Автор: М.У. Рабаев (Филиал ПАО АНК «Башнефть» «Башнефть-Уфанефтехим»).
Опубликовано в журнале Химическая техника №8/2016
Оборудование нефтеперерабатывающих и нефтехимических предприятий является чрезвычайно опасным, работающим в крайне тяжелых условиях. При этом главной проблемой отечественной нефтеперерабатывающей отрасли является морально устаревшее оборудование.
Несмотря на это, своевременная и качественная ревизия и ремонт оборудования позволяют продлить срок его безопасной службы. Однако известные сегодня методы ревизии не всегда позволяют обнаружить скрытые от глаз локальные дефекты (язвенная коррозия, раковины, неравномерное изнашивание поверхности и т.д.) технологических трубопроводов. Это связано с особенностями проведения ревизии оборудования такого вида: следуя действующей нормативно технической документации, необходимо проводить наружные осмотры, ультразвуковую толщинометрию и гидравлические испытания, но не один из этих методов ревизии не отражает картину состояния внутренней поверхности трубы.
С целью повышения оперативной готовности оборудования было решено использовать метод радиографической профильной толщинометрии.
Радиография – это метод получения на рентгеновской пленке или экране изображения предмета, просвечиваемого проникающим излучением. Он основан на способности проникающего излучения проходить через непрозрачные предметы, в том числе через металлы, и действовать на рентгеновскую пленку и некоторые вещества, благодаря чему последние флуоресцируют (светятся).
Гамма-лучи через стенку трубы между внешним и внутренним радиусом трубы должны пройти сквозь слой металла в ~4 раза толще стенки трубы. Большинство лучей поглощаются металлом, оставляя на пленке неэкспонируемый участок. Этот участок (более светлый на затемненной пленке) отображает несколько увеличенную проецируемую площадь стенки трубы. При этом дефекты, встречающиеся в теле трубопровода и чаще всего имеющие характер пустот, на рентгеновской пленке имеют вид пятен (раковины, язвы) или полос.
Применяемая нами методика имеет название профилометрия (англ. profilometry) – процесс измерения («снятия») профиля сечения поверхности в плоскости, перпендикулярной к ней и ориентированной в заданном направлении, различными видами проникающей радиации.
К основным положительным сторонам данного метода неразрушающего контроля можно отнести следующие [1]:
- отсутствие необходимости в демонтаже трубной изоляции;
- долговечное сохранение на пленке визуальной информации о состоянии трубопровода;
- более достоверное обнаружение язвенной коррозии (и других видов неравномерной коррозии) в отличие от ультразвуковой толщинометрии;
- обеспечение обзора большого участка трубопровода;
- возможность наблюдения над положением внутренних частей арматуры (опущенные заслонки задвижки и т.п.);
- легкое перемещение радиографического оборудования по НПЗ или химическому производству;
- отсутствие источников воспламенения углеводородов.
Профилометрия также полезна для определения внешней коррозии небольших соединений под изоляцией, таких как дренажные трубопроводы, бобышки и соединения с манометрами, так как сложность обеспечения хорошего уплотнения в изоляции делает такие места особенно восприимчивыми к внешней коррозии под изоляцией.
Основными составляющими при проведении радиационного контроля являются объект контроля; источник излучения (рентгеновский аппарат или источник гаммаизлучения); детектор (пленка, запоминающая пластина, цифровая панель); время экспозиции (время воздействия источника на детектор). При этом каждая составляющая контроля напрямую влияет на результат проведения контроля. Схема контроля представлена на рис. 1.
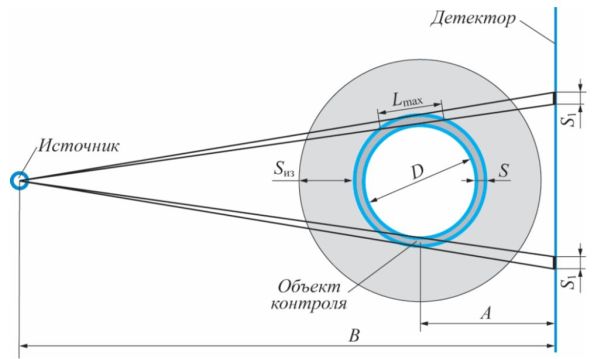
D – диаметр трубопровода; S – фактическая толщина;
Lmax – радиографическая толщина; S1 – замеренная толщина;
Sиз – толщина изоляции
При использовании радиографического метода определение остаточной толщины трубопровода происходит путем простого математического расчета – пропорцией, исходя из размеров изображения, полученного на пленке. При этом нет необходимости останавливать технологический процесс. Однако существует ограничения использования данной методики как со стороны контролирующей техники, так и со стороны объектов контроля. Например, результаты проведенных испытаний показывают, что идеальными условиями для контроля толщины источником рентгеновского излучения является трубопровод диаметром условного прохода менее 110 мм и толщиной менее 6 мм. А в случае контроля источником гамма-излучения (иридий-192) – трубопровод диаметром условного прохода менее 220 мм и толщиной 10 мм. В обоих случаях среда должна быть однородной, состоящей из низкокипящих компонентов или газов, толщина изоляции при этом не должна превышать 100 мм.

Далее приведены результаты работ, включенных в состав технического задания по выполнению экспертизы промышленной безопасности. На образце П-33 (рис. 2) выявлено локальное утонение в околошовной зоне галтерной врезки трубопровода диаметром 57 мм в трубопровод диаметром 159 мм. При исполнительной толщине стенки 5 мм трубы диаметром 57 мм остаточная толщина равна 1,25 мм.
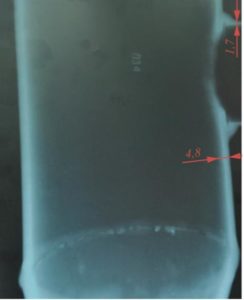
При анализе снимка П-34 (рис. 3) обнаружен аналогичный локальный дефект в виде утонения. Остаточная толщина стенки трубы равна 1,7 мм при исполнительной толщине 5 мм. Дополнительно выявлено нарушение норм стыковки трубопроводов диаметром 159 мм и 57 мм при выполнении галтерной врезки, а также дефекты шва приварки перехода 159/89 мм к трубе диаметром 159 мм.
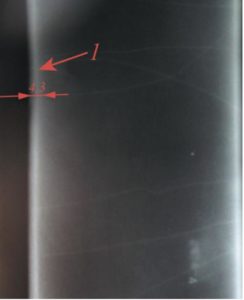
На рис. 4 показан трубопровод диаметром 159 мм; стрелкой 1 указан участок локального коррозионного износа, при этом дефект является наружным, скрытым под изоляцией. Наименьшая расчетная толщина на дефектном участке – 4,3 мм при исполнительной толщине 8 мм.
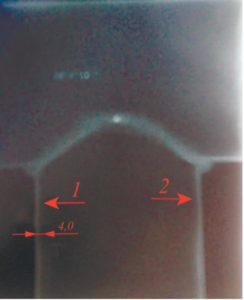
Показанный на рис. 5 участок трубопровода имеет две зоны локального утонения 1 и 2. При исполнительной толщине трубопровода 8 мм наименьшая расчетная толщина равна 4 мм. Светлая точка в центре сварного шва – это саморез, применяющийся при установке изоляционного покрытия на трубопроводе.
Класс эффективности обследования | Объем проведения инспектирования | Метод толщинометрии | Положительные качества обследования | Отрицательные качества обследования |
Класс С – типичное обследование | Измерения толщины проведены на 10% компонента | Контроль методом ультразвуковой толщинометрии | – | Изоляция удалена с отступлением от требований
локальных нормативных документов |
Класс В – среднее обследование | Измерения толщины проведены на 50% компонента | Контроль методом ультразвуковой толщинометрии | Изоляция удалена согласно требованиям локальных нормативных документов.
Проведение визуального и измерительного контроля наружного состояния трубопровода |
Увеличение времени инспектирования |
Класс А – высокоэффективное обследование | Измерения толщины проведены на 100% компонента | Контроль методом ультразвуковой толщинометрии | Изоляция удалена сверх требований локальных нормативных документов.
Проведение визуального и измерительного контроля наружного состояния трубопровода |
Увеличение времени инспектирования. Дополнительные затраты
на восстановление изоляции |
Контроль методом гаммаграфической профилометрии | Нет необходимости удалять изоляцию.
Долговечная визуальная запись состояния трубопровода |
– |
В мировой практике профилометрия получила большое распространение и используется наряду с традиционным ультразвуковым контролем толщины. При этом на европейских нефтеперерабатывающих комплексах при подготовке к капитальным ремонтам обрабатываются тысячи снимков профилей трубопроводов. Полученные при этом достоверные данные о состоянии технических устройств подразумевают более качественное проведение ремонтов и, как следствие, меньший риск возникновения нештатных ситуации.
Данный метод контроля толщины является предпочтительным и наиболее эффективным при проведении инспектировании с учетом факторов риска (RBI). Например, программный продукт PCMS, разработанный MISTRAS
Group, выделяет три класса эффективности инспектирования, показанные в таблице [2].
Количественная оценка риска возникновения отказа технического устройства зависит от эффективности обследования. Из рис. 6 можно видеть, что чем выше качество инспектирования, тем ниже вероятность возникновения отказа технического устройства [2].
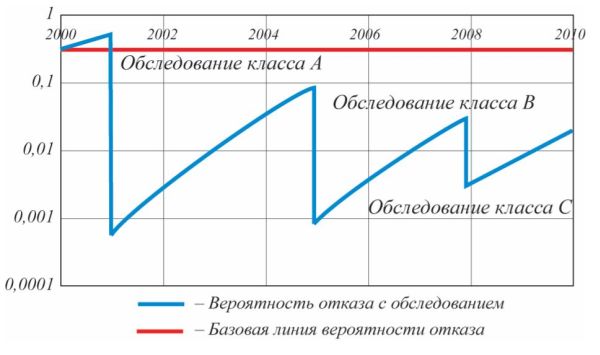
Применение метода позволяет значительно сократить затраты на изоляционные работы, провести ревизию не только «холодных» трубопроводов, но и «горячих», подразумевает больший объем подготовительных работ перед капитальным ремонтом, что позволит заранее предсказывать число отбракованных элементов трубопроводов. Более того, применение радиографической профилометрии повышает эффективность обследования, и, как следствие, выявляемость локальных дефектов элементов трубопроводов, уменьшая при этом риск возникновения отказа технических устройств в межремонтный пробег и увеличивая их операционную готовность, что, безусловно, имеет весомый положительный экономический эффект.
Список литературы
- Рекомендации по инспектированию компонентов системы трубопроводов API RP 574. Американский нефтяной институт. Второе издание, июнь 1998 г.
- Техническое руководство по RBI. MISTRAS Group. Июль 2014 г.