Авторы: А.Н. Монахов (НПП ООО «Корсистем»), М.А. Меркушева (МИП ООО «Эко-Кемикел»)
Опубликовано на портале «Химическая техника», ноябрь 2020
В настоящее время экономические потери из-за коррозии технологического оборудования огромны и сопоставимы с затратами на развитие крупнейших отраслей промышленности, при этом потери возрастают вследствие интенсификации производств и изменения состава рабочих сред.
По мнению экспертов [1, 2], занимающихся изучением коррозионного изнашивания оборудования НПЗ, можно выделить ряд существенных факторов, с которыми можно столкнуться в перспективе:
- повышение содержания сернистых соединений в товарных нефтях;
- неподготовленность оборудования для переработки высокосернистой и тяжелой нефти;
- увеличением рисков, ведущих к отказам оборудования из-за повышения содержания коррозионно-активных элементов в перерабатываемых средах
На НПЗ России, начиная с 1991 г. и по настоящее время, наблюдается неритмичность загрузки мощностей основных производств при переработке нефти, вызванная в первую очередь нестабильностью на рынке спроса и предложения.
Промышленные испытания [3–5] показали, что при переработке нефти из-за коррозии из строя выходит прежде всего колонное, емкостное и конденсационно- холодильное оборудование установок.
Анализ результатов испытаний показал, что при эксплуатации установок первичной переработки нефти питтинговой коррозии подвержены все черные металлы. Наибольшая глубина питтингов отмечена для стали 08X13 – основном материале плакирующих слоев. Питтинговая коррозия стали 08X13 является одной из главных причин коррозионного растрескивания плакирующих слоев, сварных швов и околошовных зон, которое зафиксировано во всех аппаратах и сосудах, изготовленных из биметаллов. При этом скорость питтинговой коррозии на порядок превышает показатель обшей коррозии, что говорит о недооценке коррозионного износа в случае, если за основу берется показатель общей коррозии, что в основном и делается на большинстве НПЗ в России.
Полученные результаты свидетельствуют, что не все материалы, выступающие в качестве плакирующего слоя, обеспечивают необходимую коррозионную стойкость. Отложения, формируемые при эксплуатации на теплообменном оборудовании, создают очаги коррозионной активности в процессе осаждения на них влаги (особенно при пропаривании) и способствуют развитию питтинговой коррозии. При этом возникает необходимость в изучении коррозионного влияния на металл оборудования не только на этапе эксплуатации, но и на этапах проведения ремонта или запуска (остановки) установок как при регламентных режимах эксплуатации, так и вне.
Напрашивается необходимость в проведении всестороннего анализа при оценке износа оборудования установок с учетом комплексного подхода: при изучении причин коррозионного изнашивания оборудования и проводимых мероприятий по его антикоррозионной защите.
В настоящее время существует понимание, что уровень коррозионных процессов на установках первичной перегонки нефти зависит от ритмичности и стабильности загрузки в рамках действующего регламента, а также от частоты простоев, периодов горячей и холодной циркуляции, подготовки к ремонтам, ремонтов, консервации оборудования на периоды простоев и т.п. При этом перед проведением ремонтных работ пропаривание аппаратов и трубопроводов производят по старым регламентным схемам, без учета изменений состава рабочих сред и формируемых осадков, что приводит к образованию коррозионно-агрессивных конденсатов – водных растворов электролитов, содержащих в высоких концентрациях хлорид-, сульфат-, тиосульфат-, сульфид-, сульфит- и другие ионы.
Формируемые на стенках после пропаривания кислоты водные конденсаты усугубляют коррозионные проблемы и ведут к преждевременному изнашиванию оборудования.
В процессе эксплуатации основная углеводородная составляющая нефти не обладает коррозионной агрессивностью. Коррозию вызывают продукты расщепления и превращения примесей и гетероорганических соединений, содержащихся в нефтях: серу-, азот-, кислород- и хлорсодержащих соединений, нейтральных и кислых смолистых веществ, нафтеновых кислот, металлоорганических соединений, под воздействием температуры и давления,.
По данным опытно-промышленных испытаний, проведенных на МНПЗ [6], состав хлорорганических соединений и солей в нефтях, поступающих на установки первичной перегонки нефти, нестабилен (рис. 1, 2).
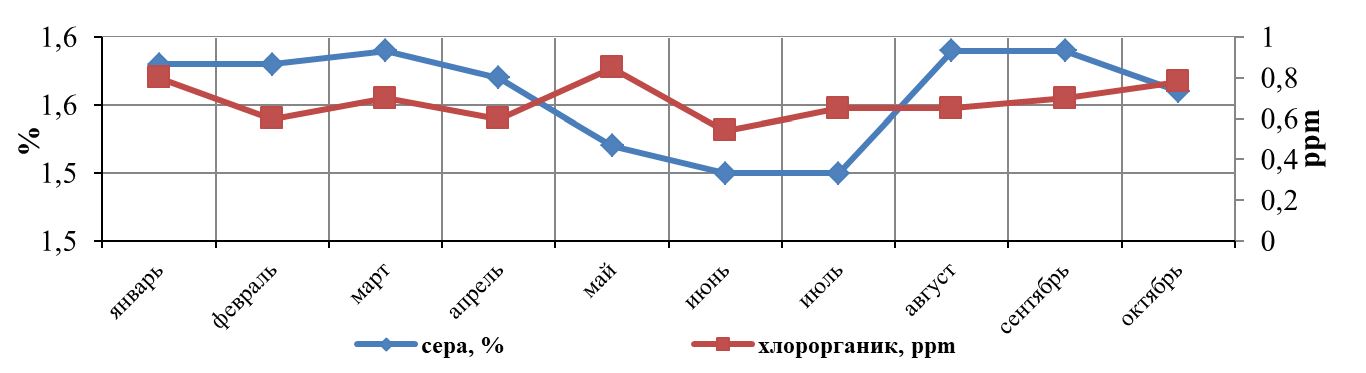
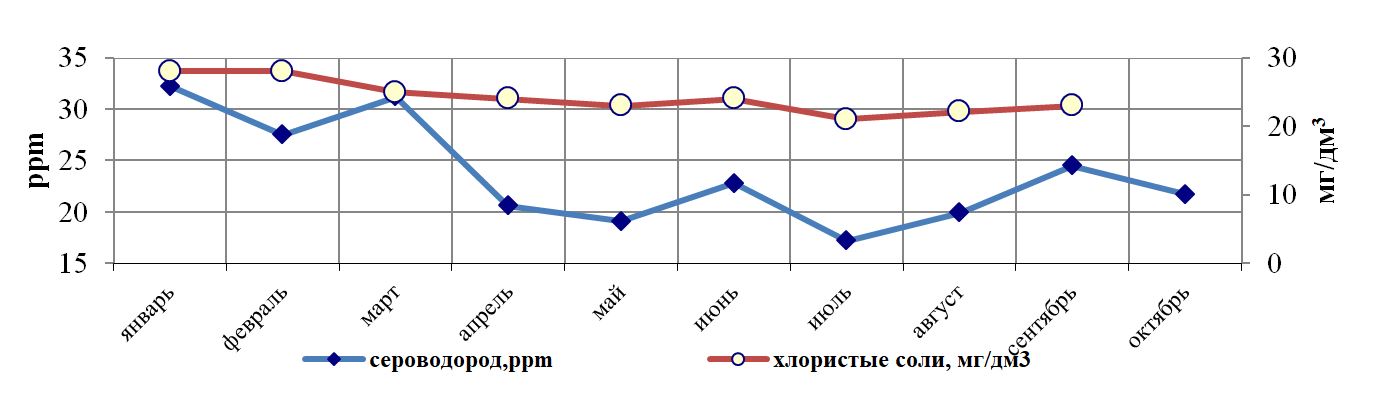
Все это говорит о периодических и непредсказуемых последствиях, вызываемых коррозионной активностью среды, ведущих к преждевременному изнашиванию оборудования.
Как следствие, на многих НПЗ процесс коррозионного изнашивания оборудования имеет нестабильный характер. В качестве примера на рис. 3 представлены динамические тренды контроля скорости коррозии в шлем линиях атмосферных и стабилизационных колонн в ОАО «НК НПЗ» за период с период с 2007 по 2012 годы [7].
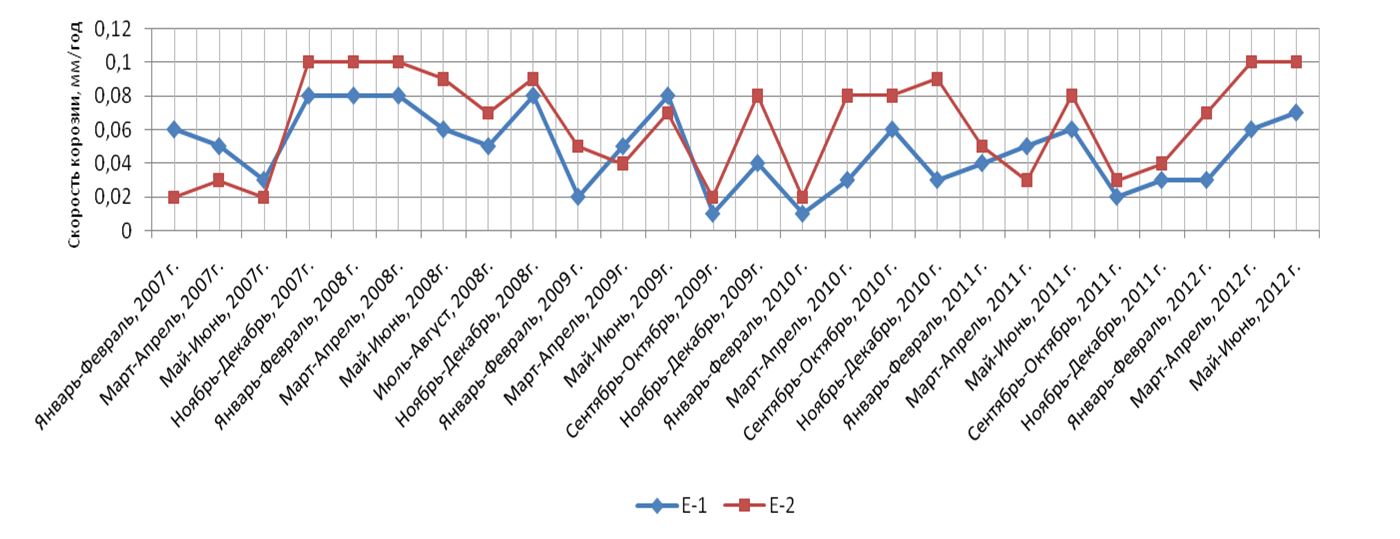
Как видно, несмотря на то, что службами завода выполняются регламентные работы по защите технологического оборудования от коррозии, показатель скорости нестабилен. Аналогичная ситуация практически на всех заводах НПЗ в России.
В чем проблема и где пути выхода?
Этим вопросом в настоящее время задаются многие специалисты, на которых возложена задача по предупреждению коррозионного изнашивания оборудования. Понятно, что надежность и долговечность эксплуатации оборудования технологических установок НПЗ обеспечивается рациональным подбором конструкционных материалов и оптимальным подходом в организации химико-технологической защиты, начиная от процесса обессоливания. При этом по настоящее время на эффективность антикоррозионных мероприятий оказывают влияние человеческий фактор и традиционные устаревшие регламентные процедуры по контролю рабочей среды и выполнению антикоррозионных мероприятий. Большинство инженеров воспринимают коррозионный процесс как постоянный и стабильный процесс, за основу которого взяты работы по фиксированию скорости коррозии за определенные периоды времени. В реальных условиях характер влияния коррозии связан прежде всего с изменением условий переработки и состава рабочей среды во времени.
В настоящее время по-прежнему наблюдается большая зависимость от человеческого фактора и выбора правильности решений при разработке как процедур контроля, так и проводимых мероприятий защите от коррозии. Зачастую, не имея данных по скорости коррозии в динамике и аналитических данных во времени, специалисты ошибаются при подборе типа ингибиторов и регламентных дозировок, материалов в процессе ремонтов и проектных работ, антикоррозионных покрытий и разработке технологических режимов. Бесспорным подспорьем в решении указанных проблем могут быть системы аналитического контроля в режиме реального времени, включая системы управления ингибиторной защитой и коррозионного мониторинга. В этом случае показатель скорости коррозии уже воспринимается не как статистическая величина, а как переменная во времени, которая позволит управлять и оптимизировать химико-технологической защитой.
Не менее важным аспектом при осуществлении антикоррозионных мероприятий является правильный выбор средств контроля над процессами коррозии. Анализ датчиков коррозии, применяемых в настоящее время на НПЗ, приводит к выводу, что подбор датчиков порой определяется не детальным изучением необходимости, а ценой. Большая часть средств контроля коррозии определяет только общую коррозию во времени, что ограничивает понимание преобладающего влияния некоторых видов скорости коррозии на металл, особенно в условиях воздействия сернистой нефти. Не получая нужной информации, инженеры-коррозионисты часто возвращаются к применению гравиметрического метода, что существенно снижает понимание воздействия коррозии на металл.
В настоящее время изменения состава рабочих сред и условий при переработке нефтей приводят к следующим выводам.
Первое. Подбор средств контроля должен осуществляться после детального анализа специалистами, занимающимися изучением коррозии и ее причин, а не полагаться на рекомендации заводов – поставщиков оборудования, ибо решаемые задачи на предприятии и поставщиков зачастую разные.
Второе. Внедрение систем контроля реального времени не решает проблему оптимизации антикоррозионных мероприятий на НПЗ, ибо влияние человеческого фактора на правильность и своевременность управленческих решений еще значительно сохраняется.
Третье. Система коррозионного мониторинга в реальном времени – это лишь инструмент, при помощи которого можно получить большой экономический и технический эффект, но для достижения этого эффекта необходимо внедрить современный коррозионный менеджмент на предприятии.
Именно в Положении о коррозионном менеджменте должны быть четко определены политика и стратегия в области коррозионной защиты и целостности технологического оборудования на предприятии, а также взаимодействие служб и специалистов, прямо или косвенно влияющих своими действиями на коррозионные процессы при эксплуатации.
Четвертое. При работе с высокосернистыми и тяжелыми нефтями в России уже столкнулись с высокими экономическими потерями, вызванными более интенсивным протеканием коррозионных процессов. В связи с этим требуется проведение НИОКР по изучению коррозионных процессов и разработки новых нормативно-методических документов, включающих такие разделы, как применение системы контроля и управления ингибиторной защитой в реальном времени.
Список литературы
- 1. N.P. HILTON. Mitigate corrosion in your crude unit кeal-time analyzers can provide improved monitoring of chloride levels and enable better corrosion control practices//Nalco Energy Services, Sugar Land, Texas, and J.L. SCATTERGOOD. Special Report. September 2010/ NALCO.
- J. Gutzeit, R.D. Merrick and L.R. Scharfstein. Corrosion in petroleum refining and petrochemical operations//ASM Handbook. Corrosion. Vol. 13. ASM International, 1987.
- Алцыбеева А.И., Бурлов В.В., Палатик Г.Ф., Соколов В.Л. Принципы ингибиторной защиты оборудования установок первичной переработки нефти//Вестник Удмурдского университета. 2006. №8.
- Бурлов В.В. Комплексная защита от коррозии металла оборудования нефтеперерабатывающих и нефтехимических производств // Инфлисток. ЛЦНТИ. 1991. №243.
- Бурлов В.В., Алцыбеева А.И., Парпуц И.В. Защита от коррозии оборудования НПЗ. СПб: Химиздат, 2005.
- Отчет по опытно-промышленным испытаниям на АВТ-3 и ЭЛОУ АВТ-6 МНПЗ ингибиторов коррозии Dodigen , Dodicor. М.: Clariant, 2010.
- Отчет по анализу технологического оборудования и методов контроля антикоррозионной защиты на установках АВТ-6 ОАО «СНПЗ», АВТ-11 ОАО «НК НПЗ». Материалы ОАО «СвНИНП», 2009.