Автор: Е.И. Тескер (ООО «Агромаш).
Опубликовано в журнале Химическая техника №9/2014
В современных условиях наиболее актуальными являются проблемы, связанные с повышением технического уровня, надежности и эффективности эксплуатации машинного оборудования, продлением его жизненного цикла, увеличения межремонтных пробегов и других эксплуатационных показателей.
Именно эти характеристики определяют конкурентоспособность машиностроительной продукции.
На основе всестороннего анализа технической документации отечественных и зарубежных фирм – производителей насосно-компрессорного оборудования, отзывов с мест эксплуатации и данных о предельных состояниях быстроизнашивающихся базовых деталей и узлов насосно-компрессорного и газотербинного оборудования фирм (Ruhrpumpen, Burghardt, Siemens, Greenfild, Neuman Esser, KSB, Hermetic, Sulzer, ITT, ASCO, LEWA, Siemens KKK, Pollrich, General Electric и др.), можно констатировать следующее:
- уровень конкурентоспособности и условия импортозамещения определяются прежде всего точностью сопряжений, которая у импортного оборудования на 1…2 класса выше по сравнению с общемашиностроительными нормами РФ для аналогичных изделий. Следует отметить, что ужесточение требований к точности сопряжений и качеству рабочих поверхностей импортного оборудования не всегда технически обосновано и чаще всего связано с повышением конкурентоспособности и в какой-то мере защитой от копирования оригинальных изделий. Можно утверждать, что общемашиностроительные стандарты РФ и действующие технические условия на производство отечественных технических объектов во многом устанавливают более обоснованные характеристики качества. Это положение основано на многолетнем опыте работы автора в соответствующих Технических комитетах Госстандарта России и ISO. Кроме того, автор является разработчиком ряда ГОСТов, в том числе и межгосударственных;
- в конструкциях импортного оборудования часто отсутствуют новые оригинальные технические решения на основе ноу-хау. Фирмы практически без изменений много лет выпускают оборудование в одном и том же конструктивном исполнении (например, гиперкомпрессоры фирмы Burghardt);
- в конструкциях импортных машин применяются детали из обычных экономно-легированных конструкционных материалов, но при этом обеспечиваются высокие требования к химическому составу, микроструктуре и физико-механическим свойствам.
- в последние годы в машиностроении наметился прогресс в области применения новых конструкционных материалов и износостойких покрытий, например на основе карбида вольфрама (уплотнения, подшипники, лопатки и т.п.). Ограничения применения покрытий различного назначения обусловлены технологическими трудностями и значительным удорожанием изделий;
- во многих случаях низкое качество имеют детали и узлы, поставляемые как запасные части, для поддержания жизненного цикла оборудования. Эти комплектующие по своим показателям и свойствам существенно хуже оригинальных. Попытка повлиять на поставщиков с целью повышения качества комплектующих была предпринята ООО «Лукойл». Компания разработала новые ТУ на поставку насосных агрегатов, в которых установлены требования к ресурсу, например быстроизнашивающихся деталей, не менее трех лет. Многочисленные поставщики предлагают более низкие гарантийные сроки (12 мес.).
Необходимо отметить, что импортозамещение определяется прежде всего соответствием оригинального технического уровня и эксплуатационных показателей, а также полной взаимозаменяемостью составных частей и комплектующих, что очень важно для разработки технически обоснованных норм поставки по импорту.
В неблагоприятных условиях находятся ремонтные производства, технический уровень которых в большинстве случаев существенно ниже, фирм-производителей.
В большинстве случаев ремонту подвергается оборудование, которое выработало свой проектный ресурс.
Фирма-изготовитель для такого оборудования, как правило, сама уже запасные части не изготавливает, а передает документацию фирмам с более низким уровнем производства. Положение усугубляется тем, что на многих предприятиях достоверный входной контроль запасных частей и комплектующих практически отсутствует. Фирмы не предоставляют конструкторско-технологическую документацию. На ремонтных производствах часто нет необходимых средств измерений и оценки качества.
По указанным причинам эксплуатационные показатели отремонтированного оборудования значительно уступают характеристикам новых изделий.
Необходимо отметить, что увеличение эксплуатационных показателей в послеремонтный период является серьезным резервом для импортозамещения, для снижения себестоимости продукции, экономии средств, материалов, энергии и трудовых затрат, что особенно важно в тех случаях, когда длительность эксплуатации оборудования значительно превышает нормативные и проектные сроки.
Таким образом, для обеспечения необходимых эксплуатационных показателей оборудования (как при изготовлении, так и в послеремонтный период) и реализации концепции импортозамещения требуется разработка новых инновационных импортозамещающих ремонтных технологий, обеспечивающих полное восстановление технических характеристик и работоспособности оборудования.
Одной из важнейших проблем при ремонте насоснокомпрессорного и газоперекачивающего оборудования иностранного производства является отсутствие ремонтной нормативно-технической документации, содержащей сведения, необходимые для нормальной эксплуатации и обеспечения требуемого качества ремонта оборудования. Как правило, иностранные фирмы-производители не предоставляют необходимую документацию, содержащую указания о критериях предельных и допустимых состояний деталей, лимитирующих ресурс машин; сведения о допустимых зазорах в сопряжениях; данные о характеристиках применяемых материалов, покрытий и т. д.
Установлено, что предельные состояния деталей машинного оборудования нефтехимических и газовых производств в процессе длительной эксплуатации чаще всего обусловлены постепенным накоплением в материале детали повреждений, приводящих к зарождению макротрещин и их развитию до критических размеров, а также предельным износом и разрушением трущихся деталей и поверхностей в условиях многофакторного воздействия.
Только достоверные критерии предельных состояний, основанные на закономерностях процессов накопления и развития повреждений при эксплуатации, позволяют прогнозировать остаточный ресурс, предотвращать отказы, правильно планировать ремонтно-обслуживающие мероприятия.
Таким образом, для обеспечения необходимого уровня надежности машинного оборудования требуется системный подход и комплексный подход к созданию инновационных технологий и многофункциональных покрытий, используемых для формирования поверхностных слоев быстроизнашивающихся деталей.
Разработанный нами комплексный подход, реализуемый при разработке новых технологий, включает следующие этапы:
- получение достоверной информации о техническом состоянии оборудования и его составных частей на основе критериев работоспособности, динамики развития повреждений и изнашивания базовых деталей в реальных условиях эксплуатации;
- разработку расчетных методов оценки несущей способности рабочих поверхностей высоконагруженных деталей, от которых зависит ресурс оборудования в целом;
- разработку методов прогнозирования ресурса высоконагруженных деталей на основе механики разрушения в условиях многофакторного воздействия;
- определение требуемых свойств поверхностных слоев деталей, определяющих сопротивляемость разрушению и изнашиванию;
- разработку новых технологий формирования поверхностных слоев, обеспечивающих необходимые эксплуатационные свойства.
Приведем краткую информацию о результатах реализации комплексного подхода при выполнении работ по разработке новых импортозамещающих лазерных технологий, используемых для производственного насосно-компрессорного оборудования дочерних предприятий ОАО «Газпром», ОАО «Каустик», ООО «Ротор», Брянск «Турборемонт» и др.
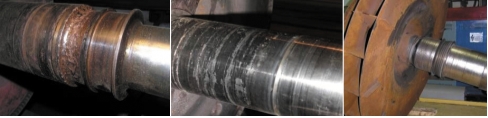
На основании анализа данных о предельных состояниях деталей насосно-компрессорного и газотурбинного оборудования установлены причины выхода из строя деталей, виды повреждений и факторы, влияющие на работоспособность оборудования. В качестве примера рис. 1 показаны детали насосно-компрессорного оборудования иностранного производства после длительной эксплуатации на предприятиях ОАО «Газпром». Основной причиной выхода деталей из строя является интенсивное изнашивание и разрушение поверхностных слоев, работающих в условиях многофакторного воздействия (агрессивная среда, высокие контактные нагрузки, интенсивные процессы трения и изнашивания).
Результаты всесторонних исследований поверхностных повреждений свидетельствуют о том, что применение традиционных методов упрочняющих обработок или нанесение газотермических покрытий не позволяет обеспечить необходимую сопротивляемость разрушению и изнашиванию деталей.
Для повышения надежности и эффективности эксплуатации нефтехимического и газового машинного оборудования был разработан комплекс новых технологий, который включает:
- получение износостойких покрытий лазерной наплавкой с использованием нанокомпозиционных сложнолегированных материалов отечественного производства, многослойных покрытий с эффектом демпфирования (для деталей, работающих в условиях действия высоких нагрузок), жаропрочных и жаростойких покрытий, комбинированных многослойных покрытий;
- технологии лазерной заварки трещин и других дефектов на деталях газотурбинных двигателей;
- применение антифрикционных коррозионно-стойких эластогидродинамических покрытий на основе износостойких полимеров триботехнического назначения;
- лазерную модификацию рабочих поверхностей с целью управления свойствами поверхностных слоев и целенаправленного их формирования для повышения свойств деталей трибосопряжений.
Технологии аттестованы ОАО «Газпром» в установленном порядке и рекомендованы к использованию на ремонтных предприятиях, удостоены премии ООО «Газпром» в области науки и техники.
Примеры реализации технологии приведены на рисунках 2–5.
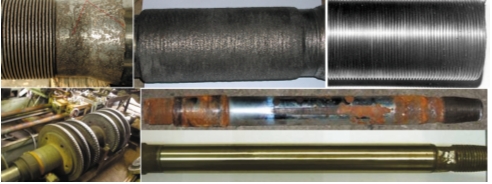
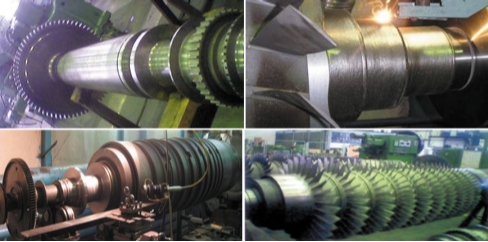
а – роторы ОК и ТВД ГТК – 10И, ОК и ТВД ГТК 10-4;
б – ротор турбины Framatone
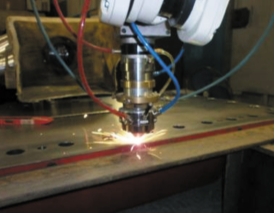
Применение новых технологий позволяет обеспечить высокие физико-механические и адгезионные свойства; отсутствие пористости и дефектов, снижающих свойства поверхностных слоев; высокую трещиностойкость и сопротивляемость ударным, знакопеременным нагрузкам; высокую коррозионную стойкость; износостойкость, в том числе и условиях ограниченной смазки; возможность восстановления номинальных геометрических размеров предельно изношенных деталей и повышение свойств их рабочих поверхностей в зонах концентраторов напряжений (резьба, шпоночные канавки, упорные бурты и т.п.); возможность применения новых принципов конструирования и формирования заданных свойств высоконагруженных деталей с композиционными биметаллическими многофункциональными покрытиями на быстроизнашивающихся участках рабочих поверхностей.
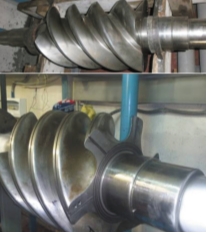
Результаты длительной эксплуатации оборудования различных типов свидетельствуют о существенных преимуществах разработанных технологий. При этом обеспечиваются высокие эксплуатационные показатели не только новых изделий, но и восстановленных предельно изношенных (вышедших из строя) сложных дорогостоящих деталей насосно-компрессорного и газоперекачивающего оборудования.
Стоимость реновации предельно изношенных деталей, узлов и агрегатов не превышает 30 % стоимости новых изделий при гарантии работоспособности на уровне новых изделий. Процесс реновации реализуется на роботизированном лазерном комплексе с применением отечественных материалов.
Основная часть номенклатуры восстановленного оборудования приведена в таблице.
Оборудование | Производитель |
ГТК-10И (OK и ТВД ТНД) | Nuovo Pignone (Италия); General Electric (США) |
ЦБН PCL | Nuovo Pignone (Италия) |
Нагнетатели CDP | Ingersol Rend (США) |
Паровые турбины 6РЗ | Creaseau Loire (Франция) |
Газодувки ROTUNI-130 | Neu (Франция) |
Центробежные компрессоры RD7B | Framatome (Франция); John Crane |
Поршневые компрессоры | Creaseau Loire |
Технологические насосы | Wortington (Германия) |
Плунжерные насосы | Clextral, Brann und Lubbe, (Италия, Германия) |
Пневмоприводы | Cameroon, Malbranuue, (Германия) |
Центробежные насосы | Ruhrpumpen |
Компрессор первого/второго каскада | Burghardt |
Паровые турбины | Siemens |
Поршневые компрессоры | Greenfild |
Поршневые компрессоры | Neuman Esser |
Центробежные насосы | KSB, Hermetic, Sulzer |
Шестеренчатые насосы | ASCO |
Турбокомпрессор | Siemens |
Турбина насоса питательной воды | Siemens KKK |
Экономический эффект от внедрения новых технологий только при ремонте оборудования ООО «Газпром Трансгаз Волгоград» превысил 500 млн. руб. При этом полностью обеспечивается импортозамещение.
Ресурс некоторых базовых деталей в послеремонтный период увеличился в 5–8 раз и более.
По нашему мнению, расширение применения новых технологий позволят решить сложные проблемы импортозамещения и повышения эксплуатационных показателей машинного оборудования.