Авторы: Д.С. Бирюков, Д.Г. Федотов (ООО «ГК «ИНТРАТУЛ»).
Опубликовано в журнале Химическая техника №11/2018
В условиях стремительного перехода промышленности на рельсы «Индустрии 4.0» и продолжающейся цифровизации производства все больше российских компаний нефтегазового сектора, химии и энергетики обращают внимание на данные тенденции и проводят активные преобразования на своих предприятиях. Так, отдельным пунктом выделяется цифровизация в стратегиях развития «Роснефти» и «ЕВРАЗ», а «Газпромнефть» даже создает в своей структуре дирекцию по цифровой трансформации. Эффективное использование современных цифровых технологий, поиск «узких мест» в технологическом процессе, внедрение лучших мировых практик – все это становится серьезным вызовом для инжиниринговых компаний.
В настоящей статье рассмотрим проблему управления режимами работы вращающихся печей. В настоящее время вращающиеся печи используются в различных процессах в нескольких отраслях промышленности: для прокалки нефтяного кокса (УПНК), для спекания шихт в производстве глинозема, получения цементного клинкера, окислительного, восстановительного, хлорирующего обжига, прокалки гидроокиси алюминия, карбонатов, сульфатов и др., получения гашеной извести, обезвоживания материалов, извлечения цинка и свинца (вельц-печи), получения железа или сплавов цветных металлов их прямым восстановлением из руд в твердой фазе (кричные печи), обжига огнеупорного сырья.
Вращающаяся печь располагается под уклоном порядка 3…4°, в верхней ее части («холодный обрез») происходит загрузка сырья, в нижней части («горячий обрез») выгружается на конвейер нагретый продукт, который затем подвергается охлаждению в холодильнике. За счет медленного вращения печи вокруг своей оси вещество плавно опускается в нижний конец и подвергается перемешиванию. Горячие газы, за счет которых происходит нагревание вещества, продуцируются встроенной в горячий обрез печи форсункой и проходят по печи в обратном направлении. Топливом для форсунки может быть газ, масло, размельченный нефтяной кокс или молотый уголь. Печь снабжена огнеупорной футеровкой, установлена при помощи бандажей на роликовые опоры с подшипниками скольжения.
Типовых проблем, которые можно решить за счет тепловизионного контроля, две: слежение за состоянием футеровки с ранним обнаружением проблемных зон и управление самим процессом прокалки. Если первую проблему на многих предприятиях уже более или менее удачно решают за счет тепловизоров (чаще всего переносных) и сканеров, то решение второй проблемы в большинстве случаев находится на уровне «каменного века». Стоит обратить внимание, что даже применение периодического теплового контроля не избавляет производственные подразделения от риска возникновения нештатной ситуации и прогара с сопутствующими потерями в виде простоя, ликвидации последствий и внепланового ремонта.
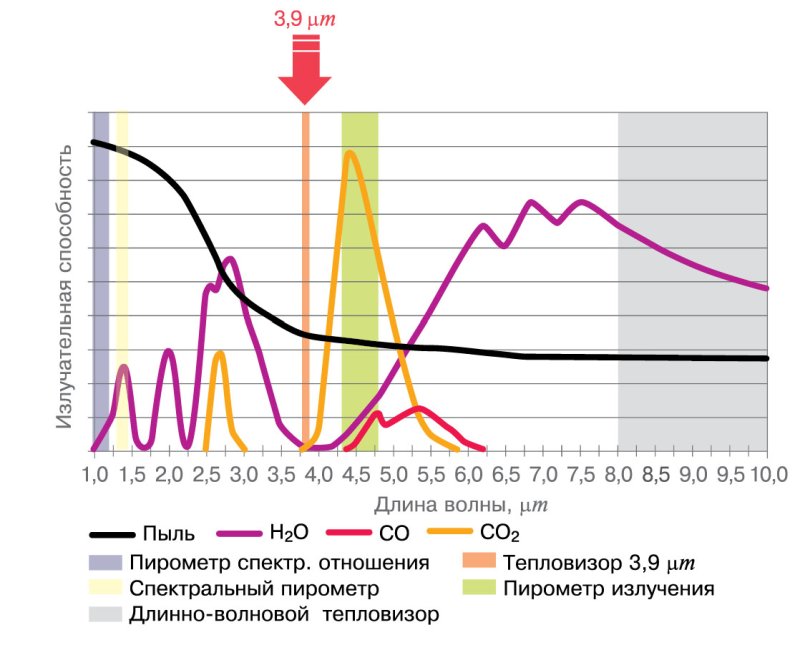
Управление печью оператор-прокальщик осуществляет вручную, оценивая на глаз положение зоны прокаливания и температуру в ней через смотровое окно печи. Оценив ситуацию, он регулирует объем подачи топлива и/или скорость вращения печи. При этом операторная зачастую расположена на удалении от самой печи, так что в процессе возникает дополнительное запаздывание по управляющему воздействию. Несвоевременные или неправильные действия оператора могут привести либо к чрезмерному охлаждению прокаливаемой массы (в этом случае на выходе идет бракованный продукт) либо, наоборот, к ее перегреву (может быть повреждена загрузочная шайба на холодном обрезе печи, холодильник либо конвейер транспортировки охлажденного продукта, расположенный после холодильника). Все эти нештатные ситуации в конечном счете ведут к значительным финансовым потерям за счет вынужденного останова и замены поврежденных компонентов.
Очевидно и решение проблемы: устранить человеческий фактор, автоматизировав процесс управления положением зоны прокалки. В этом случае выходными сигналами системы управления будут интенсивность подачи топлива на форсунку и скорость вращения печи, а входными – массив данных о температуре в каждой точке зоны прокалки и фактическом расположении этой зоны. Сложность состоит лишь в практическом измерении этих параметров, для чего понадобится специализированный тепловизионный комплекс.
Конструкция печи позволяет встроить в горячий обрез тепловизионную камеру для наблюдения за зоной прокалки. Однако ситуация осложняется наличием пламени между камерой и наблюдаемой зоной. Визуально оператор ничего не увидит, кроме того, измерение температуры также будет неточным.
Это обстоятельство можно обойти с помощью использования матричных приемников, работающих на определенной длине волны и специальных инфракрасных фильтров, рассчитанных на характерный спектр поглощения топочных газов. Окно прозрачности в данном случае находится на длине волны 3,9 µm, что видно на рис. 2.
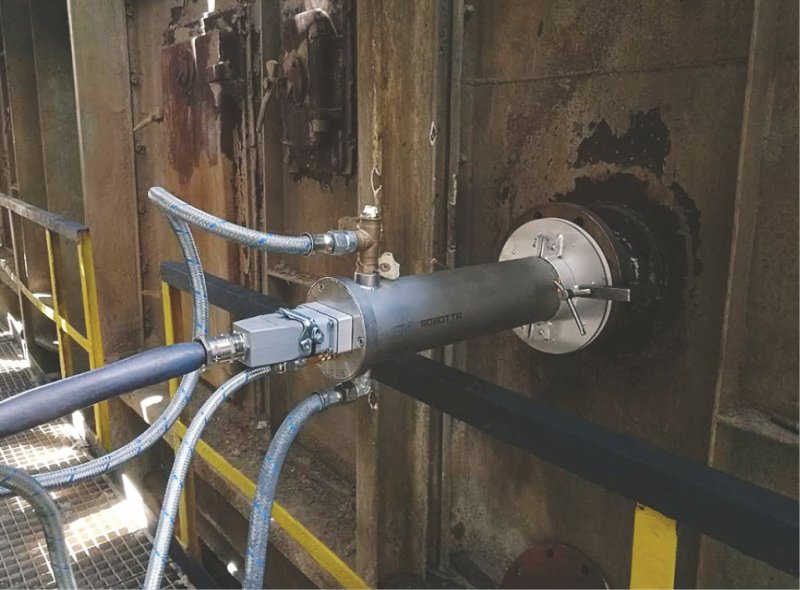
Таким образом, у нас появляется нужный инструмент – специализированный тепловизор для внутрипечного мониторинга с функцией отсечки пламени. Для работы в условиях высоких температур тепловизионный модуль помещается в оболочку с водяным и воздушным охлаждением. Внешний вид такого тепловизора показан на рис. 3.
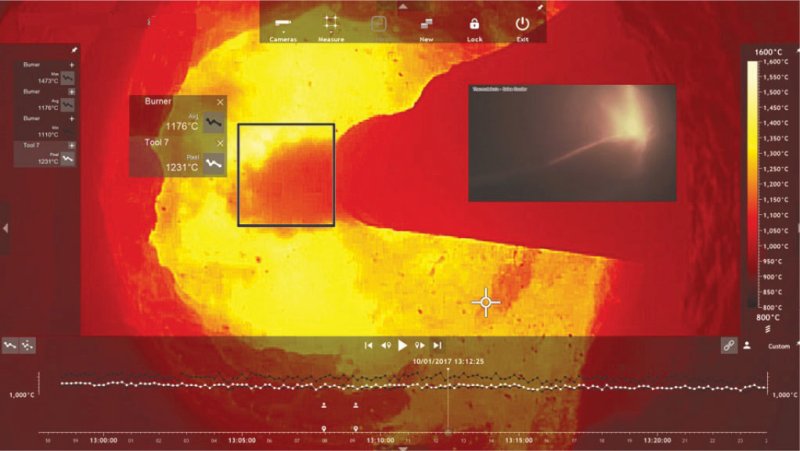
Характеристики внутрипечного тепловизора
Спектральный диапазон, мкм 3,9
Диапазон измерений, °С 400…1250
Матрица 2D микроболометра с датчиком 640×480 пикселей
Поле зрения объектива (FOV) От 28° × 21° до 75° × 54°
Расстояние измерения, м > 1×
Погрешность измерения, % 2
Температурный дрейф, % 0,1
Разность температур, эквивалентная шуму, К < 1 (1 000°C, 25 Гц)
Частота кадров, Гц 50
Время отклика, мс 40
Интерфейс Ethernet,
Масса, кг ~10
Питание От 12 В до 36 DC
Степень защиты IP65
Рабочая температура камеры, °C От –25 до +150 с водяным охлаждением)
Рабочая температура системного кабеля, °C От –25 до +80
Условия хранения, °C от –20 до 70
Выходной сигнал тепловизора представляет собой, с одной стороны, поток радиометрических данных (фактически каждая точка видимого изображения становится «виртуальным термометром»), а с другой – очищенное от влияния пламени видеоизображения, которое можно вывести на монитор оператора для визуального контроля. Поток данных после калибровки становится входным сигналом для системы автоматического управления, задача которой – удержание зоны с определенной температурной уставкой в нужном месте. Если прогретая до нужной температуры точка смещается в сторону холодного обреза, система уменьшит интенсивность поступления газа в форсунку, если смещение пойдет в сторону горячего обреза, подача газа будет увеличена.
Возвращаясь к поставленным в начале статьи типовым проблемам эксплуатации вращающихся печей, логично дополнить систему и средствами контроля состояния футеровки. Для этого можно использовать тепловизоры внешней установки без рубашки охлаждения, контролирующие всю длину печи.
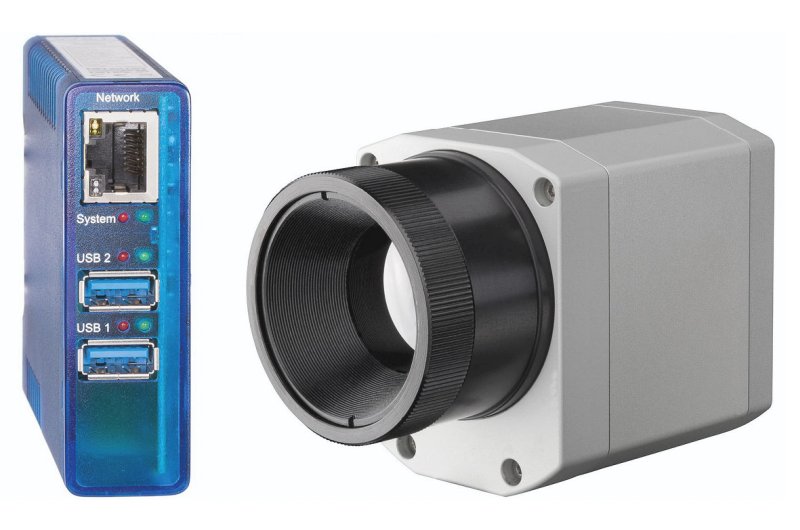
Полученные с такого тепловизионного комплекса (рис. 4) данные позволяют обнаружить проблемные зоны, в которых футеровка начинает разрушаться, по температурным трендам в автоматическом режиме, подавать сигналы тревоги, вести архивацию событий в журнале, строить графики изменения температуры в произвольно выбранной зоне за любой промежуток времени. Благодаря тому, что печь вращается в процессе работы, нетрудно построить по серии замеров и ее термографическую 3D модель (рис.5).
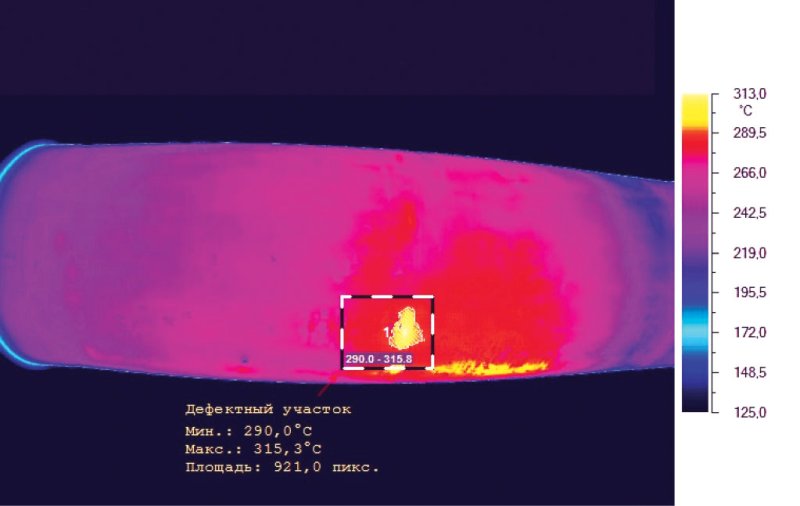
Построенный таким образом тепловизионный комплекс решает одновременно две проблемы эксплуатации вращающихся печей (управление зоной прокалки и контроль футеровки), позволяет устранить человеческий фактор и сэкономить средства клиента за счет уменьшения потерь, связанных с простоем и ремонтом технологического оборудования.
Группа компаний «ИНТРАТУЛ» с 2013 года разрабатывает и внедряет системы инфракрасного мониторинга технологических процессов, предоставляя своим клиентам самые современные цифровые решения. Накопленный опыт и успешно проведенные опытно-промышленные испытания позволяют уверенно реализовывать проекты в различных отраслях промышленности.