полях электрофильтра 4.
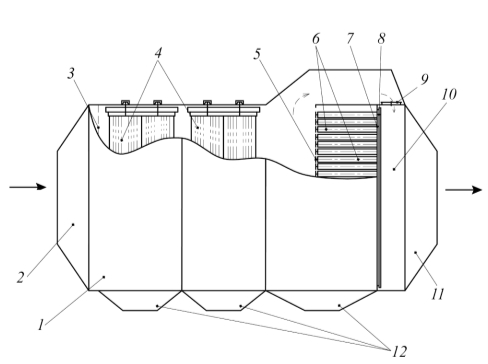
из электростатического и механического фильтров, для очистки пылегазовоздушных выбросов
Далее пылегазовоздушный поток поступает через фиксирующую газораспределительную решетку 5 к фильтрующим рукавным элементам 6 плоской формы. Фильтрующий материал решетки собран в складки, где происходит окончательная очистка от пыли. Горловины фильтрующих элементов 6 механического фильтра закреплены в рукавной плите 7, которая в свою очередь закрывает торцевую часть корпуса 1 по ходу движения пылегазовоздушного потока. За ней расположена система регенерации 8 фильтрующих элементов 6, которая расположена в камере 10 очищенного пылегазовоздушного потока, являющейся камерой для обслуживания фильтрующих элементов 6, причем выше нее расположены предохранительные клапаны с программным контроллером 9. В случае резкого увеличения температуры поступающего на очистку пылегазовоздушного потока предохранительные клапаны с программным контроллером 9 открываются и газовый поток направляется напрямую от последнего поля электрофильтра в камеру чистого газа 10, а далее в конфузор 11, минуя фильтрующие элементы 6 и тем самым предохраняя их от сгорания. При снижении температуры поступающего на очистку газа до нормы, предохранительные клапаны с программным контроллером 9 закрываются, и очистка газа фильтрующими элементами 6 возобновляется.
Улавливаемая полями электрофильтра и фильтрующими элементами пыль накапливается в бункерах 12, расположенными под корпусом 1 фильтра-пылеуловителя.
С целью повышения эффективности очистки пылегазовоздушного потока от аэрозольных частиц разработана электростатическое очистительное устройство [3], конструктивная схема которого изображена на рис. 2.
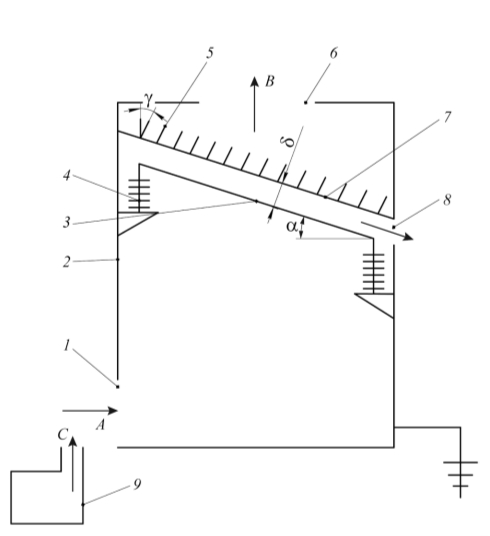
Устройство включает корпус 2 с входной полостью 1 и выходной полостью 6. В поперечном сечении корпуса 2 под углом α к горизонту смонтирован пористый осадительный электрод 7, выполненный из обычной металлической сетки. С зазором δ относительно пористого осадительного электрода 7 на изоляторах 4 смонтированы коронирующие электроды 3, выполненные в виде проводов малого (менее 1 мм) диаметра. Для эффективного горения коронного разряда зазор δ должно быть равным ~10 см.
У входной полости 1 установлен диспергатор 9, генерирующий воздушно-капельную смесь. Для повышения эффективности работы устройство снабжено направляющими лопатками 5, устанавливаемыми за электродом 7 и обеспечивающими разворот очищаемого пылегазовоздушного (газового) потока вдоль корпуса 2 в направлении выходной полости 6. Лопатки 5 устанавливаются под углом γ к электроду 7. Для отвода сепарируемой жидкости в корпусе 2 в месте контакта нижней части электрода 7 выполнено дренажное отверстие 8, к которому присоединяется шланг для отвода загрязненной жидкости в систему утилизации отходов (на рис. 2 шланг и система не показаны).
При подаче высокого напряжения на коронирующие электроды 3 зажигается коронный разряд между коронирующими электродами 3 и осадительным электродом 7. Образующийся в процессе коронного разряда ионный ветер движет газовую массу от электродов 3 к электроду 7, формируя направленный газовый поток от входной полости 1 (потом входит по стрелке А) к выходной полости 6 (поток выходит по стрелке В). У входной полости 1 с помощью диспергатора 9 формируется капельная дисперсия. Подлежащий очистке газовый поток, входящий по стрелке А, смешивается с капельной дисперсией и с помощью ионного ветра попадает в разрядный промежуток δ (зазор δ), в котором капли жидкости и подлежащие сепарации от газового потока аэрозоли получают электрические заряды. Вследствие сложных микрофизических процессов происходит захват подлежащих сепарации от газового потока аэрозолей каплями жидкости. Электрически заряженные капли жидкости, захватившие аэрозоли, двигаясь по силовым линиям электрического поля, попадают на поверхность заземленной сетки (электрод 7). Электрически заряженные капли при прохождении через поры осадительного электрода 7 осаждаются на его заземленной поверхности. Очищенный газовый поток выносится за пределы пористого осадительного электрода 7 ионным ветром и, отражаясь от направляющих лопаток 5, выносится через выходное отверстие 6 наружу по стрелке В. Собранные на поверхности осадительного электрода 7 капли укрупняются и через поры стекают вниз за счет гравитационных сил к дренажному отверстию 8.
Установка осадительного электрода 7 под углом γ к горизонту снижает вероятность срыва капель жидкости с его поверхности и попадания их в разрядный промежуток δ (заряд δ), что снижает вероятность электрического пробоя и обеспечивает устойчивое горение коронного разряда.
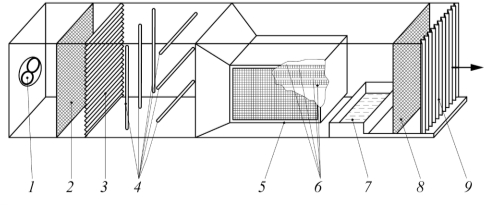
Высокой эффективностью очистки пылегазовоздушных потоков от пыли, аэрозоля и вредных химических загрязнителей за счет определенной последовательности размещения секций с оценкой эффективности очистки, оптимальной по критерию стоимость/эффективность отличается очистительное устройство [4] (рис. 3), состоящее из секции электростатической очистки для удаления из очищаемого потока пыли и аэрозоля, защищенной от облучения ультрафиолетовыми и вакуумными ультрафиолетовыми излучателями, фотоокислительной секции для фотохимического окисления загрязнителей в зависимости от их состава, фотокаталитической секции для уничтожения вторичных продуктов, увлажнительной секции для удаления не разлагаемых конечных продуктов фотопроцессов. Загрязненные пылегазовоздушные выбросы подаются на вход очистительного устройства вентилятором 1 и поступают на металлическую сетку 2 и уголковые жалюзи 3 электростатического фильтра.
На сетку 2 из тонкой проволоки подается высокое напряжение. Возникающие большие градиенты электрического поля образуют вокруг сетки облако электронов, которые заряжают отрицательным зарядом пыль и аэрозоль. Далее на пути пылегазовоздушного (газового) потока расположена система уголковых жалюзи 3, находящихся под положительным потенциалом. Жалюзи 3 выполняют две функции. Во-первых, на них оседают отрицательно заряженные пыль и аэрозоль. Во-вторых, уголковая форма надежно защищает сетку 2 от ультрафиолетового и вакуумного ультрафиолетового облучения из следующей фотоокислительной секции. Кроме того, жалюзи 3 такой формы имеют малое газодинамическое сопротивления и, соответственно, не приводят к значительным дополнительным энергозатратам.
Далее очищенный от пыли и аэрозоля газовый поток поступает в секцию фотоокисления, которая содержит излучатели нового поколения, основанные на барьерном разряде (эксилампы). Эксилампы 4 излучают в узких (от 50 до 150 А) спектральных интервалах, максимумы которых расположены в 14 позициях спектральной области 1260…3420 А. В процессе окисления образуются фрагменты исходных загрязнителей и продукты их фотохимических реакций в газе. Если загрязнителем является органическое вещество, то, как правило, оно представляет из себя смесь гомологов, то есть соединений сходного строения, но различного молекулярно веса. Наименьшей фотодеструкции подвергаются первые члены гомологического ряда, поэтому их уничтожение определяет эффективность очистительного устройства. Газовый поток с продуктами фотоокисления поступает в секцию фотокатализа, которая состоит из фотокаталитического фильтра 5 и облучателей 6 в спектральной области 2 200…3 500 А, которыми служат эксилампы или ртутные лампы низкого давления.
На поверхности фотокаталитического фильтра 5 образующиеся гидроксильные группы и активный кислород «дожигают» продукты фотоокисления до термодинамически устойчивых соединений (вода, углекислый газ и др.).
В этой же секции происходит уничтожение избыточного озона. Если в исходных пылегазовоздушных выбросах содержатся такие распространенные загрязнители, как сернистый ангидрид или другие окислы, производится растворение их в воде с образованием кислот. Для этого газ после обработки в фотокаталитическом фильтре 5 поступает в секцию увлажнения, содержащую генератор водяного аэрозоля 7, электростатическую сетку 8 и выходные жалюзи 9, на которые подается положительный потенциал. Окислы, содержащиеся в обработанном фотокаталитическом фильтром 5 газе, растворяются в водном аэрозоле. Для предотвращения фотоэффекта оси излучателей 6 перпендикулярны к плоскости электростатической сетки 8. Частицы воды, получающие отрицательный заряд, оседают на выходных жалюзи 9, имеющих положительный потенциал и стекают по ним в принимающий резервуар, а затем в генератор водяного аэрозоля 7. При уменьшении количества воды в генераторе 7 ниже заданного уровня вырабатывается управляющий сигнал на автоматическую смену воды или ее пополнение. Выходные жалюзи 9 защищают персонал, обслуживающий очистительное устройство, от облучения.
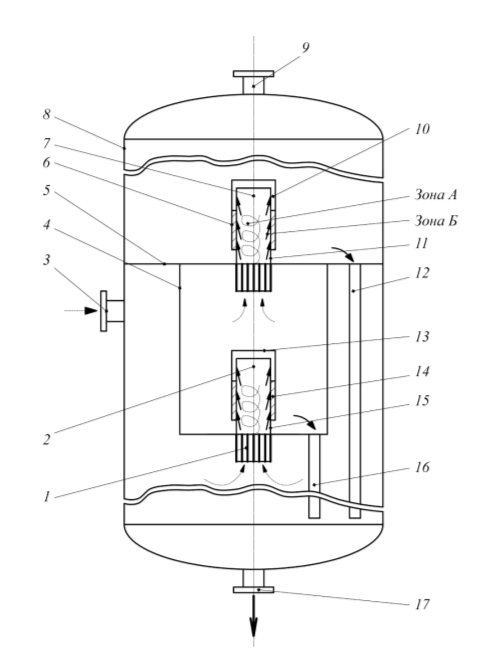
Эффективная технология силовой очистки потока производственных пылегазовоздушных выбросов от вредных жидких примесей [5] с использованием центробежных сил, возникающих при закручивании пылегазожидкостного потока, отличается высокой производительностью процесса сепарации (рис. 4). Поток пылегазовоздушных выбросов через патрубок 3 попадает в корпус 8 очистительного устройства и далее на завихритель 1 центробежного элемента 2 камеры 4, в котором очищаемый поток приобретает центробежное движение, при этом формируются центральная (зона А) и периферийная (зона Б) зоны разделяемого пылегазожидкостного потока.
Под действием центробежных сил жидкая фаза потока перемещается в периферийную зону Б центробежного поля, при этом вода осаждается на внутренней гидрофильной поверхности обечайки 15 центробежного элемента 2. Вода обволакивает гидрофильную поверхность обечайки 15, после чего основное количество воды в виде пленки направляется в зазор между обечайкой 15 и пленкосъемником 13, стекает по каплеотбойнику 14 в нижнюю часть камеры 4 и через дренажный патрубок 16 и далее патрубок 17 отводится из устройства. Вместе с водой через зазор между обечайкой 15 и пленкосъемником 13 частично отводится захваченный воздух и часть масла в режиме револьвентного течения стекающего по пленке воды. Основная часть масла уносится вместе с очищенным воздухом в центробежный элемент 7, внутренняя поверхность обечайки 11 которого олеофильна. Попав в зону действия центробежного поля, масляная аэрозоль под действием центробежных сил направляется в периферийную зону Б центробежного поля, где и осаждается на внутреннюю олеофильную поверхность обечайки 11 центробежного элемента 7. Масло обволакивает олеофильную поверхность обечайки 11, после чего в виде пленки направляется в зазор между обечайкой 11 и пленкосъемником 10, стекает по каплеотбойнику 6 на горизонтальное полотно 5 и через дренажный патрубок 12 и далее патрубок 17 отводится из устройства. Очищенный воздух отводится за пределы протекания процесса через центральное отверстие пленкосъемника 6 и выводится из очистительного устройства через патрубок 9.
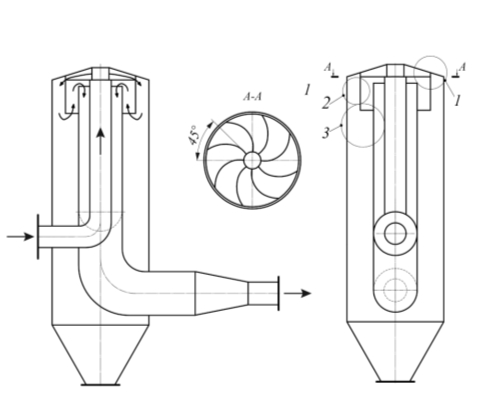
Эффективная работа силового центробежно-инерционного фильтра-пылеуловителя нового поколения [6] основана на сочетании центробежной и инерционной очистки от пыли при скоростях очищаемого пылегазовоздушного потока в рабочих зонах, составляющих 10…20 м/с, что как минимум в 4…5 раз превышает скорости в промышленных циклонах. В фильтре-пылеуловителе процесс отделения пыли от пылегазовоздушных выбросов происходит в трех разных рабочих зонах (рис. 5): 1 – зона закручивания потока пылегазовоздушных выбросов; 2 – зона формирования слоя твердой фазы (пыли) на стенке корпуса под действием центробежной силы; 3 – зона вывода частиц (пыли) из сепарационной зоны за счет отстаивания более инерционных мелкодисперсных твердых частиц или конденсированной фазы при развороте очищаемого потока (вторичное пылеулавливание). Процесс пылеулавливания в центробежноинерционном фильтре-уловителе более чем в 1,5…2 раза эффективнее очистки пылегазовоздушных выбросов от пыли в обычном промышленном циклоне, и степень очистки в зависимости от дисперсности и плотности улавливаемой пыли составляет от 75 до 98% для различных мелкодисперсных аэрозолей конденсированной фазы.
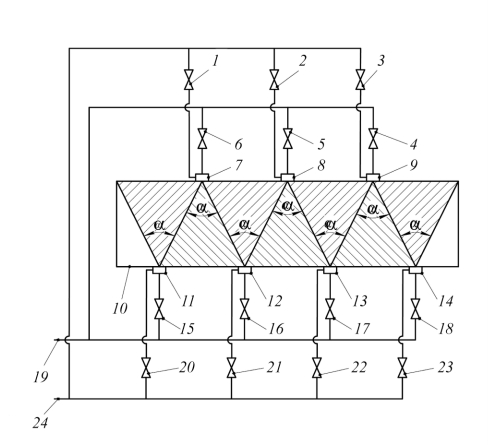
Система для равномерного распределения порошкообразного адсорбента (рис. 6) в очищаемых пылегазовоздушных выбросах [7] оборудована дополнительными устройствами для распыления, например тремя (7, 8, 9) выполненными по конструкции аналогично основным устройствам для распыления адсорбента, например четырьмя, (11, 12, 13, 14), и установленными относительно друг друга на противоположных сторонах корпуса 10 очистительной установки. К дополнительным и основным устройствам для распыления порошкообразного адсорбента 7, 8, 9, 11, 12, 13, 14 по трубопроводу 19 подводится порошкообразный адсорбент, а по трубопроводу 24 – сжатый воздух. Оптимальные параметры потока пылевоздушной смеси (порошкообразный адсорбент + воздух), выходящей их каждого устройства 7, 8, 9, 11, 12, 13, 14, обеспечиваются с помощью регулировочных вентилей 1…6, 15…18, 20…23.
Благодаря плоскопараллельной форме расширяющихся потоков пылевоздушной смеси (адсорбент + воздух) с углом распыла α = 60° от обеих противоположных сторон корпуса 10, обеспечивается равномерное распределение пылевидного адсорбента по всему поперечному сечению очищаемого потока отходящих пылегазовоздушных выбросов в корпусе 10 очистительной установки, что, в свою очередь, повышает степень очистки пылегазовоздушных выбросов от вредных газовых примесей.
Система для равномерного распределения порошкообразного адсорбента в потоке очищаемых пылегазовоздушных выбросов отличается удобством эксплуатации и надежностью в работе.
Термический способ очистки горячих отходящих пылегазовоздушных выбросов от оксидов азота [8] исключает использование катализаторов и газов-восстановителей.
Согласно способу в реактор загружается порция активированного угля и включается нагрев реактора. Поток пылегазовоздушных выбросов направляется на очистку от оксидов азота в реактор, где достижение конечного результата очистки осуществляется с помощью процессов физической адсорбции. В качестве адсорбента используется активированный уголь с динамической активностью по бензолу не менее 45 мин. Взаимодействие оксидов азота с активированным углем протекает в самоподдерживающемся тепловом режиме без дополнительного нагрева. В случае низкого содержания оксидов азота в очищаемых пылегазовоздушных выбросах для поддержания процессов горения активированного угля вводится атмосферный воздух. Очищенные и обезвреженные от оксидов азота пылегазовоздушные выбросы направляются из реактора в атмосферу.
Для эффективной очистки горячих пылегазовоздушных выбросов от механических частиц загрязнений и от диоксида углерода предназначено устройство [9], схема которого изображена на рис. 7.
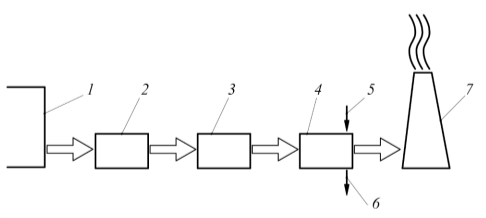
Горячие пылегазовоздушные выбросы от промышленной установки 1 поступают сначала в механический фильтр 2 сухой очистки, а затем в механический фильтр мокрой очистки (скруббер) 3. Очищенные от механических примесей пылегазовоздушные выбросы поступают в абсорбционную очистительную камеру 4, в которой расположены носители, покрытые слоем катализатора, способного удерживать (задерживать) диоксид углерода, и циркулирует водный раствор аммиака. По трубопроводу 5 в абсорбционную камеру 4 поступает обедненный диоксидом углерода (CO2) водный обогащенный раствор аммиака (NH3), а по трубопроводу 6 отводится обогащенный диоксидом углерода обедненный раствор аммиака в регенерационное устройство (на рис. 7 не показано) для повторного использования. Катализатор, которым покрывают носители, подбирают таким образом, чтобы он обладал способностью удерживать диоксид углерода в течение некоторого времени, тем самым увеличивая время контакта диоксида углерода и водного раствора аммиака, являющегося растворителем-абсорбентом.
Поток очищенных пылегазовоздушных выбросов от механических примесей и диоксида углерода из абсорбционной камеры 4 направляется в дымовую трубу 7, а затем в атмосферный воздух.
Устройство для очистки горячих пылегазовоздушных выбросов от механических частиц загрязнений и диоксида углерода удобно в эксплуатации и отличается надежностью в работе.
В современных условиях значительного воздействия недостаточно очищенных от пыли и вредных газовых примесей пылегазовоздушных выбросов предприятий химического и нефтехимического комплекса и других промышленных предприятий на окружающую среду весьма актуален поиск наиболее эффективных и экономичных способов, устройств и установок для их очистки и обезвреживания.
Совершенствование конструкции фильтров, устройств и установок для очистки и обезвреживания производственных пылегазовоздушных выбросов – непрерывный процесс, являющийся составной частью технического прогресса. Он обусловлен все возрастающими экологическими и санитарно-гигиеническими требованиями к окружающей воздушной среде и основан на достижениях во многих областях науки и техники.
Список литературы
- Буренин В.В. Очистка и обезвреживание пылегазовоздушных выбросов химических и нефтехимических предприятий//Химическая техника. 2012. №2.
- Патент РФ 2483780. МПК В01Д 36/02. Электрофильтр с фильтрующими элементами.
- Патент РФ 2483786. МПК В01Д 53/32. Способ очистки газов от аэрозолей.
- Патент РФ 2494794. МПК В01Д 53/86. Способ очистки воздушных потоков от химических загрязнителей и устройство для его осуществления.
- Патент РФ 2493900. МПК В01Д 46/00. Способ сепарации газожидкостного потока.
- Чистяков Я.В., Махнин А.А., Гурилева Н.Л., Володин Н.И. Исследование процесса пылеулавливания в центробежноинерционных аппаратах//Экология и про-мышленность России. 2013. №11.
- Патент РФ 2484903. МПК В05В 7/14. Система для распыления сорбента в среде дымовых газов теплотехнических установок.
- Патент РФ 2495708 Россия. МПК В01Д 53/56. Способ очистки газовых выбросов от оксидов азота.
- Патент РФ 2486946 Россия. МПК В01Д 53/62. Устройство и способ усовершенствованного извлечения CO2 из смешанного потока газа.