Автор: В.А. Меньщиков, Г.Г. Лякишев, И.П. Семенов, Л.Х. Гольдштейн (ООО «ВНИИОС-наука).
Опубликовано в журнале Химическая техника №11/2016
Производство этилена является наиболее многотоннажным в нефтехимии. Оно составляет ~ 130 млн т/год и постоянно растет на 2–6 % в год. Практически весь этилен производится пиролизом различного углеводородного сырья. Окислительная димеризация метана (ОДМ) является процессом, альтернативным традиционному.
Огромный интерес к этому процессу связывался в первую очередь с низкой стоимостью метана по сравнению с другими углеводородами. К настоящему времени опубликовано ~ 4000 научных статей и более 1500 патентов.
Максимум публикаций приходится на 1988–1993 гг. Однако до сих пор не создано действующего даже опытного производства.
В ходе исследований, описанных в литературе, использовались самые различные катализаторы. Наилучшие результаты показали Li2O, PbO, La2O3 и другие редкоземельные металлы на различных, как правило основных, окислах (чаще всего MgО, Na–Mn–W/SiO2).
При повышении конверсии метана (ХСН4) селективность по углеводородам С2 (SC2) падает и выход С2 за проход (ВС2) практически никогда не превышает 25 %.
Высокие выходы С2 всегда достигаются в реакторах малого размера (диаметр 3…4 мм) с количеством катализатора 0,05…0,1 г, состоящего из очень мелких частиц (0,2…0,5 мм), при объемном расходе потока 30 000…80 000 1/ч.
Такой размер частиц соответствует наружной удельной поверхности катализатора 1200…2000 м2/м3. Время пребывания потока в слое катализатора составляет 0,015…0,04 с (без учета давления и температуры).
Достижение близких выходов С2 на совершенно различных катализаторах говорит о том, что механизм ОДМ на них одинаков или достаточно близок.
Исходя из кинетической модели процесса, существует предельный выход углеводородов С2, составляющий ~ 25 %, что подтверждается экспериментальными данными.
Технологические аспекты процесса
Наилучшие лабораторные результаты получены на частицах катализатора 0,2…0,3 мм и при высоких объемных скоростях потока. В условиях промышленного производства это приведет к высокому сопротивлению реакторного узла и повышению давления в нем. В то же время установлено, что с повышением давления селективность процесса падает. Таким образом, давление в реакторе должно быть минимальным.
Кроме того, было показано, что при превышении некоторого значения объемной скорости, зависящего от температуры процесса, начинает падать степень конверсии кислорода.
Исследования катализаторов, имеющих различных размер частиц, показали, что при диаметре частиц dч < < 1,5 мм выход С2 остается постоянно высоким, а с увеличением dч уменьшается.
Как уже было сказано, максимальный теоретический выход С2 в процессе составляет ~ 25 %. В реакторах диаметром 15…20 мм достигнут выход С2 ≈ 20% (SС2 ∼ 61% и ХСН4 ~ 32 -34 %) при соотношении СН4/О2 – 3…4 и использовании воздуха. Эти результаты вполне приемлемы для разработки технологии на их основе. Но количество выделяющейся теплоты таково, что адиабатический разогрев потока составляет ~1800 °С. Отсюда следует, что оформление реакторного узла может быть двух типов:
- изотермический реактор с теплоотводом;
- адиабатический реактор.
Для реактора с теплоотводом необходимо решить как минимум три проблемы: выбор теплоносителя, размещение теплообменных поверхностей в слое катализатора и материал теплообменных поверхностей, работающих при температуре 900 °С.
Более реальным является адиабатический реактор.
Даже, если после запуска реактора в него можно будет подавать холодный метано-кислороднй поток, его температура не должна превышать 900 °С. Это достигается при реакционный узел должен представлять собой каскад из двух– трех групп аппаратов с охлаждением потока между ними и подачей кислорода в каждый из них. В этом случае охлаждение реакционного потока может быть совмещено с генерацией пара высокого давления, как это делается на этиленовых установках при охлаждении пирогаза в закалочно-испарительных аппаратах (ЗИА).
Для решения части обозначенных вопросов было разработано несколько укрупненных лабораторных и пилотных установок с реакторами диаметром 30; 48; 70; 124 и 260 мм и объемом катализатора 50…3000 мл. Высота слоя катализатора составляла 25…85 мм. При этом достигается практически полная конверсия кислорода.
В результате исследования позонной подачи окислителя в каскаде из двух реакторов установлено, что при позонной подаче кислорода можно получить выход С2, достигнутый при подаче всего кислорода на вход в реактор при одинаковых соотношениях СН4/О2. С увеличением скорости потока при раздельной подаче кислорода можно ожидать лучшие результаты.
На основании проведенных исследований была разработана и рассчитана технологическая схема процесса производительностью 200 тыс. т этилена в год. Режим работы реакционного узла (каскад из двух реакторов) и состав продуктов реакции (результаты получены на лабораторной установке) приведены ниже:
Соотношение СН4/О2, мол | 4,6 |
Конверсия метана, % | 24,75* |
Селективность по С2 | 59,0* |
Выход С2 (за проход), % | 14,6 |
Максимальная температура, °С | 850…880 |
Состав продуктов (% об.): | 0,8 Н2; 1.0 N2; 81,2 CH4;0,1 O2; 3,5 CO; 4,3 CO2;5,45 C2H4; 1,9 C2H6;0,08 C2H2; 0,2 C3H6;0,15 C4H6; 0,15 C6H6. |
Примечание. * с учетом углеводородов С3+. |
Соотношение СН4/О2, мол 4,6
Конверсия метана, % 24,75*
Селективность по С2 59,0*
Выход С2 (за проход), % 14,6
Максимальная температура, °С 850…880
Состав продуктов (% об.): 0,8 Н2; 1.0 N2; 81,2 CH4; 0,1 O2; 3,5 CO; 4,3 CO2; 5,45 C2H4; 1,9 C2H6; 0,08 C2H2; 0,2 C3H6; 0,15 C4H6; 0,15 C6H6.
Примечание. * с учетом углеводородов С3+.
Предполагается возврат непрореагировавшего метана в реактор и превращение образовавшегося этана в этилен традиционным пиролизом в печи. Блок-схема процесса показана на рис. 1.
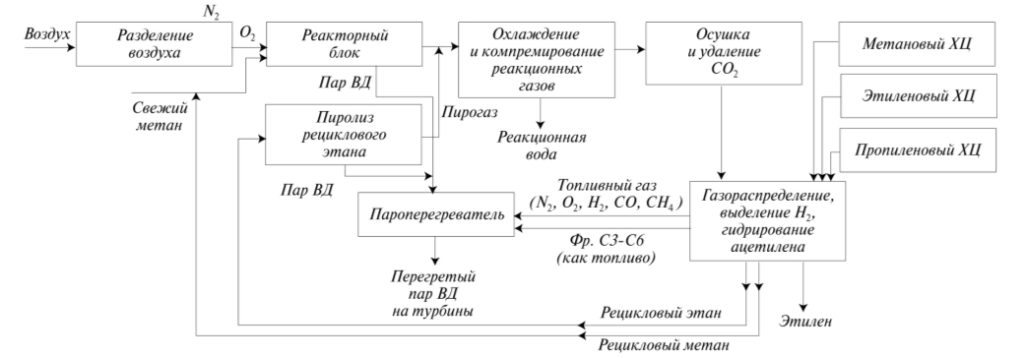
Основные принципы разработанной технологии:
- возврат непрореагировавшего метана в реактор ОДМ;
- двухступенчатый реактор с позонной подачей кислорода и охлаждение реакционного газа за счет генерации пара высокого давления;
- превращение образовавшегося этана в этилен пиролизом в трубчатых печах;
- выделение СО2 с адсорбцией с помощью короткоцикловой адсорбции (КЦА)или абсорбцией этаноламином;
- выделение водорода, необходимого для очистки от ацетилена, с помощью КЦА;
- использование СО, Н2 и некоторого количества метана в пиролизных и нагревательных печах;
- привод компрессоров и высокопроизводительных насосов от паровых турбин, работающих на своем перегретом паре высокого давления;
- фракция С3–С6 используется в качестве топлива;
- минимальное потребление электроэнергии «со стороны».
На основании рассчитанной технологической схемы была выполнена оценка капиталовложений в установку мощностью 200 тыс. т/год этилена. Они составляют ~ 600 млн. дол.
Расходные нормы на 1 т этилена:
- метан – 3,04 т/т (собственно на этилен – 2.15 т/т; остальное – на выработку дополнительного пара для турбин);
- кислород – 3,56 т/т;
- электроэнергия – 185 квт-ч/т.
Принятые цены на основные продукты в США и России приведены ниже:
Страна | США | Россия |
Этилен, дол./т | 1400 | 1050 |
Метан, дол./т | 220 | 110 |
Кислород, дол./т | 44 | 44 |
Электроэнергия, дол./кВт-ч | 80 | 60 |
Для учета амортизации в себестоимости этилена окупаемость принята в 20 лет, а прибыль оценена в 20 %.
На рис. 2 показано влияние цены метана на стоимость этилена при величине капиталовложений 600 млн. дол. Предельная цена для России составляет 200 дол/т (145 дол/тыс. нм3), для США ~ 320 дол./т (~ 220 дол./тыс. нм3). Для Европы, где цена природного газа оценивается в 350 дол./т (~ 250 дол./тыс. нм3), процесс ОДМ оказывается при принятых условиях нерентабельным.
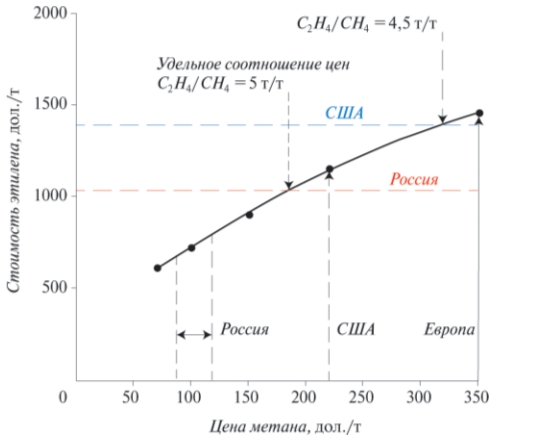
И для России, и для США, чтобы процесс получения этилена методом ОДМ был рентабельным, соотношение стоимостей за 1 т этилена и метана должно быть 5 или больше.
Таким образом, на основании описанного можно сделать вывод, что процесс получения этилена методом ОДМ может в принципе быть рентабельным и конкурентоспособным. Но для этого необходимо:
- проверить на пилотной установке реакционного узла в виде каскада из двух реакторов с подачей кислорода в каждый из них;
- выход С2 за проход должен быть не ниже 14 %;
- проверить работу катализатора в длительном режиме.