Автор: А.Л. Колбин, Д.С. Тихонов, В.И. Эльманович (ООО «Диагностика и анализ риска»).
Опубликовано в журнале Химическая техника №1/2014
Короткоцикловая адсорбция (КЦА) широко используется на химических, нефтеперерабатывающих и нефтехимических предприятиях [1]. Поскольку рабочий цикл адсорберов КЦА короткий (3…5 мин), таких циклов за время эксплуатации накапливается слишком много для аппаратов, спроектированных и изготовленных по ОСТ 26.291–94 [2] (в последнее время – по ГОСТ Р 52630–2012 [3] и ПБ 03-584–03 [4]). Так, при трехминутном цикле получается 20 циклов в час и 173 тыс. циклов за 8 640 ч (год непрерывной работы).
При проектировании адсорберов КЦА расчет на прочность для однократного (статического) нагружения (число циклов нагружения не превышает 103) проводится по ГОСТ Р 52857–2007 [5].
Поверочный расчет на циклическую прочность проводят для сосудов, спроектированных и изготовленных до 2008 г. по ГОСТ 25859–83 [6]. Число главных циклов нагружения от давления, стесненности температурных деформаций или других видов нагружений должно находиться в пределах 103…5105 за весь срок эксплуатации сосуда.
Начиная с 2008 г., расчет на прочность сосудов, эксплуатируемых в условиях малоцикловой усталости, выполняют по ГОСТ Р 52857–2007 [5], в котором число главных циклов нагружения от давления, стесненности температурных деформаций или других видов нагружений составляет 103…106 за весь срок эксплуатации сосуда.
При числе циклов нагружения более 106 изделия (например, коленчатые валы двигателей, вагонные оси) работают в условиях многоцикловой усталости, а это уже совсем другие требования к технологии и качеству изготовления, чем заложенные в ОСТ 26.291–94 и ГОСТ Р 52630–2012.
Таким образом, предельное число циклов безопасной эксплуатации адсорберов КЦА находится в пределах 5105…106, и срок безопасной эксплуатации адсорберов КЦА составляет 3…5 лет непрерывной работы. После выработки этого срока в зонах концентрации напряжений происходит зарождение и развитие усталостных трещин. При этом срок службы сосуда определяется уже не прочностью, а его живучестью, т.е. способностью сопротивляться развитию трещин.
Особенности накопления усталостных повреждений металла сосудов и аппаратов при малоцикловой и многоцикловой усталости
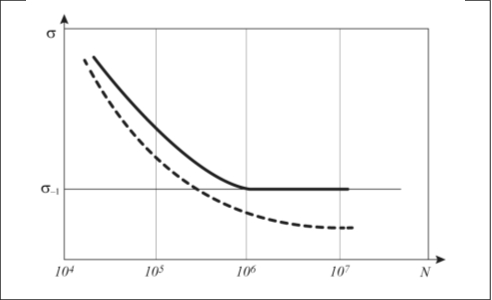
При действии циклических (повторно-переменных) напряжений в металлах и сплавах происходит зарождение и постепенное развитие трещин (усталость металла), вызывающее в конечном итоге полное разрушение детали или конструкции. Это разрушение особенно опасно, так как может происходить под действием напряжений, намного меньших пределов прочности и текучести [7].
Процесс усталостного разрушения разделяется на две основные стадии: .
- стадия 1 – накопление необратимых изменений, приводящее к возникновению трещин на поверхности металла;
- стадия 2 – развитие трещины
На стадии 1 происходит накопление субмикроскопических и микроскопических изменений в структуре металла. Повреждения на стадии 1 не могут быть выявлены средствами неразрушающего контроля (НК).
Стадия 2 процесса усталостного разрушения состоит в распространении усталостной трещины. Стадия распространения трещины чаще всего занимает значительную долю общего времени, необходимого для усталостного разрушения. Повреждения на стадии 2 могут быть выявлены средствами НК. На этой стадии наиболее эффективен акустико-эмиссионный (АЭ) мониторинг.
Сопротивление металлов усталости обычно характеризуется так называемой кривой усталости (кривая Велера), которая описывает зависимость числа
N циклов напряжений до разрушения от амплитуды s переменных напряжений (рис. 1). В большинстве случаев кривая усталости (сплошная линия) имеет асимптотический характер, например для большинства сталей.
В этом случае может быть определен «физический» предел усталости как наибольшее напряжение цикла s–1, которое может выдержать без разрушения металл при сколь угодно большом числе циклов нагружения.
В ряде случаев кривая усталости имеет непрерывно падающий характер (штриховая линия), и предел усталости (или предел выносливости) рассматривается лишь в зависимости от числа циклов (ограниченный предел).
Многоцикловая усталость
При напряжениях, не превосходящих предела текучести металла, усталостные процессы связаны лишь с явлениями микропластической деформации весьма неоднородно-напряженного конгломерата поликристаллической структуры стали, не проявляющимися макроскопически, и рассматриваются как квазиупругие.
Число циклов, необходимое для усталостного разрушения при таких уровнях напряженности, составляет сотни тысяч и даже миллионы, а соответствующий процесс называется многоцикловой усталостью.
Многоцикловая усталость характерна для многих деталей динамического оборудования, работающего в нефтеперерабатывающей, нефтехимической и химичес- кой отраслях промышленности (компрессоры и насосы различных типов, механические сепараторы и другое динамическое оборудование).
Малоцикловая усталость
При напряжениях, превосходящих предел текучести, явления усталости сопровождаются макроскопическими пластическими деформациями и рассматриваются как упругопластические. Число циклов, необходимое для разрушения в этой области, измеряется тысячами и сотнями тысяч, а соответствующий процесс называется малоцикловой усталостью.
Малоцикловая усталость характерна для статического оборудования (сосуды, аппараты, адсорберы, абсорберы, колонны и т.п.), а также для деталей технологи- ческих трубопроводов. Эффекты малоцикловой усталости наблюдаются при числе главных циклов нагружения от давления, стесненности температурных деформаций и других видов нагружения – 103…5105 за весь срок эксплуатации.
Усталость материалов и усталость конструкций
Вопросы усталости материалов и усталости конструкций детально рассмотрены в Стандарте США API 579-1/ASME FFS-1 [8]. В стандарте показано, что следует крайне осторожно подходить к использованию характеристик усталости материалов, полученных по данным испытаний на циклическую прочность гладких образцов, при расчете на прочность и долговечность сосудов и аппаратов. В силу конструктивных особенностей и технологии изготовления сосудов и аппаратов кривая Велера для них будет всегда иметь ниспадающий характер (см. рис. 1, штриховая линия). «Физического» предела усталости s–1 сосудов не существует. При числе циклов нагружения более 105 безотказная, безопасная и безаварийная эксплуатация сосудов возможна только при внедрении адекватных компенсирующих мероприятий и мониторинга.
Приведем результаты акустико-эмиссионного мониторинга адсорбера КЦА, проведенного специалистами ООО «Диагностика и анализ риска».
Объектом акустико-эмиссионного мониторинга являлся адсорбер, изготовленный в апреле 2004 г. в ОАО «СалаватНефтеМаш». Основанием для проведения мониторинга была необходимость временной эксплуатации (до замены новым) аппарата с отступлениями от действующих норм и правил. При техническом освидетельствовании адсорбера, проведенном в июне 2013 г., была обнаружена трещина в околошовной зоне вертикального сварного шва. Длительная остановка технологического процесса для ремонта или замены адсорбера новым была связана с неприемлемыми для компании экономическими потерями. Для приобретения и монтажа нового адсорбера требовалось 30 дней. Было принято решение изготовить временную ремонтную конструкцию путем приварки накладной латки (рис. 2). Такой ремонт сосуда, работающего под давлением, является отступлением от действующих норм и правил (ПБ 03-576–03 [9], ОТУ–3 [10]). Эксплуатация временной ремонтной конструкции возможна только при условии организации непрерывного мониторинга для отслеживания возможного развития дефектов. Согласно ПБ 03-593–03, п. 2.1.2 [11], в качестве метода мониторинга использован акустико-эмиссионный (АЭ) метод.
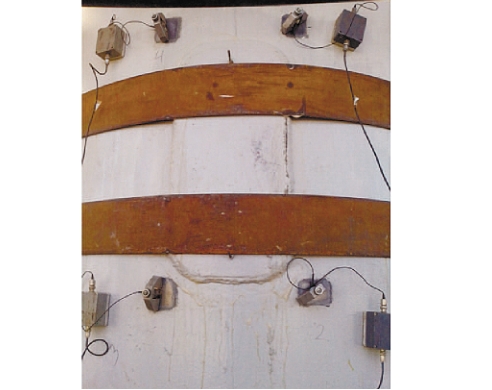
адсорбера
Цель мониторинга: проследить динамику возможного развития дефектов в аппарате, дать оценку опасности дефектов для принятия решения о необходимости аварийной остановки адсорбера.
АЭ мониторинг был проведен в следующем порядке:
- поверочный расчет адсорбера на прочность и трещиностойкость, оценка возможности и условий отсутствия аварийного разрушения аппарата;
- разработка технологии проведения АЭ мониторинга и аппаратное оформление системы мониторинга;
- монтаж системы мониторинга; l калибровка и настройка параметров АЭ мониторинга;
- сбор данных АЭ мониторинга (непрерывно);
- обработка и анализ данных мониторинга (3 раза в сутки – утром, днем и вечером);
- демонтаж системы мониторинга.
Проведенные расчеты на прочность по ГОСТР 52857–2007 [5] и трещиностойкость по нормам ПНАЭ Г-7-002–86 [12] показали следующее: n статическая прочность адсорбера с накладной латкой обеспечена; n при циклическом нагружении сосуда выполнено условие существования докритической сквозной трещины (концепция «течь перед разрушением» по стандарту API 579-1/ASME FFS-1 [8]); n в процессе эксплуатации адсорбера с накладной заплатой мгновенного гильотинного разрыва стенки не произойдет. Возможное разрушение аппарата будет проходить в три этапа: этап 1 – зарождение усталостной трещины на внутренней поверхности аппарата; этап 2 – подрастание усталостной трещины и образование докритической сквозной трещины (протечка); этап 3 – рост сквозной трещины, закритическое развитие и гильотинный разрыв аппарата Þ выброс опасных веществ Þ взрыв-пожар.
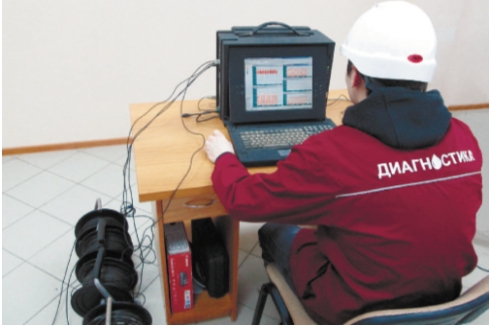
мониторинга адсорбера
Таким образом, задачей непрерывного мониторинга являлось отслеживание возможного развития усталостных трещин на стадии 2.
Анализ результатов акустико-эмиссионного мониторинга адсорбера
АЭ мониторинг проведен на базе АЭ системы A-Line 32D производства фирмы «ИНТЕРЮНИС» (рис. 3). Установка четырех датчиков по периметру латки (см. рис. 2) позволила выполнить точную оценку месторасположения и опасности дефектов.
Для проведения АЭ мониторинга была организована круглосуточная трехсменная работа. Сбор данных АЭ мониторинга проводили в постоянном режиме с последующей их компьютерной обработкой.
Обработку и анализ данных АЭ мониторинга проводили ежесменно для принятия решения о необходимости аварийной остановки адсорбера.
На основании анализа результатов АЭ мониторинга адсорбера установлено:
- при работе адсорбера дважды (25.07.2013 г. и 28.07.2013 г.) зарегистрированы источники АЭ II и III классов (активные и критически активные в соответствии с классификацией ПБ 03-593, (рис. 4, 5), что свидетельствует о наличии в сварных швах латки развивающихся дефектов;
- ввиду циклического режима эксплуатации сосуда возможно образование течи через сварные швы приварки латки.
Для решения вопроса о выводе сосуда из эксплуатации проведен мониторинг протечек – периодический осмотр зоны заплаты персоналом установки с обмыливанием сварных швов приварки латки. Сквозных трещин не обнаружено.
Таким образом, обеспечение безотказной, безо- пасной и безаварийной эксплуатации адсорберов КЦА после наработки более 500 тыс. циклов возможно только при внедрении АЭ мониторинга для отслеживания возможного развития усталостных трещин.
В процессе эксплуатации необходимо вести учет циклов и при приближении к наработке 500 тыс. циклов проводить обследование сосудов для выявления зарождения трещин (АЭ контроль) и возможного развития выявленных дефектов (АЭ мониторинг).
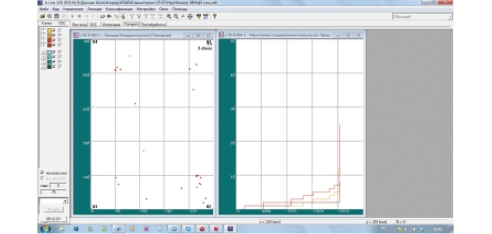
при мониторинге (25.07.2013; 10 ч 50 мин)
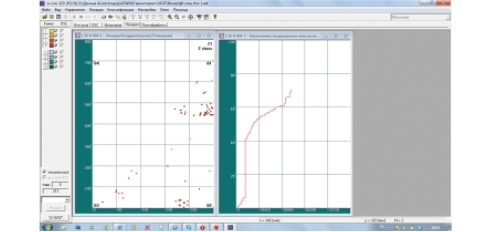
при мониторинге (28.07.2013; 21 ч 50 мин)
Убытки от простоя, инцидента, аварии не сравнимы с затратами на АЭ мониторинг. Внедрение АЭ мониторинга адсорберов КЦА позволит достигнуть правильного баланса интересов бизнеса и безопасности (оптимизация затрат на ремонт и замену оборудования при минимальном простое установок).
Список литературы
- Кёпсель К. Рациональные области использования установок короткоцикловой адсорбции в химической промышленности//Химическая техника. 2005. №3.
- ОСТ 26.291–94. Сосуды и аппараты стальные сварные. Общие технические условия.
- ГОСТ Р 52630–2012. Сосуды и аппараты стальные сварные. Общие технические условия.
- ПБ 03-584–03. Правила проектирования, изготовления и приемки сосудов и аппаратов стальных сварных.
- ГОСТ Р 52857–2007. Сосуды и аппараты. Нормы и методы расчета на прочность.
- ГОСТ 25859–83. Сосуды и аппараты стальные. Нормы и методы расчета на прочность при малоцикловых нагрузках.
- Серенсен С.В., Когаев В.П., Шнейдерович Р.М. Несущая способность и расчеты деталей машин на прочность. М.: Машиностроение, 1975.
- API 579-1/ASME FFS-1 Fitness-For-Service. 2007. USA Standard.
- ПБ 03-576–03. Правила устройства и безопасной эксплуатации сосудов, работающих под давлением.
- ОТУ–3. Сосуды и аппараты. Общие технические условия на ремонт корпусов.
- ПБ 03-593–03. Правила организации и проведения акустико-эмиссионного контроля сосудов, аппаратов, котлов и технологических трубопроводов.
- Нормы расчета на прочность оборудования и трубопроводов атомных энергетических установок (ПНАЭ Г-7-002-86). Госатомнадзор СССР, М.: Энергоиздат, 1989.