Авторы: С.Н. Скуридин, А.В. Сарыгин (АО «ННК-Хабаровский НПЗ»), В.Н. Костюков, А.В. Костюков, Е.В. Тарасов (НПЦ «Динамика»).
Опубликовано в журнале Химическая техника №10/2015
Технологический процесс нефтеперерабатывающего предприятия обеспечивает выпуск готовой продукции в плановых объемах и надлежащего качества. В технологическом цикле используются десятки тысяч единиц динамического оборудования, и для надежной безаварийной эксплуатации производственного процесса необходим контроль технического состояния находящегося в эксплуатации динамического оборудования в режиме реального времени, т.е. надо обеспечить мониторинг технического состояния и автоматическую диагностику.
Мониторинг технического состояния агрегатов – наблюдение за процессом изменения его работоспособности с целью предупреждения персонала о достижении предельного состояния. Мониторинг позволяет перевести большинство отказов из категории внезапных для персонала в категорию постепенных за счет раннего их обнаружения.
Обеспечение мониторинга технического состояния и автоматической диагностики в режиме реального времени на основе применения автоматизированных систем управления безопасной ресурсосберегающей эксплуатации оборудования (АСУ БЭРтм) позволяет предоставлять технологическому персоналу оперативную информацию о работающем оборудовании, показывать проблемные и узкие места, своевременно выводить из эксплуатации агрегаты, техническое состояние которых угрожает безопасности производственного процесса.
Непосредственным ведением технологического процесса на производстве занимаются конкретные специалисты, и именно от них зависит не только качество выпускаемой продукции, но и обеспечение вопросов безопасной и безаварийной эксплуатации производств.
В свою очередь, применение автоматизированных систем мониторинга технического состояния и диагностики позволяет уменьшить субъективное влияние человеческого фактора на обеспечение безаварийной эксплуатации производства, а в случае принятия определенных организационных мер на предприятии и полностью его исключить. При применении на нефтеперерабатывающем предприятии АСУ БЭРтм вся информация о техническом состоянии находящегося в эксплуатации оборудования, о действиях технологического персонала передается всем заинтересованным в безопасной и безаварийной эксплуатации производства: службам главного механика, энергетика, технадзору и т.д., а также главным специалистам и руководителям предприятия. Такой подход позволяет обеспечить постоянный, круглосуточный контроль действий технологического персонала на установках предприятия.
При работе динамического оборудования происходит выработка его ресурса. Применение систем мониторинга технического состояния и автоматической диагностики АСУ БЭРтм позволяет обеспечить эксплуатацию диагностируемого оборудования по его фактическому техническому состоянию. Таким образом, в ремонт поступает оборудование, техническое состояние которого «Требует принятия мер» либо «Недопустимо», т.е. именно в то время, когда ресурс оборудования практически полностью выработан и требуется его восстановление.
При этом процесс проведения ремонта агрегата для обеспечения стабильного качества выходящего из ремонта оборудования также должен проходить в контролируемых и управляемых условиях. Для обеспечения контроля качества ремонта ремонтные подразделения оснащаются системами, обеспечивающими входной контроль изделий и материалов, используемых при ремонте, а также системами, обеспечивающими выходной контроль качества проведенного ремонта. При таком подходе из ремонта на технологическую установку поступает оборудование надлежащего качества с максимальным эксплуатационным ресурсом.
Автоматизированные системы управления безопасной ресурсосберегающей эксплуатацией оборудования
В АО «ННК-Хабаровский НПЗ» внедрены все элементы технологии АСУ БЭРтм (рис. 1):
- стационарными системами мониторинга технического состояния и автоматической диагностики оснащены агрегаты 1-й, 2-й категории [1] на установках АТ-1, 35/11-300, состояние вспомогательного динамического оборудования контролируется персональной системой автоматической диагностики Compacs®-micro;
- на предприятии установлен сервер и развернута диагностическая сеть Compacs®-Net;
- ремонтное производство оснащено стендовыми системами контроля качества подшипников качения (КОМ-ПАКС®-РПП), контроля качества ремонта электродвигателей (КОМПАКС®-РПЭ) и консольных насосов (КОМ-ПАКС®-РПМ).
Стационарные системы мониторинга технического состояния и автоматической диагностики
Система мониторинга технического состояния и автоматической диагностики (рис. 2) представляет собой сеть первичных преобразователей, установленных непосредственно на диагностируемом оборудовании нефтеперерабатывающего (нефтехимического) комплекса.
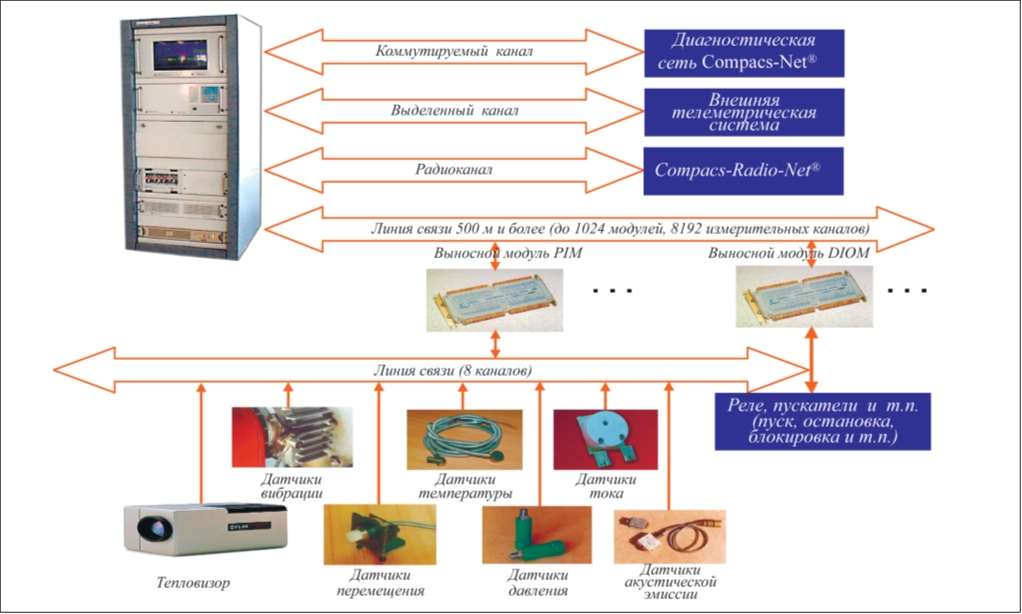
Датчики выполняют преобразование измеряемых параметров различных физических величин (вибрация, температура, ток, давление и др.) в электрический сигнал.
Электрический сигнал с датчиков по кабельным линиям связи поступает в программируемые интерфейсные модули для предварительной обработки и далее в диагностическую станцию для окончательной обработки, проведения автоматической диагностики и визуального отображения в реальном времени полученных результатов измерений. Для обеспечения безаварийной эксплуатации оборудования в соответствии с общими техническими требованиями к системам диагностики и мониторинга [2] система выдает речевые предупреждения персоналу при переходе агрегатов из допустимого технического состояния в состояние «Требует Принятия Мер» или «Недопустимо».
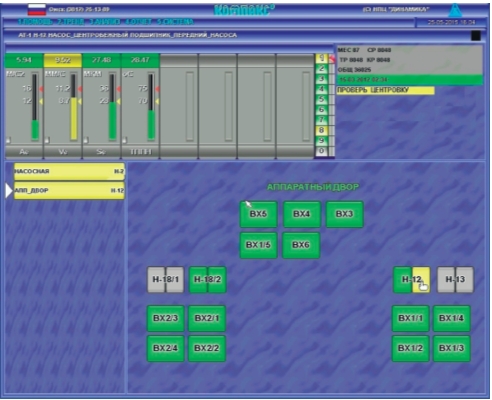
На экране «Монитор» системы диагностики и мониторинга (рис. 3) схематично представлено диагностируемое оборудование в интуитивно понятной любому человеку форме. Основные измеряемые параметры вибрации – виброускорение (Ае), виброскорость (Ve), виброперемещение (Se) в соответствии с ГОСТ Р 32106–2013 [3] и прочие – представлены в левой верхней части экрана в виде мензурок с установленными пороговыми значениями: желтый треугольник – порог «Требует принятия мер», красный треугольник – порог «Недопустимо».
При ухудшении технического состояния агрегата и превышении измеряемыми параметрами соответствующих пороговых значений система выдает речевое предупреждение технологическому персоналу, и курсор автоматически устанавливается на наихудший агрегат.
В представленном на рис. 3 случае насос агрегата Н-12 перешел в состояние «Требует принятия мер», автоматическая экспертная система провела анализ вибросигнала и выдала текстовое сообщение – рекомендации, которые необходимо выполнить персоналу для обеспечения безаварийной эксплуатации оборудования и приведения его к техническому состоянию «Допустимо».
Предписания автоматической экспертной системы расположены в правой верхней части экрана «Монитор»: «Проверь_ центровку».
Автоматический мониторинг технического состояния динамического оборудования опасных производственных объектов в течение всего периода эксплуатации позволяет перевести большинство отказов из категории внезапных в категорию постепенных и наблюдаемых за счет раннего их обнаружения.
Внедрение технологии АСУ БЭРтм на Хабаровском НПЗ было начато в 2010 г. с оснащения системой компьютерного мониторинга технического состояния и предупреждения аварий установки АТ-1. На установке АТ-1 система обеспечивает автоматический мониторинг технического состояния и диагностику 21 насосного агрегата первой категории опасности согласно ГОСТ Р 53564– 2009, 13 воздушных холодильников 2-й категории опасности с помощью вибродиагностического и параметрического методов неразрушающего контроля посредством 65 датчиков вибрации, 52 датчиков температуры и 21 датчика тока.
Применение систем компьютерного мониторинга технического состояния и предупреждения аварий позволило обеспечить безаварийную работу всего динамического оборудования установки АТ-1 путем автоматической диагностики обнаружения зарождающихся неисправностей и постоянного мониторинга развития неисправностей в реальном времени. Все измеряемые системой параметры накапливаются в базах данных за различные временные интервалы – от 12 ч до 9 лет (12 ч, 4 и 40 сут, 1 год и 9 лет) и могут быть представлены персоналу по их запросу для просмотра и анализа (рис. 4–6). Встроенная экспертная система ведет контроль параметров и скоростей их роста в соответствии с ГОСТ Р 32106–2013 [3, 4].
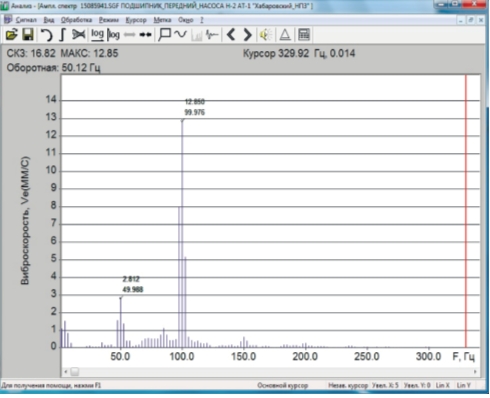
Для специалистов-вибродиагностов в системе имеется режим «Анализ», в котором в ручном режиме можно провести анализ вибросигнала и уточнить работу автоматической экспертной системы. На рис. 4 приведен спектр виброскорости подшипника переднего насоса (ППН) насосного агрегата Н-2. В спектре виброскорости присутствуют первая и вторая гармоники оборотной частоты 49,9 Гц и 99,9 Гц с амплитудами соответственно 2,81 мм/с и 12,85 мм/с, что составляет 93% общего уровня виброскорости 16,8 мм/с, что указывает на расцентровку насосного агрегата со стороны насоса. туды – на оборотную частоту (49,9 Гц) и ее гармонические составляющие (соответственно 99,9; 149,9; 197,5 Гц), что указывает на расцентровку насосного агрегата со стороны насоса.
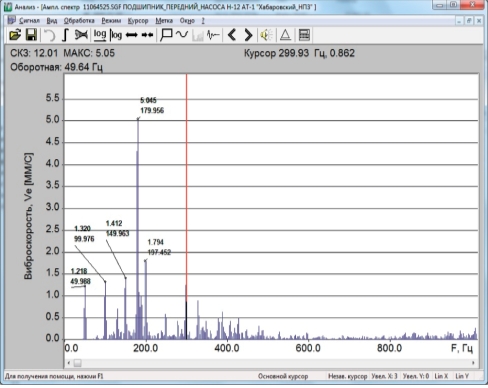
На рис. 6 приведен четырехсуточный тренд вибропараметров Н-12 с экспертными сообщениями, выданными автоматической экспертной системой на основе виброанализа, проведенного без участия человека.
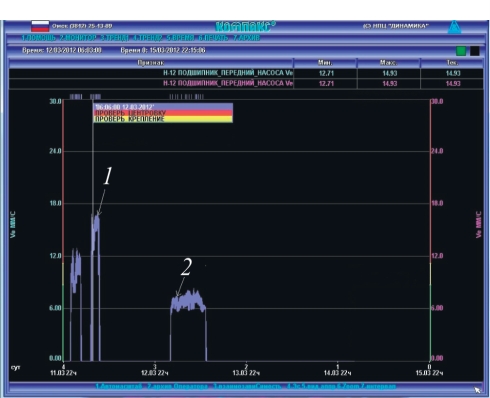
На трендах наблюдается переход агрегата из состояния «Допустимо» в состояние «Недопустимо» в течение 2,5 ч (см. рис. 6, участок 1). С 12.03.2012 г. наблюдается повышение вибрации и предупреждение экспертной системы сообщением: «ПРОВЕРЬ ЦЕНТРОВКУ», «ПРОВЕРЬ КРЕПЛЕНИЕ». За 3 ч эксплуатации агрегата Н-12 виброскорость (Ve) выросла с 9 до 15 мм/с. По рекомендациям системы персонал установки запустил в работу резервный агрегат, а агрегат Н-12 был остановлен и выведен в ремонт. Выполнена центровка насосного агрегата, обтяжка креплений. После выполненного ремонта включение в работу насоса показало, что ремонт проведен качественно, техническое состояние насоса «Допустимо» (см. рис. 6, участок 2).
Все стационарные системы объединены в диагностическую сеть предприятия, которая обеспечивает доступ к информации о состоянии оборудования в реальном времени и контроль работы персонала со стороны руководства завода (см. рис. 1).
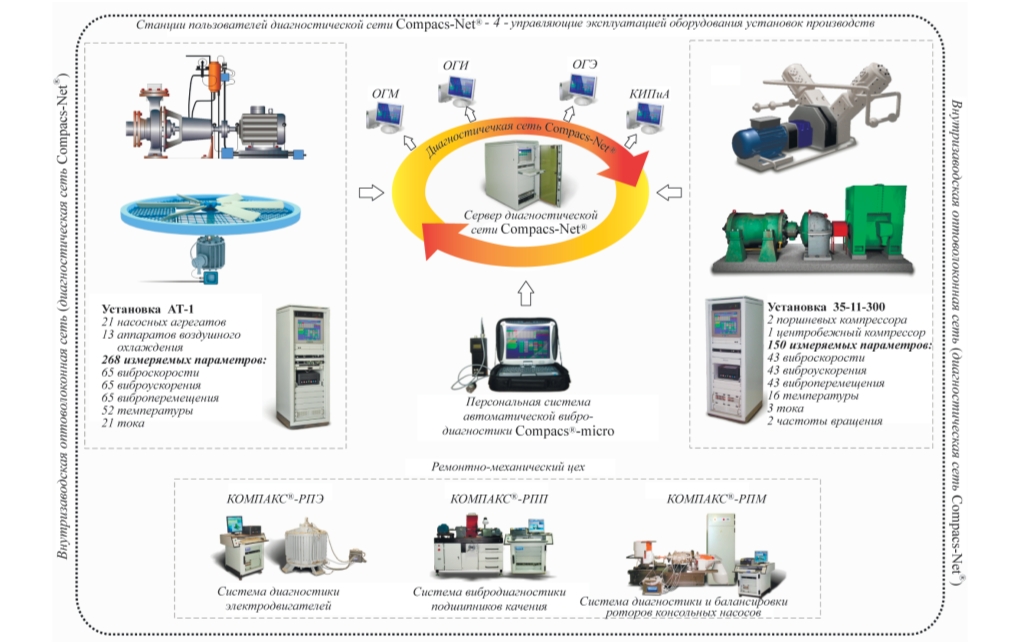
Применение стационарных систем [5] на установках АТ-1, 35/11-600 позволило перевести диагностируемые системой агрегаты от системы планово-предупредительных ремонтов на эксплуатацию по фактическому техническому состоянию с проведением ремонтов по рекомендациям систем.
Персональная система автоматической диагностики Compacs®-micro
Мониторинг состояния вспомогательного динамического оборудования ведется с помощью переносной персональной системы автоматической диагностики Compacs®-microтм, которая обеспечивает диагностику технического состояния узлов машин и механизмов на месте эксплуатации автоматически по уровням параметров вибрации (виброускорение, виброскорость, вибропереме-щение) по стандартам ГОСТ Р 32106–2013, ГОСТ ИСО 10816-3, ГОСТ 20815, ГОСТ 30576, а также автоматический анализ вибросигналов с выводом сообщений экспертной системы.
Применение персональной системы автоматической диагностики позволяет вести периодический (согласно графику) мониторинг технического состояния второстепенных агрегатов, обеспечивать на технологической позиции приемку агрегатов из ремонта и при необходимости проводить динамическую балансировку на месте эксплуатации. Персональная система автоматической диагностики, как и стационарная система, имеет режимы «Тренд», «Анализ» для проведения вибрационного анализа специалистами-диагностами и контроля во времени изменения параметров вибрации.
Стендовые системы контроля качества ремонта
На ремонтном производстве Хабаровского НПЗ внедрены стендовые системы КОМПАКС®, обеспечивающие выполнение качественного ремонта динамического оборудования.
Система вибродиагностики подшипников качения КОМПАКС®-РПП предназначена для объективной оценки технического состояния поступающих на предприятие подшипников качения и обеспечения автоматической сортировки подшипников на три категории качества:
- рекомендуемые к применению на оборудовании 1-й категории опасности быстроходных агрегатах с частотой вращения до 3 000 об/мин и более;
- рекомендуемые к применению на оборудовании 2-й категории опасности с частотой вращения не более 1 500 об/мин;
- рекомендуемые к применению на оборудовании 3-й категории опасности с частотой вращения не более 1 000 об/мин.
Система вибродиагностики подшипников качения имеет автоматическую экспертную систему, которая обеспечивает определение конкретных дефектов в подшипниках качения. По результатам входного контроля на каждый подшипник выдается акт проверки.
Оснащение ремонтного производства системой вибродиагностики подшипников качения позволило исключить поставку некачественных подшипников на завод, обеспечить возврат не прошедших входной контроль подшипников поставщикам, а в агрегаты устанавливать только бездефектные подшипники с максимальным потенциальным ресурсом.
Система диагностики качества сборки и динамической балансировки роторов консольных насосов в собственных подшипниках КОМПАКС®-РПМ позволяет проводить выходной контроль качества ремонта насосов в сборе по параметрам вибрации, температуре, частоте вращения, а также выполнять динамическую балансировку при наличии дисбаланса в контролируемом насосе.
В системе диагностики качества сборки и динамической балансировки роторов консольных насосов в собственных подшипниках реализован новый способ «SVOS™балансировки», который обеспечивает плавный разгон ротора до номинальной частоты вращения. В режиме разгона при обнаружении дисбаланса реализуется алгоритм автоматической балансировки насоса на достигнутой частоте. «SVOS™-балансировка» позволяет устранить динамический дисбаланс на частотах, меньших номинальной частоты вращения, что уменьшает динамические нагрузки и обеспечивает целостность подшипников в случае неверного монтажа или большого дисбаланса.
Встроенная автоматическая экспертная система позволяет без участия человека проводить диагностику и определять неисправности опоры насоса. По результатам испытаний насоса система выдает акт выходного контроля, который с прочей ремонтной документацией поступает в паспорт агрегата на технологическую установку.
Применение системы диагностики качества сборки и динамической балансировки роторов консольных насосов в собственных подшипниках на Хабаровском НПЗ позволило выдавать из ремонта насосы с минимальными уровнями вибрации [6].
Система диагностики электродвигателей КОМПАКС®-РПЭ обеспечивает автоматический контроль качества ремонта электродвигателей по вибропараметрам (виброускорение, виброскорость, виброперемещение), измеряемым в плоскостях переднего и заднего подшипника в вертикальном, горизонтальном и осевом направлениях, тока потребления, измеряемого по фазам питающего напряжения, температуры переднего и заднего подшипника, частоты вращения ротора двигателя.
Встроенная автоматическая экспертная система позволяет без участия человека проводить диагностику и определять неисправности электродвигателей. По завершению испытаний система выдает акт выходного контроля электродвигателя.
Основными достоинствами стендовых систем являются стабильность работы, простота в эксплуатации и обслуживании, автоматическая диагностика оборудования, не требующая от персонала теоретических знаний по вибрации, диагностике и балансировке. Применение стендовых систем на АО «ННК-Хабаровский НПЗ» позволило выпускать из ремонта на технологические установки качественное оборудование с максимальным ресурсом эксплуатации.
Экономический эффект
Надежная работа оборудования опасного производства определяется большим числом факторов, важнейшими из которых являются качество его изготовления, монтажа, эксплуатации, ремонта, оптимальные технологические параметры и характер ведения технологического процесса, культура производства и уровень технологической и исполнительской дисциплины персонала.
В современных условиях рост эффективности работы нефтеперерабатывающих предприятий достигается в основном за счет обеспечения безаварийной эксплуатации технологического оборудования производств, увеличения межремонтного периода эксплуатации производств и оптимизацией эксплуатационных затрат на ремонт и техническое обслуживание оборудования [6].
За указанный период простоев технологической установки не зафиксировано. Коэффициент эксплуатационной (технической) готовности оборудования за счет своевременных и целенаправленных действий персонала за указанный период составил 100%.
Экономический эффект от внедрения и использования системы при эксплуатации динамического оборудования на примере установки АТ-1 за один год составил около 30 млн. руб.
Таким образом, применение АСУ БЭРтм КОМПАКС® в АО «ННК-Хабаровский НПЗ» позволило перейти на эксплуатацию динамического оборудования по его фактическому техническому состоянию в реальном времени, т.е. проводить своевременный, целенаправленный ремонт или техническое обслуживание, повысить надежность и безопасность эксплуатации оборудования, исключить возникновение аварийных ситуаций.
Обслуживающий персонал технологических установок АТ-1, 35-11/300 и ремонтных участков активно использует системы мониторинга технического состояния в своей работе, не допуская работы оборудования в условиях развивающихся дефектов, своевременно реагируя на все изменения и проводит мероприятия по рекомендациям систем.
Экономический эффект от внедрения и использования системы КОМПАКС® при эксплуатации динамического оборудования установки первичной переработки нефти (~ 30 млн. руб за год эксплуатации) позволяет констатировать многократную окупаемость систем за время их службы.
Список литературы
- ГОСТ Р 53564–2009 Контроль состоянии и диагностика машин. Мониторинг состояния оборудования опасных производств. Требования к системе мониторинга. М.: Стандартинформ, 2010.
- ГОСТ Р 53563–2009 Контроль состоянии и диагностика машин. Мониторинг состояния оборудования опасных производств. Порядок организации. М.: Стандартинформ, 2010.
- ГОСТ Р 32106–2013 Контроль состоянии и диагностика машин. Мониторинг состояния оборудования опасных производств. Вибрация центробежных насосов и компрессорных агрегатов. М.: Стандартинформ, 2014.
- Костюков В.Н., Науменко А.П. и др. Стандарты в области мониторинга технического состояния оборудования опасных производств//Безопасность труда в промышленности. 2012. №7.
- Костюков В.Н. Мониторинг безопасности производства. М.: Машиностроение, 2002.
- Костюков В.Н., Науменко А.П. Основы виброакустической диагностики и мониторинга машин. Новосибирск: Изд. Сиб. отд. РАН, 2014.