Автор: А. Кобзев (ООО «Фойт Турбо»)
Опубликовано на портале «Химическая техника», сентябрь 2021
Промышленные предприятия, особенно нефтегазовой промышленности и энергетического сектора, являются одними из самых ответственных и опасных производств. Жесткие требования применяемых в этих отраслях стандартов обусловлены в первую очередь критериями безопасности и надежности. В современных условиях к этим требованиям добавляется еще необходимость максимальной экономической выгоды производства.
Ротационное оборудование, в частности насосное, является наиболее критичным с точки зрения как надежности, так и эффективности. Выбор правильного насоса во многом определяет параметры всей технологической установки. Современные насосы должны также обеспечивать высокие показатели при различных режимах работы, когда изменяются не только требования процесса к расходу и напору, но и параметры перекачиваемой среды. Именно для таких целей используется регулирование частоты вращения.
Для примера рассмотрим характеристические кривые центробежного насоса (рис. 1). Основными характеристиками центробежного насоса являются зависимости напора H, КПД η насоса, потребляемой мощности N и кавитационного запаса насоса NPSHr от расхода Q. Насос подбирается таким образом, чтобы рабочая точка лежала как можно ближе к точке максимального КПД (точке 1). Сама же рабочая точка насоса определяется пересечением напорно-расходной характеристики насоса (зависимости H от Q) и характеристической кривой гидравлической системы (см. кривые S1, S2 и S3). При изменении гидравлического сопротивления в системе меняется крутизна характеристической кривой гидравлической системы. Например, при закрытии задвижки на нагнетании ее форма становится более крутой (S2), и насос работает в точке 2 с большим напором и меньшим расходом. Наоборот, при открытии задвижки сопротивление системы падает, и насос работает в точке 3 с большим расходом и меньшим напором. Таким образом, в определенных пределах обеспечивается регулирование параметров насоса.
Однако такой метод регулирования является ненадежным и неэффективным. КПД в точках 2 и 3 значительно ниже КПД в точке 1, а уровень вибрации V – выше. Следует также отметить, что значение кавитационного запаса насоса в точке 3 больше соответствующего значения в исходной точке 1, что необходимо учитывать для обеспечения отсутствия кавитации в насосе. Помимо этого, необходимо проверить, насколько получаемые параметры напора в точках 2 и 3 соответствуют технологическим параметрам – ведь все точки, в которых может работать насос с расчетной подрезкой рабочего колеса и при постоянной частоте вращения, лежат на напорно-расходной характеристике. Другими словами, если по какой-либо причине необходим напор, соответствующий точке 1, и расход, соответствующий точке 2, то регулированием задвижкой достичь такой рабочей точки не получится. В связи с этим данный способ регулирования параметров центробежного насоса – т. н. дроссельное регулирование – рекомендуется применять только в узком диапазоне расхода для маломощных насосов и некритических применений.
Следовательно, для оптимизации работы при изменении характеристики гидравлической системы необходимо также изменять характеристические кривые насоса. Существует два основных способа: изменение подрезки рабочего колеса и изменение частоты вращения (рис. 2). Характеристики насоса при этом изменяются по закону подобия:
Q2/Q1 = d2/d1 = n2/n1; H2/H1 = (d2/d1)2 = (n2/n1)2; N2/N1 = (d2/d1)3 = (n2/n1)3.
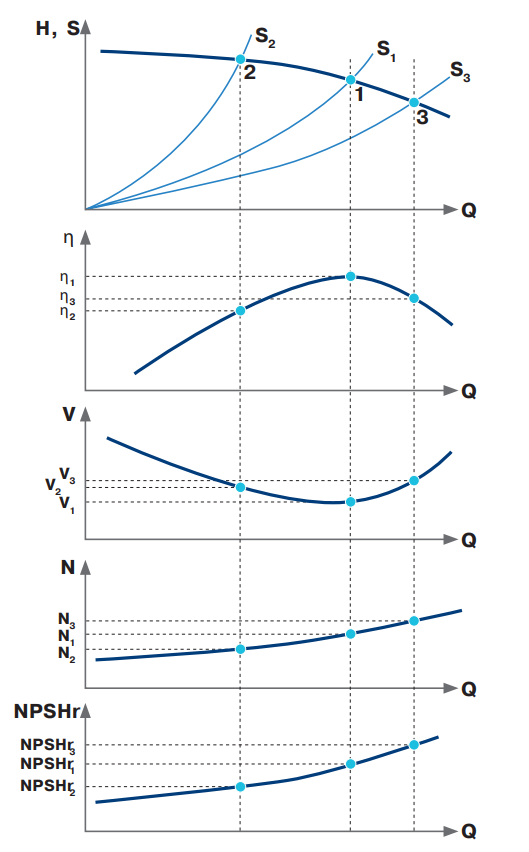
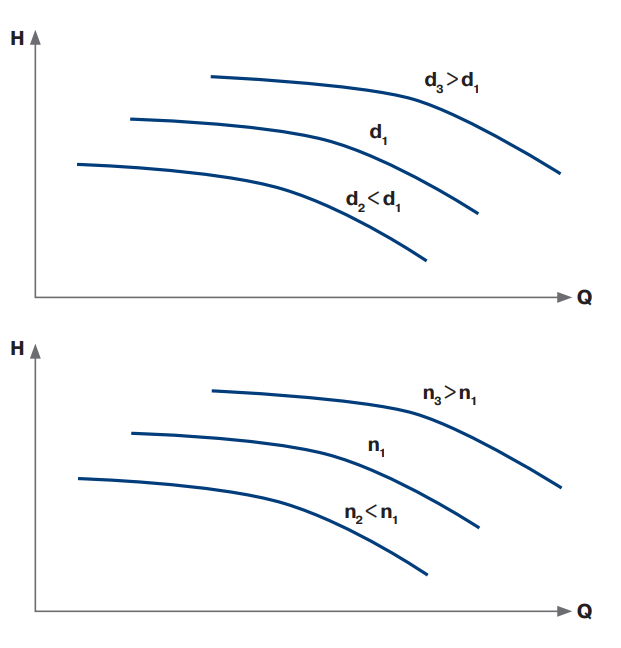
На производстве замена рабочих колес колесами другого диаметра, особенно в многоступенчатых насосах и при часто изменяющихся параметрах, нецелесообразна. Поэтому наиболее эффективный метод регулирования – это регулирование частоты вращения.
Наглядное сравнение, насколько частотное регулирование экономически более эффективно дроссельного регулирования, приведено на рис. 3.
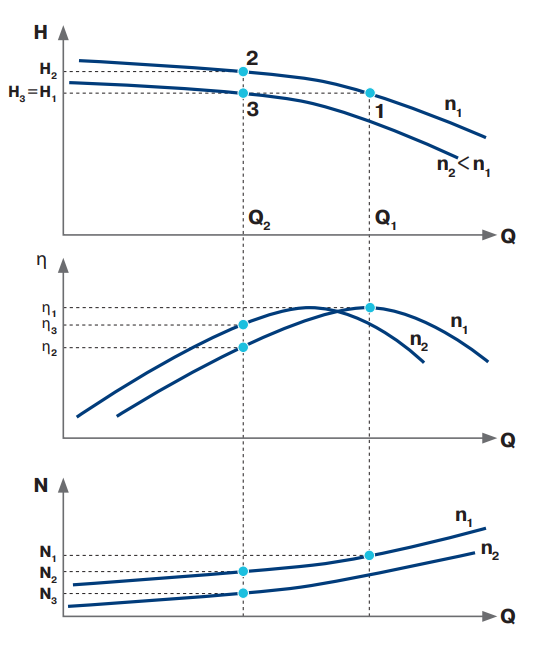
Предположим, что, исходя из технологических параметров, необходимо снизить расход насоса с Q1 до Q2, но не изменять напор. При дроссельном регулировании с помощью задвижки на нагнетании насос будет работать в рабочей точке 2, как описано выше. В этом случае сохранить значение напора физически невозможно, напор в точке 2 будет больше, чем напор в точке 1.
Путем регулирования частоты вращения можно задать практически любую точку в рабочем диапазоне насоса, соответственно Н3 = Н1. Характеристические кривые мощности и КПД, построенные по закону подобия, показывают, что при регулировании частоты вращения удается не только обеспечить требуемые технологические параметры (Q2 и Н3 = Н1), но и повысить КПД и соответственно уменьшить потребляемую мощность насоса, что особенно критично для высокомощных агрегатов.
На примере центробежного насоса с приводом от электродвигателя рассмотрим два основных метода регулирования частоты вращения: применение частотно-регулируемого привода (рис. 4, слева) и гидродинамической муфты (рис. 4, справа).
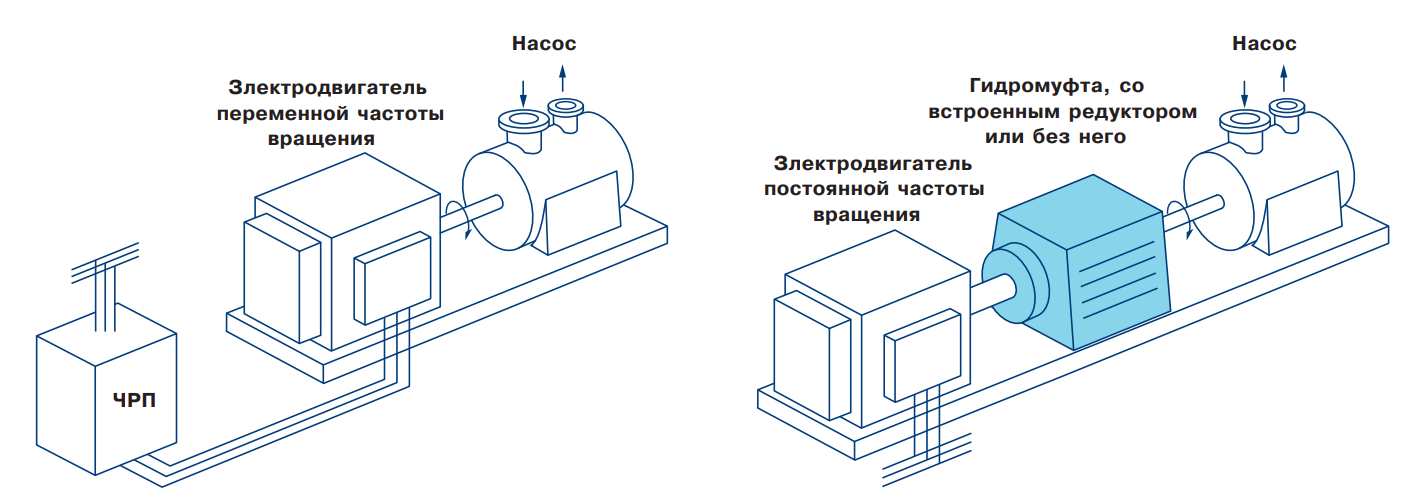
В случае применения частотно-регулируемого привода (ЧРП) непосредственно с его помощью изменяется частота вращения двигателя, с которым посредством жесткого соединения (как правило, с помощью пластинчатой муфты) соединен насос. При применении гидродинамической муфты электродвигатель вращается с постоянной частотой вращения, а регулирование частоты вращения осуществляется непосредственно в гидродинамической муфте. При этом двигатели имеют разное исполнение: двигатель, предназначенный для работы с ЧРП, имеет специальное исполнение с изолированным подшипником и, как правило, больший коэффициент запаса по мощности, в то время как при использовании гидродинамической муфты (существуют также исполнения со встроенным редуктором) применяется стандартный электродвигатель с питанием от электросети.
Принцип передачи крутящего момента посредством циркуляции жидкости между двумя лопастными колесами приведен на рис. 5.
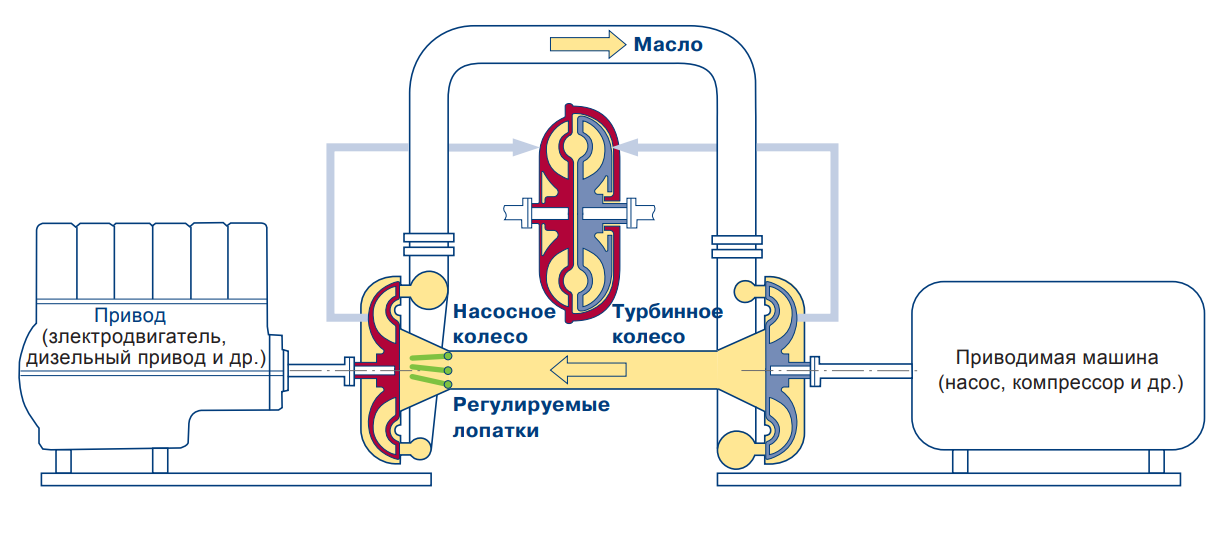
Сама конструкция гидродинамической муфты без использования дополнительных трубопроводов была запатентована немецким инженером Германом Феттингером (1877–1945) в 1905 году, который разместил насосное и турбинное колесо на минимальном расстоянии друг от друга. Механическая энергия от привода преобразуется насосным колесом в энергию потока жидкости (масла), которая впоследствии преобразуется обратно в механическую энергию в турбинном колесе. Частота вращения турбинного колеса может быть изменена за счет изменения количества циркулирующего масла (с помощью черпаковой трубы, такие машины называются черпательными гидромуфтами) либо с помощью регулируемых лопаток (такие машины называются гидротрансформаторами).
Так как нет прямого «металлического» контакта между приводом и приводимой машиной (в качестве среды, передающий крутящий момент, выступает масло), для такого типа передачи крутящего момента износ не характерен.
Конструкция и основные элементы гидромуфты приведены на рис. 6.
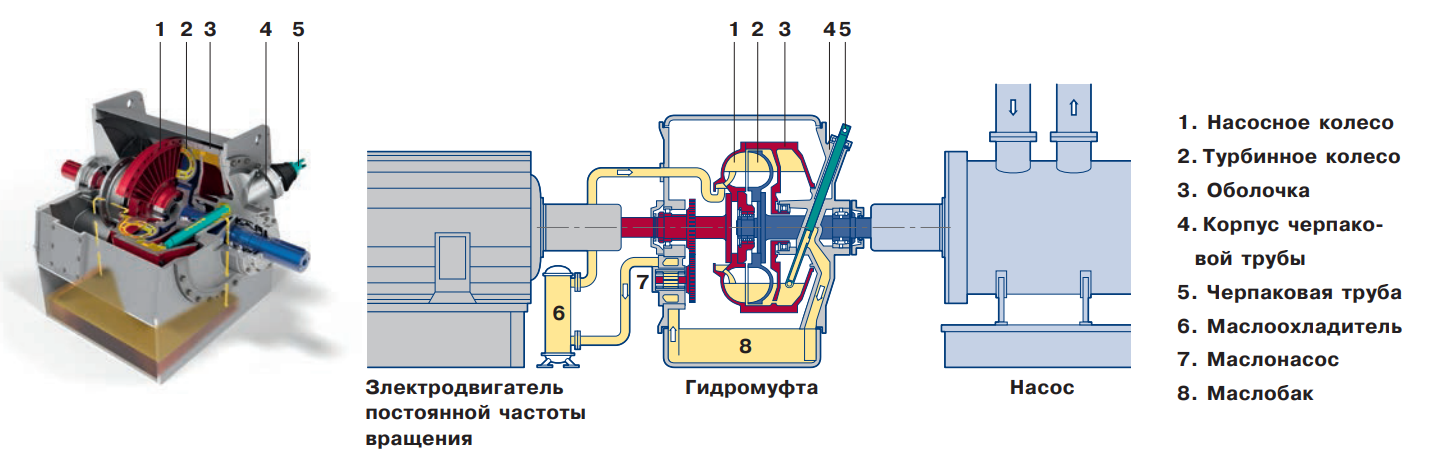
Поток масла циркулирует через маслоохладитель 6 с помощью маслонасоса 7, который приводится от вала привода через зубчатое зацепление. Поток масла подается на насосное колесо, жестко сцепленное с валом привода, где ускоряется и отводится на турбинное колесо, которое в свою очередь жестко скреплено с валом приводимого устройства (насоса). С помощью изменения положения черпаковой трубы 5 изменяется количество масла в рабочей камере (оболочке) и соответственно между лопатками колес гидромуфты. При полностью поднятой черпаковой трубе (см. рабочие характеристики гидромуфты на рис. 7) количество масла в оболочке 4 максимальное, и крутящий момент передается практически полностью (потери на проскальзывание составляют, как правило, около 2 %). При опускании черпаковой трубы количество масла уменьшается и соответственно снижается частота вращения турбинного колеса и приводимой машины. Типовой диапазон регулирования с помощью гидромуфты составляет от 20 до 98 %.
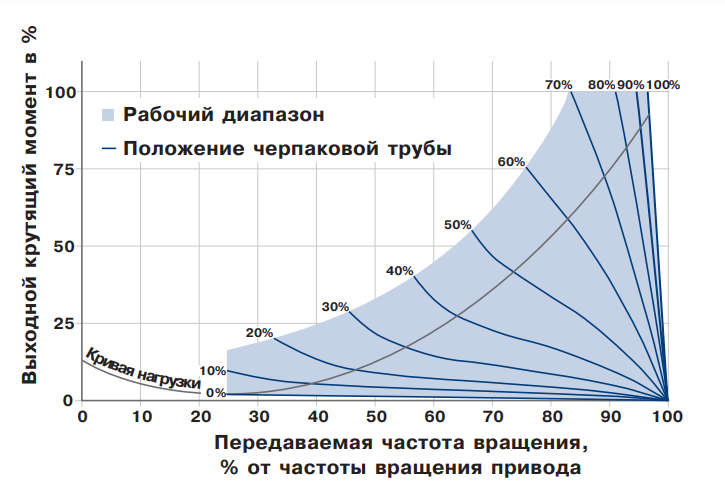
Как упоминалось ранее, регулирование частоты вращения и крутящего момента можно изменять не только с помощью черпаковой трубы, но и с помощью регулируемых лопаток (рис. 8) – на этом принципе построена работа гидротрансформатора. Гидротрансформатор применяется в том числе для электродвигателей с постоянной скоростью (с короткозамкнутым ротором или асинхронных) и дизельных двигателей с ограниченным диапазоном регулирования. Гидротрансформаторы используются в приводах поршневых насосов, винтовых насосов или компрессоров, а также мешалок, смесителей, экструдеров, лебедок. Прекрасно применимы в условиях тяжелого пуска больших роторных масс.
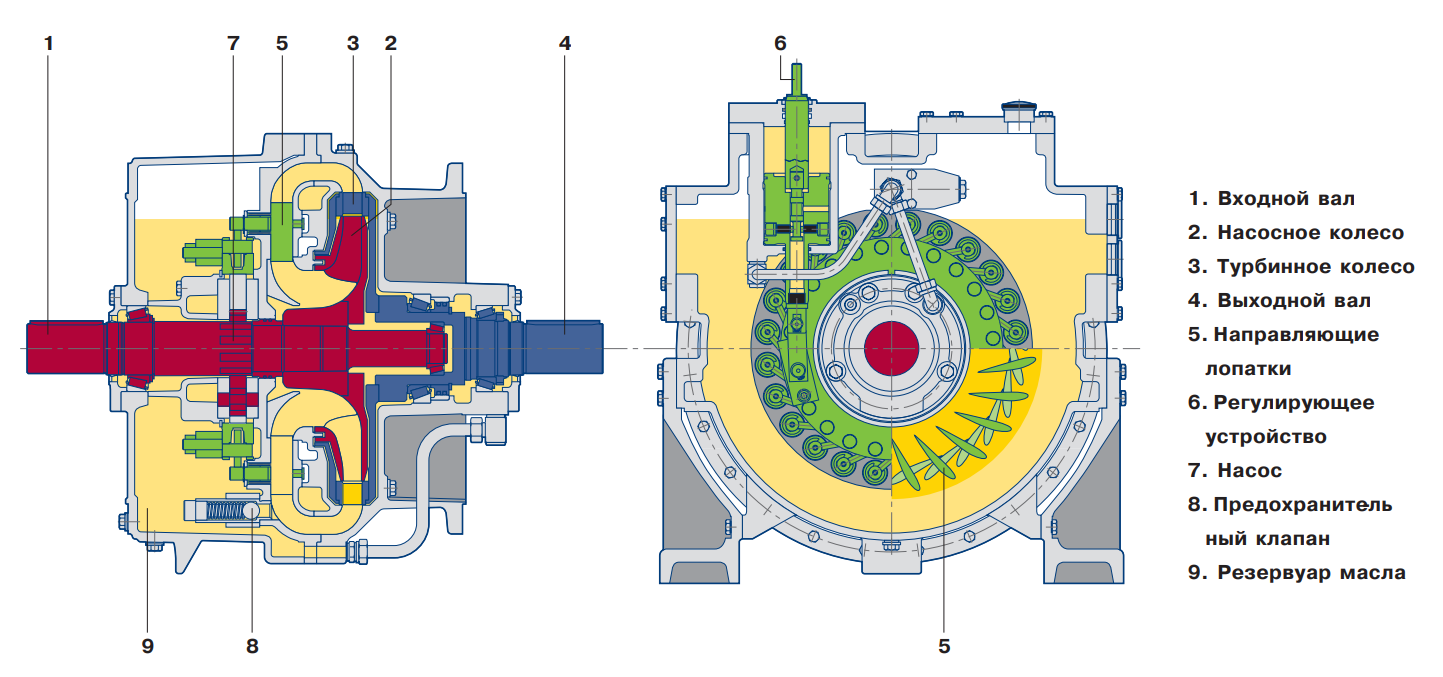
Из принципа работы и приведенных полей характеристик следует, что с помощью гидромуфты и гидротрансформатора невозможно повысить частоту вращения насоса выше частоты вращения привода. Однако, если такое повышение частоты требуются, то используются т.н. регулируемые редукторные передачи (рис. 9), которые по сути представляют из себя комбинацию из гидромуфты или гидротрансформатора и редуктора.
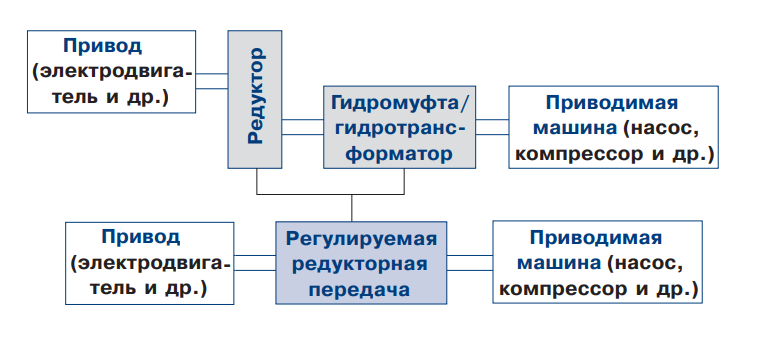
На рис. 10 приведены конструкция и принцип действия такой передачи на примере регулируемой передачи модели RK производства компании Voith – сочетания гидродинамической муфты и цилиндрического редуктора.
Основными компонентами являются цилиндрическая зубчатая передача 1 и регулируемая гидромуфта 2. С помощью электрогидравлического исполнительного органа 4, на который поступает сигнал 4…20 мА, осуществляется регулировка позиции черпаковой трубы 3 и соответственно контроль уровня масла в гидромуфте. Клапан управления циркуляцией масла участвует в регулировании расхода масла и снижает потери. Масло подается из общей емкости 12, а контуры рабочего масла (для гидромуфты) и смазочного масла для подшипников передачи разделены (соответственно предусмотрены маслоохладители 5 и 6), так как расход и температура рабочего масла выше, чем смазочного. Встроенная система смазочного масла может также использоваться для смазки подшипников привода и приводимой машины, что исключает необходимость в дополнительной маслосистеме насосного агрегата.
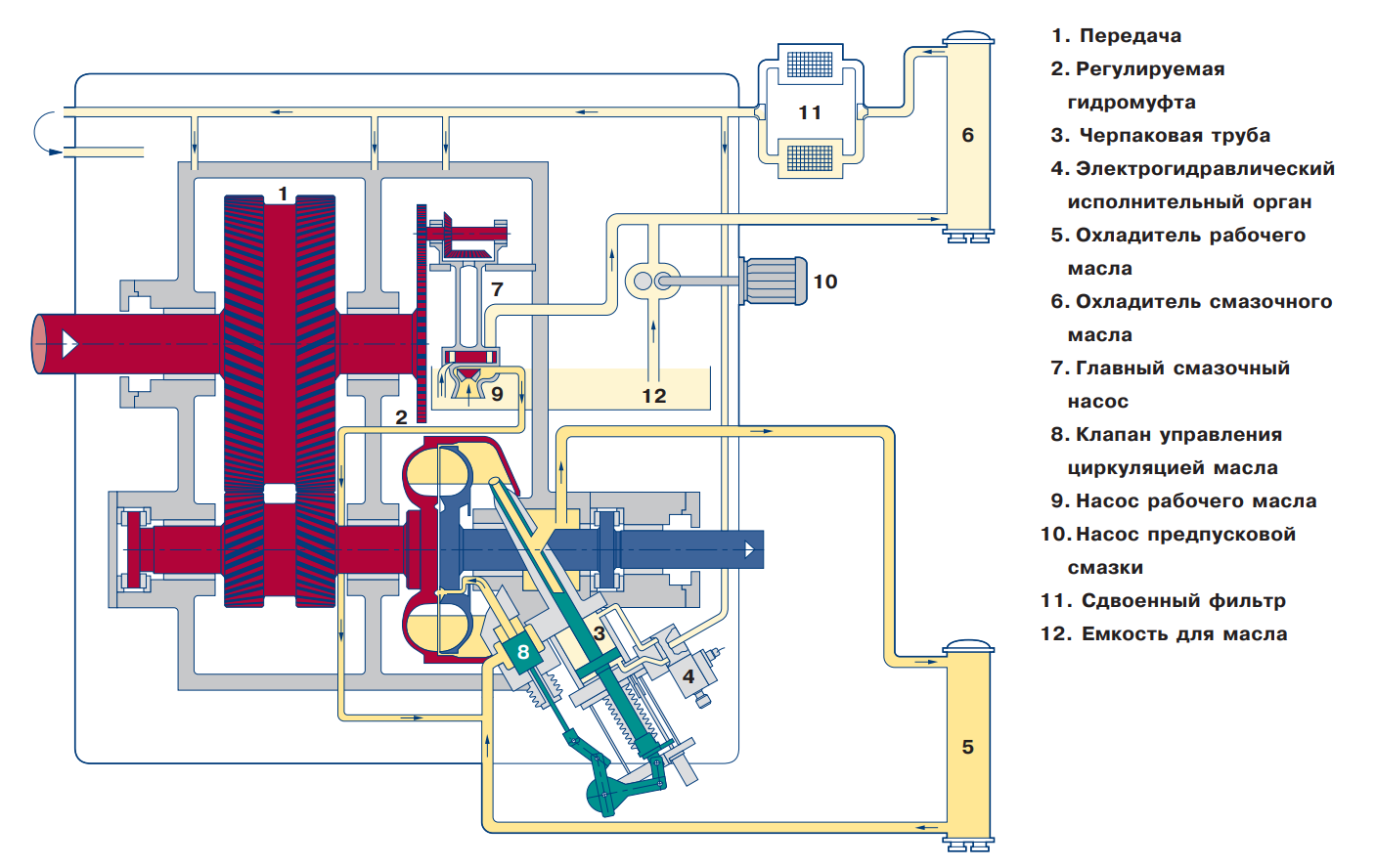
Такие регулируемые редукторные передачи нашли широкое применение в приводе мощных насосов на тепловых и атомных электростанциях (одно из типовых применений – для питательных насосов котла) и в нефтегазовой промышленности (например, для магистральных нефтяных насосов).
Дальнейшим развитием регулируемых редукторных передач стало применение планетарного редуктора и принципа раздельной передачи энергии. Рассмотрим конструкцию и принцип действия (рис. 11).
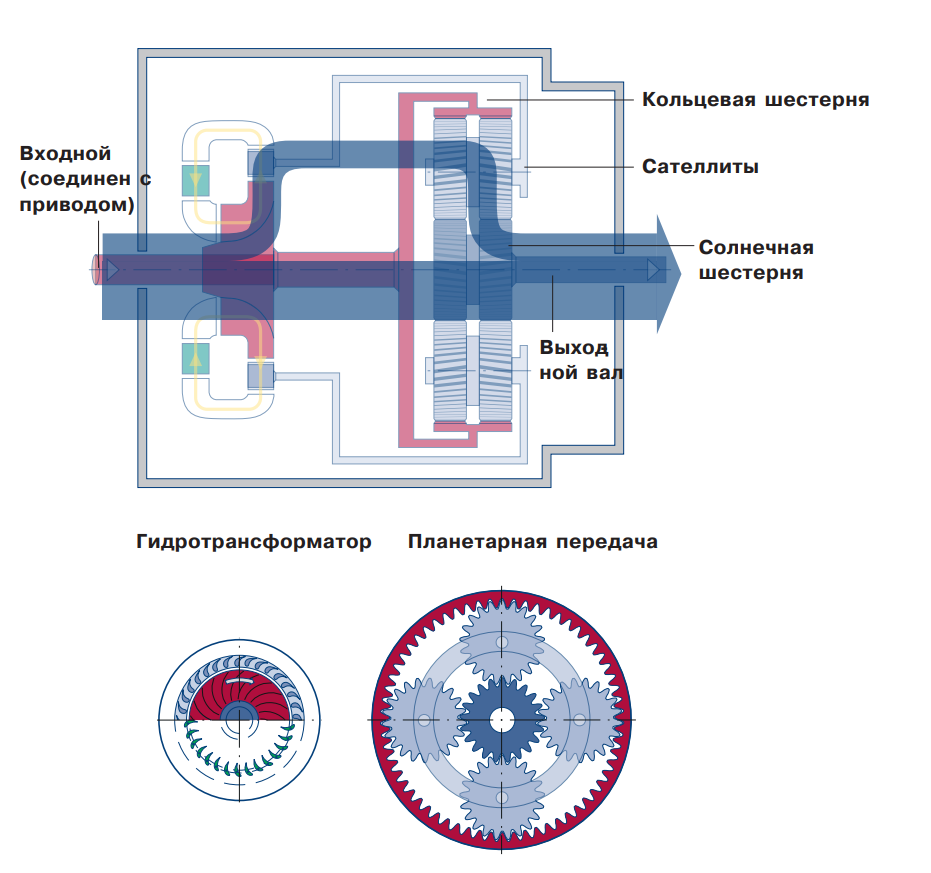
Vorecon состоит из гидротрансформатора и планетарной передачи, которые установлены в одном корпусе. Примерно 75 % мощности передается через планетарный редуктор, а 25 % – через гидротрансформатор. Изменяя положение направляющих лопаток (показаны зеленым цветом), можно регулировать скорость и направление вращения сателлитов и тем самым регулировать частоту вращения солнечной шестерни, которая жестко соединена с выходным валом, соединенным с приводимой машиной (насосом, компрессором и др.). Одним из ярких примеров подобной передачи является модельный ряд Vorecon от компании Voith, который включает как самые сложные машины для высоких мощностей, частот вращения и диапазона регулирования (RW), так и компактные модульные конструкции (VoreconNX, где регулируется частота вращения солнечной шестерни), рис. 12.
В поиске наиболее эффективных и экономичных решений по передаче и регулированию частоты вращения с помощью комбинирования механического и электрического оборудования были созданы приводы с КПД до 96,5 % (рис. 13). Принцип работы такой электромеханической передачи аналогичен принципу работы Vorecon, однако для привода сателлитов используется не гидротрансформатор (максимальный КПД которого достигает 85 %), а регулируемые с помощью ЧРП низковольтные электродвигатели, КПД которых значительно выше (до 98–99 %).
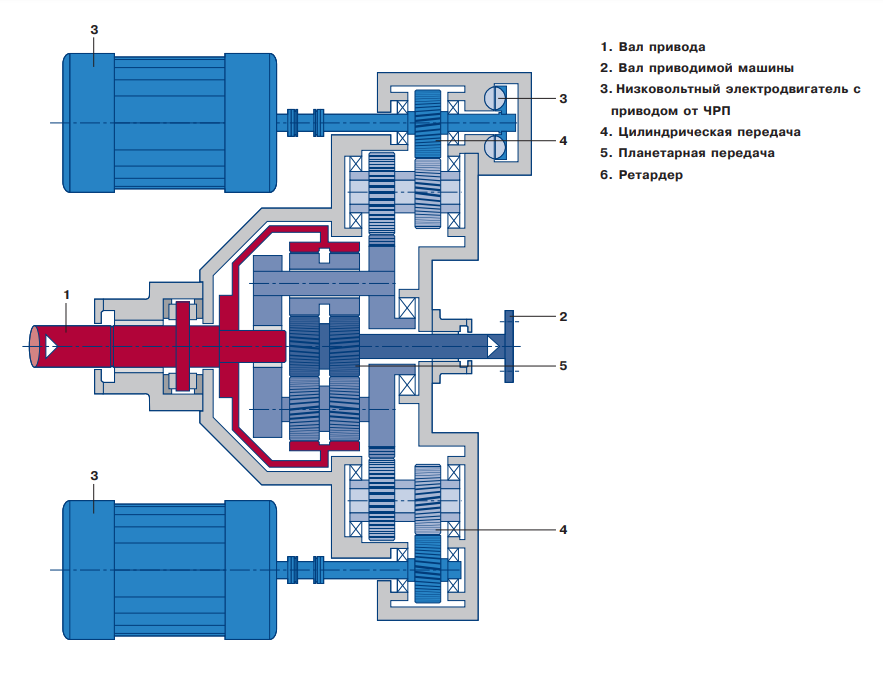
Существует довольно много разных способов регулирования частоты вращения, выбор каждого из них обусловливается конкретными задачами и условиями на производстве. Надежность и долговечность гидродинамических муфт и регулируемых зубчатых передач делает их одним из наиболее привлекательных вариантов для регулирования параметров промышленных насосов.