Автор: В.В. Буренин, канд. техн. наук, профессор
(Московский автомобильно-дорожный государственный технический университет (МАДИ))Опубликовано на портале «Химическая техника», май 2022
Наиболее острой в настоящее время является проблема повышения экологической безопасности различных производств, в том числе химических, нефтехимических и нефтеперерабатывающих. Решение проблемы экологической безопасности промышленных производств требует точной оценки степени и характера отрицательного влияния тех или иных техногенных факторов на состояние окружающей среды, обоснования критериев экологичности работы технологического оборудования.
Весьма опасными источниками негативного воздействия на природную среду являются пылегазовоздушные выбросы химических, нефтехимических и нефтеперерабатывающих предприятий, содержащие вредные примеси, в атмосферный воздух. По данным Госкомстата РФ ежегодно только нефтеперерабатывающими заводами выбрасывается в атмосферу более 1500 тыс. т загрязняющих веществ, в том числе: углеводородов – 1182; оксидов серы – 232; оксидов азота – 27; оксида углерода – 112; твердых частиц – 14 и прочих – 16 тыс. т. Удельные выбросы вредных веществ в воздушный бассейн в целом по заводам отрасли составили, кг/т нефти: углеводородов – 3,83; оксида серы, азота и углерода соответственно 0,79; 0,09; 0,41 [1].
Наиболее эффективным способом защиты окружающей природной среды от вредного воздействия пылегазовоздушных выбросов промышленных предприятий является переход к безотходному производству, под которым подразумевается создание оптимальных технологических систем с замкнутыми материальными и энергетическими потоками. Такое производство не должно иметь вредных производственных пылегазовоздушных выбросов в атмосферу, не потреблять воду из природных водоемов и не сливать производственные сточные воды, содержащие вредные вещества, на рельеф местности или в водные объекты. Несмотря на то, что создание и внедрение технологических процессов и систем, работающих по замкнутому циклу, является наиболее эффективным способом защиты окружающей среды, однако по технологическим и экономическим соображениям безотходная технология создание беструбных и бессточных промышленных предприятия, полная утилизация отходов производства станут основой нашей производственной деятельности только в будущем. В связи с этим в настоящее время очень актуальны очистка и обезвреживание производственных пылегазовоздушных выбросов с помощью газоочистительного оборудования.
В соответствии с характером вредных примесей, содержащихся в производственных пылегазовоздушных выбросах, различают способы их очистки от взвешенных части загрязнений, от аэрозолей и от газообразных и парообразных примесей. Все способы очистки и обезвреживания пылегазовоздушных выбросов определяются, в первую очередь, физико-химическими свойствами вредных примесей, их агрегатным состоянием, дисперсностью, химическим составом и др. Разнообразие вредных примесей в производственных пылегазовоздушных выбросах приводит к большому разнообразию типов и конструкций фильтров- пылегазоочистителей.
Механическая очистка пылегазовоздушных выбросов от твердых и пластичных частиц загрязнений осуществляется пропусканием их через твердые (пористая керамика, металлокерамика, пластмассы, металлические сетки и др.) и мягкие (ткани, стекловолокно, хлопок, асбоцеллюлоза и др.) фильтрующие перегородки, а также насыпные зернистые (гранулированные) слои фильтрующего материала. Конструктивно фильтрующие перегородки (кроме стационарных) оформляются в виде сменных патронов, кассет, рукавов или неподвижных, движущихся или псевдоожиженных слоев зернистых (гранулированных) частиц. Фильтрующие перегородки и насыпные слои могут быть сухими или мокрыми.
Преимуществами механической очистки являются: сравнительная низкая стоимость очистительного оборудования и высокая эффективность очистки; недостатками – высокое аэродинамическое (гидравлическое) сопротивление и забивание фильтрующих перегородок частицами загрязнений.
Очистка производственных выбросов от загрязнений в силовых фильтрах-пылеуловителях (силовая очистка) осуществляется за счет использования силовых полей: электрического, инерционного, гравитационного, магнитного и т.д.
Механические и силовые фильтры-пылегазоуловители мокрой очистки (скрубберы) предназначены для промывки жидкостями производственных пылегазовоздушных выбросов с целью их очистки от частиц загрязнений и обезвреживания от вредных газовых примесей, а также для извлечения одного или нескольких загрязняющих компонентов для дальнейшего использования. Достоинством скрубберов является сравнительная низкая стоимость очистки пылегазовоздушных выбросов, недостатками – образование большого количества шлака, необходимость очистки образующихся сточных вод, повышенный брызгоунос и требование защиты фильтров от коррозии при обработке агрессивных сред.
В силовых электрических фильтрах (электрофильтрах) очистка пылегазовоздушных выбросов от пыли происходит под действием электрических сил. Частицы пыли, содержащиеся в производственных пылегазовоздушных выбросах, проходя через электрическое поле, получают электрический заряд, а затем осаждаются на противоположно заряженных электродах.
Промышленные системы электростатического осаждения частиц пыли из потока очищаемых пылегазовоздушных выбросов (очистительные системы с электрофильтрами) позволяют обрабатывать (очищать) значительные потоки выбросов (~100 тыс. м3/ч), имеющих высокую температуру и агрессивность. КПД таких очистительных систем достаточно высок.
Для очистки и обезвреживания пылегазовоздушных выбросов промышленных предприятия от вредных газовых загрязнений используются сорбционные, химические, биологические, термические и другие способы очистки.
В последние годы заметно повысился интерес российских и зарубежных фирм по производству техники для очистки и обезвреживания пылегазовоздушных выбросов промышленных предприятий к созданию новых фильтров-пылегазоуловителей с высокими технико-экономическими показателями [2].
ЗАО «НТЦ «Бакор» (Россия) разработало пористые проницаемые керамические материалы различной структуры и технологию получения фильтрующих элементов для механических фильтров из этих материалов [3]. Фильтрующие элементы из этой керамики отличаются низким гидравлическим (аэродинамическим) сопротивлением, оптимальным размером пор и максимальной эффективностью при очистке, стойкостью против кислот и щелочей, способностью выдерживать резкие колебания температур (термоудары) очищаемых пылегазовоздушных выбросов, стабильностью физико-механических свойств в течение длительного времени при воздействии очищаемых горячих запыленных газов, хорошей регенерируемостью, т.е. восстановлением фильтрующих характеристик после периодической продувки сжатым воздухом высокого давления.
Использование в механических фильтрах-пылеуловителях фильтрующих элементов из пористой проницаемой керамики дает большой экономический и экологический эффект. Кроме того, экологическая составляющая этого эффекта может быть увеличена за счет нанесения катализатора и химических веществ на высокопористую поверхность фильтрующих элементов, т.е. появляется дополнительная возможность очистки горячих газов (горячих производственных пылегазовоздушных выбросов) от паров вредных веществ.
Повышенной эффективностью очистки горячих производственных пылегазовоздушных выбросов от твердых и пластичных частиц загрязнений отличается механический фильтр-пылеуловитель с фильтрующей перегородкой в виде слоев зерновых (гранулированных) частиц [4]. Подачу загрязненных выбросов на очистку производят через гранулированный слой технического углерода с размером гранул 0,5…3,0 мм, насыпной плотностью 300…1000 кг/м3 и высотой фильтрующего слоя 100…200 мм. Производственные выбросы подаются в фильтр-пылеуловителей сверху вниз и пропускаются через слой гранул со скоростью 0,5…1,5 м/с в течение 20…40 с с интервалом от 3 до 20 минут.
Высокую степень очистки производственных пылегазовоздушных выбросов от частиц пыли и сажи обеспечивает силовой двухзонный электрофильтр [5], включающий (рис. 1) корпус 1, ионизатор 2, осадитель 3, состоящий из установленных параллельно потоку очищаемых пылегазовоздушных выбросов коронирующих 4 и некоронирующих 5 электродов, и источник высокого напряжения 6. Поток очищаемых пылегазовоздушных выбросов по горизонтали направляется на вход корпуса 1 и поступает в ионизатор 2, в который из устройства для образования гидратированных ионов 7, содержащего закрепленную в нижней части корпуса 1 емкость 8 с водой, и расположенными в ней кольцевым короткозамкнутым анодом 9 и замкнутым в кварцевую трубку 10 цилиндрическим катодом 11, перпендикулярно очищаемому потоку диспергируются гидратированные ионы, при соударении которых с нейтральными частицами пыли и сажи происходит ионизация последних. При включении таймера 14 происходит срабатывание электронного ключа 13 и замыкание электрической цепи, состоящей из отрицательно заряженной пластины конденсаторной батареи 15, токопровода 12, цилиндрического катода 11, замкнутого в кварцевую трубку 10, паров воды над катодом 11, воды в емкости 8, короткозамкнутого анода 9, соединенного токопроводом с положительно заряженной пластиной конденсаторной батареи 15.
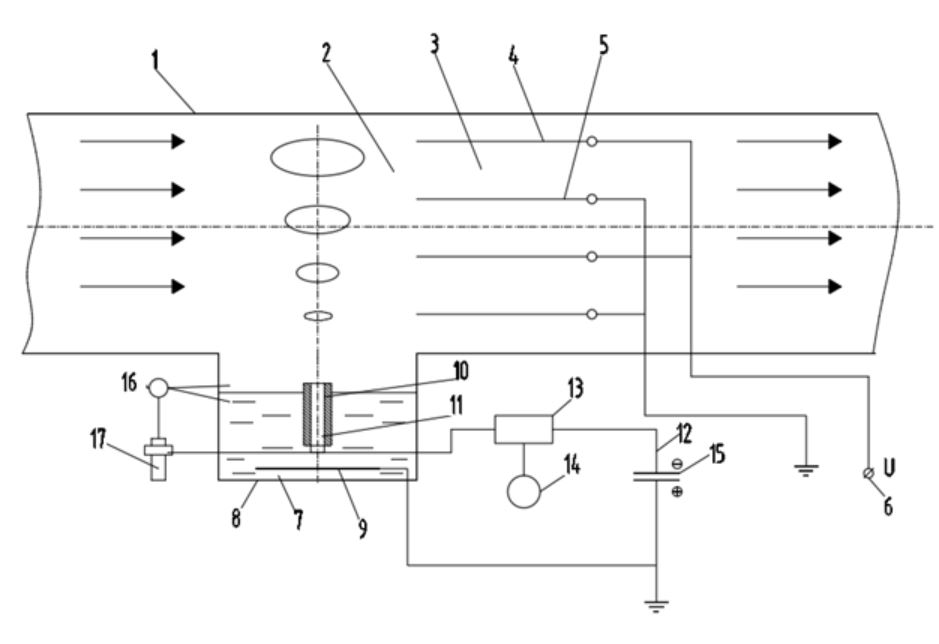
При смачивании каплей воды верхней торцовой части цилиндрического катода 11 из нее вылетает плазменная струя на высоту 15…20 мм. Через 0,1 с электрический разряд прекращается, образуется плазмоид, который поднимается вверх перпендикулярно потоку очищаемых пылегазовоздушных выбросов. Через 1…2 с оболочка плазмоида исчезает и положительно и отрицательно заряженные гидратированные ионы поступают в очищаемый поток пылегазовоздушных выбросов. При соударении с нейтральными частицами пыли и сажи положительно и отрицательно заряженные гидратированные ионы сообщают им заряд, т.е. ионизируют их. Далее поток пылегазовоздушных выбросов, содержащий ионизированные частицы пыли и сажи, поступает в пространство между коронирующими 4 и некоронирующими 5 электродами осадителя 3.
При этом между коронирующими электродами 4, подключенными к выводу высоковольтного источника 6, и некоронирующими электродами 5, соединенными с заземленным выводом источника напряжения 6, создается электрическое поле. Под действием кулоновских сил электрического поля ионизированные частицы пыли и сажи осаждаются на некоронирующих электродах 5 и выводятся из очищаемого потока пылегазовоздушных выбросов.
Изменение положения верхней торцовой части катода 11 над уровнем воды регистрируется с помощью фотодатчика 16, сигнал которого поступает на механизм регулирования положения катода 17, выполненного в виде реечной передачи. Если верхняя торцовая часть цилиндрического катода 11 опускается ниже уровня воды в емкости 8, то включается привод реечной передачи (не показан) и верхняя торцовая часть катода 11 поднимается вверх. Наоборот, если верхняя торцовая часть катода 11 поднимается выше уровня воды на высоту более 5 мм, то включается привод реечной передачи (не показан) и верхняя торцовая часть катода 11 опускается вниз.
Эксплуатация электрофильтра в промышленных условиях позволяет снизить потребление электрической энергии за счет снижения установочной мощности источника высокого напряжения 6.
Максимальную степень очистки пылегазовоздушных выбросов от пыли независимо от ее концентрации, дисперсности, удельного электрического сопротивления обеспечивает комбинированный фильтр-пылеуловитель [6], включающий электрофильтр и последовательно за электрофильтром установленный механический тканевый фильтр с соотношением активных объемов тканевого фильтра к электрофильтру 0,1…0,9 (рис. 2).
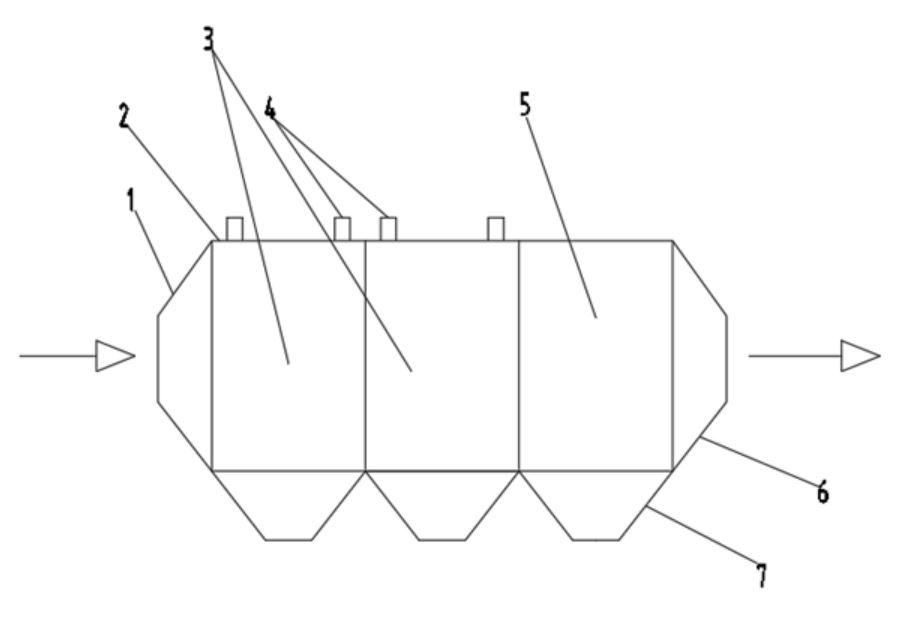
Активным объемом электрофильтра является объем фильтра-пылеуловителя, который занимает электродная система, а в тканевом фильтре – объем фильтра-пылеуловителя, занимаемый фильтрационными элементами. Пылегазовоздушные выбросы на очистку входят в диффузор 1 корпуса 2 фильтра-пылеуловителя, очищаются сначала в электрофильтре 3, состоящем из двух секций, а затем в механическом тканевом фильтре 5, и очищенными выходят из конфузора 6. Высокое напряжение в электрофильтр 3 подается через изоляторы 4, а уловленная пыль поступает в бункер 7. Фильтр-пылеуловитель имеет большой ресурс работы.
Увеличенной степенью силовой очистки пылегазовоздушных выбросов от частиц пыли и повышенной стабильностью брикетирования, отличается способ очистки [7] (рис. 3), реализуемый с помощью силового фильтра циклонного типа (циклона).
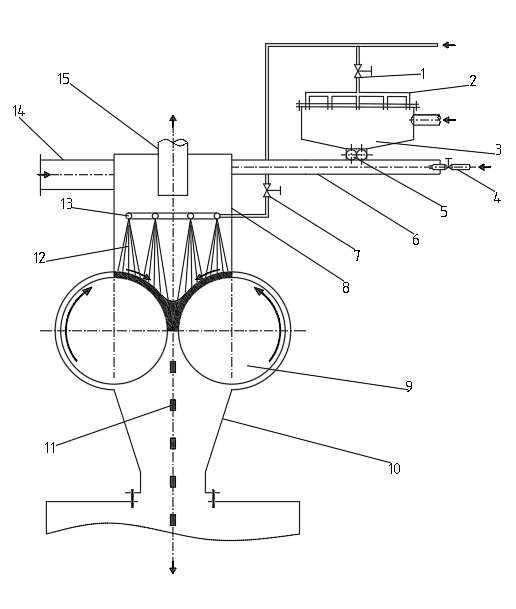
Поток производственных пылегазовоздушных выбросов подается тангенциально через подводящий патрубок 14 в цилиндрический корпус 8 циклона. Также из бункера 3 в корпус 8 циклона через питатели 5 и аэратор 6 поступают предварительно увлажненные коагулирующей жидкостью с помощью форсунок 2 и аэрируемые сжатым воздухом, подаваемым через сопло 4, древесные опилки. В процессе очистки от пыли поток пылегазовоздушных выбросов и увлажненные древесные опилки за счет действия центробежных сил совершают поступательное вращательное движение сверху вниз, в ходе которого за счет инерционной коагуляции пыль улавливается увлажненными древесными опилками. Увлажненные древесные опилки, насыщенные пылью, поступают в зону орошения вспомогательной коагулирующей жидкости, подаваемой через трубопровод 13 в виде струй 12. Образующаяся смесь уловленной пыли, жидкости и древесных опилок поступает на вращающиеся рабочие поверхности вальцового пресса 9. Затем смесь транспортируется вальцами в загрузочный узел пресса 9, где брикетируется с получением брикетов 11, которые поступают в пылесборник 10, выполняющий функцию накопителя брикетов. Регулирование расхода коагулирующей жидкости, подаваемой в бункер 3 и в нижнюю часть корпуса 8 циклона, осуществляется с помощью запорной арматуры 1 и 7. Очищенный поток пылегазовоздушных выбросов выходит в окружающую среду через выходной трубопровод 15.
Повышенной эффективностью и надежностью процесса пылеулавливания отличается силовой фильтр-циклон мокрой очистки (скруббер) [8] (рис. 4), содержащий корпус 7 с периферийным вводом потока очищаемых пылегазовоздушных выбросов через входной тангенциальный патрубок 1.
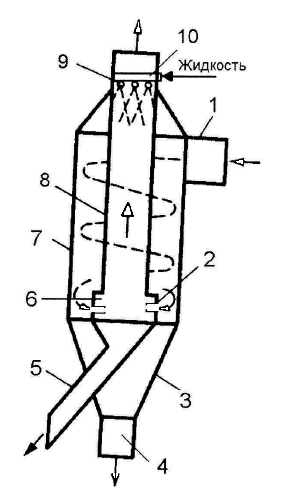
Внутри корпуса 7 поток пылегазовоздушных выбросов закручивается и по нисходящей спирали опускается вниз к нижнему торцу выходной трубы 8. При этом более крупные частицы пыли центробежной силой прижимаются к внутренней поверхности корпуса 7 и сползают в нижнюю коническую часть 3 корпуса 7, из которой выпадают в бункер 4. Освободившись от крупных частиц пыли, поток очищаемых пылегазовоздушных выбросов через отверстия 2 и 6 в нижней части выходной трубы 8 попадает в нее, движется вверх навстречу водяным факелам, образуемым форсунками 9. Очищенные пылегазовоздушные выбросы удаляются в окружающую среду через патрубок 10. Орошение очищаемых пылегазовоздушных выбросов водой в выпускной трубе 8 приводит к дополнительной их очистке от мелких частиц пыли. Вода вместе со шламом (мелкими частицами пыли) удаляется по трубе 5.
Фильтр-циклон с двухступенчатой мокрой очисткой пылегазовоздушных выбросов от частиц пыли имеет высокую степень пылеулавливания (до 90–92 %) и низкое аэродинамическое (гидравлическое) сопротивление потоку очищаемых пылегазовоздушных выбросов.
Пониженными энергозатратами при работе и повышенным качеством очистки производственных пылегазовоздушных выбросов отличается силовой вихревой фильтр-пылеуловитель мокрой очистки (скруббер) [9], содержащий цилиндрическую сепарационную камеру 5 (рис. 5) с верхним 19 и нижним 7 газоходами для подачи на очистку производственных пылегазовоздушных выбросов.
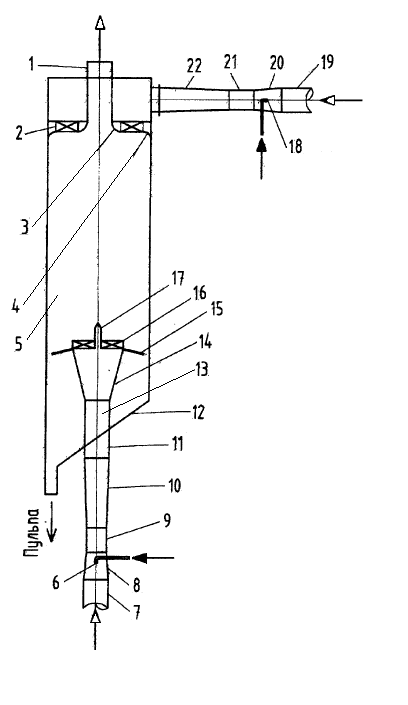
Верхний 19 и нижний 7 газоходы состоят соответственно из конфузора 20 или 8, горловины 21 или 9, диффузора 22 или 10. В нижней части сепарационной камеры 5 расположены патрубок 11, стабилизирующее устройство 13, цилиндрический обтекатель 17, лопаточный завихритель 16, отбойная шайба 15 и бункер 12. В верхней части сепарационной камеры 5 расположены лопаточный завихритель 2, стабилизирующие обтекатели 3 и 4 и коаксиально расположенный выходной патрубок 1 для очищенных выбросов.
В конфузоре 20 газохода 19 и конфузоре 8 газохода 7 перед горловинами соответственно 21 и 9 навстречу потокам очищаемых пылегазовоздушных выбросов установлены соответственно форсунки 18 и 6 для подачи воды, дисперсный состав которой составляет соответственно 10…70 мкм и 2…10 мкм, при этом расход воды для орошения потоков по газоходам 19 и 7 очищаемых пылегазовоздушных выбросов через форсунку 18 в 2–3 раза больше, чем расход воды через форсунку 6.
Дисперсный состав частиц разбрызгиваемой форсункой 18 воды способствует лучшей сепарации частиц пыли из очищаемого потока пылегазовоздушных выбросов и лучшему смыву уловленной пыли. Дисперсный состав частиц разбрызгиваемой форсункой 6 воды в поток очищаемых пылегазовоздушных выбросов обеспечивает лучшую взаимную коагуляцию пылевых и жидких частиц во всем объеме сепарационной камеры 5. Кроме того, орошение водой через форсунки 18 и 6 потоков очищаемых пылегазовоздушных выбросов приводит к образованию на внутренней поверхности сепарационной камеры 5 жидкой пленки, которая препятствует отскоку пылевидных частиц от стенок камеры 5 и способствует их улавливанию и смыванию в сборный бункер 12.
Повышенной эффективностью мокрого пылеулавливания отличается силовой вихревой фильтр-пылеуловитель с акустическим распылением жидкости [10], содержащий цилиндрический корпус 1 (рис. 6) с коническим бункером 10, осевой вход 9 (ввод на очистку запыленных пылегазовоздушных выбросов) с завихрителем 6, обтекателем 5, отбойной шайбой 8 и эжекционным насадком 7, ввод 2 вторичного потока пылегазовоздушных выбросов с завихрителем 4, осевой патрубок 3 для вывода очищенных пылегазовоздушных выбросов. Эжекционный насадок 7 образует со стенкой центрального входа (ввода) 9 кольцевой канал, сообщающийся с полостью корпуса 1 под отбойной шайбой 8, которая выполняется конической (тарельчатой), а кольцевой канал эжекционного насадка 7 образуется цилиндрическими или коническими поверхностями соответственно осевого ввода 9 и эжекционного насадка 7, при этом плоскость среза эжекционного насадка располагается ниже плоскости среза конической шайбы 8.
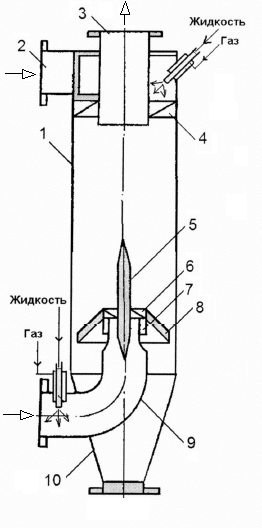
В нижнем патрубке осевого ввода 9 запыленных пылегазовоздушных выбросов с завихрителем 6, обтекателем 5 и отбойной шайбой 8, а также в верхнем патрубке периферийного ввода 2 вторичного потока с завихрителем 4 установлены акустические форсунки для подачи орошающей жидкости.
Поток очищаемых пылегазовоздушных выбросов входит через верхний ввод 2 и, закручиваясь лопаточным завихрителем 4, движется вниз в корпусе 1. Навстречу ему снизу через осевой ввод 9 подается первичный поток пылегазовоздушных выбросов, который закручивается аксиально-лопаточным завихрителем 6 в ту же сторону, что нисходящий вторичный поток. Частицы пыли при этом под действием центробежных сил отбрасываются к стенкам корпуса 1. Закрученный вторичный поток, наталкиваясь на отбойную шайбу 8, частично разворачивается, взаимодействуя с первичным потоком, исходящим из центрального ввода 9. Частицы пыли, обладающие большей инерцией, отделяются от потока при его повороте у отбойной шайбы 8 и через зазор между ней и стенками корпуса 1 вылетают в бункер 10. В бункере создается разрежение благодаря эжекционной насадке 7, установленной в осевом вводе 9 вплотную к завихрителю 6. Отсасываемый эжектором поток, который может содержать самые мелкие частицы пыли, особенно с малым удельным весом и размером менее 10 мкм (легкие твердые частицы), поступает сразу на лопатки завихрителя 6, при этом на максимальном радиусе, что обеспечивает максимальную их закрутку и вывод с периферии газовой струи во вторичный поток и затем опять в бункер 10. Это способствует оптимальному взаимодействию закрученной струи первичного потока с нисходящим потоком закрученного вторичного потока и повышению эффективности пылеулавливания за счет возврата в бункер частиц пыли с малым удельным весом.
Таким образом, выполнение корпуса 1 силового вихревого фильтра-пылеуловителя цилиндрическим и наличие эжекционного насадка 7, установленного под отбойной шайбой 8, позволяет обеспечить высокую эффективность отделения мелких частиц загрязнений (пыли) с малым удельным весом и большую надежность в работе фильтра-пылеуловителя.
Высокое качество очистки потока производственных пылегазовоздушных выбросов от частиц пыли обеспечивает скруббер с подвижной насадкой [11], содержащий корпус 1 (рис. 7) с патрубками 9 и 5 соответственно для входа на очистку и выхода очищенного потока выбросов.
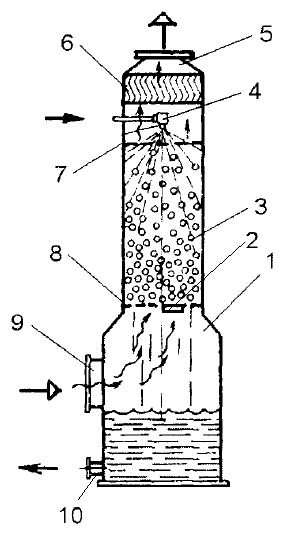
Запыленный поток выбросов поступает в корпус 1 через патрубок 9 и встречает на своем пути завесу из насадки 3 в виде полых шаров, выполненных из упругих материалов и смачиваемых водой из оросительного устройства 4. Слой насадки 3 расположен между нижней опорно-распределительной тарелкой 8 и верхней ограничительной тарелкой 7. Для обеспечения свободного перемещения насадки 3 в режиме полного развитого псевдоожижения, при котором увеличивается эффективность взаимодействия насадки 3 с очищаемым газовым потоком выбросов и водой из оросительного устройства 4, на нижней опорно-распределительной тарелке 8 установлен вибратор 2, создающий режим колебаний или автоколебаний, который способствует увеличению эффективности взаимодействия насадки 3 с орошаемой водой. Задержанные частицы пыли из очищаемых выбросов отводятся с водой из корпуса 1 скруббера через патрубок 10. Брызгоуловитель 6 установлен в корпусе 1 перед патрубком 5 выхода очищенного потока выбросов.
Способ очистки отходящих дымовых газов от диоксида углерода методом абсорбции [12] включает абсорбцию диоксида углерода водным раствором абсорбента с содержанием моноэтаноламина (МЭА) 10–14 % мас. При степени насыщения абсорбицонного раствора не менее 0,65, десорбцию диоксида углерода при температуре 70…90 °С с получением диоксида углерода и обедненного диоксидом углерода раствора абсорбента, который возвращают на стадию абсорбции полностью без дополнительной очистки. Способ очистки отходящих дымовых газов отличается минимизацией потерь МЭА, связанных с высокотемпературной деградацией, снижением коррозии очистительного оборудования, уменьшением расхода тепла и повышением степени удаления диоксида углерода из отходящих дымовых газов.
Отличается удобством эксплуатации устройство для мокрой комплексной очистки производственных пылегазовоздушных выбросов от вредных примесей [13], состоящее из двух контуров очистки.
Первый контур очистки содержит газопромыватель с промывочной жидкостью, каплеотделитель для отделения отходящих пылегазоводушных выбросов после газопромывателя от промывочной жидкости, регенерационный резервуар для сбора отделенной промывочной жидкости и удаления твердых частиц загрязнений из промывочной жидкости, блок подачи для возвращения промывочной жидкости из регенерационного резервуара в газопромыватель.
Второй контур очистки содержит трубопровод для отвода части потока промывочной жидкости из первого контура, колонный десорбер для удаления органических веществ из отведенной промывочной жидкости отдувочным газом, подаваемым в промывочную жидкость, возвратный трубопровод для частичного возвращения промывочной жидкости после удаления накопленных органических веществ в первый контур.
Повышенной эффективностью и надежностью процесса пылеулавливания из потока производственных пылегазовоздушных выбросов, а также пониженной металлоемкостью отличается фильтр-пылеуловитель комплексной очистки [14], содержащий корпус, опорную часть с бункером для сбора пыли, входной и выходной короба фильтровальной секции с фильтрами рукавного типа, систему регенерации фильтра-пылеуловителя. Во входном коробе фильтровальной секции установлено газораспределительное устройство, выполненное в виде створчатой пластины с механизмом изменения ее ширины и блоком управления, состоящей из двух створок, плотно прилегающих друг к другу таким образом, что они образуют пластину, выполняющую функции инерционного пылеотделительного элемента. Система регенерации рукавных фильтров выполнена с механизмом импульсной продувки, которая снабжена блоком управления каждого электромагнитного клапана сопл и соединена с общим блоком управления регенерацией, связанным электронной связью с общим микропроцессором, при этом гидравлическое сопротивление фильтровальной секции составляет 15–25% гидравлического сопротивления всего фильтра-пылеуловителя комплексной очистки производственных пылегазовоздушных выбросов, а материал фильтров рукавного типа обладает повышенными звукопоглощающими свойствами. Корпусные детали и ограждения фильтра-пылеуловителя выполнены из конструкционных композиционных или полимерных материалов, например, полиэтилена, капрона, полиуретана, с помощью литья, штамповки, формования, при этом на их поверхности нанесен слой мягкого вибродемпфирующего материала.
Фильтр-пылеуловитель комплексной очистки имеет высокую производительность по очистке производственных пылегазовоздушных выбросов, имеющих обычную и высокую температуру.
Повышенной степенью очистки производственных пылегазовоздушных выбросов от токсичных полициклических ароматических углеводородов, в том числе бензапирена, пониженной кислотной коррозией газохода и экономичностью работы отличается установка [15], блок-схема работы которой изображена на рис. 8.
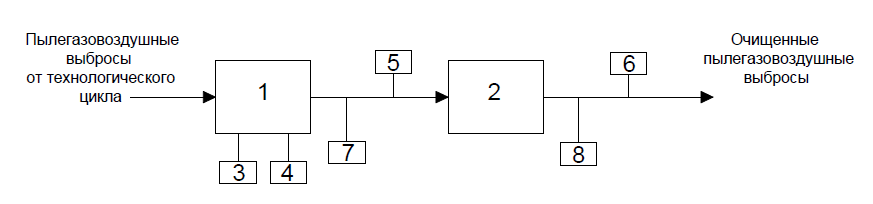
Пылегазовоздушные (газовые) выбросы от технологического оборудования (цикла) поступают на очистку в устройство 1, куда подаются также озон и вода в виде жидкости или пара, где подвергаются облучению ультрафиолетовым излучением устройством 3 при чередовании больших и меньших значений средней плотности световой энергии в спектральном интервале длин волн 310…410 нм при помощи импульсно-периодического генератора электрического разряда. Озон поступает в устройство 1 из камеры предварительного облучения 4. Затем насыщенные озоном пылегазовоздушные выбросы облучают с помощью устройства 2 ультрафиолетовым излучением с чередованием больших и меньших значений средней плотности световой энергии в спектральном интервале длин волн 310…410 нм. Перед устройством 2 облучения ультрафиолетовым излучением и после него в газоходе установлены пробоотборники 5 и 6 для взятия проб на смолистые соединения, включая бензапирен. После устройств 1 и 2 установлены устройства для удаления твердых отходов (твердых частиц загрязнений) 7 и 8 соответственно.
При использовании установки для очистки производственных пылегазовоздушных выбросов от полициклических ароматических углеводородов, в том числе бензапирена, степень очистки достигает 90–99%, а в некоторых случаях в очищенных производственных пылегазовоздушных выбросах присутствуют лишь следы такого канцерогенного (токсичного) соединения, как бензапирен.
В современных условиях значительного воздействия недостаточно очищенных пылегазовоздушных выбросов промышленных предприятий, в том числе предприятий химических, нефтехимических и нефтеперерабатывающих производств, от пыли и вредных газовых примесей на окружающую среду весьма актуален поиск наиболее эффективных и экономичных способов и устройств для их очистки и обезвреживания. Одной из особенностей эффективной очистки производственных пылегазовоздушных выбросов от вредных примесей является ситуация, связанная с часто меняющимися условиями проведения процесса очистки выбросов, в частности с изменением расхода и концентрации примесей в очищаемых пылегазовоздушных выбросах. Разрабатываемые способы и устройства для очистки и обезвреживания производственных пылегазовоздушных выбросов должны учитывать требования к качеству очищенных выбросов, физико-химические свойства улавливаемой пыли и вредных газовых примесей, энергетические и экономические показатели очищающих устройств и др.
Список литературы
- Катин В.Д., Булгаков С.В. Проблемы повышения экологической безопасности нефтеперерабатывающих производств и пути их решения // Безопасность жизнедеятельности. 2019. №2. С. 44–48.
- Буренин В.В. Очистка и обезвреживание пылегазовоздушных выбросов химических и нефтехимических предприятий // Химическая техника. 2012. №2. С. 41–44.
- Красный Б.Л., Тарасовский В.П., Красный А.Б. Принципиально новые возможности очистки высокотемпературных газов от пыли без их предварительного охлаждения // Химическая техничка. 2019. №11. С. 27–30.
- Пат. 2569099 Россия. МПК B 01 D 46/30. Способ фильтрации аэрозолей в зернистом фильтре.
- Пат. 2476271 Россия. МПК B03 C 3/08. Электрофильтр двухзонный.
- Пат. 2248837 Россия. МПК B 01 D 36/02. Пылеулавливающий аппарат.
- Пат. 2567310 Россия. МПК B 04 C 5/00. Способ очистки газов от пыли.
- Пат. 2646923 Россия. МПК B 04C 9/00. Циклон комбинированный.
- Пат. 2650999 Россия. МПК B 04C 3/06. Вихревой пылеуловитель.
- Пат. 2654730 Россия. МПК B01D 47/06. Вихревой пылеуловитель с акустическим распылением жидкости.
- Пат. 2654744 Россия. Скруббер с подвижной насадкой.
- Пат. 2656661 Россия. МПК B 01 D 53/14. Способ удаления диоксида углерода из газовых смесей.
- Пат. 2645143 Россия. МПК B 01 D 47/0. Способ и устройство для очистки отходящего воздуха, полученного при переработке древесины.
- Пат. 2650922 Россия. МПК В 04 С 9/00. Устройство пылеулавливания.
- Пат. 2541320 Россия. МПК В 01 D 53/32. Способ очистки газовых выбросов от полициклических ароматических углеводородов, в том числе бензапирена.