Авторы: Ф.С. Советин, Т.Н. Гартман, В.Д. Сафонова, О.П. Шумакова, И.И. Тамбовцев (РХТУ им. Д.И. Менделеева).
Опубликовано в журнале Химическая техника №10/2014
Хлорирование ароматических углеводородов – один из важнейших методов синтеза их галогенопроизводных, являющихся важной группой промежуточных продуктов [1]. Хлорбензол является важным органическим растворителем. Кроме того, хлорбензол применяется в органическом синтезе (например, в производстве 1,1,1-трихлор,2,2-ди(п-хлорфенил)этана, так называемого ДДТ), а также в производстве фенола [1, 2].
Непрерывные технологические линии синтеза хлорбензола из бензола являются крупнотоннажными, а также энергои ресурсоемкими, поэтому даже незначительное снижение потребления энергии и ресурсов может обеспечить существенный экономический эффект.
Решение задачи энергои ресурсосбережения указанных технологических линий не представляется возможным без использования современных комплексов программ (так называемых симуляторов химических производств), позволяющих создавать «виртуальные» химико-технологические системы (ХТС) [3–5].
Использованию комплекса программ CHEMCAD для моделирования производств тонкого органического синтеза посвящены работы [6–8]. Математическая модель процесса непрерывного хлорирования бензола по Беркману с использованием интегрального метода расчета ХТС рассмотрена в работе [9]. Моделированию процесса хлорирования бензола до п-дихлорбензола посвящена работа [10]. Однако требуется дополнительно рассмотреть вопрос построения блочной компьютерной модели непрерывной технологической схемы хлорирования бензола по Беркману с применением комплекса программ CHEMCAD.
В данной статье предложено решение задачи разработки блочной компьютерной модели технологической линии непрерывного хлорирования бензола по Беркману с использованием декомпозиционного метода расчета ХТС и комплекса программ CHEMCAD.
Описание технологической схемы процесса непрерывного хлорирования бензола по Беркману
Описание технологической схемы заимствовано из работ [1–2]. Блоксхема блочной компьютерной модели рассматриваемой технологической схемы изображена на рис. 1.
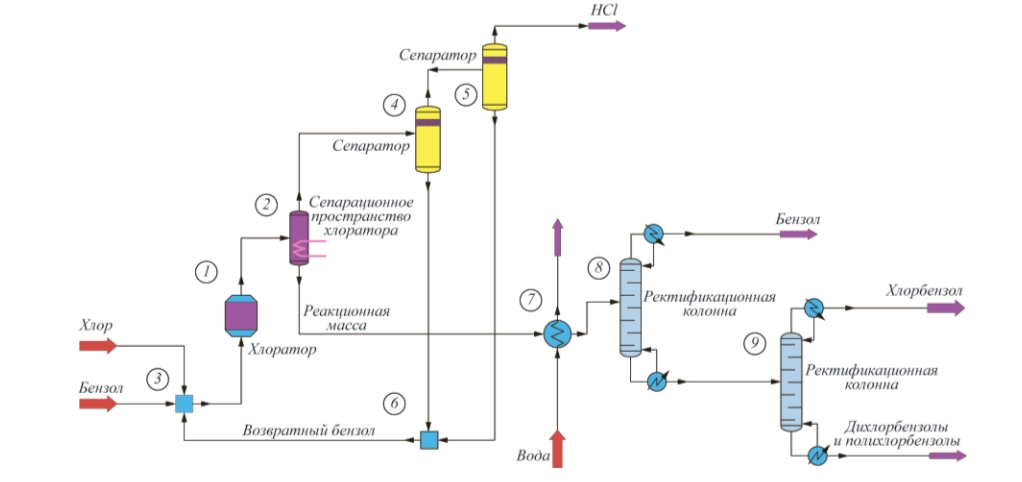
7 – расчетный модуль теплообменника, 8, 9 – расчетные модули ректификационных колонн
Хлорирование бензола проводят в хлораторе (модуль 1), представляющем собой трубку, заполненную перемешанными стальными и керамическими кольцами. В верхней части аппарата имеется сепарационный объем (модуль 2). Бензол и хлор подают прямотоком снизу в реактор, где протекают следующие основные реакции:
Данные реакции являются каталитическими. Катализатор – FeCl3, который образуется при взаимодействии хлора и железа. Процесс проводится при кипении реакционной массы. Для нормального режима работы в хлораторе должен поддерживаться такой гидродинамический режим, при котором продукты реакции не могли бы возвращаться в зону реакции. В зависимости от требуемого состава реакционной массы в производственных реакторах поддерживают температуру 75…95°С.
Для уменьшения количества образования дихлорбензолов и полихлорбензолов (по отношению к хлорбензолу), хлорирование ведут при 76…83°С. Из реактора непрерывно выводится реакционная масса, содержащая бензол, хлорбензол, дихлорбензолы, полихлорбензолы и хлороводород.
Весь испарившийся и уходящий из хлоратора бензол необходимо улавливать и возвращать в процесс.
Для этого смесь паров из реактора поступает в два последовательно соединенных сепаратора (модули 4, 5).
Сконденсировавшийся бензол собирается в сборнике (модуль 6), откуда подается на хлорирование.
Реакционную массу разделяют на бензол, хлорбензол, дихлорбензолы, а также полихлорбензолы путем непрерывной двухступенчатой ректификации. В первой колонне (модуль 8) отделяют бензол от смеси хлорбензола, дихлорбензолов и полихлорбензолов. Во второй колонне (рис. 1, модуль 9) отделяют хлорбензол от дихлорбензолов и полихлорбензолов.
Описание хода моделирования технологической схемы процесса непрерывного хлорирования бензола по Беркману
Хлоратор моделируется модулем равновесного реактора (модуль 1).
На основе анализа экспериментальных данных о функционировании данной технологической линии установлено, что в реакторе протекают две основные реакции – (1) и (2).
Указаны стехиометрические данные реакций (1) и (2). Степень конверсии базового реагента (бензол) в реакции (1) – 0,31, в реакции (2) – 0,01.
Температура 80°С, давление 0,18 МПа. Сепарационное пространство хлоратора моделируется модулем сепаратора компонентов (модуль 2), при этом заданы: температура 80°С и доли компонентов в паровом потоке (бензол – 0,77, хлороводород –1) – потоке в сепараторы 4, 8.
Результаты расчета хлоратора приведены в табл. 1. В этой же таблице приведено сравнение результатов расчета реактора с экспериментальными данными, заимствованными из работ [1–2].
Сепараторы для отделения хлороводорода от бензола (модули 4, 5) моделируются модулями фазовых сепараторов [11]. Заданы давления и температуры в сепараторах. Для сепаратора 4: температура 5°С, давление 0,1 МПа. Для сепаратора 5: температура –10°С, давление 0,1 МПа.
Колонна выделения бензола из реакционной массы (модуль 8) моделируется модулем строгого расчета ректификации TOWR с использованием алгоритма Inside/Out [12–13].
Число тарелок – 20, № тарелки питания – 12, массовый расход дистиллята – 15 615 кг/ч, паровое число – 3.
Диаметр колонны – 2,9 м. Результаты расчета колонны приведены в табл. 2.
Таблица 1
Сравнение результатов расчетов хлоратора с экспериментальными данными
Показатель | На входе | На выходе | |||
Парожидкос тной поток (входной поток
в реактор) |
Паровой поток (поток в сепараторы 4 и 5) | Жидкий поток (поток в колонны 8, 9) | |||
Расчет | Расчет | Расчет | Экспери- мент [1, 2] | ||
Давление, МПа | 0,2 | 0,18 | 0,18 | – | |
Температура,°С | 25 | 80 | 80 | 80 | |
Массовый расход, т/ч | 130,52 | 68,43 | 62,09 | – | |
Массовая доля компонента, % мас. |
Бензол | 77 | 76,53 | 25,15 | 29,99 |
Хлорбензол | 0 | 0 | 71,83 | 68 | |
Дихлорбензолы | 0 | 0 | 3,03 | 2 | |
Хлороводород | 0 | 23,47 | 0 | 0,01 | |
Хлор | 23 | 0 | 0 | 0 |
Колонна выделения хлорбензола от смеси (модуль 9) моделируется модулем строгого расчета ректификации TOWR с использованием алгоритма Inside/Out. Число тарелок – 20, № тарелки питания – 10, массовый расход кубового остатка – 1 842 кг/ч, флегмовое число – 3. Диаметр колонны – 3,66 м. Результаты расчета колонны приведены в табл. 3.
Таблица 2
Результаты расчета колонны выделения бензола из реакционной массы
Показатель | На входе | На выходе | ||
Дистиллят | Кубовый остаток | |||
Давление, МПа | 0,18 | 0,16 | 0,15 | |
Температура,°С | 50 | 94 | 148 | |
Массовый расход, т/ч | 62,09 | 15,61 | 46,48 | |
Массовая доля компонента, % мас. |
Бензол | 25,15 | 100 | 0 |
Хлорбензол | 71,83 | 0 | 95,96 | |
Дихлорбензолы | 3,03 | 0 | 4,04 | |
Хлороводород | 0 | 0 | 0 | |
Хлор | 0 | 0 | 0 |
Таблица 3
Результаты расчета колонны выделения хлорбензола
Показатель | На входе | На выходе | ||
Дистиллят |
Кубовый остаток | |||
Давление, МПа | 0,15 | 0,13 | 0,14 | |
Температура,°С | 148 | 147 | 193 | |
Массовый расход, т/ч | 46,48 | 44,64 | 1,84 | |
Массовая доля компонента, % мас. |
Бензол | 0 | 0 | 0 |
Хлорбензол | 95,96 | 100 | 0 | |
Дихлорбензолы | 4,04 | 0 | 100 | |
Хлороводород | 0 | 0 | 0 | |
Хлор | 0 | 0 | 0 |
При расчете технологического узла непрерывного хлорирования бензола по Беркману в целом для обеспечения сходимости рецикла использовался метод простых итераций. Также было использовано методическое обеспечение блочного компьютерного моделирования энергои ресурсоемких ХТС [14].
Для сепараторов 4, 5 проведен анализ влияния температуры и давления на массовую долю бензола в жидких выходных потоках. Также исследовано влияние парового числа на массовую долю бензола в выходном потоке дистиллята для колонны 8. Результаты проведенных анализов приведены на рис. 2–6.
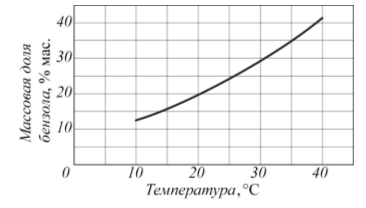
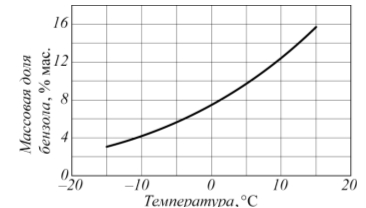
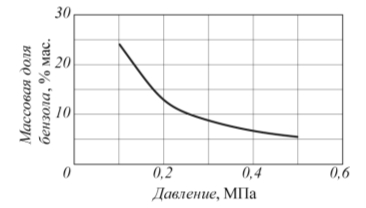
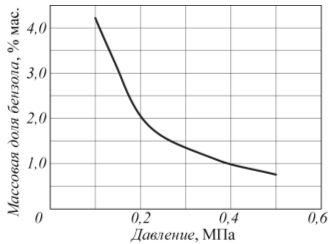
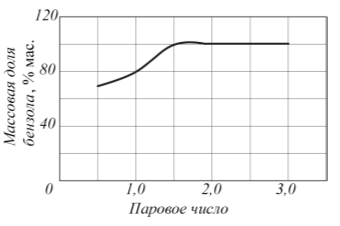
в колонне 8
Таким образом, разработана компьютерная модель крупнотоннажной технологической схемы процесса непрерывного хлорирования бензола по Беркману. Эта модель применима, как для оптимизации работы отдельных аппаратов, так и для оптимизации работы ХТС в целом. Посредством разработанной компьютерной модели возможно проведение реконструкции данной технологической линии. Модель пригодна при решении задач ресурсосбережения промышленных производств.
Изучены влияния температуры и давления в каждом сепараторе для разделения парожидкостных смесей на массовую долю бензола в жидком выходном потоке, а также проведен анализ влияния парового числа на содержание бензола в дистилляте для колонны выделения бензола.
Список литературы:
- Лисицын В.Н. Химия и технология промежуточных продуктов. М: Химия, 1987 г.
- Орехов В.С., Дьячкова Т.П., Субочева М.Ю., Колмакова М.А.Технология органических полупродуктов. Тамбов: ТГТУ, 2007. Ч. 1.
- Гартман Т.Н., Советин Ф.С., Лосев В.А. Современный подход к модернизации химических производств на основе применения пакетов моделирующих программ//Химическая техника. №12.
- Гартман Т.Н., Клушин Д.В. Основы компьютерного моделирования химикотехнологических процессов. М: «Академкнига», 2008.
- Гартман Т.Н., Советин Ф.С. Аналитический обзор современных пакетов моделирующих программ для компьютерного моделирования химико-технологических систем//Успехи в химии и химической технологии. 2012. Т. 26. №11 (140).
- Советин Ф.С. Гартман Т.Н. Применение комплекса программ CHEMCAD для разработки компьютерной модели технологического узла нитрования крупнотоннажного производства нитробензола//Химическая техника. №4. 2012.
- Щеглова А.А. Реконструкция технологического узла нитрования крупнотоннажного производства нитробензола//Успехи в химии и химической технологии. 2012. Т. 26. №11 (140). С. 127-132.
- Мешкова А.А., Советин Ф.С., Гартман Т.Н., Проскуров Е.А., Сафонова В.Д. Разработка компьютерной модели технологического узла получения анилина из нитробензола с применением комплекса программ CHEMCAD//Химическая техника. №7. 2014.
- Перевалов В.П., Колдобский Г.И. Основы проектирования и оборудование производств тонкого органического синтеза. М. 1997.
- Алферова Е.А. Селективное хлорирование бензола до парадихлорбензола. Дис…. канд. хим. наук. М.: РХТУ им. Д.И. Менделеева. 2011.
- Проектирование и расчет аппаратов основного органического и нефтехимического синтеза. Под. ред. Лебедева Н.Н. М.: «Химия», 1995.
- Голованов М.Л. Разработка энергосберегающей технологии ректификации продуктов каталитического крекинга. Дис. … канд. техн. наук. М.: МГАТХТ (МИТХТ) 2007.
- Комиссаров Ю.А, Гордеев Л.С, Вент Д.П. Научные основы процессов ректификации. Под ред. Серафимова Л.А. В 2 томах. М.: Химия, 2004.
- Советин Ф.С. Разработка и применение методического обеспечения блочного компьютерного моделирования энергоресурсоемких химико-технологических систем c применением инструментальных комплексов программ. Дис. … канд. техн.наук. М.: РХТУ им. Д.И. Менделеева. 2011.