Автор: Е.И. Тескер, С.Е. Тескер (ООО «Агромаш»),Д.Б. Жиляев (ООО «НГХК»).
Опубликовано в журнале Химическая техника №11/2014
Арматура является одним из самых распространенных устройств, используемых в нефтехимии и газовой отрасли. Эксплуатация различных типов клапанов, задвижек и т.п. осуществляется в сложных условиях, характеризуемых агрессивной средой, циклическими и ударно-циклическими нагрузками, недостаточной смазкой или ее полным отсутствием, широким диапазоном температур и т.п. В указанных условиях достаточно быстро развиваются процессы деградации поверхностных слоев контактирующих деталей, что приводит к изнашиванию и выходу из строя устройств. Для поворотных устройств характерны также высокие моменты страгивания, обусловленные большими коэффициентами трения сопрягаемых поверхностей. Создание таких моментов требует увеличения габаритных размеров и массы приводов. В результате многие фирмы выпускают продукцию, не удовлетворяющую требования потребителей.
Для повышения срока службы арматуры требуется создание принципиально новых технических решений, основанных не только на совершенствовании конструкций, но и на современных прогрессивных технологиях формирования требуемых свойств рабочих поверхностей быстро изнашивающихся деталей арматуры. Не случайно слоганом одной из ведущих фирм-производителей «NELES JAMESBURY» является «Пионеры в технологии производства клапанов».
Опыт эксплуатации арматуры свидетельствует о том, что конструктивные усовершенствования не всегда дают ожидаемый эффект. Кроме того, при этом отмечается значительное удорожание устройств. Расширение применения новых материалов, прежде всего эластичных полимеров, дает эффект только при определенных условиях эксплуатации. Применение гальванических покрытий (например, хромирование), а также наплавок разного рода не приводят к заметному улучшению эксплуатационных свойств.
В последние годы ряд зарубежных фирм освоил выпуск шаровых клапанов с уплотнением металл по металлу. Однако такие клапаны требуют высокой точности изготовления сопрягаемых поверхностей, что трудно обеспечить при высокой твердости металла клапана и седла (наплавка стеллитом).
На основании изложенного можно сделать вывод о том, что для успешного решения указанной проблемы требуются высокоэффективные универсальные технические решения, основанные на новых технологиях формирования поверхностных слоев трущихся деталей с заданными свойствами.
Приведем некоторые результаты исследований и разработок в области создания новых технологий и покрытий рабочих поверхностей быстро изнашивающихся деталей, выполненных специалистами ООО «Агромаш» (Россия, г.Волгоград) и фирмы Surfatec(Канада).
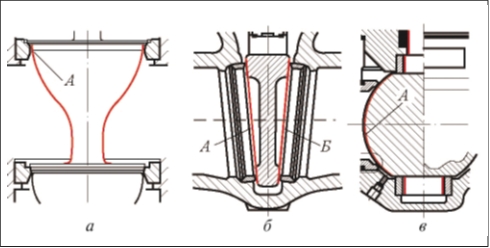
а – затвор клапана; б – фрагмент крана-задвижки;
в – шаровый клапан; А, Б – поверхности, подвергаемые обработке (помечены красным)
На рис. 1 представлены конструктивные схемы запорных и регулирующих устройств, для которых создавались новые технологии. Показаны участки рабочих поверхностей, которые подвергались лазерной обработке с применением новых технологий.
При выборе свойств поверхностных слоев деталей в качестве исходных данных необходима следующая информация:
- состав рабочей среды (включая возможные добавки и примеси);
- состояние среды (жидкое, газообразное, твердое, пар);
- санитарно-гигиенические требования (например, пищевые продукты);
- давление, температура среды; функциональное назначение устройства (запорное, регулирующее);
- режим работы (частота циклов и т.п.).
На первом этапе работ являлись исследовали предельные состояния рабочих поверхностей, которые приводят к потере работоспособности и выходу из строя деталей в результате интенсивного изнашивания.
Примеры предельно изношенных деталей приведены на рис. 2 и иллюстрируют состояние рабочих поверхностей после длительной эксплуатации устройств в ООО «Газпром Добыча Астрахань».
Метан, об.% 49,8
Сероводород, об.% До 27
Углекислый газ, об.% До 20
Жидкие углеводороды, г/м3 250
Сероорганические соединения, г/м3 До 10
Твердые парафины, мас.% До 2,17
Вода пластовая, г/м3 До 50
Общая минерализация пластовой воды г/м3 До 122
Показатель pH пластовой воды 3…3,5
Ионный состав пластовой воды, г/ дм3:
Хлорид-ион До 36
Сульфат-ион До 0,6
Гидрокарбонат-ион До 6
Натрий + калий До 27
Кальций До 14
Магний До 0,4
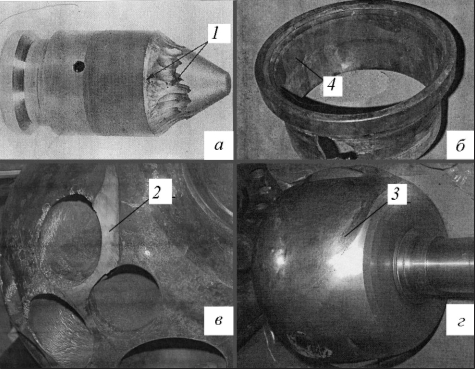
а – запорная игла; б – седло; в, г – шар;
1–4 – предельно изношенные участки поверхностей
На рис. 3, а изображены коррозионные повреждения клапанов из пищевого алюминия (анодированного) после длительного хранения в ООО «Новоуренгойский Газохимический Комплекс». Состав газожидкостной смеси, используемый в ООО «Газпром Добыча Астрахань»:
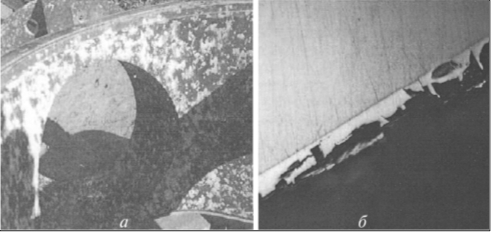
а – коррозия анодированного алюминия; б – разрушение покрытий, нанесенных по известным технологиям напыления порошковых материалов
Поскольку добыча и транспортировка, например нефти или газа, осуществляется в различных климатических зонах, оборудование должно надежно работать в диапазоне температур от –60 до +120°С в средах с различным содержанием H2S, CO2, хлоридов и других агрессивных веществ. По опыту создания арматуры для различных целей (химические технологии, атомная энергетика, гидроэнергетика, транспортировка нефти и газа) рекомендуется применять покрытия из сплавов следующих групп:
- кобальтовые;
- сложнолегированные сплавы(Fe–C2–Ni–Si, Mo);
- сплавы типа 20Х13;
- никелевые.
Кроме того, при создании арматуры применяется хромирование (твердое, диффузионное).
Одним из основных принципов получения высококачественных поверхностных слоев является отсутствие пористости, наличие которой приводит к быстрому разрушению покрытия (см. рис. 3, б).
На основании приведенных данных с целью повышения сопротивляемости изнашиванию и разрушению рабочих поверхностей были разработаны с использованием ноухау новые технологии лазерной модификации и нанесения композиционных многофункциональных покрытий.
Это позволило повысить конкурентоспособность, срок службы и эксплуатационные качества арматуры, обеспечить импортозамещение, сократить расходы на изготовление и эксплуатацию, значительно снизить коэффициент трения, в том числе при отсутствии смазки, уменьшить габаритные размеры и массу приводных устройств, снизить шум и вибрации и пр.
С целью повышения эксплуатационных качеств и восстановления работоспособности арматуры был разработан комплекс лазерных технологий и композиционных покрытий. Внешний вид деталей с нанесенными покрытиями приведен на рис. 4.
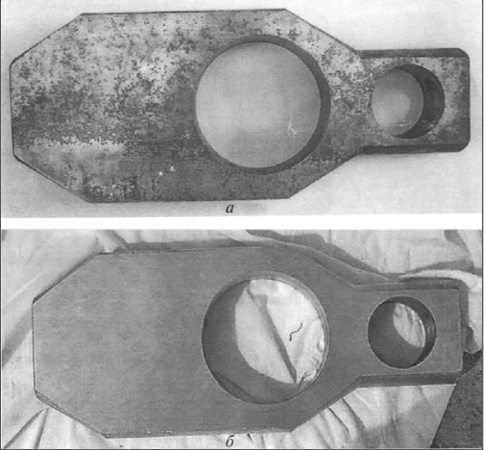
а – разрушение в процессе эксплуатации, поверхностный слой получен газотермическим напылением; б – состояние детали после нанесения лазерного покрытия и последующей эксплуатации
Как показали исследования и испытания свойств поверхностных слоев, разработанные технологии и покрытия имеют неоспоримые преимущества, которые заключаются в следующем:
- в структуре металла покрытия полностью отсутствует пористость, неметаллические включения и другие дефекты, снижающие контактную прочность и сопротивляемость изнашиванию (рис. 5); покрытие имеет более низкий коэффициент трения;
- покрытие обладает более высокими адгезионными свойствами, прочность сцепления с основным металлом находится в пределах 300…350 МПа, что в несколько раз превышает адгезионную прочность известных газотермических покрытий;
- покрытие может быть получено на локальных участках в зонах интенсивного изнашивания;
- химический состав покрытий может варьироваться в широких пределах, в том числе и в виде наноструктурируемых добавок, обеспечивающих оптимальную микроструктуру и необходимые свойства покрытий;
- при нанесении покрытий обеспечивается необходимая совместимость сопрягаемых трущихся поверхностей деталей запорного устройства;
- нанесение композиционных сложных покрытий требуемой толщины осуществляется на детали из экономнолегированных сталей, что обеспечивает значительный экономический эффект;
- разработанные методы формирования покрытий реализуются на роботизированных технологических лазерных комплексах. Процессы полностью автоматизированы.
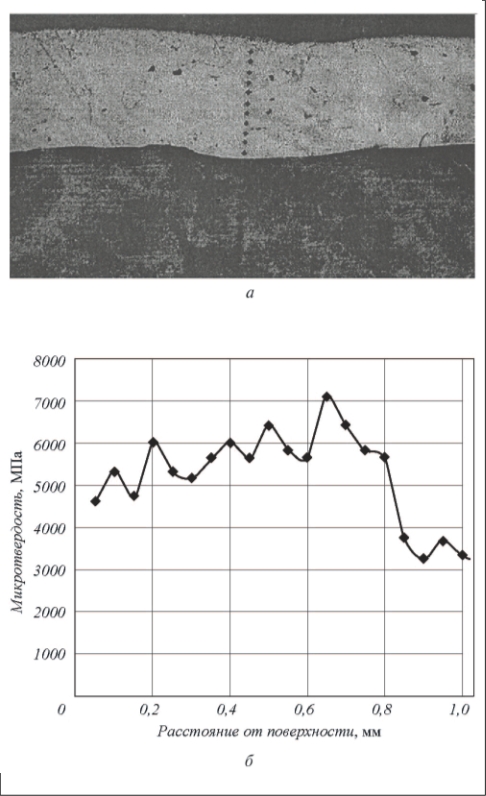
а – вид лазерного покрытия в поперечном шлифе; б – распределение микротвердости по толщине упрочненного лазером слоя
Покрытия наносятся на рабочие поверхности окончательно изготовленного изделия (запорного органа, седла и т.п.).
Особый интерес для арматуростроения представляют новые технологии формирования комбинированных покрытий с использованием специальных тонкопленочных и полимерных композиций (ноу-хау фирмы Surfatec). ООО «Агромаш» является эксклюзивным представителем фирмы Surfatec в России.
Основные преимущества комбинированных лазерных эластогидродинамических покрытий:
- нейтральны по отношению к самым агрессивным средам, что обеспечивает высокую коррозионнои износостойкость;
- обладают высокими адгезионными свойствами;
- имеют низкий коэффициент трения, значение которого без смазки соответствует режиму жидкостного трения. Это исключает «залипание» или схватывание поверхностей деталей запирающих устройств, особенно при низкой периодичности срабатывания в положениях открыто–закрыто. При изготовлении устройств без полимерных покрытий длительный силовой контакт уплотнительных поверхностей запорного устройства приводит к развитию фреттинг-износа, потере герметичности и выходу из строя устройства. Покрытие полностью исключает фреттинг-износ контактируемых поверхностей. Низкий коэффициент трения способствует значительному снижению момента трения и усилий в приводных устройствах, что позволяет оптимизировать их габаритные размеры и массу, увеличить срок службы, исключить поломки из-за перегрузок при страгивании сопрягаемых деталей;
- улучшенные характеристики шероховатости поверхности, увеличение площади фактического контакта сопрягаемых деталей (снижаются поверхностные контактные напряжения и нагруженность контактируемых деталей);
- значительное снижение шума и вибрации благодаря демпфирующим свойствам полимерной пленки, разделяющей поверхности трения деталей запорного устройства;
- исключается изнашивание в условиях сухого или граничного трения( в режиме «масляного голодания»).
- возможность применение для защиты резиновых уплотнительных элементов от воздействия различных агрессивных сред, а также в устройствах, где разрешено применение материалов только пищевого исполнения (например, для повышения стойкости против набухания и маслобензостойкости);
- применение для формирования покрытий отечественных материалов.
На рис. 4 приведены некоторые результаты исследований свойств покрытий и примеры, иллюстрирующие состояние деталей с покрытиями после длительных испытаний.
Применение новых лазерных технологий и основанных на них технических решений позволяет значительно повысить конкурентоспособность и эксплуатационные характеристики и технический уровень изделий арматуростроения, обеспечить импортозамещение, снизить затраты на эксплуатацию.