Авторы: А.В. Костюков, С.Н. Бойченко, А.В. Щелканов, Е.А. Бурда (ООО «НПЦ «ДИНАМИКА»), С.А. Аверьянов, В.И. Майоров (ООО «РМЗ «Газпромнефть – ОНПЗ»).
Опубликовано в журнале Химическая техника №7/2016
При работе технологических установок по переработке нефти первоочередной задачей является обеспечение безопасной и ресурсосберегающей эксплуатации оборудования, особенно в тех случаях, когда возникновение аварийной ситуации может причинить большой ущерб.
Для предотвращения таких ситуаций на нефтеперерабатывающих и нефтехимических производствах все большее распространение получают различные системы мониторинга технического состояния. Такие системы предотвращают внезапные отказы и позволяют перейти на обслуживание оборудования по фактическому техническому состоянию вместо прежней концепции планово-предупредительных ремонтов, что повышает безопасность и увеличивает экономическую эффективность эксплуатации [1].
Одним из наиболее распространенных типов промышленного электрооборудования являются асинхронные электродвигатели (АЭД), что обусловливает необходимость разработки современных методов диагностирования технического состояния их основных узлов. При этом для максимального повышения достоверности диагностики необходимо исключить человеческий фактор путем полной автоматизации процесса диагностирования.
Известно, что 85–95% отказов электромагнитной системы АЭД происходит из-за повреждений изоляции обмоток. Применяющиеся в настоящее время методы контроля состояния изоляции не лишены недостатков.
Так, испытания повышенным напряжением возможны только на выведенном из эксплуатации оборудовании.
Данный вид испытаний может ухудшить состояние изоляции и требует повышенных мер безопасности. Измерения коэффициентов абсорбции и поляризации также требуют отключения электрической машины, но при этом показывают только общее состояние изоляции – степень ее увлажнения и старения, и не позволяют определить тип возможных дефектов изоляции.
Существующие стенды для испытания электродвигателей обычно контролируют параметры вибрации, температуры, частоты вращения и тока потребления АЭД [2].
Это позволяет с высокой достоверностью оценить состояние механических узлов АЭД, но состояние изоляции АЭД при этом определяется лишь косвенно.
Перспективным методом диагностирования дефектов изоляции обмоток статоров АЭД является метод контроля параметров частичных разрядов.
Частичный разряд – это электрический разряд, который шунтирует лишь часть изоляции между электродами, находящимися под разными потенциалами [3]. Частичные разряды (ЧР) возникают в дефектах изоляции, включениях, неоднородностях, пустотах между слоями изоляции. Такие места, имеющие диэлектрические свойства, отличные от свойств основной изоляции, вызывают перераспределение электрического поля, что приводит к возникновению участков изоляции с повышенной напряженностью электрического поля. Многократное повторение ЧР во время эксплуатации электрооборудования оказывает негативное влияние на состояние изоляции и (при достаточной интенсивности ЧР) приводит к увеличению размера дефекта вплоть до электрического пробоя, что может послужить причиной выхода электрооборудования из строя и возникновения аварийной ситуации.
В настоящее время методы контроля частичных разрядов параметров ЧР при экспресс-диагностике АЭД, например в условиях ремонтного производства, не имеют широкого распространения. Существующая практика предусматривает обычно длительный контроль параметров АЭД стационарными системами или периодический контроль переносными приборами. По этой причине использование метода ЧР при входном и выходном контроле на ремонтных предприятиях затруднено, так как время испытаний АЭД ограничено.
Метод контроля параметров ЧР имеет много преимуществ: щадящее диагностирование электрооборудования под рабочим напряжением, возможность установки систем мониторинга для контроля динамики изменения состояния изоляции, относительная простота датчиков и безопасность их применения. Использование такого метода позволяет повысить полноту диагностики машинного оборудования.
В целом можно утверждать, что адаптация и внедрение методов контроля параметров ЧР в изоляции АЭД в условиях ремонтного производства повысит надежность применения АЭД в промышленности и безопасность производственных процессов в целом.
Цель настоящей работы – интеграция метода контроля параметров ЧР в состав стендовой системы КОМ- ПАКС®-РПЭ производства НПЦ «Динамика» для повышения достоверности диагностирования АЭД. Указанная стендовая система установлена в цехе №51 ООО «РМЗ «Газпромнефть – ОНПЗ» (РМЗ).
Система диагностики электродвигателей КОМПАКС®- РПЭ (рис. 1) предназначена для диагностики технического состояния электродвигателей с рабочим напряжением 380 и 6 000 В по параметрам вибрации, температуры, частоты вращения и току потребления по трем фазам.
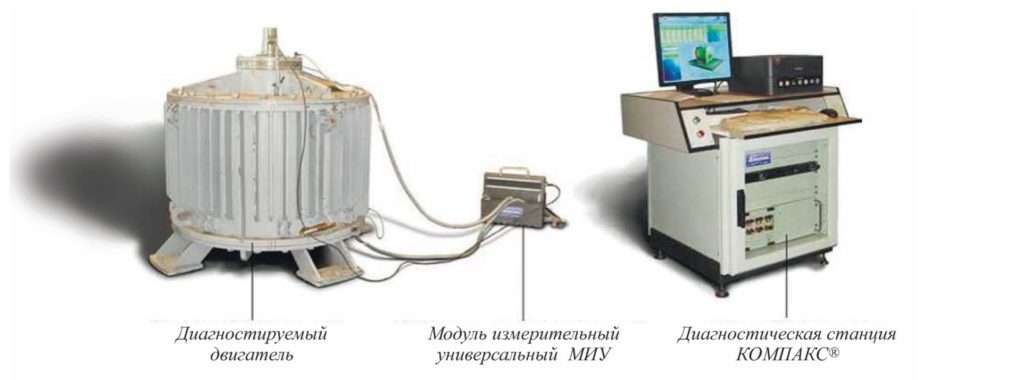
Система позволяет диагностировать одновременно до восьми электродвигателей как переменного, так и постоянного тока. После диагностики автоматически формируется акт технической готовности электродвигателя, на котором отображается номер акта с датой проведения диагностики, тип продиагностированного электродвигателя с паспортными данными, омическое сопротивление и сопротивление изоляции обмоток электродвигателя, биение вала, значения измеренных параметров (температура, ток, вибропараметры), время испытаний, а также автоматические экспертные сообщения, выданные системой.
Использование модернизированной стендовой системы КОМПАКС®-РПЭ с интегрированной подсистемой ЧР позволяет диагностировать дефекты изоляции на ранних стадиях их возникновения и предупреждать возникновение аварийных ситуаций, благодаря чему исключаются простои и затраты, связанные с необходимостью вывода оборудования из эксплуатации для диагностирования обычными методами и ремонта.
Действующий на территории Российской Федерации ГОСТ Р 55191–2012 «Методы испытаний высоким напряжением. Измерения частичных разрядов» [3] распространяется на электрооборудование напряжением переменного тока промышленной частоты до 400 Гц действующим значением свыше 1 000 В и напряжением постоянного тока свыше 1 000 В. Схема измерения параметров ЧР (рис. 2), реализованная в составе модернизированной стендовой системы КОМПАКС®-РПЭ, соответствует схеме Б.1, приведенной в Приложении Б к указанному стандарту.
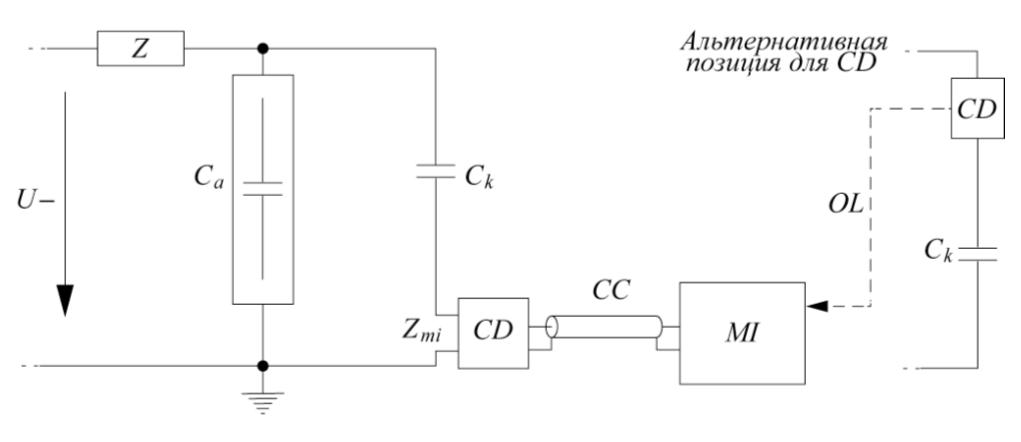
U – рабочее напряжение; Z – опциональный фильтр (не используется); Ca – испытываемый образец;
Ck – соединительный конденсатор; Zmi – входное сопротивление подсистемы ЧР; CD – соединительное устройство; CC – соединительный кабель;
MI – измерительный прибор; OL – оптическая связь (не используется)
Устоялось мнение, что ЧР происходят в изоляции электрооборудования, к которому приложено электрическое напряжение 1 000 В и более [4], а в изоляции статоров АЭД с рабочим напряжением 380 В ЧР отсутствуют по причине недостаточного напряжения для их возникновения. Однако известно, например, что в воздушных включениях между проводами типа ПЭВ-2 и ПЭТВ частичные разряды возникают уже при 400…500 В, а ионизационные процессы в дефектах изоляции возникают при еще более низких напряжениях. Кроме того, виды электроразрядной активности (ЭРА) не ограничиваются классическими ЧР. Так, согласно документу [5], в двигателях низкого напряжения (380 В) возможны искровые явления в обмотках и контактах, а в двигателях всех классов напряжения возможны искрения и дуговые явления в активной стали статора. Также, например в работе [6], описан механизм возникновения коронных разрядов в обмотках статоров АЭД с рабочим напряжением 380 В при использовании частотно-регулируемых приводов (ЧРП), получающих все более широкое распространение. При этом в кабельных линиях и обмотках статоров АЭД могут возникать 10-кратные перенапряжения относительно рабочего напряжения. Эти перенапряжения являются следствием волновых процессов из-за наличия гармоник высокой частоты, передающихся к АЭД от ЧРП по кабелю питания.
Приведенные утверждения послужили основанием для включения в программу исследований асинхронных электродвигателей на 380 В. Проверялось наличие искровых явлений (витковых, в пакете) и возможность контроля этой разрядной активности с помощью приведенной выше схемы измерения параметров ЧР.
Разработанный метод диагностирования состояния изоляции статоров испытываемых АЭД по параметрам ЧР заключается в определении скорости повторения импульсов ЧР (имп/с) и максимальной амплитуды ЧР (мВ) и сравнении их с критическими значениями.
В процессе проведения отработки методики ЧР была собрана и оценена статистическая информация из более чем 4300 актов испытаний АЭД, из них свыше 140 АЭД имели рабочее напряжение 6 000 В.
По результатам обработки полученных данных были нормированы параметры ЧР, т.е. были установлены пороги таких параметров, как скорость повторения импульсов и их амплитуда. В настоящее время выбранные нормы параметров ЧР применяются на РМЗ при диагностировании АЭД, испытываемых на стенде КОМ- ПАКС®-РПЭ с подсистемой ЧР.
При проведении испытаний АЭД параметры электроразрядной активности, превышающие пороговые значения, были зафиксированы для 5% всех испытанных высоковольтных и 2% низковольтных АЭД.
При дальнейшем контроле указанных высоковольтных АЭД с помощью методов вибродиагностики и визуального контроля было подтверждено наличие дефектов электрического характера, таких, как повреждения изоляции, искрение в контактах, загрязнение изоляции.
В качестве примера использования метода ЧР можно привести описание следующего случая. При проведении входного контроля одного из поступивших в ремонт высоковольтных АЭД в изоляции фазы А подсистемой ЧР системы КОМПАКС®-РПЭ автоматически были зафиксированы ЧР со скоростью повторения до 105 имп/с и амплитудой до 20 мВ. После разборки данного АЭД и извлечения из него ротора было обнаружено наличие сильного загрязнения лобовых и пазовых частей обмоток смазочными материалами (рис. 3).
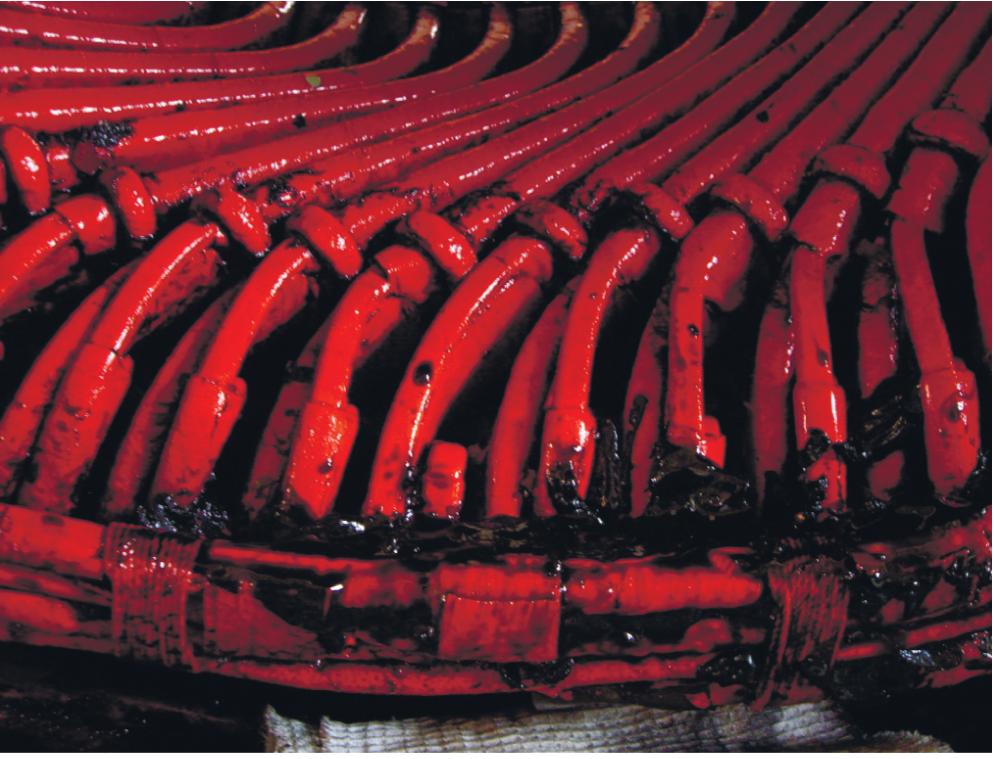
Для устранения обнаруженного загрязнения статор указанного АЭД был снят с испытаний и подвергнут мойке на специализированном участке, после чего ремонт АЭД был продолжен. При выходном контроле было зафиксировано снижение до нуля значений параметров ЧР в фазе А, что связано с устранением загрязнения изоляции после технологической мойки. Приведенный пример служит подтверждением высокой чувствительности метода ЧР, которая позволяет фиксировать даже наличие загрязнений электромагнитной системы АЭД.
Как показывают результаты исследований, интенсивность ЭРА в случае ее возникновения мало зависит от мощности электродвигателей и больше связана с тяжестью условий (температура, влажность, загрязнение) эксплуатации АЭД, непосредственно влияющей на степень старения изоляции. Например, при испытаниях погружных насосов, работающих в условиях повышенной влажности, обычно регистрировался повышенный уровень ЭРА.
Результаты проведенных экспериментов позволяют сделать вывод о целесообразности применения рассматриваемого метода для контроля состояния изоляции статоров АЭД с рабочими напряжениями 380 и 6 000 В в условиях ремонтного производства.
Проведение сплошного контроля изоляции при выходе АЭД из ремонта уменьшает вероятность пропуска АЭД с дефектами изоляции в эксплуатацию. При этом не требуются дополнительные затраты времени или выполнение каких-либо вспомогательных операций персоналом испытательного стенда. Это достигается благодаря тому, что датчики подсистемы ЧР системы КОМПАКС®-РПЭ установлены стационарно, а сама процедура контроля состояния изоляции выполняется системой автоматически и параллельно с измерением прочих параметров АЭД.
В свою очередь, входной контроль изоляции с применением метода ЧР при поступлении АЭД в ремонт позволяет с высокой степенью достоверности определить фактическое состояние изоляции обмоток статора и, соответственно, уточнить необходимый объем ремонтных работ. Это важно, в первую очередь, для высоковольтных АЭД по причине большой стоимости, сложности и трудоемкости ремонта их обмоток. Так, если при входном контроле обнаруживается необходимость проведения дополнительных работ по улучшению состояния изоляции, то появляется возможность выполнить эти работы параллельно с запланированными, не увеличивая общее время ремонта АЭД, либо включить в план дальнейших работ заранее. В целом же затраты времени на входной контроль могут быть скомпенсированы сокращением объема выполняемого ремонта или обслуживания изоляции в зависимости от ее фактического технического состояния.
Таким образом, систему КОМПАКС®-РПЭ с интегрированной подсистемой ЧР можно рекомендовать для широкого применения как высокоэффективное комплексное решение для выявления механических и электрических дефектов асинхронных электродвигателей.
Список литературы
- Костюков В.Н. Мониторинг безопасности производства. М.: Машиностроение, 2002.
- Костюков В.Н., Бойченко С.Н., Костюков А.В. Автоматизированные системы управления безопасной ресурсосберегающей эксплуатацией оборудования нефтеперерабатывающих и нефтехимических производств (АСУ БЭР КОМПАКС®). М.: Машиностроение, 1999.
- ГОСТ Р 55191–2012 Методы испытаний высоким напряжением. Измерения частичных разрядов. М: Стандартинформ, 2014.
- IEEE P1434/D1.1 Руководство по измерению частичных разрядов в электрических машинах переменного тока. США, 2010.
- Методические указания: МУ 1.3.3.99.0036–2009. Диагностика изоляции вращающихся машин классов напряжения от 0,4 кВ до 24 кВ по характеристикам частичных разрядов. ОАО «Концерн Росэнергоатом». 2009.
- Коробцов А.А., Леонов А.П., Похолков Ю.П. и др., Применение эмалированных проводов в обмотках асинхронных двигателей с частотным управлением//Кабели и провода. 2014. №3 (340). С 16–18.