Автор: Алик Гройсман | Технион (Израильский Технологический Институт), Хайфа, Израиль
E-mail: alecgroysman@gmail.com | Website: www.groysmanalec.com
Опубликовано на портале «Химическая техника», июль 2021
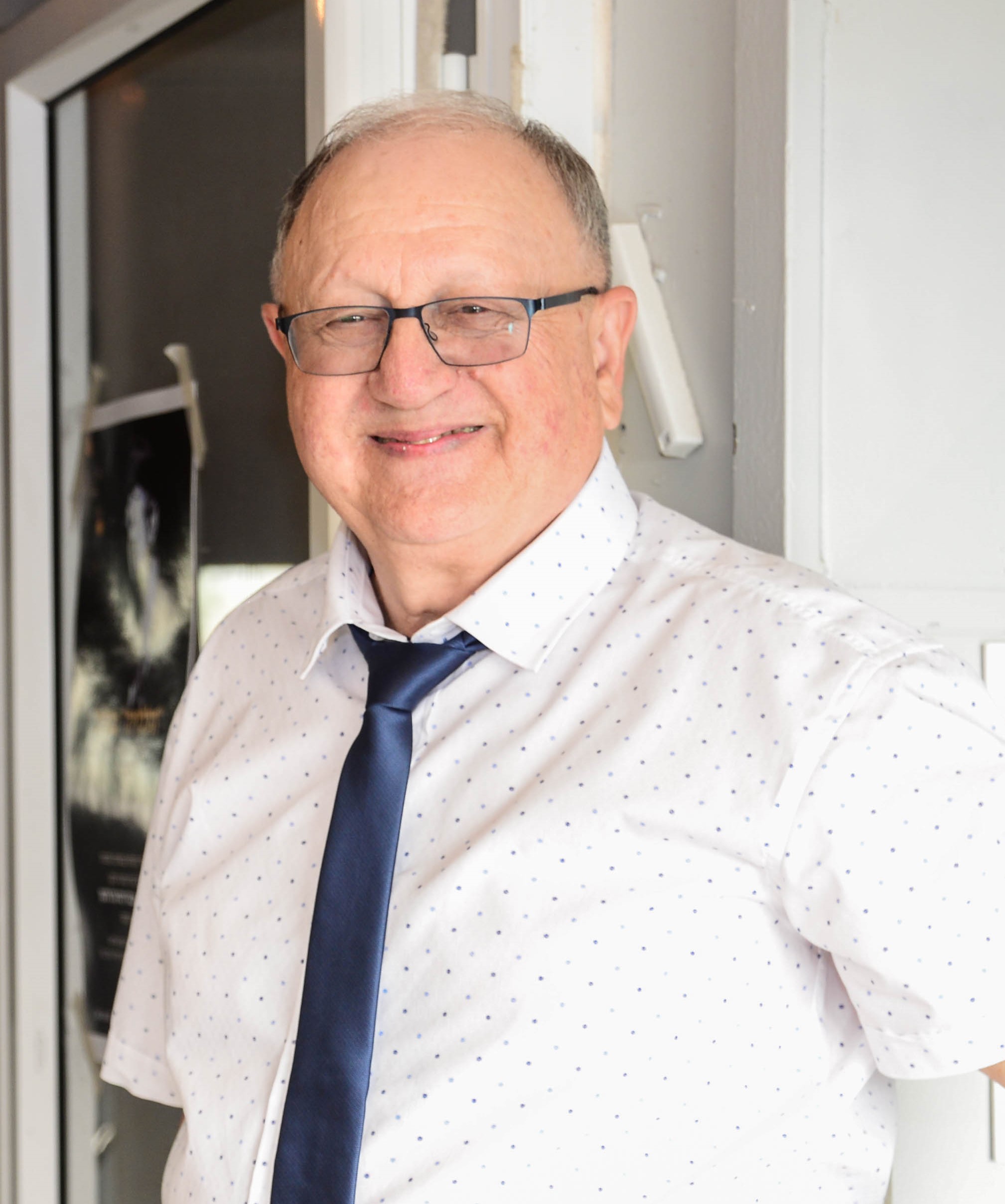
Доктор Алик Гройсман
имеет более чем 40-летний опыт работы в сфере материаловедения, коррозии, контроля коррозии и мониторинга коррозии в нефтеперерабатывающей, нефтегазовой и нефтехимической промышленности, исследований и преподавания в указанных областях.
Точечная (питтинговая) коррозия – это форма локальной коррозии, происходящей на отдельных участках поверхности металла, приводящей к образованию небольших углублений различных размеров, в то время как другие части поверхности могут оставаться полностью нетронутыми (рис. 1).
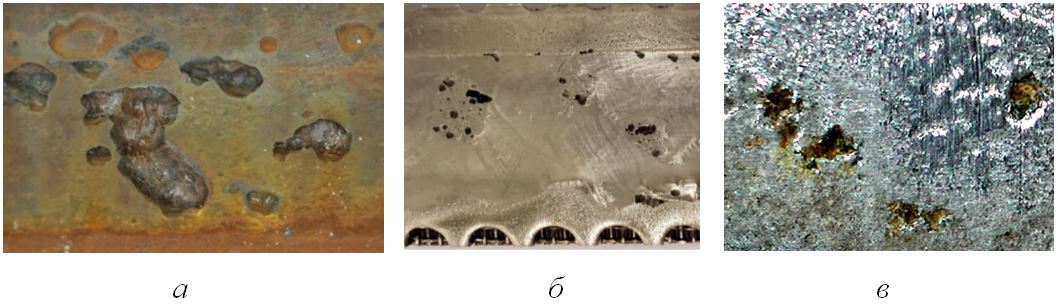
Английские слова pitting или pits означают небольшие вмятины, впадины, полости, каверны или отверстия на поверхности металла. Впервые слово pit было зарегистрировано в английском языке в 1655–1665 гг. и означало «дыра в земле» (рис. 2).
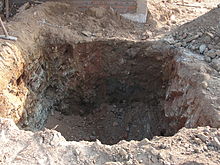
Слово было заимствовано из латинского языка: puteus – колодец или яма. Так что, по-видимому, правильнее было бы назвать «ямочной коррозией». Русский перевод не совсем точно отражает суть явления, так как форма точечной (питтинговой или ямочной) коррозии может принимать форму от узких глубоких отверстий (точечных иглоподобных отверстий-язв) до широких поверхностных и подповерхностных язв-углублений (см. рис. 1). Отсюда часто можно встретить в русской литературе словосочетание «язвенная коррозия», соответствующее английскому «shallow pit». Иногда в русской литературе можно встретить понятия точечной и язвенной коррозии, что объясняется различием размеров (глубине и площади) коррозионных повреждений. Мы же будем употреблять один термин – питтинговая коррозия. Уж и так много иностранных слов в русском научно-техническом языке!
В стандарте ASTM-G46 вы найдёте фотографии для оценки точечной коррозии [1]. Форму питтинговой коррозии определяют только с помощью металлографии, когда образец с ямками имеет поперечное сечение, и можно определить форму и глубину их проникновения в металл (рис. 3). Глубину питтинга вы можете определить с помощью оптического микроскопа.
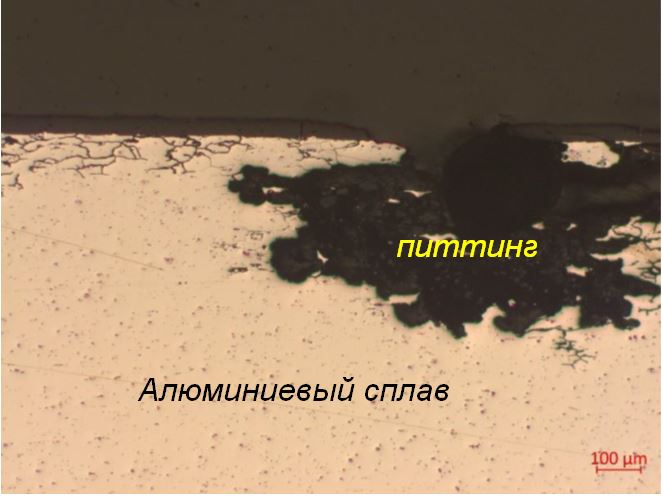
Питтинговая коррозия – одна из таинственных форм локальной коррозии, поэтому она обросла мифами. Меня часто спрашивают, почему питтинг здесь, а не здесь, в 10 см от этого места. Непросто ответить на этот вопрос. С одной стороны, можно сослаться на гетерогенность металла и среды. С другой стороны, существует довольно много причин питтинговой коррозии. Попытаемся разобраться в этом. Но прежде нам необходимо дать определения основным понятиям, используемым в анализе питтинговой коррозии. Вообще любое путешествие в мир коррозии и материалов следует начинать с определений. Главное из них – что такое коррозия?
Итак, коррозия – это физико-химическое взаимодействие между материалом, обычно металлом, и окружающей средой, которое приводит к изменению качества материала и окружающей среды. Мы будем периодически возвращаться к этому важному определению. Во многих учебниках вы найдёте «к ухудшению» вместо «к изменению», предполагая, что коррозия всегда приводит к деградации материала. Оказывается, существует довольно много конструктивных (положительных, полезных) коррозионных процессов, которым вы находите применение, даже не подозревая об этом [2]. В любой батарейке используется коррозия одного из металлов для получения электрического тока. И качество нашей жизни ухудшилось бы без этой конструктивной коррозии. Практически все домашние приборы работают именно благодаря ей. При катодной защите также используется коррозия жертвенного анода, чтобы защитить металлическую конструкцию, эксплуатирующуюся в грунте или в воде. Таким образом, вы можете найти 21 случай «полезной коррозии» [2].
Предлагаю вам следующий путь в мир питтинговой коррозии:
- Причины;
- Механизм;
- Методы определения стойкости металлов и сплавов против питтинговой коррозии;
- Прогнозирование;
- Предупреждение и контроль;
- Примеры питтинговой коррозии.
Не волнуйтесь, постараюсь как можно короче изложить материал, чтобы каждый читатель нашёл для себя самое важное, полезное и интересное.
Читая любой учебник по коррозии, вы увидите, что все виды локальной коррозии (а их 15!) начинаются с питтинговой коррозии. Почему? Потому что она является одним из основных и часто встречающихся механизмов разрушения металлов и сплавов. Питтинги вызывают разрушение из-за перфорации и являются началом таких видов коррозионного разрушения, как коррозионное растрескивание под напряжением, щелевая коррозия, фреттинг-коррозия, усталостная коррозия, микробиологическая коррозия, ударная коррозия, эрозия-коррозия и кавитация.
Практически все виды металлов и сплавов, находящиеся в пассивном состоянии, подвержены питтинговой коррозии при определённых условиях. Кратко объясним, что такое пассивное состояние металлов, и продолжим путешествие по объявленному маршруту.
Пассивность – это потеря электрохимической активности металла, снижающая его скорость коррозии в миллион и более раз (не до нуля!). Пассивность объясняется наличием на поверхности металла тонкой и прочной плёнки – слоя, состоящего из оксидов или смеси оксидов-гидроксидов металла или его солей. Так, присутствие оксида хрома (Cr2O3) на поверхности нержавеющих сталей, оксида алюминия (Al2O3) – на алюминии, оксида титана (TiO2) – на титановых сплавах, оксида никеля (NiO) – на никелевых сплавах объясняет возможность их использования во многих промышленных и природных условиях.
Важно подчеркнуть, что пассивность – это метастабильное состояние (квази- или как бы стабильное), то есть оно неустойчивое, и защитную пассивную плёнку можно разрушить. Это разрушение и приводит к питтинговой коррозии нержавеющих сталей, алюминиевых, титановых и никелевых сплавов. Малоуглеродистые стали тоже подвержены питтинговой коррозии, но механизм может быть другим, и мы тоже это обсудим.
- Причины питтинговой коррозии
Склонность сплавов к питтинговой коррозии определяется внутренними и внешними факторами. Это вытекает из самого определения коррозии (прочтите его ещё раз).
Внутренние факторы:
- природа металла и сплава. Железо, никель, алюминий, титан и их сплавы, особенно нержавеющие стали и никелевые сплавы подвержены питтинговой коррозии;
- состояние поверхности металла, присутствие пассивной плёнки и загрязнений. Шероховатые поверхности менее стойкие, чем отполированные;
- термообработка.
К внешним факторам относятся:
- природа среды. Наличие ионов-активаторов (галогенидов, особенно хлорид- и бромид-ионов) и кислые среды более способствуют развитию питтинговой коррозии;
- различие концентрации кислорода в растворе (дифференциальные аэрационные ячейки);
- отложения (осадки неорганического и органического происхождения);
- условия: повышение температуры, скорость и режим потока жидкости; особенно опасна стагнация. Застойные зоны с большей вероятностью приведут к появлению питтинговой коррозии, особенно, если есть вещества, способные оседать из жидкости на поверхность металла. Но и очень сильная струя может привести к питтингу.
Наиболее существенное влияние на протекание питтинговой коррозии имеют содержание хлоридов (Cl–) и температура. Поэтому именно эти два фактора были выбраны для оценки сравнительной стойкости сплавов против питтинговой коррозии (см. раздел 3). Растворы NaCl, FeCl3, морская вода (где хлоридов около 3,5%), смеси соляной и азотной кислот являются идеальными средами для питтинговой коррозии. Есть и другие ионы, вызывающие питтинговую коррозию, например, Br–, I–, S2O32–, OCl–. Но обычно говорят о хлоридах, потому что они самые распространённые в промышленных и природных растворах.
Важным фактором является наличие определенных фаз в сплавах (в частности, включения сульфида марганца). Они появляются в сталях, так как сера и марганец всегда присутствуют в железных рудах.
Фаза феррита (α-Fe) может быть вредной для аустенитных сталей (особенно в сварочных швах) при определённых условиях окружающей среды. Присутствие феррита при концентрации более 3% является слабым местом в сварочных швах нержавеющих сталей, так как отсутствие хрома превращает эти зоны в обычную углеродистую сталь, не стойкую против питтинговой коррозии. Вот почему иногда мы наблюдаем поражения питтингами именно сварочных швов. Поэтому существует требование к содержанию феррита не более 2% в сварочных швах нержавеющих сталей. И, конечно, есть методы и приборы, позволяющие это сделать.
Чистая и гладкая поверхность сталей повышает стойкость против питтинговой коррозии. Загрязнение поверхности нержавеющей стали углеродистой сталью в результате сварки вблизи изделий из углеродистой стали значительно ускоряет начало питтинговой атаки.
К питтингам может приводить не только сама по себе питтинговая коррозия, но и следующие виды коррозии:
- щелевая – можно рассматривать как частный случай питтинговой коррозии, поэтому часто вы встречаете выражение «стойкость против питтинговой и щелевой коррозии»;
- гальваническая;
- эрозия и кавитация;
- микробиологическая;
- коррозия при температуре точки росы;
- селективная;
- фреттинг-коррозия;
- усталостная.
Теперь вы понимаете, что, увидев питтинги на поверхности металла, не так просто определить, что стало причиной их образования. Почему питтинги опасны? Как правило, невозможно определить скорость развития питтингов, а, значит, прогнозировать стойкость оборудования в конкретных условиях. Те немногочисленные модели, разработанные для объяснения протекания питтинговой коррозии, настолько специфичны, что применимы исключительно для конкретных условий, и навряд ли можно их распространить на все случаи эксплуатации оборудования (см. раздел 3).
Питтинговая коррозия опасна ещё и тем, что именно питтинги провоцируют и приводят к другим, тоже мало предсказуемым и не контролируемым видам коррозии, таким как коррозионное растрескивание под напряжением, усталостная коррозия и фреттинг-коррозия. Проще говоря, всё начинается с питтинга.
И здесь начинается настоящее расследование. Только определив причину и механизм питтинговой коррозии, мы сможем повлиять, уменьшить и даже предотвратить появление питтингов.
- Механизм протекания питтинговой коррозии
Питтинги зарождаются на микроскопическом уровне в пассивной плёнке в местах дефектов (механических и физико-химических). Обнаружение ранних стадий питтинговой коррозии требует методов измерения микроскопичных явлений, происходящих на уровне атомов.
Питтинги развиваются по следующему пути:
а. Зарождение (возникновение) питтинга;
б. Развитие (рост) питтинга;
в. Прекращение роста питтинга (репассивация).
Казалось, всё так просто. К сожалению (или к счастью), оказывается, что необходимо ждать довольно долго (иногда 60 дней и более), чтобы «родился» питтинг. Но это не значит, что он будет расти всё время по какому-то определённому закону. Он может замедлять свой рост, «залечиваться» или ускоряться, соединяться с другими питтингами до появления катастрофического отверстия. Как видите, довольно много сценариев в жизни питтингов. И практически невозможно предположить вероятность каждого из них. Кого вам это напоминает? Ну да, жизнь людей … Кто-нибудь может предсказать срок нашей жизни?
а. Зарождение питтинга происходит в местах дефектов пассивной пленки (царапины, разрывы, неоднородность сплава, различные интерметаллические включения и … среды) при достижении определенного электрического потенциала на поверхности сплава – потенциала питтингообразования. Было бы легче объяснить с помощью электрохимии, но нам придётся обойтись без неё в этом путешествии. Ионы-активаторы (хлориды) разрушают оксидную защитную пленку (Cr2O3 на нержавеющей стали) и замещают кислород в ней. Например, устойчивый оксид хрома превращается в соль CrCl3, способную гидролизоваться с образованием кислоты:
где M3+ = Cr3+ или Fe3+. Ионы гидрония (H3O+), образующиеся в этой реакции, и ионы Cl–, присутствующие в окружающей среде, будут объединяться с образованием соляной кислоты (HCl), что приведет к снижению pH примерно до 1…2 в областях под дефектами в пассивной плёнке. Раствор за пределами этих кислотных областей является нейтральным, в котором происходит катодная реакция.
Не только разрушение оксидной плёнки, но и слоя нерастворимой соли или плёнки ингибитора тоже может вызвать питтинговую коррозию.
Из-за неоднородности поверхности на нержавеющей стали под пассивной плёнкой будут образовываться питтинги разной формы, плотности и размера. Форма, плотность, размер и глубина образовавшихся питтингов зависят от концентрации анионов, температуры и режима течения жидкости. Чем медленнее течет раствор, тем больше время контакта анионов с поверхностью металла и тем выше вероятность повреждения плёнки и возникновения питтинга.
б. Развитие питтинга происходит по электрохимическому механизму вследствие растворения пассивной защитной оксидной плёнки и слоя под ней. Иногда эту стадию делят на две. На первой стадии, называемой активационной, происходит интенсивный рост питтинга. На второй стадии, называемой диффузионной, происходит замедление роста питтинга из-за расширения его площади и возникающих диффузионных ограничений.
Существует несколько состояний развития питтинга, каждое с конечной вероятностью. Несколько переменных факторов влияют на эту вероятность.
в. Прекращение роста питтинга. Вновь образованные питтинги, которые не развиваются, могут репассивироваться.
- Методы определения стойкости металлов и сплавов против питтинговой коррозии
Лабораторные методы испытаний были разработаны для определения сопротивления металлов питтинговой коррозии. Эти испытания преследуют две основные цели. Во-первых, дать возможность ранжировать каждый сплав в порядке стойкости против питтинговой коррозии. Во-вторых, как мера контроля качества нержавещей стали, чтобы гарантировать, что определенные партии стали произведены с получением не только правильного состава, но также надлежащим образом прокатаны и подвергнуты соответствующей термообработке.
3.1. Эквивалентное число сопротивления питтингу (PREN – pitting resistance equivalent number)
Было обнаружено экспериментально, что оценка сопротивления питтингу может быть сделана на основе расчета эквивалентного числа сопротивления питтингу (PREN):
где: %Cr (хром), %Mo (молибден), %N (азот)– массовая концентрация трёх важных компонентов нержавеющих сталей. Обратите внимание, что множитель перед Cr – 1, перед Mo – 3,3, а перед N – 16. Этот факт указывает на возрастающую роль Mo и N в нержавеющих сталях в их стойкости против питтинговой коррозии, поэтому необходимо выбирать сталь как можно с большим значением PREN. Несложно, не так ли?
Общее правило: в морской воде рекомендуется применять нержавеющие стали с PREN > 40. Как правило, это нержавеющие стали, содержащие не менее 6% Mo и ~0,2%N, например, 254 SMO и AL-6XN.
Необходимо отметить, что Мо является дорогой добавкой. Азот практически ничего не стоит. Нет, стоит, но недорого. Некоторые авторы считают, что вольфрам W тоже положительно влияет на стойкость стали против питтинговой коррозии. Поэтому необходимо найти баланс в стоимости сплава и его стойкости против питтинговой коррозии. К сожалению, Mo обладает отрицательным свойством в сварочных швах.
3.2. Эффект сварки
Процесс сварки приводит к металлургическим изменениям как в зоне плавления сплава, так и в зоне термического влияния. В большинстве сплавов при сварке происходит некоторое ухудшение стойкости против питтинговой коррозии. Так, сплавы с высоким содержанием Mo особенно чувствительны к микросегрегации в зоне плавления, что приводит к снижению сопротивления питтингу. Такие сплавы, как UNS S34565 (Remanit 4565 S), которые достигают своей стойкости против питтинговой коррозии за счет высокого содержания N (0,4–0,6%), а не за счет очень высокого уровня Mo (4–5%), в меньшей степени подвержены сегрегации материала в сварных швах.
Эти эффекты можно свести к минимуму, если использовать надлежащие материалы электродов и соответствующие методы сварки. Важно запрашивать у поставщиков сплавов правильную информацию.
3.3. Критическая температура образования питтингов (CPT – critical pitting temperature)
CPT определяется как самая низкая температура, при которой начинается питтинговая коррозия на металлической поверхности. Ниже этой температуры нержавеющая сталь не подвержена питтинговой коррозии при воздействии агрессивных хлоридных растворов (например, FeCl3) [3] или когда подвергается постоянному анодному потенциалу в агрессивной среде [4]. Эксперимент с постоянным анодным потенциалом может быть проведен для определения CPT путем повышения температуры испытания до тех пор, пока не возникнет большой ток питтингообразования. CPT – это температура, при которой плотность тока превышает 100 мкА/см2 в течение не менее 60 с. Значения CPT являются более точным и надежным средством для сравнения различных типов нержавеющих сталей, чем значения PREN (рис. 4).
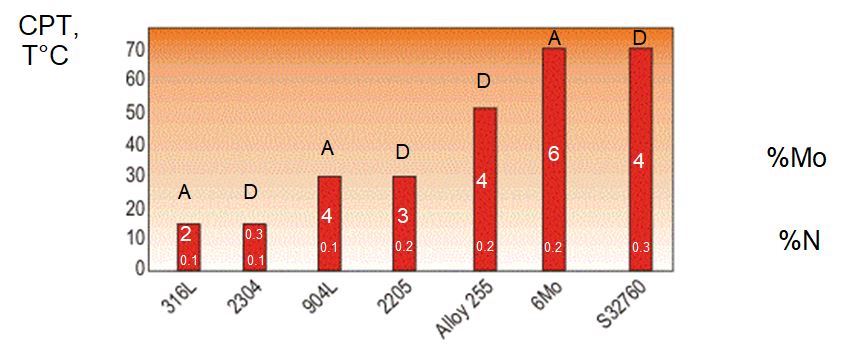
Необходимо отметить, что любые лабораторные испытания являются сравнительными и не дают 100%-ной гарантии, что питтинговая коррозия не произойдёт. Нельзя забывать, что как сплав, так и среда вокруг сплава могут быть гетерогенны и изменяться во времени. И мы, как правило, не способны это контролировать. Это может привести к питтинговой коррозии даже в случаях, когда сплав успешно прошел лабораторные испытания.
- Прогнозирование питтинговой коррозии
Хлорид-анионы наиболее распространены в окружающей среде и промышленных системах. По этой причине было решено сформулировать рекомендации относительно критической концентрации хлорид-анионов в воде при различных температурах, которые могут представлять значительный риск возникновения питтинговой коррозии нержавеющих сталей различных видов. К сожалению, разные авторы предложили разные значения критической концентрации хлорид-анионов для одной и той же стали.
Расчет значений PREN и определение критических температур CPT позволило специалистам определить, какие типы нержавеющих сталей подходят для использования при различных концентрациях хлоридов и при разных температурах (рис. 5).
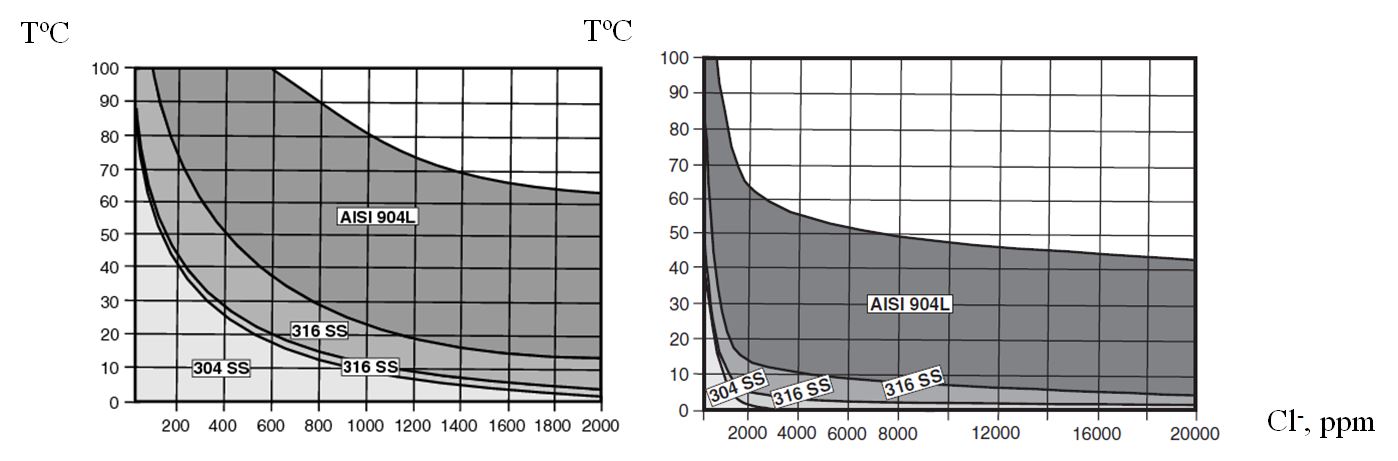
Чем выше температура, тем ниже критическая концентрация хлоридов в воде, необходимая для образования питтингов.
- Меры по уменьшению, предупреждению и контролю питтинговой коррозии
Существует довольно широкий спектр мер по предотвращению и контролю питтинговой коррозии.
а. Перед тем, как выбрать сплав, постарайтесь полностью изучить физико-химический состав окружающей среды, контактирующей с ним, и условия эксплуатации (температуру и гидродинамический режим, возможность стагнации жидкости). По возможности, контролируйте её состав и условия: как можно с меньшим содержанием хлоридов и низкой температурой. Если в воде присутствуют микроорганизмы, то необходимо предусмотреть меры по периодическому введению биоцидов (например, гипохлорит натрия) и постоянному контролю микроорганизмов и самих биоцидов. Можно воду фильтровать через специальные биологические фильтры, но учтите, что это процесс довольно медленный.
б. Выполняйте проект оборудования таким образом, чтобы избегать образование щелей и застойных зон.
в. Правильно выбирайте материалы с повышенной стойкостью против питтинговой коррозии. Используйте сплавы с достаточно высоким содержанием хрома, молибдена и азота. Как правило, такими сплавами являются аустенитные и дуплексные нержавеющие стали. Помните, что добавка молибдена существенно увеличивает стойкость сплава против питтинговой коррозии. Так, она растёт в ряду (в скобках указана концентрация молибдена в массовых процентах): 316 (2–3) 08Х17Н13М2 < 317 (3–4) 08X19H13M3 < 904L (4–5) < 254 SMO (6,1) или AL-6XN (6,3).
г. Выполняйте сварку с использованием подходящих материалов и методов и убедитесь в отсутствии образования случайных щелей по окончании сварки.
д. Перед эксплуатацией оборудования подготовьте его поверхность: удалите неровности, дефекты, включения и все загрязнения на поверхности, особенно свободное железо и окалину, а затем проведите пассивацию поверхности нержавеющей стали [5]. Зеркальная поверхность наиболее стойка против питтинговой коррозии.
е. Уменьшайте агрессивность окружающей среды (нейтрализация кислот, уменьшение температуры, удаление хлоридов, очистка и промывка от кислых осадков).
ж. Проводите технологические мероприятия: обеспечьте хорошую циркуляцию воды; дренаж и промывку, если циркуляция остановлена. Правильно обслуживайте оборудование из нержавеющей стали.
з. Используйте ингибиторы коррозии. Нитраты (NO3–), гидроксиды (OH–) и фосфаты (PO43–) уменьшают образование питтингов в присутствии Cl– в окружающей среде. Использование этих анионов основано на их избыточной адсорбционной способности на поверхности нержавеющих сталей по сравнению с хлоридами.
и. Используйте электрохимическую защиту: катодную и анодную (для пассивных металлов), иногда вместе с ингибиторами. Катодная защита предохраняет металлическую поверхность от коррозии, превращая ее в катод или заряжая отрицательным зарядом. Анодная защита предусматривает содержание металлической конструкции в пассивном состоянии.
к. Используйте покрытия. Они изолируют металлические поверхности от воздействия хлоридов и других агрессивных компонентов.
Как видите, есть много возможностей контроля питтинговой коррозии. Несмотря на прогресс в понимании механизма протекания питтинговой коррозии, возможности определения склонности сплавов к ней и разработки мер предотвращения, я постоянно наблюдаю преобладающее её проявление в разных отраслях промышленности. В связи с этим хочу поделиться разными случаями питтинговой коррозии, которые мне пришлось исследовать.
- Примеры питтинговой коррозии в промышленности
По-видимому, не существует промышленности и установок, где бы не происходила питтинговая коррозия. Более всего страдают нержавеющие стали. Само понятие нержавеющие стали – это оксюморон (сочетание противоречащих друг другу понятий), как горячий снег, честный политик, сухое вино, страшно красив. Так вот, с нержавеющими сталями может происходить 15 коррозионных явлений. И самое неприятное – питтинговая коррозия. Все нержавеющие стали можно считать восприимчивыми к питтинговой коррозии, но их сопротивление сильно различается.
6.1. Питтинговая коррозия малоуглеродистых сталей
Причин питтинговой коррозии малоуглеродистых сталей существует довольно много. И даже не обязательно присутствие хлоридов. Рассмотрим на конкретных примерах некоторые из них.
6.1.1. Питтинговая коррозия углеродистой стали в чистой воде
Деаэрированная вода поступала в парогенератор при температуре 90°C и давлении 5 бар. В линии не было измерителя растворенного кислорода в течение 4 лет. Таким образом, качество воды в этот период было неизвестно. Кислородомер, установленный на 5-й год, регистрировал высокие концентрации растворенного кислорода в деаэрированной воде, до 200 ppb, когда допустимая максимальная концентрация должна была быть не более 30 ppb. Питтинги были обнаружены на дне корпуса парогенератора через 5 лет (рис. 6). На внутренней поверхности стенок парогенератора образовалась красно-коричневая ржавчина, что указывало на присутствие растворённого кислорода в воде и паре.
-
Рис. 6. Питтинговая коррозия углеродистой стали в чистой воде. Причина: аэрационные пары (кислородная коррозия, питтинговая коррозия из-за растворенного кислорода). а – днище корпуса парогенератора; б – стенка парогенератора Решение: поддерживать концентрацию растворенного кислорода в деаэрированной воде менее 30 ppb.
6.1.2. Питтинговая коррозия углеродистой стали под неорганическими отложениями
Иногда неорганические или органические соли, образующиеся на поверхности углеродистой стали, могут вызывать питтинговую коррозию (рис. 7). Например, это явление можно увидеть в верхней части атмосферной дистилляционной колонны нефти на нефтеперерабатывающих заводах. В этой зоне могут образовываться отложения солей хлорида аммония (NH4Cl) на поверхности углеродистой стали, которая гидролизуется следующим образом:
Рис. 7. Питтинговая коррозия углеродистой стали под кислыми отложениями:
а – питтинги на трубной решетке теплообменника в верхней части атмосферной дистилляционной колонны нефти (4 года); б – металлический купон (4 месяца)Образовавшаяся соляная кислота накапливается под солью и вызывает уменьшение pH до 3, а затем появление питтинговой коррозии на соответствующих участках (см. рис. 6). Иногда этот тип коррозии называют коррозией под отложениями.
Решение: промывка водой от отложений.
6.1.3. Питтинговая коррозия углеродистой стали при температуре ниже температуры точки росы кислот
Конденсация кислот при при температуре ниже температуры точки росы – еще один механизм, который может вызвать питтинговую коррозию (рис. 8).
Рис. 8. Интенсивная питтинговая коррозия корпуса теплообменника из углеродистой стали в результате конденсации HCl. Поверхность выглядит губчатой и напоминает морфологию, вызванную кавитацией. Кислотная питтинговая коррозия углеродистой стали при температуре ниже температуры точки росы. Решение: поддержание температуры на 30ºС выше температуры точки росы.
6.1.4. Питтинговая коррозия углеродистой стали в водных растворах, содержащих хлориды (Cl–)
При любой концентрации хлоридов в воде углеродистая сталь подвержена питтинговой коррозии (рис. 9). Режим протекания воды и концентрация хлоридов существенно влияют на форму питтинговой коррозии.
Рис. 9. Питтинговая коррозия углеродистой стали в растворах, содержащих хлориды (Cl-):
а – купон после контакта с 3,5% NaCl в течение 30 суток (стагнация); б – внутренняя поверхность теплообменника с оборотной водой, содержащей 0,01–0,05% хлоридов (4 года); в – увеличение рис. б после удаления рыхлой ржавчиныРешение: применение лакокрасочных покрытий; впрыскивание ингибиторов коррозии; замена углеродистой стали медными сплавами; применение лакокрасочных покрытий совместно с катодной защитой.
6.1.5. Питтинговая коррозия углеродистой стали из-за гальванической коррозии, вызванной наличием катионов металла в воде
В системах водяного охлаждения часто используются теплообменники из различных сплавов (углеродистой стали и латуни, алюминия и меди), при этом сплавы не находятся в электрическом контакте. Однако эти комбинации могут вызвать гальваническую коррозию, приводящую к образованию питтингов (рис. 10).
Рис. 10. Гальваническая коррозия углеродистой стали из-за наличия катионов Cu2+ в охлаждающей воде (через 40 дней):
а – купоны из стали с частицами меди на поверхности; б – те же купоны после удаления частиц медиЕсли ингибиторы коррозии меди не вводятся в охлаждающую воду, то медь корродирует в воде, содержащей растворенный кислород, и накапливается на стальных поверхностях. Катионы меди будут находиться в физическом контакте с атомами железа и получать от них электроны. Другими словами, гальванические элементы будут формироваться на поверхности железа, которое будет подвергаться питтинговой коррозии в точках контакта с атомами меди (см. рис. 10). В связи с этим необходимо вводить ингибиторы коррозии меди в водные оборотные охлаждающие системы.
Особую опасность представляет совместное присутствие алюминиевых и медных конструкций в водных системах. Разница электрических потенциалов между медью и алюминием может достигать более одного вольта. Часто алюминий, подвергающийся такой гальванической коррозии, превращается в порошок гидроксида алюминия. Жаль, что электрический ток, образовавшийся в результате гальванической коррозии между медью и алюминием, не может быть использован с пользой …
Решения: при совместном присутствии стальных и медных конструкций необходимо вводить ингибиторы коррозии меди в водные оборотные охлаждающие системы; не рекомендуется использовать алюминиевые и медные конструкции в одной водной системе.
6.1.6. Питтинговая коррозия как результат эрозии-коррозии
В насосах часто образуется турбулентный поток жидкостей, что приводит к эрозии – кавитации – коррозии (рис. 11). Несложно обнаружить это явление по морфологии повреждённой поверхности: как будто кто-то ел мороженое маленькой ложечкой.
Рис. 11. Питтинговая коррозия внутренней поверхности насоса из чугуна после 4-х лет эксплуатации (среда – метилдиэтаноламин). Эрозия – кавитация – коррозия из-за турбулентности потока Решение: использовать насосы с внутренней поверхностью из нержавеющей стали 316.
6.1.7. Питтинговая коррозия как результат микробиологической коррозии
Микробиологическая коррозия (МБК) – это коррозия, которая происходит с участием некоторых особых видов микроорганизмов на поверхности металлов. Для возникновения МБК недостаточно присутствия в окружающей среде микроорганизмов. Они должны быть активными и способствовать коррозии металла. МБК происходит на металлической поверхности в присутствии подходящей среды и условий. Результаты МБК на металлических поверхностях обнаруживаются в виде углублений, которые похожи на питтинговую коррозию (рис. 12). Поэтому специалисты по коррозии дали юмористическое определение: «МБК – термин, используемый для описания питтинговой коррозии, когда никакой другой механизм коррозии не соответствует данным условиям».
Рис. 12. Язвы на днище надземных резервуаров для хранения дизельного топлива – 15 лет (а); нефти – 18 лет (б); мазута – 15 лет (в) Решение: нанесение лакокрасочных покрытий и тщательная периодическая промывка днищ от отложений.
Питтинговая коррозия и юмор
Чувство юмора – это высочайшее проявление интеллекта. Старайтесь в любой встрече и теме находить смешное.
Ударная коррозия или ударная атака (Impingement attack) – это форма эрозии-коррозии, обычно связанная с местным ударом высокоскоростной среды о металлическую поверхность. Обычно, как вы видите из рис. 13, ударная коррозия, приводящая к питтингу, – это неожиданная, непредвиденная, внезапная атака.
Рис. 13. «Ударная коррозия» – локальная атака, связанная с большой скоростью протекающей среды. Слева – питтинг, образовавшийся на Адмиралтейской латуни от удара выходящим паром из треснувшей трубки Вместо заключения
Говорят, путешественник радуется дважды: когда выходит из дома и возвращается домой. В нашем же путешествии мы узнали столько интересного и неожиданного, что я с нежеланием расстаюсь с этой темой и тобой, читатель. Несмотря на мою длительную карьеру в коррозии, мне продолжает быть интересно … Потому что я вижу в ней красоту и новые дали… Тем не менее, подведём итоги нашего путешествия и заглянем в будущее. Что я предлагаю вам делать, чтобы уменьшить опасность питтинговой коррозии?
- На этапе проектирования знание природы окружающей металла среды и, в частности, концентрации хлорид-ионов и температуры, является полезным для оценки пригодности конкретной марки нержавеющей стали для предполагаемого применения в конкретных условиях. Несмотря на существование критических величин концентрации хлоридов в водных средах, следует к ним относиться осторожно, как к «практическому ориентировочному правилу» (Rule of thumb).
- Стойкость нержавеющих сталей против питтинговой коррозии определяется легирующими элементами, такими как хром, молибден, азот и вольфрам. Синергетический эффект этих легирующих элементов помогает стабилизировать пассивную пленку, а в случае её разрушения может произойти быстрая репассивация питтингов и заживление поврежденного участка. Этот эффект обычно определяется числом PREN. Чем оно больше, тем больше стойкость нержавеющей стали против питтинговой коррозии. Поскольку питтинги являются зародышами в щелевой и некоторых других видах локальной коррозии, то значение PREN является и критерием стойкости нержавеющих сталей. Принято считать, что стали с PREN > 40 проявляют высокую стойкость в морской воде. Обычно такие стали содержат 6% молибдена и 0,2% азота. Не забывайте, что значения PREN не гарантируют иммунитет нержавеющих сталей против питтинговой коррозии. При определённых обстоятельствах и они могут подвергаться питтинговой коррозии.
- Не рекомендуется использовать нержавеющие стали в морской непроточной воде, потому что длительный контакт с ней и отсутствие достаточного потока вызывают возможность длительного контакта хлоридов с пассивной плёнкой стали и ее повреждение. Когда морская вода течет по трубопроводам, теплообменникам или насосам, хлориды не успевают оседать на металлических поверхностях и находиться с ними в продолжительном контакте. В связи с этим оборудование из нержавеющей стали можно использовать только в морской воде с постоянным её потоком. Кроме того, не забудьте слить воду, содержащую хлориды, из оборудования при его остановке и обязательно промойте стальные поверхности водой, не содержащей хлорид-анионов.
- Так что? Выходит, нет 100%-ного спасения от питтинговой коррозии? И здесь вас ждёт философский ответ: и да, и нет. Стремитесь к выполнению всех мер по уменьшению, предупреждению и контролю питтинговой коррозии. Как и всё в природе, рождается, живёт и умирает, в наших силах продлить жизнь металла. И, конечно, пока математики и физики не подключатся к построению моделей и прогнозированию питтинговой коррозии, успеха не видать.
Список литературы
- ASTM G46 – 94(2018). Standard Guide for Examination and Evaluation of Pitting Corrosion//ASTM International, West Conshohocken, PA, USA, 2018.
- Alec Groysman. Corrosion for Everybody//Springer, Dordrecht, 2010, 368 p.
- ASTM G48-11(2020)e1. Standard Test Methods for Pitting and Crevice Corrosion Resistance of Stainless Steels and Related Alloys by Use of Ferric Chloride Solution//ASTM International, West Conshohocken, PA, USA, 2020.
- ASTM G150-18. Standard Test Method for Electrochemical Critical Pitting Temperature Testing of Stainless Steels and Related Alloys//ASTM International, West Conshohocken, PA, USA, 2018.
- ASTM A380 / A380M-17. Standard Practice for Cleaning, Descaling, and Passivation of Stainless Steel Parts, Equipment, and Systems//ASTM International, West Conshohocken, PA, USA, 2017.
Об авторе
Доктор Алик Гройсман Доктор Алик Гройсман
имеет более чем 40-летний опыт работы в сфере материаловедения, коррозии, контроля коррозии и мониторинга коррозии в нефтеперерабатывающей, нефтегазовой и нефтехимической промышленности, исследований и преподавания в указанных областях.
В настоящее время доктор Алик Гройсман проводит курсы лекций по дисциплинам «Коррозия и контроль коррозии» и «Материалы и стандарты в нефтегазовой инженерии» в Израильском технологическом институте («Технион»), «Коррозия и контроль коррозии в биотехнологии» в Ариэльском университете (Израиль), «Коррозия и контроль коррозии в энергетической промышленности» в Израильском иституте энергии и охраны окружающей среды.
Особый интерес для него представляют взаимосвязи между безопасностью технологических процессов, окружающей средой и явлениями коррозии, а также роль безопасности и человеческого фактора в управлении и контроле коррозией; образование в области коррозии и поиск взаимосвязей между коррозией, искусством, историей и философией.
Алик Гройсман является автором трёх книг:
- «Corrosion for Everybody» («Коррозия для всех»),
- «Corrosion in Systems for Transportation and Storage of Petroleum Products and Biofuels» («Коррозия в системах транспортировки и хранения нефтепродуктов и биотоплив»),
- «Corrosion Problems and Solutions in Oil Refining and Petrochemical Industry» («Проблемы коррозии и их решения в нефтеперерабатывающей и нефтехимической промышленности»).
В настоящее время издаётся его книга-учебник о коррозии на иврите.
Он также пишет главу о коррозионных свойствах авиационных топлив на английском.
Он является консультантом по вопросам материаловедения и коррозии в нефтяной, газовой, нефтеперерабатывающей, нефтехимической и химической промышленности, производстве металлического и неметаллического оборудования, а также организатором курсов по коррозии в Великобритании, Чехии, Словакии, России (Санкт-Петербург), Новой Зеландии, Канаде и Казахстане.
Доктор Гройсман является почетным президентом Израильской ассоциации инженеров-химиков и химиков.
Публикации и полную информацию о докторе Алике Гройсмане можно найти на его сайте: www.groysmanalec.com