Авторы: В.В. Мусатов (ЗАО «ГИАП-ДИСТцентр), В.И. Иванов (НИИИН МНПО «Спектр»).
Опубликовано в журнале Химическая техника №7/2015
Введением Федерального закона от 4 марта 2013 г. №22-ФЗ [1] был открыт новый этап в развитии подходов к оценке и регулированию промышленной безопасности (ПБ). Этот закон фактически регламентировал необходимость использования показателя риска аварии в качестве количественной оценки ПБ. Надеемся, что последняя редакция закона о промышленной безопасности №22 завершила важный этап дальнейшего развития законодательных представлений в области ПБ.
То, что закон о ПБ претерпел с 1997 г. много поправок, можно интерпретировать как недостаток первичных редакций, но, скорее всего, это знак ускоренного развития представлений в области ПБ. Обычно стандарты, законы и другие нормативные документы отражают предшествующий опыт развития области, охватываемой нормотворчеством. В законе №22-ФЗ использован как опыт отечественной практики, так и направления международных тенденций в развитии ПБ. Одним из важнейших направлений развития является использование показателя риска аварии для оценки ПБ.
Действующие методики оценки риска аварии, разработанные после принятия упомянутого закона, включают в качестве основных операций «определение сценариев развития аварии, оценку частоты возможных сценариев аварий, оценку возможных последствий аварий по рассматриваемым сценариям, расчет показателей риска аварии» [2]. Однако количественная оценка (тем более расчет) риска с использованием действующих методик в настоящее время затруднительна (в части получения и дальнейшего использования величины вероятности аварии). Это связано с тем, что в существующих методических документах не предусмотрено использование информации, получаемой при выполнении технического диагностирования.
Современные требования количественной оценки риска аварии не могут быть обеспечены без данных о реальном состоянии технических устройств, которые можно получить только при выполнении комплекса работ по неразрушающему контролю и техническому диагностированию (НК и ТД). Техническое диагностирование – «Определение технического состояния объекта с целью оценки безопасности и прогнозирования ресурса». Основными составляющими технического диагностирования являются НК, механика разрушения (МР), анализ коррозии, металловедение.
В принятых документах по оценке риска аварии (например, в руководстве [2] и во многих других) «строят» логические цепочки деревьев событий, на «входе» которых используют значение интенсивности (частота) событий, которое получают при статистической обработке (усреднение числа аварий). Эти данные собираются в течение нескольких лет, и они не отличаются высокой точностью. В статистике отсутствуют данные о техническом состоянии конкретного технического устройства, получаемые только при выполнении НК и ТД. Кроме того, как показано в работе [3], значение частоты аварий имеет большой разброс. При этом максимальные разбросы оценок вероятности поражения персонала объекта для различных вариантов аварийных ситуаций имеют значения, достигающие 2…4 порядков (рис. 7.1 в руководстве [2]).
Это стимулирует дальнейшее развитие подходов оценки риска аварии в направлении использования НК и ТД.
Несмотря на отмеченные ограничения, «рисковый» подход при оценке ПБ является основным направлением развития технологий, используемых в практике обеспечения ПБ. Даже первый этап использования «рисковых» подходов способствует повышению уровня ПБ, поскольку существенно повышает культуру эксплуатации сложных технических устройств, применяемых на опасных производственных объектах I и II классов опасности.
Требование оценки риска аварии инициирует также ускорение развития новых подходов при использовании НК и ТД. До сих пор в промышленности используется правило, основанное на бинарном критерии оценки технического состояния объекта: «годен – не годен», «брак – не брак». При этом отсутствует оценка реального технического состояния объекта. В настоящее время такой подход следует признать устаревшим. Необходимы более дифференцированные оценки. Следует не просто обнаруживать дефекты и грубо определять их параметры, подгоняя зачастую к значениям, позволяющим считать объекты годными к эксплуатации. Необходимо проводить операции измерения параметров дефектов и рассчитывать их влияние на прочность объекта, пригодность его к дальнейшей эксплуатации и оценку вероятности аварии объекта, содержащего дефекты. Произошло разделение методов НК на измерительные и индикаторные, которые также играют важную роль.
При этом возникают задачи практического использования новых показателей и характеристик, повышающих информативность НК и ТД. С 70-х годов прошлого века за рубежом было выполнено более 20 программ, посвященных развитию методов НК в направлении повышения информативности, оценки достоверности, использования вероятностных оценок параметров контроля, характеристик обнаружения и пропуска дефектов, измерения их параметров. Названия некоторых из этих программ перечислены в статье [4].
Наиболее мощной программой по развитию новых подходов в НК была программа PISC (Programme for the Inspection of Steel Components), которая длилась более 20 лет (с 1975 по 1995 г.) и состояла из трех этапов. Обширный материал и результаты выполнения первого этапа программы PISC содержатся в книге [5]. В ней приведены, например, сведения об использовании акустической голографии, применении фазированных решеток и других передовых методов. Эти направления развивались также в отечественных разработках, выполненных отдельными исследователями [6–11]. Существенным достижением в области НК можно считать подход, представленный в работе [8], позволяющий впервые в практике НК проводить оценку пригодности объекта к эксплуатации и определение срока работы объекта путем непосредственного расчета прочности с использованием измеренных параметров дефектов. При этом измеряют размеры обнаруженных дефектов, рассчитывают прочность объекта и назначают время дальнейшей эксплуатации объекта, содержащего дефекты того или иного размера [8].
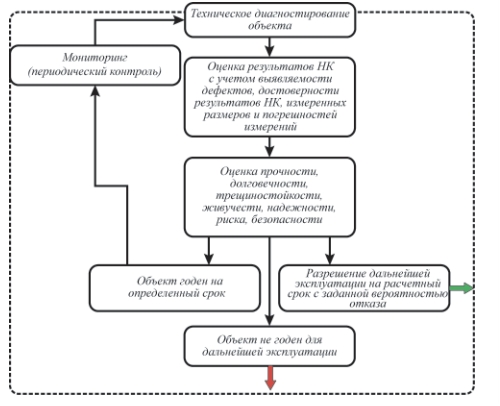
Обобщенная схема, реализующая подход, основанный на использовании достижений в области НК и ТД, приведена на рис. 1. Методы исследования и получение выводов о состоянии объекта, основанных на рассмотрении проблем прочности, долговечности, трещиностойкости, живучести с применением критериев риска, приведены в работе [9]. Для реализации схемы рис. 1 необходимо иметь информацию о дефектности объекта, полученную с использованием следующих характеристик НК:
- калибровочной характеристики – характеристики дефектометрической корреляции, представляющей зависимость, связывающую реальные размеры дефектов и приборные показания размеров дефектов;
- вероятностной диаграммы обнаружения дефектов – зависимости вероятности обнаружения дефектов от их размеров Ро.д(а) – выявляемость, и соответственно диаграммы пропуска дефекта Рпр = 1 – Ро.д(а) [6, 11, 12], где а – размер (высота) дефекта;
- диаграммы информативности НК (в зарубежной литературе ROC-диаграмма – Receiver Operation Characteristic).
В отечественной практике эти диаграммы представляют в форме «Матрицы достоверности» [13–15].
Примеры перечисленных характеристик приведены на рис. 2–5.
Основным показателем НК, позволяющим в настоящее время непосредственно оценить вероятность разрушения объекта, должна стать калибровочная характеристика, которая дает возможность по показанию системы НК определить параметры дефектов (см. рис. 2).
В соответствии с моделями МР разрушение объекта, содержащего трещину, являющуюся максимально опасным дефектом, происходит при условии, когда коэффициент интенсивности напряжений в области максимальных напряжений (на кончике трещины) превышает критическое значение Кс. Это условие для трещины отрыва имеет вид
где q – коэффициент, определяемый видом нагружения, размерами и формой конструкции; σ – значение механических напряжений в результате действия приложенных нагрузок; a – глубина трещины; KIc – определяется прочностными свойствами материала.
При постоянной нагрузке и увеличении размера дефекта неопределенность момента разрушения (обусловливающая вероятность разрушения) связана с неопределенностью знания свойств материала и ошибками измерения размеров трещины.
1 – консервативная оценка, 2 – реалистическая оценка,
3 – оптимистическая оценка, 4 – допустимый уровень вероятности разрушения (для корпуса реактора составляет 10–7 на реактор в год) [9]
Таким образом, измерив глубину трещины a и используя кривую 2 (см. рис. 3), можно оценить вероятность разрушения объекта (в данном случае – корпус атомного реактора). Следует отметить, что кривые, подобные приведенным на рис. 3, необходимо рассчитывать для каждого объекта, риск разрушения которых необходимо определить.
Другой важной характеристикой, которая служит показателем качества системы НК и может повлиять на вероятность аварии, является вероятность обнаружения дефекта – Pо.д. При обнаружении относительно крупного дефекта оценка вероятности разрушения производится описанным выше способом. Вероятность присутствия в объекте двух дефектов, существенно влияющих на прочность объекта, весьма мала. Как показано в работе [10], разрушение объекта, как правило, происходит в результате развития одной трещины максимального размера, поэтому оценку прочности объекта можно проводить, используя параметры обнаруженного дефекта максимального размера, вероятность обнаружения которого для качественной системы НК составляет
Ро.д ≥ 0,6…0,8. В связи с этим знание величины Ро.д весьма важно.
Уровень проработок подходов при получении Ро.д-диаграмм таков, что они могут быть получены теоретически [11], экспериментально [12], а также посредством использования методики компьютерного моделирования [7]. Данный показатель может быть использован для оценки вероятности разрушения в случае, если известно исходное распределение дефектов в объекте.
а – схематическое представление диаграммы информативности (m – уменьшение отношения сигнал/шум, n – последовательное увеличение квалификации системы НК – 123 [15]); б – результаты различных экспериментов
для построения диаграммы информативности НК [16]
В отечественной практике эти диаграммы представляют в форме «Матрицы достоверности» [13–15].
Следует подчеркнуть, что Ро.д(а) на рис. 5, а не является функцией Рл.о, но плоскость этой диаграммы представляет собой комплексную характеристику качества системы НК. Линия 1 – случай, когда система НК работает в условиях равнозначности вероятности обнаружения дефекта и вероятности ложного показания дефекта при его отсутствии, т.е. это ситуация полной неопределенности (максимум энтропии). Кривые 2 и 3 относятся к системам НК все более высокого качества.
На рис. 5, б представлены точки, соответствующие показателям работы различных методик НК, полученные в экспериментах [16]. Рекомендуемая область работы системы НК – Ро.д(а) ≥ 0,8 и Рл.о ≤ 0,2. Использование таких диаграмм, как Ро.д(а) и диаграмма информативности, в практике промышленного НК в настоящее время пока не нашло широкого применения, однако, по нашему мнению, их использование неизбежно, несмотря на то, что потребует значительных затрат.
Можно констатировать, что научная база НК и ТД, а также методические аспекты проработаны в степени, достаточной для адекватного использования при контроле промышленных объектов таких показателей, как калибровочная характеристика, показатель выявляемости и диаграмма информативности для оценки риска аварии. Но для реального освоения этих характеристик и новых подходов и их практического использования необходимо создание методических документов –стандартов. Для этого потребуется финансирование в меньших размерах, чем это потребовалось бы 20…30 лет тому назад. Но без финансирования указанных разработок невозможно их продвижения в промышленность.
Таким образом, использование НК и ТД при оценке риска аварии позволяет:
- сделать показатель величины риска действительно количественной характеристикой ПБ и существенно уменьшить погрешность измерения и расчета риска аварии;
- придать импульс дальнейшему развитию количественных методов оценки (измерения) риска и использованию в промышленности наработанных в лабораториях методик НК и ТД;
- оптимизировать затраты на обеспечение ПБ и ввести в практику количественное обоснование оптимальных затрат. В случаях, когда обнаружен дефект размером, превышающим нормы отбраковки, следует проводить экспертный НК и по его результатам с использованием металлографического анализа, определения коррозионного состояния и оценок с применением методов механики разрушения определять необходимость ремонта, либо возможность и сроки дальнейшей эксплуатации. Это позволит сократить время простоя и отменить напрасные работы по ремонту технических устройств.
Список литературы
- Федеральный закон от 4 марта 2013 г. №22-ФЗ «О внесении изменений в Федеральный закон «О промышленной безопасности опасных производственных объектов». Принят Гос. Думой 15 февраля 2013 г. Одобрен Советом Федерации 20 февраля 2013 г.
- Руководство по безопасности «Методика оценки риска аварий на опасных производственных объектах нефтегазоперерабатывающей, нефтеи газохимической промышленности». Утверждено приказом Ростехнадзора 27 декабря 2013 г. №646.
- Жулина С.А., Лисанов М.В., Савина А.В. Методическое руководство по оценке степени риска аварий на магистральных нефтепроводах и нефтепродуктопроводах//Безопасность труда в промышленности. 2013. №1.
- Шаталов А.А, Власов И.Э., Иванов В.И. Современные проблемы неразрушающего контроля оборудования производственных объектов//Химическая техника. 2003. №8.
- None-Destructive Examination in Relation to Structural Integrity/ Edited by R.W.Nichols. ASP Publishers LTD. London:1980.
- Щербинский В.Г. Технология ультразвукового контроля сварных соединений. СПб.: СВЕН, 2014.
- Ультразвуковая дефектометрия, 25 лет: юбилейный сборник трудов ООО «НПЦ «ЭХО+»/под ред. А.Х. Вопилкина. М.: СПб: СВЕН, 2015.
- Бадалян В.Г., Вопилкин А.Х. Мониторинг сварных соединений трубопроводов с использованием систем АУЗК с когерентной обработкой данных//Автоматизированный ультразвуковой контроль объектов повышенной опасности. Юб. сб. трудов ООО НПЦ «ЭХО+». М.: СПб.: СВЕН, 2010.
- Махутов Н.А., Фролов К.В., Драгунов В.Г. и др. Анализ риска и повышение безопасности водо-водяных энергетических реакторов/Под ред. Н.А. Махутова и М.М. Гаденина. М.: Наука, 2009.
- Иванов В.И., Куранов В.Н., Рябов А.Н. Об акустической эмиссии при малоцикловой усталости//Доклады АН СССР, 1986. Т. 288. №6.
- Донин А.Р. Расчет оперативных характеристик при радиографическом контроле//Дефектоскопия. 1982. №4.
- Forli O. Development and optimisation of NDT for practical use -Nordtest NDT programme – project presentation//V NordiskaNDT Symposiet Esbo, Finland, IIW Report Number IIW-V-967-91, 1990.
- Коновалов Н.Н. Нормирование дефектов и достоверность неразрушающего контроля сварных соединений. М.: ГУПНТЦ ПБ, 2004.
- Волченко В.Н. Вероятность и достоверность оценки качества металлоконструкций. М.: Металлургия, 1979.
- Иванов В.И., Власов И.Э. Некоторые проблемы неразрушающего контроля//Дефектоскопия. 2002. №7.
- Reliability assessment for containers of hazardous materialRACH. Technical Software Consultants Limited for the HSE. Offshore Technology Report 2000/095, 2001.