Автор: З.А. Мамедов (SOCAR, ПО «Азерхимия»), И.П. Семенов , А.И. Абсаттаров (ООО «ВНИИОС-наука», МИТХТ)
Опубликовано в журнале Химическая техника №11/2017
В процессе каталитического крекинга на НПЗ помимо основных продуктов вырабатывается от 3 до 5% мас. сухого газа. В указанном газе содержится до 10,17% мас. этилена; 13,86% мас. этана; 29,21% мас. пропилена; и до 9,09% мас. пропана. Эти компоненты могут быть выделены и эффективно использованы в рамках производства этилена и пропилена. Чаще всего для переработки доступно два потока от установок каталитического крекинга: фракция С1–С2, часто называемая «сухой газ», и фракция С3 или пропан-пропиленовая фракция (ППФ). Оба этих потока могут быть эффективно использованы в качестве сырья для получения этилена и пропилена.
Могут быть рассмотрены два варианта использования газов каталитического крекинга в качестве сырья. Первый путь – создание отдельной установки выделения этилена или пропилена, второй путь – переработка данных фракций на существующих установках пиролиза углеводородного сырья.
Разделение фракции С3 с выделением товарного пропилена является тривиальной задачей, разделение происходит в ректификационной колонне, часто разрезной. Для подвода тепла в колонну обычно используется принцип теплового насоса, но может быть организована и стандартная схема с обогревом паром и конденсацией оборотной водой. Безусловно, для переработки ППФ с установок каталитического крекинга необходима ее очистка, а чаще всего еще и тонкая очистка товарного пропилена.
Выделение этилена из «сухого газа» является более сложной задачей, так как в смеси содержаться углеводороды С1 и С2 и заметное количество СО2. ООО «ВНИИОС-наука» на протяжении многих лет занимается разработкой и совершенствованием технологии выделения этилена из «сухого газа», имеет среди своих разработок и абсорбционную, и криогенную технологии. Применение той или иной технологии определяется конкретными условиями планируемого производства. Кроме того, в ООО «ВНИИОС-наука» разработана схема выделения этилена из «сухого газа» с получением потока чистого этана и его пиролизом для увеличения выработки товарного этилена из доступного количества «сухого газа».
Создание новых установок по получению этилена и пропилена из газов установок каталитического крекинга требует больших капитальных вложений, с этой точки зрения выгодным решением может быть использование таких газов в качестве сырья для существующих установок получения этилена и пропилена методом пиролиза.
Успешный опыт вовлечения потоков отходящих газов установок каталитического крекинга в действующую установку получения этилена и пропилена (установка проекта ЭП-300) имеется у ПО «Азерхимия», SOCAR (г. Сумгаит, Азербайджан). На этом предприятии в качестве сырья вовлекают и «сухой газ» (фракцию С1 –С2) и ППФ. Главная задача, которую нужно решать, вовлекая в действующую схему установки ЭП-300 потоки газов каталитического крекинга, – это задача глубокой очистки данных потоков. Так как газы каталитического крекинга содержат значительно больше примесей (главным образом, сернистые соединения и углекислый газ), чем поток пирогаза, получаемый на установках пиролиза, использовать предусмотренные схемой ЭП-300 узлы очистки неэффективно, необходимо создание отдельных узлов очистки, при этом становится возможным вовлечение потоков «сухого газа» и ППФ непосредственно на стадии разделения продуктов, предусмотренные схемой.
Рассмотрим подробнее подходы к очистке и вовлечению газов от установок каталитического крекинга, применяемые в ПО «Азерхимия».
Вовлечение «сухого газа»
Значительное количество полученных фракций С1 –С2 содержат кислые компоненты, сероводород и диоксид углерода, а также сернистые соединения. Сероводород, как и диоксид углерода, в присутствии воды образует кислоты, которые вызывают химическую и электрохимическую коррозию металлов. Кроме сероводорода в углеводородных газах присутствуют другие соединения серы: меркаптаны (метилмеркаптан, этилмеркаптан и другие общая формула R–SH–), сероокись углерода (СОS), сероуглерод (СS2). Данные соединения являются ядами для катализаторов как в узлах установки ЭП-300, так и на дальнейших стадиях переработки этилена и пропилена, поэтому их концентрация в продуктовых и технологических потоках производства этилена–пропилена строго ограничена. Это вызывает необходимость предусматривать стадию щелочной очистки сухого газа.
Выбор процесса очистки газа от сернистых соединений определяется экономикой и зависит от многих факторов, основными из которых являются состав и параметры фракции С1 –С2, требуемая степень очистки и область использования, наличие и параметры энергоресурсов, отходы производства и другие.
Наиболее широко используемым является метод очистки углеводородных газов с применением аминов. Однако из-за отсутствия установки для очистки углеводородных газов с применением аминов на предприятии в настоящее время производится щелочная очистка газа, принципиальная схема которой показана рис. 1.
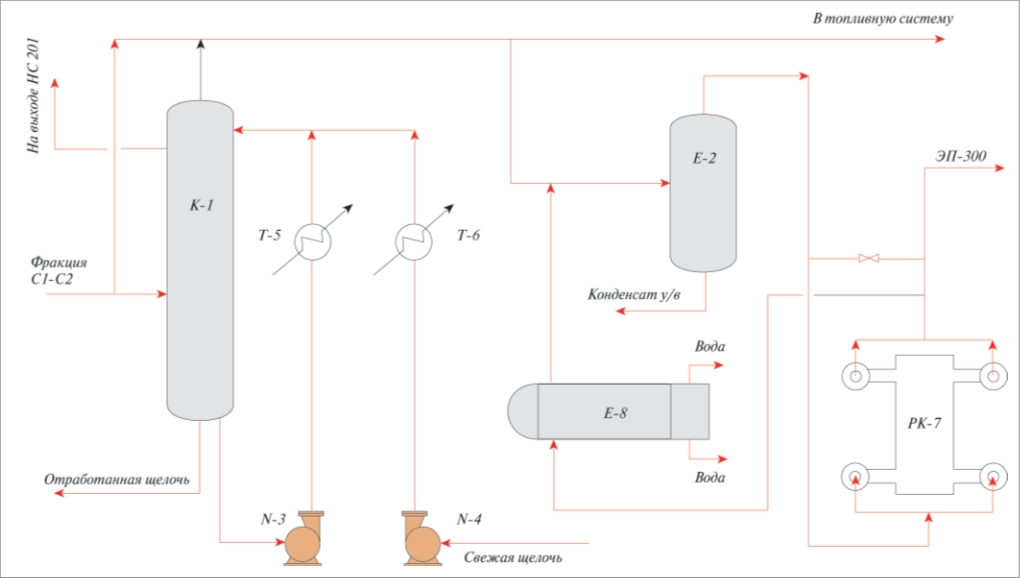
К-1 – нейтрализационная колонна; Е-2 – сепаратор; Т-5,6 – теплообменники; N-3,4 – насосы; РК-7 – компрессор; Е-8 – емкость
Из адсорбционной колонны установки каталитического крекинга поступает фракция С1 –С2 (сухой газ) расходом 10 000…12 000 нм3/ч в колонну щелочной очистки К-1. В верхнюю часть колонны К-1 п насосами Н-3 и Н-4 подается около 7 т/ч 15%-ного раствора NaOH и одновременно подается 6…6,5 т/ч теплого конденсата. В колонне поддерживается температура 50…55°С и давление до 0,95 МПа. Очищенный от сероводорода и СО2 сухой газ проходит через сепаратор E-2 и поступает на компрессор РК-7, затем под давлением 2,2…2,4 МПа подается на установку ЭП-300. Отработанная щелочь поступает на очистку сточных вод.
Результаты хроматографического анализа сухого газа, проведенного на хроматографе «Кристал 5000», представлены на рис. 2.
Состав сухого газа до и после щелочной очистки представлен в табл. 1 (поток анализировался различными методами, в том числе с помощью индикаторных трубок).
Как видно из табл. 1, количество сероводорода снизилось от 20 000 до 1 ррm, а диоксида углерода – от 3,19 до 0,14%. Остальные примеси в том числе, арсин, фосфин, изопропанол, аммоний и NOX практически не изменились.
Фракция С1 –С2 (сухой газ), направляемая на производство ЭП-300, после очистки от сернистых соединений и других примесей подается в сепаратор Е-10, смешивается с пирогазом пиролизных печей, и эта смесь поступает в сепараторы Е-11/1,2 для отделения жидких углеводородов и воды. Из сепаратора Е-11/1,2 смешанный пирогаз направляется на всассывание 1-й ступени турбокомпрессора М-1, а жидкость откачивается насосом Н-15 в емкость Е-5. Анализ состава смешанного пирогаза после сепаратора Е-10 представлен в табл. 2.
Далее пирогаз подвергается ступенчатому сжатию с охлаждением и конденсацией после каждой ступени сжатия, технологической схемой предусмотрены различные рецикловые сдувки на разные ступени компрессии пирогаза. Анализ пирогаза после каждой ступени компрессора М-1 представлен в табл. 3.
Схемой установки ЭП-300 предусмотрена стадия щелочной очистки пирогаза. Пирогаз с верха сепаратора Е-15 направляется в колонну К-9 узла щелочной очистки. После этого пирогаз, очищенный от кислых газов и сернистых соединений, поступает в сепаратор Е-16, откуда направляется на всасывание V ступени компрессора М-1. В сепаратор Е-16 поступают сдувки от теплообменников Т-66а, метановая отдувка колонны К-13 и отдувка из емкости Е-55. Жидкость с низа сепаратора Е-16 отводится в емкость Е-5. С нагнетания V ступени компрессора М-1 пирогаз под давлением до 3,8 МПа и температурой не выше 120°C проходит параллельно работающие водяные холодильники Т-17/1,2, трубное пространство параллельно стоящих теплообменников Т-18, Т-18а. После охлаждения газожидкостная смесь направляется в сепаратор Е-17 для отделения углеводородного конденсата. Углеводородный конденсат из сепаратора Е-17 направляется в емкость Е-55 узла отпарки легких углеводородов, а водный слой по уровню отводится в сепаратор Е-16. Пирогаз из сепаратора Е-17 направляется в осушитель С-1/1,2,3 и сушится до температуры точки росы минус 60…80°C и, проходя холодный блок, направляются в колонну К-10 (деметанизатор). С верха колонны К-10 выделяется метан-водородная фракция, а с низа колонны смешенная фракция пирогаза подается в отделения газоразделения, где разделяется на целевые и побочные продукты пиролиза. Полученные фракции этан и пропан с рециклом направляются в качестве сырья на печи пиролиза, а остальные продукты пиролиза на дальнейшую переработку.
Таким образом, реализованная схема переработки сухого газа и пирогаза включает две стадии щелочной очистки. На первой стадии очистке подвергается только сухой газ, в щелочной колонне удаляется сероводород и большая часть диоксида углерода, однако его концентрация выше допустимой для пирогаза этиленового производства. Вторая стадия щелочной очистки происходит в предусмотренной схемой установки ЭП-300 щелочной колонне, в которой смешанный пирогаз и сухой газ подвергаются доочистке от сероводорода и СО2. Содержание СО2 в пирогазе доводится до нормативных значений. В результате интеграции двух схем удается избежать
необходимости поддерживать высокую степень очистки от СО2 на узле щелочной очистки сухого газа.
необходимости поддерживать высокую степень очистки от СО2 на узле щелочной очистки сухого газа.
Режим работы щелочных колонн
Колонна Щелочная К-1 Щелочная К-9
Температура, °С 50–55 50–55
Расход свежей щелочи, т/ч 7 0,04
Давление, МПа 0,95 1,5
Расход газа, м3 /ч 11 000 30 000
Концентрация
свежей щелочи, % мас. 15 15
свежей щелочи, % мас. 15 15
Вовлечение ППФ
В составе пропан-пропиленовой фракции, полученной на установке каталитического крекинга нефтеперерабатывающего завода им. Г. Алиева, частично присутствуют вода, кислые газы, сероорганические соединения, в том числе метил-, этилмеркаптаны, карбонилсульфид, арсин, фосфин, изопропанол и другие вредные примеси. Для вовлечения ППФ применяется двухстадийная очистка.
На первой стадии происходит очистка ППФ от кислых газов на основе аминовых соединений, далее очищается от меркаптанов экстракцией с NaOH и KOH. Основную часть щелочи можно вернуть в систему при участии воздуха в процессе регенерации. На второй стадии выбран процесс адсорбции для очистки малого количества вредных остаточных примесей в составе ППФ.
Химический состав ППФ был проанализирован с помощью хроматографического прибора «Кристалл 5000», а меркаптаны и карбонилсульфиды потенциометрическим прибором КЕМ модели АТ-510, работающем с автоматическим титратором. Определение арсина и фосфина проведено в индикаторных трубках.
На рис. 3 представлена принципиальная технологическая схема процесса нейтрализации ППФ, полученной на установке каталитического крекинга 15%-ным раствором каустической соды.
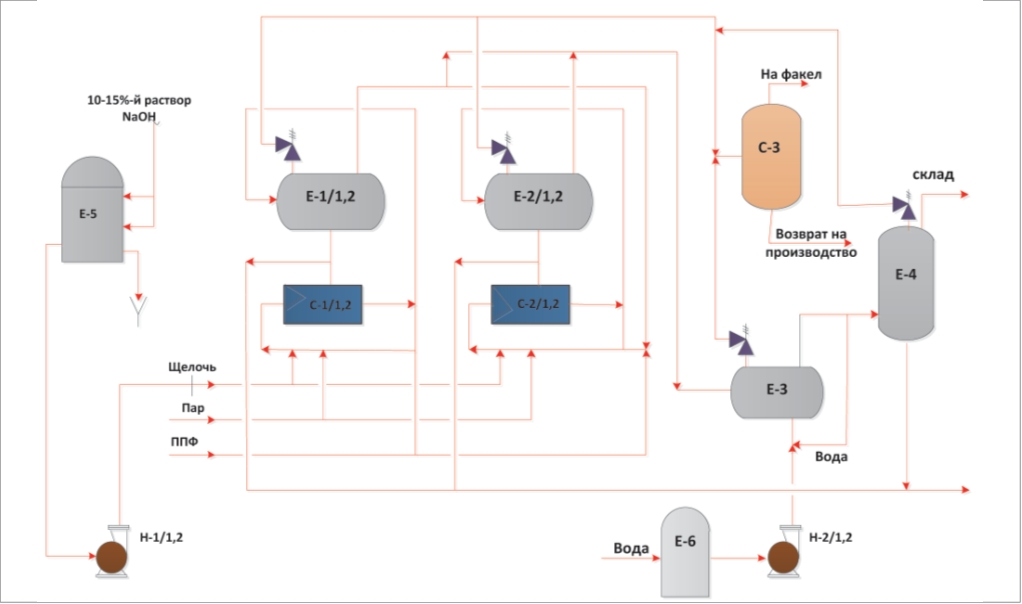
E-1/1,2, E-2/1,2 – емкости смешения ППФ с 15%-ным раствором каустической соды; С-1/1,2, С-2/1,2 – ижекторы;
C-3 – сепаратор; E-3 – емкость отмывки ППФ водой; E-4 – емкость для осушки ППФ хлористым натрием;
E-5 – емкость для 10–15%-ного раствора NaOH; E-6 – емкость для воды; N-1/1-2, N-2/1-2 – насосы
ППФ с установки каталитического крекинга, водяной пар и 10–15%-ный раствор каустической соды подаются через инжекторы S-11,2 и S-21,2 в емкости E-11,2 и E-21,2 при помощи насосов N-11-2. За счет подачи в систему водяного пара поддерживается температура 40…60°C и давление 1,8 MПa. В емкостях E-11,2 и E-21,2 процесс проводится до уменьшения концентрации щелочи до 2–3% и потом отработанная щелочь выводится из сис-темы и заменяется новой щелочью концентрацией 10–15%. Для того, чтобы промыть остатки щелочи и соли, выходящие после нейтрализации, их подают из емкостей E-11,2 и E-21,2 в емкость Е-3. Для повышения эффективности процесса промывки из емкости Е-6 в емкость Е-3 с помощью насоса Н-21-2 периодически подается вода, которая циркулирует для поддержания определенного уровня. Из верхней части емкости E-3 легкая часть ППФ в малом количестве направляется в сепаратор С-3 и оттуда подается в факельную систему. Скопившаяся в емкости жидкая часть ППФ возвращается в систему ППФ на производстве. Для осушки ППФ из емкости E-3 направляют в емкость Е-4, наполненную NaCl, откуда из ее верхней части осушенную ППФ подают на следующую стадию – адсорбцию с целью очистки от микропримесей.
Как видно из табл. 4, во время процесса щелочной очистки (первая стадии очистки) в составе ППФ количество сернистых соединений снизилось: H2S от 0,65% до 15 ppm, меркаптанов от 41,7 ppm до 15 ppm, COS от 30 ppm до 18 ppm; содержание арсина и фосфина составляло 3,0 ppm.
Для удаления микропримесей (метил- и этилмеркаптаны, карбонилсульфид, арсин, фосфин, изопропанол) ППФ подается на установку тонкой очистки (вторая стадия очистки). Свойства адсорбентов, используемых для тонкой очистки ППФ, приведены в табл. 5.
Как видно из табл. 5, сорбенты марки AxSorb 984, AxSorb 900 и AxTrap-194 фирмы Axens состоят в основном из промоторов + Al2O3. Только в состав сорбента AxSorb 900 было добавлено 0,02% Fe2O3 и 0,002% TiO2.
На рис. 4 приведена схема узла тонкой очистки ППФ. Как видно, часть воды из состава ППФ отделяется в холодильник Т-1. Водная фаза, отделенная из состава ППФ, собирается в осадителе Е-2 и направляется в подземную дренажную емкость. Параметры режима емкости E-2 поддерживаются в следующих пределах: давление 1,8 MПa; температура 15°C, уровень 80%. Осушка ППФ и процесс очистки одной части от вредных примесей проводится в адсорберах C-4/1 и C-4/2. Когда один адсорбер находится в рабочем состоянии, другой находится на регенерации или в резерве. В адсорберах C-4/1-2 используются адсорбенты, состоящие из двух систем AxSorb 984 и AxSorb 900 фирмы Axens, обладающие высокой адсорбционной способностью и имеющие длительный срок эксплуатации.
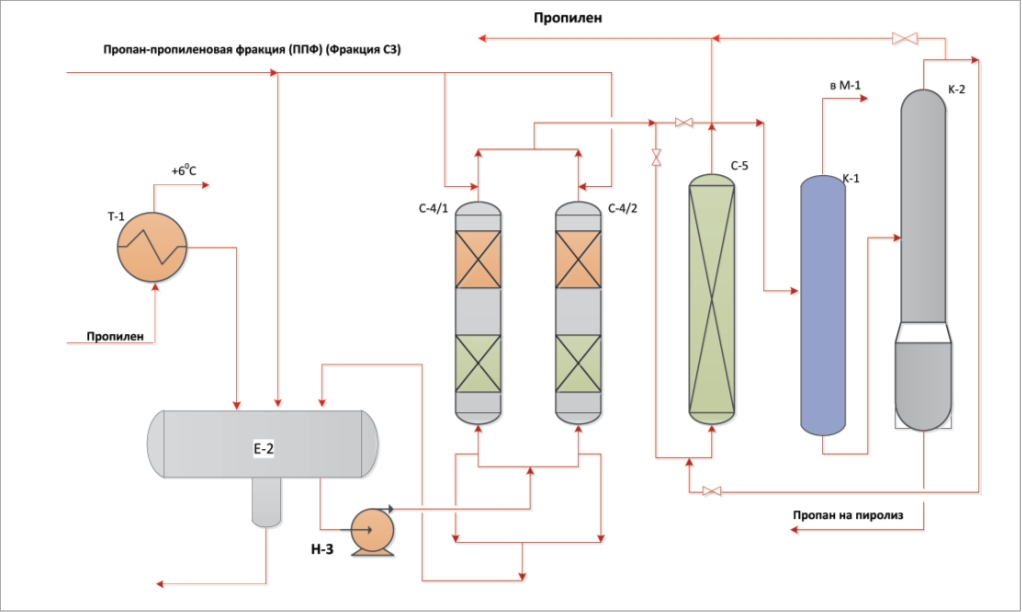
Рис. 4. Принципиальная схема очистки ППФ методом адсорбции от микропримесей:
T-1 – теплообменник; E-2 – емкость; Н-3 – насос; C-4/1-2 – адсорбер для осушки от влаги и сернистых соединений;
C-5 – адсорбер очистки от арсена и фосфина; K-1 – колонна деэтанизации; K-2 – колонна отделения пропилена от пропана
Из сырьевой емкости Е-2 ППФ насосом Н-3 направляется в адсорбер C-4/1-2. После очистки от воды, RSH (меркаптаны) и COS она подается в адсорбер C-5, где очищается от соединений AsH3 и PH3.
В соответствии со схемой, показанной на рис. 4, ППФ после очищения под давлением 1,9 MПa, при температуре 20°C в количестве 36 м3 /ч направляется в теплообменник Т-1. В межтрубном пространстве теплообменника в качестве охлаждающего агента используется пропилен (6°C) из сепаратора пропиленового холодильного цикла установки ЭП-300. Вода с углеводородной жидкой фазой собирается в осадителе емкости Е-2 и непрерывно выводится из системы. Из емкости E-2 фракция, проходя через механические фильтры, с помощью насоса Н-3 подается в нижнюю часть адсорбера C-4/1-2, откуда направляется в верхнюю часть и, проходя через адсорбенты AxSorb 902 и AxSorb 984, в первом слое осушается, а во втором – очищается от сернистых соединений. Расход фракции на нагнетании насоса Н-3 регулируется автоматически.
Технологические параметры работы адсорберов
Абсорбер | С-4/1–2 | С-5 |
Рабочая фаза | Жидкая | Жидкая |
Удельная молекулярная масса, кг/кмоль |
42,85 | 42,85 |
Удельная масса, кг/м3 | 522,3 | 522 |
Вязкость, cП | 0,1 | 0,1 |
Температура, °C | 15…20 | 15…35 |
Давление, Mпa | 2,1…2,5 | 2,14 |
Расход, кг/ч | 15 000 | 15 000 |
Перепад давления, МПа | < 0,1 | < 0,1 |
Как видно, оба адсорбера работают с жидкой фазой и перепад давления удерживается менее 0,1 МПа.
На выходе из адсорбера C-4/1-2 температура точки росы не должна быть выше минус 60°C, и для тонкой очистки далее фракция подается в нижнюю часть адсорбера C-5, наполненную адсорбентом AxTrap194.
На выходе из адсорбера C-4/1-2 температура точки росы не должна быть выше минус 60°C, и для тонкой очистки далее фракция подается в нижнюю часть адсорбера C-5, наполненную адсорбентом AxTrap194.
Очищенная от вредных соединений ППФ с верха адсорбера C-5 под давлением 2,1 MПa и температурой 35°C подается в линию питания колонны деэтанизации К-16 (колонна в действующей схеме ЭП-300), которая служит для очистки от легких компонентов (водород, метан, этилен и этан) с поддержанием давления на уровне 2,1,0 МПа. Температура в верхней части колонны составляет 50°C, в нижней – 55°C. С низа колонны К-16 жидкая фаза ППФ, проходя через теплообменник, как питание подается в колонну К-17. Легкая фракция С2, отделенная с верхней части колонны, направляется на всасывание турбокомпрессора М-1. Колонна К-17 служит для отделения товарного пропилена от ППФ. Пары пропилена с верха колонны конденсируются в теплообменнике, собираются в емкости и оттуда подаются на процесс обработки, а пропановая фракция из куба K-2 подается на установку ЭП-300 печей пиролиза в качестве сырья.
На основании изложенного можно сделать следующий вывод. В ПО «Азерхимия» впервые на установке проекта ЭП-300 использован «сухой газ» как сырье для получения этилена и пропилена, что позволило получить дополнительно до 2 т/ч этилена и 5 т/ч пропилена, не увеличивая нагрузку на печи пиролиза. Разделенная водородная фракция используется для селективного гидрирования ацетиленистых соединений в составе этан-этиленовой и пропан-пропиленовой фракций. Метановая фракция используется в качестве топлива в пиролизных печах. Таким образом, полностью утилизируется потенциал сухого газа как сырья установки получения этилена–пропилена.
Организована схема очистки и переработки ППФ от каталитического крекинга, за счет чего может быть увеличена выработка мономеров или сэкономлено сырье пиролиза (бензин, ШФЛУ).
Главные проблемы и задачи, с которыми столкнулось предприятие при вовлечении потоков газов с установок каталитического крекинга, – это очистка потоков, прежде всего от сернистых соединений. Для потока ППФ хорошим решением явилась комбинация щелочной очистки и адсорбционной очистки. Такая схема позволяет удалить из потока не только сероводород и СО2, но и более опасные и трудноудаляемые примеси (СОS, арсины, фосфины).
На потоке фракции С1–С2 в данный момент предприятие осуществляет внедрение стадии аминовой очистки взамен щелочной (прежде всего из-за большого количества стоков и расхода щелочи), планируется также внедрение стадии адсорбционной очистки или узла гидрирования на катализаторе для удаления микропримесей, что позволит обеспечить надежную и экономически эффективную эксплуатацию производства.